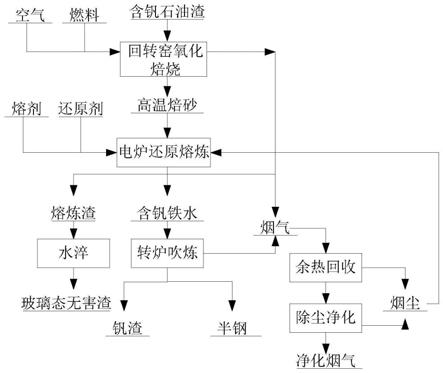
1.本发明涉及有价金属回收技术领域,具体而言,涉及一种含钒石油渣资源化、无害化处理的方法。
背景技术:
2.原油在精炼或作为燃料燃烧过程中会产生大量石油渣、石油灰或废催化剂等一系列工业固废,如不及时处理会造成环境污染,同时这些固废通常含有较高的钒、镍等有价金属,具有经济回收价值。
3.美国、日本、德国等一些西欧国家早在80年代初就开始从石油渣、石油灰和废催化剂中提钒,但多数采用湿法工艺浸出提钒,具体工艺如下:
4.1、pechenet工艺,将废催化剂直接送入回转窑在温度<700℃下焙烧4
‑
8小时,焙烧时间取决于催化剂的疏松度,炉内气体中氧的比率以及含钒量。煅烧物用热浓盐酸在90℃浸出8小时,99%的金属物都溶解于液体中,不溶物氧化硅固体经过滤分离除去,五价钒还原为四价钒释放出氯,用烧碱以次氯酸形式经水洗涤可以除去。浸出液铝的存在对其它元素的净化与提取干扰很大,应首先除去。然后浓缩除次氯酸,以氯化铝结晶形式过滤除去,钒用溶剂萃取除杂。该工艺可综合回收钒、钼、钴。最终钒以五氧化二钒形式回收。
5.2、amax工艺,针对炼油渣原料,综合回收钒、钼、钴、镍和铝,生产工艺如下:炼油渣与烧碱混合进球磨机磨细并部分浸出,浆液用泵送往一级浸出高压釜,在高温和加压下氧化。硫转变为硫化物,碳氢化合物大部分分解,溶解出钒和钼,过滤分离固液体,溶液作为回收钒和钼的原料送往回收工序,最后分别回收钒、钼和铝等元素。钒是用烧碱沉淀浸出液,经洗涤,干燥、氧化制粒等工序生产出五氧化二钒并炼成钒铁。
6.3、sadacem工艺,将废催化剂与碳酸钠混合在多膛炉内焙烧2小时,焙烧在氧化气氛下进行,温度650℃
‑
850℃,钒和钼与碳酸钠反应生成可溶盐,煅烧物用水冷却、磨碎并浸出,将不溶物与饱合浸出液逆流浸出分离。用氯化铵以多钒酸铵形式从浸出液中沉淀出钒,多钒酸铵经煅烧、熔化得到五氧化二钒。酸化过滤物并在80℃
‑
85℃加热以钼酸形式沉淀出钼来,煅烧钼酸得到氧化钼。
7.目前从含钒物料中提取五氧化二钒基本都是在上述几种工艺基础上进行开发,如钠盐制粒焙烧—水浸工艺、空白焙烧—酸浸/碱浸工艺、粉矿直接酸浸工艺、加石灰制粒焙烧—碱浸工艺等。然而,以上湿法工艺仅是从提钒角度出发,并未考虑石油渣等固废无害化处置,同时湿法工艺不仅流程复杂,而且产生大量废酸或废碱液会造成二次污染,所产浸出渣仍需要进一步无害化处理,后续处理成本高。
8.基于以上原因,有必要提供一种能够在提钒、镍等有价金属的同时,对石油工业所产含钒废料特别是含钒石油渣进行无害化处置的工艺。
技术实现要素:
9.本发明的主要目的在于提供一种含钒石油渣资源化、无害化处理的方法,以解决
现有技术中湿法工艺未考虑固废无害化处置、流程复杂、二次污染严重的问题。
10.为了实现上述目的,根据本发明的一个方面,提供了一种含钒石油渣资源化、无害化处理的方法,其包括以下步骤:使含钒石油渣在回转窑中进行氧化焙烧处理,得到高温焙砂;将高温焙砂热送入电炉中进行还原熔炼,得到含钒铁水和熔炼渣;将含钒铁水在转炉中进行吹炼,得到钒渣和铁水;其中吹炼过程吨铁耗氧量为10~15nm3,且在吹炼过程中,同时向熔池加入冷却剂以控制熔池温度在1350~1450℃;将熔炼渣进行水淬,得到玻璃态无害渣。
11.进一步地,氧化焙烧处理过程中,回转窑焙烧温度为1000~1200℃,含钒石油渣在回转窑中的停留时间为1~2h。
12.进一步地,氧化焙烧处理过程中,控制回转窑内为弱氧化性气氛,氧含量小于1wt%;优选地,氧化焙烧处理过程中,控制高温焙砂的出窑温度为750~950℃;优选地,氧化焙烧处理过程中向回转窑中加入燃料,燃料选自烟煤、褐煤、天然气、煤气中的一种或多种。
13.进一步地,还原熔炼的步骤包括:将高温焙砂、还原剂和熔剂通入电炉中进行还原熔炼;优选地,还原熔炼过程的温度为1450~1650℃,时间为1~3h。
14.进一步地,熔剂选自石灰石、石英石、石英砂、脉石、白云石的一种或多种。
15.进一步地,还原熔炼的步骤中,控制渣中m(cao)/m(sio2)=0.6~1.0,m(al2o3)/m(sio2)=0.2~0.6。
16.进一步地,还原剂选自无烟煤、烟煤、焦炭、活性炭中的一种或多种,优选还原剂的粒度小于50mm。
17.进一步地,还原剂的加入量为高温焙砂重量的5~15%。
18.进一步地,冷却剂为氧化铁皮。
19.进一步地,上述方法还包括:将氧化焙烧过程、还原熔炼过程和吹炼过程中产生的烟气一起依次进行余热回收、除尘净化,得到净化烟气和烟尘;将烟尘返回至还原熔炼步骤。
20.利用本发明提供的含钒石油渣资源化、无害化处理的方法,其包括以下步骤:使含钒石油渣在回转窑中进行氧化焙烧处理,这样可以对含钒石油渣进行脱水和脱硫。其次,将高温焙砂在电炉中进行还原熔炼,能够将钒以及镍、铁等有价金属还原并进行造渣,得到含钒铁水和熔炼渣。再次,将含钒铁水在转炉中进行吹炼,控制吨铁耗氧量为10~15nm3,并同时向熔池加入冷却剂以控制熔池温度在1350~1450℃,即可将钒优先氧化进入渣中形成钒渣,其余有价金属则保留金属态与钒渣分离。最后,本发明将熔炼渣进行水淬,即可得到玻璃态无害渣。
21.因此,利用本发明提供的方法处理含钒石油渣,能够在高效回收钒、镍等有价金属的同时,对石油行业所产含钒石油渣进行无害化处置。而且,含钒石油渣中有机组分在焙烧时作为热源得到充分利用,最终实现含钒石油渣的减量化、无害化及资源化。
附图说明
22.构成本技术的一部分的说明书附图用来提供对本发明的进一步理解,本发明的示意性实施例及其说明用于解释本发明,并不构成对本发明的不当限定。在附图中:
23.图1示出了根据本发明一种实施例的含钒石油渣资源化、无害化处理的方法工艺流程图。
具体实施方式
24.需要说明的是,在不冲突的情况下,本技术中的实施例及实施例中的特征可以相互组合。下面将参考附图并结合实施例来详细说明本发明。
25.正如背景技术部分所描述的,现有技术中采用湿法工艺处理含钒废渣时,未考虑固废无害化处置,且流程复杂、二次污染严重。
26.为了解决上述问题,本发明提供了一种含钒石油渣资源化、无害化处理的方法,如图1所示,该方法包括以下步骤:使含钒石油渣在回转窑中进行氧化焙烧处理,得到高温焙砂(又称焙烧渣);将高温焙砂热送入电炉中进行还原熔炼,得到含钒铁水和熔炼渣;将含钒铁水在转炉中进行吹炼,得到钒渣和铁水(半钢);其中吹炼过程控制吨铁耗氧量为10~15nm3,且在吹炼过程中,同时向熔池加入冷却剂以控制熔池温度在1350~1450℃;将熔炼渣进行水淬,得到玻璃态无害渣。
27.利用本发明提供的上述方法,使含钒石油渣在回转窑中进行氧化焙烧处理,这样可以对含钒石油渣进行除水和脱硫。其次,将高温焙砂在电炉中进行还原熔炼,能够将钒以及镍、铁等有价金属还原并进行造渣,得到含钒铁水和熔炼渣。再次,将含钒铁水在转炉中进行吹炼,控制吨铁耗氧量为10~15nm3,同时向熔池加入冷却剂控制熔池温度1350~1450℃,即可将钒优先氧化进入渣中形成钒渣,其余有价金属则保留金属态与钒渣分离。最后,本发明将熔炼渣进行水淬,即可得到玻璃态无害渣。
28.因此,利用本发明提供的方法处理含钒石油渣,能够在高效回收钒、镍、铁等有价金属的同时,对石油行业所产含钒石油渣进行无害化处置。而且,含钒石油渣中有机组分在焙烧时作为热源得到充分利用,最终实现石油渣等含钒石油渣的减量化、无害化及资源化。
[0029]“玻璃态无害渣”是指晶体结构为玻璃态,且重金属浸出率低,符合建材或填埋等标准。
[0030]
上述将高温焙砂热送入电炉是指氧化焙烧阶段所得高温焙砂不经冷却处理,直接以热的状态进行电炉中进行还原焙烧。
[0031]
含钒石油渣中通常含有50%~60%物理水及~6%的硫,为了更充分地去除含钒废渣携带的水并进行脱硫,在一种优选的实施方式中,上述氧化焙烧处理过程中,回转窑焙烧温度为1000~1200℃,含钒石油渣在回转窑中的停留时间为1~2h。将温度控制在上述范围内,一方面更够充分烘干和脱硫,另一方面也可以利用含钒废渣自身有机碳进行补热,节省外加能源。更优选地,氧化焙烧处理过程中,控制回转窑内为弱氧化性气氛,含氧量不高于1wt%。这样有利于充分脱除二氧化硫。进一步优选地,氧化焙烧处理过程中,控制焙烧渣的出窑温度为750~950℃。
[0032]
优选氧化焙烧处理过程中,向回转窑中加入燃料。这样,外加燃料作为主要热源,原料中有机物作为补充热源进行反应。上述燃料包括但不限于选自烟煤、褐煤、天然气、煤气中的一种或多种。在具体实施过程中,可以根据含钒石油渣中有机碳含量以及上述提到的焙烧温度、烟气含氧量等调整燃料的加入量,这是本领域技术人员都应理解的,在此不再赘述。
[0033]
待高温焙砂出窑后,将其转送至电炉进行还原熔炼,转送期间可采用热料输送设备。在一种优选的实施方式中,上述还原熔炼的步骤包括:将高温焙砂、还原剂和熔剂通入电炉中进行还原熔炼;优选地,还原熔炼过程的温度为1450~1650℃,时间为1~3h。这样,能够使高温焙砂中的钒、镍、铁等由氧化态深度还原为金属态,与渣分离。具体实施过程中,可利用电炉中的电极将炉内温度升温,然后进料熔炼。
[0034]
为了进一步提高造渣效果,在一种优选的实施方式中,上述熔剂选自石灰石、石英石、石英砂、脉石、白云石的一种或多种;优选地,还原熔炼的步骤中,控制渣中m(cao)/m(sio2)=0.6~1.0,m(al2o3)/m(sio2)=0.2~0.6。此处m(cao)/m(sio2)是指熔炼渣中cao和sio2质量比,m(al2o3)/m(sio2)是指熔炼渣中al2o3和sio2质量比。含钒石油渣中造渣用氧化物主要为氧化钙、氧化铝和二氧化硅,将渣型控制在上述范围内,一方面有利于降低冶炼渣粘度和熔点,另一方面更有利于金属和渣的分离,提高金属回收率和品位。具体实施过程中,可以通过渣型调整熔剂加入量和加入类型。
[0035]
上述还原剂优选包括但不限于无烟煤、烟煤、焦炭、活性炭中的一种或多种,优选还原剂的粒度小于50mm。为了进一步提高熔炼还原效果,提高钒回收率,在一种优选的实施方式中,还原剂的加入量为高温焙砂重量的5~15%。
[0036]
经还原熔炼后,钒、铁等以合金形式与渣分离,为了使钒进一步与其他金属分离,进行了吹炼操作。在一种优选的实施方式中,吹炼过程采用顶吹的方式向转炉中吹入富氧空气。具体实施过程中,优选将含钒铁水从电炉的金属放出口放出,通过铁水包转运至转炉内进行吹炼提钒。该条件下控制吨铁吹氧量为10~15nm3,能够得到高品质钒渣和半钢,其中钒渣含钒20~30%,钒回收率85~95%,铁回收率80~90%,还原熔炼得到的熔炼渣从电炉出渣口放出,进行水淬,得到玻璃态无害渣即可。
[0037]
在一种优选的实施方式中,上述方法还包括:将氧化焙烧过程、还原熔炼过程和吹炼过程中产生的烟气一起依次进行余热回收、除尘净化,得到净化烟气和烟尘(余热回收和除尘净化过程中均得到了部分烟尘);将烟尘返回至还原熔炼步骤。这样,可以对烟气中携带的烟尘进一步熔炼回收有价金属,净化烟气达标排放即可。具体地,余热回收可采用余热锅炉,除尘净化可采用袋式除尘器等。
[0038]
总之,本发明提供一种回转窑 电炉 转炉火法工艺处理含钒石油渣,将含钒石油渣进行无害化处置,同时高效回收钒、镍、铁等有价金属,所得钒渣用于后续钒产品生产,半钢直接外售增加经济效益,最终实现含钒石油渣减量化、资源化和无害化。
[0039]
以下结合具体实施例对本技术作进一步详细描述,这些实施例不能理解为限制本技术所要求保护的范围。
[0040]
以下实施例以某种含钒石油渣进行处理,其湿基含水约56%,烘干后干基成分如表1所示,有价金属五氧化二钒高达3.49%,氧化镍0.62%,并含有一定的氧化铁在熔炼时可形成铁合金,有机碳含量高达26%,造渣氧化物主要有氧化钙、氧化铝和二氧化硅。
[0041]
表1某含钒石油渣干基成分组成/wt%
[0042]
v2o5nioal2o3sio2fe2o3so3k2ona2ocaomgoc3.490.6212.0827.957.235.920.470.7814.580.8226.02
[0043]
实施例1
[0044]
将含钒石油渣送入回转窑高温氧化焙烧,期间采用烟煤作为燃料。回转窑内为弱
还原性气氛,其中氧含量不高于1wt%;回转窑内温度为1200℃,含钒石油渣在窑内停留时间为1h,焙烧渣的出窑温度为950℃。所得高温焙砂热送电炉内,同时加入熔剂及还原剂,使al2o3/sio2=0.28,cao/sio2=0.86,烟煤加入量为高温焙砂的10%,熔炼温度1550℃,熔炼时间2h,得到熔炼渣和含钒铁水;熔炼渣经水淬形成玻璃态无害渣,含钒铁水转运至转炉吹炼提钒,控制吨铁吹氧量为12nm3,期间加入冷却剂氧化铁皮控制吹炼温度为1400℃,得到钒渣和半钢,钒渣品位27%,钒回收率94%,铁回收率88%。
[0045]
实施例2
[0046]
与实施例1区别为:调整熔剂加入量控制三元渣型中al2o3/sio2=0.60,cao/sio2=1.0,所得钒渣品位25%,钒回收率90%,铁回收率87%。
[0047]
实施例3
[0048]
与实施例1区别为:调整熔剂加入量控制三元渣型中al2o3/sio2=0.20,cao/sio2=0.60,所得钒渣品位24%,钒回收率92%,铁回收率85%。
[0049]
实施例4
[0050]
与实施例1区别为:调整熔剂加入量控制三元渣型al2o3/sio2=0.7,cao/sio2=1.1,所得钒渣品位17%,钒回收率80%,铁回收率77%。
[0051]
实施例5
[0052]
与实施例1区别为:还原熔炼温度为1450℃时,所得钒渣品位22%,钒回收率87%,铁回收率80%。
[0053]
实施例6
[0054]
与实施例1区别为:还原熔炼温度为1650℃时,所得钒渣品位25%,钒回收率89%,铁回收率84%。
[0055]
实施例7
[0056]
与实施例1区别为:还原熔炼温度为1400℃,所得钒渣品位15%,钒回收率53%,铁回收率42%。
[0057]
实施例8
[0058]
与实施例1区别为:吹炼过程中,吨铁吹氧量为10nm3,所得钒渣品位21%,钒回收率86%,铁回收率87%。
[0059]
实施例9
[0060]
与实施例1区别为:吹炼过程中,吨铁吹氧量为15nm3,所得钒渣品位24%,钒回收率91%,铁回收率88%。
[0061]
实施例10
[0062]
与实施例1区别为:吹炼过程中,吨铁吹氧量为7nm3,所得钒渣品位14%,钒回收率55%,铁回收率85%。
[0063]
以上所述仅为本发明的优选实施例而已,并不用于限制本发明,对于本领域的技术人员来说,本发明可以有各种更改和变化。凡在本发明的精神和原则之内,所作的任何修改、等同替换、改进等,均应包含在本发明的保护范围之内。
再多了解一些
本文用于企业家、创业者技术爱好者查询,结果仅供参考。