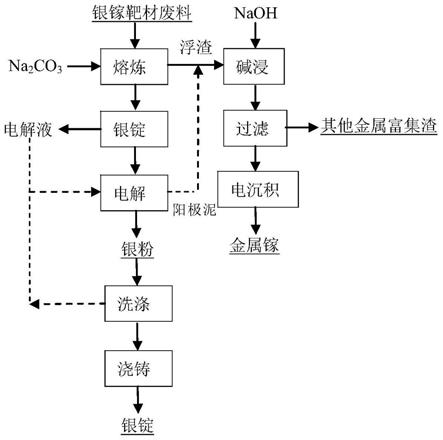
1.本公开涉及稀贵金属分离回收领域,具体涉及一种分离回收金属银、镓的方法。
背景技术:
2.银、镓作为稀贵金属原料,在太阳能、电子、半导体行业等领域有着不可替代的应用,特别是在高导电、导热材料应用方面有着优越的性能。目前,工业中很少有具体的银镓废料回收工艺方案,针对银或镓的二次物料主要以湿法工艺为主,金属银通过酸浸
‑
沉淀富集
‑
熔炼还原
‑
电解的工艺回收,金属镓采用酸浸或碱浸再经过萃取或离子交换富集后通过电沉积回收而湿法工艺存在的主要问题是耗酸较多,反应时间长,工艺步骤多。因此,需要一种高效、简单的方法来分离回收稀贵金属银、镓。
技术实现要素:
3.鉴于背景技术存在的问题,本公开的目的在于提供一种工艺流程简单、耗酸少的分离回收金属银、镓的方法,该方法回收得到的产品纯度好,其他有价金属得到很好富集。
4.在一些实施例中,本公开提供的分离回收金属银、镓的方法包括以下步骤:s1:将含有银镓的废料与碱料混合均匀后进行熔炼;s2:将步骤s1经过熔炼后得到的浮渣用碱液浸泡、过滤,然后将浸出液进行电沉积得到金属镓;s3:将步骤s1经过熔炼后得到的银锭作为阳极,硝酸银作为电解液,电解提纯金属银。
5.在一些实施例中,步骤s1中的碱料包括碳酸钠、氢氧化钠或氢氧化钾中的至少一种。
6.在一些实施例中,步骤s1熔炼的工艺条件为:熔炼温度为1000℃至1200 ℃,熔炼的时间为2h至4h,熔炼时通入氧气或压缩空气。
7.在一些实施例中,在步骤s1的熔炼过程中,碳酸钠的用量为理论量的 1.5倍至2倍,氢氧化钠的用量为碳酸钠质量的2%至10%。
8.在一些实施例中,步骤s2中的碱液包括氢氧化钠溶液或氢氧化钾溶液中的至少一种。
9.在一些实施例中,步骤s2中的碱浸工艺条件为:碱浸温度为80℃至95 ℃,碱浸时间为4h至6h,浮渣和碱液的质量比为1:10至1:20。
10.在一些实施例中,步骤s2中的电沉积工艺条件为:浸出液中的碱浓度为150g/l至200g/l,阴极和阳极为不锈钢,电流密度为1000a/m2至1800a/m2, 电解槽的电压为3v至4v,电解液的温度为40℃至60℃。
11.在一些实施例中,步骤s3中的电解工艺条件为:阴极采用钛板,电解液中银离子浓度为100g/l至120g/l,电解液的温度35℃至45℃,硝酸浓度为6g/l至8g/l,电流密度为700a/m2至800a/m2。
12.在一些实施例中,步骤s1和步骤s2同时进行。
13.在一些实施例中,含有银镓的废料成份包括含量70%至80%的银、含量 20%至
30%的镓以及杂质。
14.本公开的有益效果如下:本公开提供的分离回收金属银、镓的方法是通过火法与湿法工艺结合,能快速分离回收银、镓,整个工艺过程耗酸少、速度快,可以减少银粉的囤积,通过电解或电沉积可以回收得到纯度为99.99%的镓金属和纯度为99.999%的银金属,两者均可作为电子靶材的原料使用。
附图说明
[0015][0016]
图1为本公开分离回收金属银、镓的方法工艺流程示意图。
具体实施方式
[0017]
应理解的是,所公开的实施例仅是本公开的示例,本公开可以以各种形式实施,因此,本公开的具体细节不应被解释为限制,而是仅作为权利要求的基础且作为表示性的基础用于教导本领域普通技术人员以各种方式实施本公开。在本公开的说明中,未明确说明的术语、专业用词均为本领域技术人员的公知常识,未明确说明的方法均为本领域技术人员公知的常规方法。
[0018]
接下来说明本公开的分离回收金属银、镓的方法。
[0019]
本公开采用“火法”与“湿法”相结合的工艺回收金属银、镓,通过首步为特定的“火法”(熔炼)工艺对镓、银两种元素进行分离,回收得到的银粉和镓粉可作为原料再加工成靶材或其他同类靶材产品。本公开所提出的工艺方法、工艺流程简单,耗酸少,回收得到的产品纯度好,回收的金属镓纯度可达99.99%,回收的金属银纯度可达99.999%,且其他的有价金属也可以很好地富集。
[0020]
在一些实施例中,本公开提供的分离回收金属银、镓的方法包括以下步骤:s1:将含有银、镓的废料与碱料混合均匀后进行熔炼;s2:将步骤s1 经过熔炼后得到的浮渣用碱液浸泡、过滤,然后将浸出液进行电沉积得到金属镓;s3:将步骤s1经过熔炼后得到的银锭作为阳极,硝酸银作为电解液,电解提纯金属银。
[0021]
在一些实施例中,含有银、镓的废料成份包括含量70%至80%的银、含量20%至30%的镓以及杂质。在一些实施例中,含有银镓的废料可来自于银镓合金靶材残靶、粉末碎屑或切削料,其中,镓的质量百分含量约为20%左右,银质量百分含量约为72%
‑
78%,并且还含有少量铟(in)、锑(sb)、铋(bi)、碳等杂质。
[0022]
在一些实施例中,步骤s1中的碱料包括碳酸钠、氢氧化钠或氢氧化钾中的至少一种,碱料加入的目的是在熔炼的高温条件下,碱料可以与镓反应生成镓的钠盐,便于后续的分离、提纯。
[0023]
在一些实施例中,步骤s1熔炼的工艺条件为:熔炼温度为1000℃至1200 ℃,熔炼的时间为2h至4h,熔炼时通入氧气或压缩空气,该工艺条件可确保镓充分氧化后与碱料反应生成盐,通气的速率可根据实际的工艺确定。在步骤s1的熔炼过程中,例如碱料为na2co3时,废料中的金属镓主要发生如下化学反应:4ga 3o2=2ga2o3,ga2o3 na2co3=2nagao2 co2,为保证废料中的金属镓可以充分地被回收,碳酸钠的用量需要过量,在一些实施例中,碳酸钠的用量为理论量的1.5倍
‑
2倍,其中,理论量是基于碳酸钠和氧化镓发生反应的化学方程
式而得到的用量值。在一些实施例中,在步骤s1 的熔炼过程中,当碱料为碳酸钠和氢氧化钠时,碳酸钠的用量为理论量的1.5 倍至2倍,氢氧化钠的用量为碳酸钠质量的1%至10%,优选为2%至10%,其中,理论量是基于碳酸钠和氧化镓发生反应的化学方程式而得到的用量值,这样可以充分地将目标金属元素富集、分离。
[0024]
在一些实施例中,步骤s2中的碱液包括氢氧化钠溶液或氢氧化钾溶液中的至少一种。步骤s2中用碱液浸泡的目的在于将镓元素浸出,而其他杂质金属元素会形成沉淀富集,便于后续分离。
[0025]
在一些实施例中,步骤s2中的碱浸工艺条件为:碱浸温度为80℃至95 ℃,碱浸时间为4h至6h,浮渣和碱液的质量比为1:10至1:20,这样可以充分地将浮渣中的目标金属元素富集、分离。
[0026]
在一些实施例中,步骤s2中的电沉积工艺条件为:浸出液中的碱浓度为150g/l至200g/l,阴极和阳极为不锈钢,电流密度为1000a/m2至1800a/m2, 电解槽的电压为3v至4v,电解液的温度为40℃至60℃,在该工艺条件下,有利于金属镓在阴极析出。
[0027]
在一些实施例中,步骤s2中过滤后得到的浸出渣富集金属元素铟、锑、铋。
[0028]
在一些实施例中,步骤s3中的电解工艺条件为:阴极采用钛板,电解液中银离子浓度为100g/l至120g/l,电解液的温度35℃至45℃,硝酸浓度为6g/l至8g/l,电流密度为700a/m2至800a/m2,在该工艺条件下,可以获得纯度达到4n5至5n的高纯银粉。
[0029]
在一些实施例中,经过步骤s3提纯后得到的银粉可通过洗涤、浇铸工艺进一步制备高纯度银锭。
[0030]
在一些实施例中,步骤s1和步骤s2同时进行,在实际的工艺中两个工艺步骤同时进行可以节约回收工艺的时间,提高回收效率。
[0031]
下面结合实施例,进一步阐述本公开。应理解,这些实施例仅用于说明本公开而不用于限制本公开的范围。在下述实施例、对比例中,所使用到的试剂、材料以及仪器如没有特殊的说明,均可商购获得或本领域中公知的方法制备获得。
[0032]
实施例1
[0033]
称取银镓靶材切削料100g,然后加入9g碳酸钠与之混合均匀后进行熔炼:将混合物置于1100℃的环境中焙烧4h,同时以2l/min的速率通入压缩空气。
[0034]
回收金属镓:将经过熔炼后得到的浮渣加入到浓度为150g/l的naoh溶液(浮渣与naoh溶液的质量比为1:20)中浸出,在80℃浸出4h后,过滤得到浸出液(滤液),然后通过电解工艺回收金属镓:将浸出液中的naoh 浓度调节为150g/l,阴、阳极均选不锈钢,电流密度1000a/m2,电解温度 25℃,通过电沉积得到纯度为99.99%金属镓。
[0035]
回收金属银:通过电解工艺回收金属银,经过熔炼后得到的银锭直接作为阳极,钛板作为阴极,浓度为100g/l的硝酸银溶液作为电解液,电解液温度35℃,电解液中硝酸浓度6g/l,电流密度为700a/m2,经过电解得到纯度为99.999%金属银粉。
[0036]
实施例2
[0037]
称取银镓靶材切削料100g,然后加入碳酸钠11g和氢氧化钠0.2g混合均匀后进行熔炼:将混合物置于1100℃的环境中焙烧6h,同时以2l/min的速率通入氧气。
[0038]
回收金属镓:将经过熔炼后得到的浮渣加入到浓度为180g/l的naoh溶液(浮渣与naoh溶液的质量比为1:15)中浸出,在95℃浸出4h后,过滤得到浸出液(滤液),然后通过电
解工艺回收金属镓:将浸出液中的naoh 浓度调节为200g/l,阴、阳极均选不锈钢,电流密度1500a/m2,电解温度 40℃,通过电沉积得到纯度为99.99%金属镓。
[0039]
回收金属银:通过电解工艺回收金属银,经过熔炼后得到的银锭直接作为阳极,钛板作为阴极,浓度为110g/l的硝酸银溶液作为电解液,电解液温度35℃,电解液中硝酸浓度6g/l,电流密度为750a/m2,经过电解得到纯度为99.999%金属银粉。
[0040]
实施例3
[0041]
称取银镓靶材切削料100g,然后加入碳酸钠9g和氢氧化钠0.45g混合均匀后进行熔炼:将混合物置于1200℃的环境中焙烧4h,同时以4l/min的速率通入压缩空气。
[0042]
回收金属镓:将经过熔炼后得到的浮渣加入到浓度为200g/l的naoh溶液(浮渣与naoh溶液的质量比为1:10)中浸出,在80℃浸出6h后,过滤得到浸出液(滤液),然后通过电解工艺回收金属镓:将浸出液中的naoh 浓度调节为200g/l,阴、阳极均选不锈钢,电流密度1800a/m2,电解温度 60℃,通过电沉积得到纯度为99.992%金属镓。
[0043]
回收金属银:通过电解工艺回收金属银,经过熔炼后得到的银锭直接作为阳极,钛板作为阴极,浓度为120g/l的硝酸银溶液作为电解液,电解液温度35℃,电解液中硝酸浓度8g/l,电流密度为800a/m2,经过电解得到纯度为99.999%金属银粉。
[0044]
实施例4
[0045]
称取银镓靶材切削料100g,然后加入碳酸钠9g和氢氧化钠0.9g混合均匀后进行熔炼:将混合物置于1150℃的环境中焙烧5h,同时以4l/min的速率通入压缩空气。
[0046]
回收金属镓:将经过熔炼后得到的浮渣加入到浓度为180g/l的naoh溶液(浮渣与naoh溶液的质量比为1:10)中浸出,在90℃浸出5h后,过滤得到浸出液(滤液),然后通过电解工艺回收金属镓:将浸出液中的naoh 浓度调节为180g/l,阴、阳极均选不锈钢,电流密度500a/m2,电解温度 40℃,通过电沉积得到纯度为99.99%金属镓。
[0047]
回收金属银:通过电解工艺回收金属银,经过熔炼后得到的银锭直接作为阳极,钛板作为阴极,浓度为120g/l的硝酸银溶液作为电解液,电解液温度45℃,电解液中硝酸浓度7g/l,电流密度为750a/m2,经过电解得到纯度为99.999%金属银粉。
[0048]
对比例1
[0049]
称取银镓靶材切削料100g,以浓度为2mol/l的硝酸将其浸出,然后加入hcl或nacl得到agcl沉淀,将agcl沉淀过滤(过滤后收集滤液)、洗涤、烘干后,加入碳酸钠(碳酸钠的重量为烘干后的agcl沉淀重量的40%) 与agcl沉淀混合均匀,将混合物置于1050℃的环境中焙烧5h,得到银锭。通过电解工艺回收金属银:将得到银锭作为阳极,钛板作为阴极,浓度为 120g/l硝酸银作为电解液,电解液温度45℃,电解液中硝酸浓度7g/l,电流密度为750a/m2,经过电解得到99.999%的银粉。
[0050]
在沉银后的滤液中加入32%的naoh溶液将溶液的ph调到9,然后过滤沉淀,然后通过电解工艺回收金属镓:将naoh溶液的浓度调节为180g/l,阴、阳极均选不锈钢,电流密度500a/m2,电解液温度40℃,经过电沉积得到纯度为99.99%的金属镓。
[0051]
在实施例1
‑
4和对比例1中,纯度、杂质含量的测试根据本行业或本领域公知的标准确定,其中,回收得到的金属银中杂质的测试结果如表1所示。
[0052]
表1实施例1
‑
4和对比例1得到的金属银中的杂质及其含量(单位:ppm)
[0053] pdcufepbsnbizningacrcdnimnca
实施例1131<1<1<1<1<1<1<1<1<1<1<1实施例231<1<1<1<1<1<1<1<1<1<1<1<1实施例322<1<1<1<1<1<1<1<1<1<1<1<1实施例4<111<1<1<1<1<1<1<1<1<1<1<1对比例1<121<1<1<1<1<1<1<1<1<1<1<1
[0054]
从实施例、对比例的过程以及表1的数据中可以看出,对比例1采用的是湿法工艺,实施例1至4采用的是火法与湿法结合工艺,虽然两种工艺得到的金属银纯度基本相同。但是在纯湿法工艺过程中,氯化银需要经过多次洗涤,氯化银熔炼成银锭后通过电解回收金属银,而氯离子对设备腐蚀严重,且沉银过程及熔炼过程都有少量银在废水或废渣中残留。而火法与湿法结合工艺流程较短,废水少,银、镓回收循环速度快,产品纯度高,废液废渣中贵金属残留较少。
[0055]
以上所述,仅是本公开的示例,并非对本公开做任何形式的限制,虽然本公开以较佳实施例揭示如上,然而并非用以限制本公开,任何熟悉本专业的技术人员,在不脱离本公开技术方案的范围内,利用上述揭示的技术内容做出些许的变动或修饰均等同于等效实施案例,均在本公开技术方案的范围内。
再多了解一些
本文用于企业家、创业者技术爱好者查询,结果仅供参考。