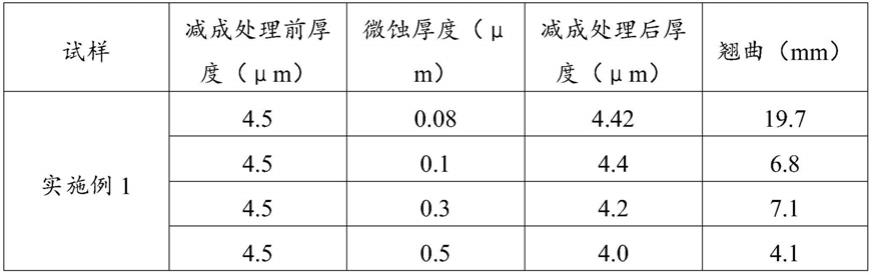
1.本发明涉及电解铜箔制备技术领域,更具体地说,涉及一种减成法制备低翘曲极薄电解铜箔的方法。
背景技术:
2.电解铜箔是制造覆铜板、印刷电路板、锂离子电池的重要材料。电解铜箔的生产工艺的主要步骤是生箔工序,生箔工序通常采用钛辊作为阴极辊,使得电解液中的铜离子沉积在钛辊表面从而得到电解铜箔。由于室温下铜是面心立方晶格,钛是密排六方晶格,二者之间的晶格差异使得直接与钛辊表面接触而沉积的铜箔面易产生翘曲缺陷。翘曲严重影响下游客户的使用,主要影响的工序是涂布,涂布过烤箱时易出现翘边后浆料厚度不均问题。在动力电池制备过程中由于铜箔存在翘曲缺陷,导致负极激光切极耳内折情况严重,需安排专人挑极耳,费时费力,严重影响生产效率和质量,急需改善。
3.公开号为cn113151759a的中国专利申请提出一种降低铜箔翘曲的电热处理装置,通过对铜箔进行加热处理,加快铜箔残余应力的释放,从而减小铜箔的翘曲。上述方法虽然在一定程度上可以减小翘曲,但是其效果一般,尤其在铜箔整体厚度较小时其效果并不明显。公告号为cn108677225b的中国专利提出一种降低电解铜箔翘曲的处理方法,包括:酸洗
‑
特殊粗化
‑
特殊固化
‑
粗化
‑
固化
‑
镀锌镍合金
‑
防氧化处理
‑
硅烷偶联剂处理
‑
干燥;通过对铜箔毛面的特殊处理,增加毛面压应力,使铜箔两面的应力得到进一步平衡,进而降低铜箔的残余应力,实现铜箔翘曲的减小。上述方法虽然能够有效减小翘曲,但是需要其工艺处理过程复杂,不利于降低生产成本。
4.故,现有技术具有较大的改进空间。
技术实现要素:
5.本发明的目的是为了弥补现有技术存在的不足,提出一种减成法制备低翘曲极薄电解铜箔的方法,通过对电解生成的铜箔进行减成处理,工艺操作简单、生产成本低,且能够有效减小电解铜箔的翘曲。
6.为了达到上述目的,本发明通过以下技术方案实现:
7.一种减成法制备低翘曲极薄电解铜箔的方法,包括如下步骤:
8.1)电解生箔:将阴极辊浸没在电解池的电解液中,在直流电的作用下,使电解液中的铜离子在所述阴极辊表面沉积形成有铜箔;
9.2)减成处理:将步骤1)中的电解液经过过滤处理后泵送到减成槽内直至浸没所述减成槽内的第一阴极板、第二阴极板;将阴极辊上的铜箔剥离并输送到减成槽内,在减成槽内使用导向辊对铜箔进行导向,所述第一阴极板、第二阴极板与电源的负极连通,铜箔与电源的正极连通,铜箔的光面与所述第一阴极板、第二阴极板相对应;通直流电,铜箔光面表面的部分铜箔得到电子变成铜离子进入电解液中,电解液的铜离子得到电子变成铜沉积在第一阴极板、第二阴极板上;
10.3)水洗处理:待铜箔光面表面的铜箔被微蚀一定厚度后,通过位于减成槽出口侧的导向辊将铜箔从减成槽内导出并导入水洗槽内进行水洗处理。
11.本发明中的减成处理是指将铜箔减少一定厚度的处理。本发明通过减成处理使得铜箔光面表面的铜箔被微蚀一定厚度,即微蚀掉直接与阴极辊直接接触的铜箔面,从而使得因铜与阴极辊存在晶格差异造成应力的铜箔表面被微蚀掉,进而降低所得电解铜箔的翘曲。
12.而且,电解生箔处理的电解液在减成处理中可以得到重复利用,减成槽内的第一阴极板、第二阴极板上沉积的铜可被回收利用,有利于降低生产成本。
13.根据以上方案,所述电解液包括10
‑
20g/lcu2
、60
‑
80g/l硫酸、1
‑
5g/l二巯基噻二唑。通过添加二巯基噻二唑作为铜缓蚀剂能够实现对铜箔层的缓蚀保护和提高抛光效果,使得铜箔在完成减成处理后自动进入钝化状态,不受电解液的损坏。
14.根据以上方案,步骤2)中通直流电,使电流密度保持在20
‑
60a/dm2。
15.根据以上方案,所述厚度为0.1
‑
0.5μm。
16.根据以上方案,还包括步骤4)防氧化处理:铜箔水洗后经导向辊导入防氧化槽内进行防氧化处理。
17.根据以上方案,所述减成槽包括减成槽主体,所述减成槽主体内的下部对称设有两个导向辊,两个所述导向辊的上方分别设有第一阴极板、第二阴极板,所述减成槽的出口侧设有导向辊。
18.根据以上方案,步骤2)减成处理完成后的电解液经硅藻土、活性炭过滤后进行回收作为电解液的制备原料进行循环使用。通过上述操作对电解液进行回收循环利用,有利于降低生产成本。
19.本发明的有益效果在于:
20.本发明提出一种减成法制备低翘曲极薄电解铜箔的方法,通过减成处理使得铜箔光面表面的铜箔被微蚀一定厚度,从而使得因铜与阴极辊存在晶格差异造成应力的铜箔表面被微蚀掉,能够有效减小所得电解铜箔的翘曲;而且电解生箔处理的电解液在减成处理中可以得到重复利用,减成槽内的第一阴极板、第二阴极板上沉积的铜可被回收利用,有利于降低生产成本,有效解决现有制备工艺复杂、生产成本高、翘曲减小效果差的技术问题。
附图说明
21.图1为实施例1所述减成法制备低翘曲极薄电解铜箔的方法的工艺示意图。
22.图中:1、电解池;2、供液泵;3、阀门;4、过滤装置;5、减成槽;6、铜箔;7、导向辊;7
‑
1、阴极辊;8
‑
1、第一阴极板;8
‑
2、第二阴极板;9、水洗槽;10、防氧化槽。
具体实施方式
23.为了更好地理解本发明,下面结合实施例进一步阐明本发明的内容,但本发明不仅仅局限于下面的实施例。
24.实施例1
25.如图1所示,一种减成法制备低翘曲极薄电解铜箔的方法,包括如下步骤:
26.1)电解生箔:将阴极辊7
‑
1浸没在电解池1的电解液中,在直流电的作用下,使电解
液中的铜离子在所述阴极辊7
‑
1表面沉积形成有铜箔;
27.2)减成处理:将步骤1)中的电解液经过过滤处理后泵送到减成槽5内直至浸没所述减成槽5内的第一阴极板8
‑
1、第二阴极板8
‑
2;将阴极辊7
‑
1上的铜箔6剥离并输送到减成槽5内,在减成槽5内使用导向辊7对铜箔6进行导向,所述第一阴极板8
‑
1、第二阴极板8
‑
2与电源的负极连通,铜箔6与电源的正极连通,铜箔6的光面与所述第一阴极板8
‑
1、第二阴极板8
‑
2相对应;通直流电,铜箔光面表面的部分铜箔得到电子变成铜离子进入电解液中,电解液的铜离子得到电子变成铜沉积在第一阴极板8
‑
1、第二阴极板8
‑
2上;
28.3)水洗处理:待铜箔光面表面的铜箔被微蚀一定厚度后,通过位于减成槽3出口侧的导向辊7将铜箔6从减成槽5内导出并导入水洗槽10内进行水洗处理;
29.4)防氧化处理:铜箔水洗后经导向辊导入防氧化槽11内进行防氧化处理。
30.进一步地说,所述电解液包括10
‑
20g/lcu
2
、60
‑
80g/l硫酸、1
‑
5g/l二巯基噻二唑。
31.进一步地说,步骤2)中通直流电,使电流密度保持在20
‑
60a/dm2。
32.进一步地说,所述减成槽5包括减成槽主体,所述减成槽主体内的下部对称设有两个导向辊7,两个所述导向辊7的上方分别设有第一阴极板8
‑
1、第二阴极板8
‑
2,所述减成槽5的出口侧设有导向辊7。
33.进一步地说,步骤2)减成处理完成后的电解液经硅藻土、活性炭过滤后进行回收作为电解液的制备原料进行循环使用。
34.对比例1
35.一种电解铜箔的制备方法,包括:将阴极辊浸没在电解池的电解液中,在直流电的作用下,使电解液中的铜离子在所述阴极辊表面沉积形成有铜箔;将阴极辊上的铜箔剥离得到电解铜箔。其中,所述电解液包括10
‑
20g/lcu
2
、60
‑
80g/l硫酸、1
‑
5g/l二巯基噻二唑。
36.实施例1通过控制步骤1)的电解时间,分别得到厚度为4.5μm、5μm、6μm的铜箔;然后再将上述不同厚度的铜箔进行步骤2)
‑
4)的操作,通过控制步骤2)的减成处理时间使上述铜箔的光面分别微蚀掉0.08、0.1、0.3、0.5、0.7μm,最终得到多种不同厚度的低翘曲电解铜箔。对比例1通过控制的电解时间,分别得到厚度为4.5μm、5μm、6μm的铜箔;将上述低翘曲电解铜箔与对比例1的电解铜箔进行翘曲测试,测试结果见下表1:
37.表1
38.[0039][0040]
上述铜箔生产工艺基本相同,不同仅在于根据所需铜箔厚度调节电解时间、根据所需微蚀厚度调节减成处理时间。
[0041]
从上表1可见,厚度为4.5
‑
6μm的铜箔未经减成处理,翘曲为20
‑
30mm;经减成处理微蚀<0.1μm,翘曲为15
‑
20mm;经减成处理微蚀0.1
‑
0.4μm,翘曲为6
‑
8mm;经减成处理微蚀0.5
‑
0.7μm,翘曲为1
‑
5mm。即电解铜箔通过减成处理微蚀一定厚度后,其翘曲得到明显的减小;当微蚀厚度为0.1
‑
0.7μm时,铜箔的翘曲相对较低,当微蚀厚度为0.5μm以上时翘曲基本消除,因此综合生产效率及生产成本进行考虑,优选微蚀厚度为0.1
‑
0.5μm时效果最佳。
[0042]
以上所述仅是本发明的较佳实施方式,故凡依本发明专利申请范围所述的构造、特征及原理所做的等效变化或修饰,均包括于本发明专利申请范围内。
再多了解一些
本文用于企业家、创业者技术爱好者查询,结果仅供参考。