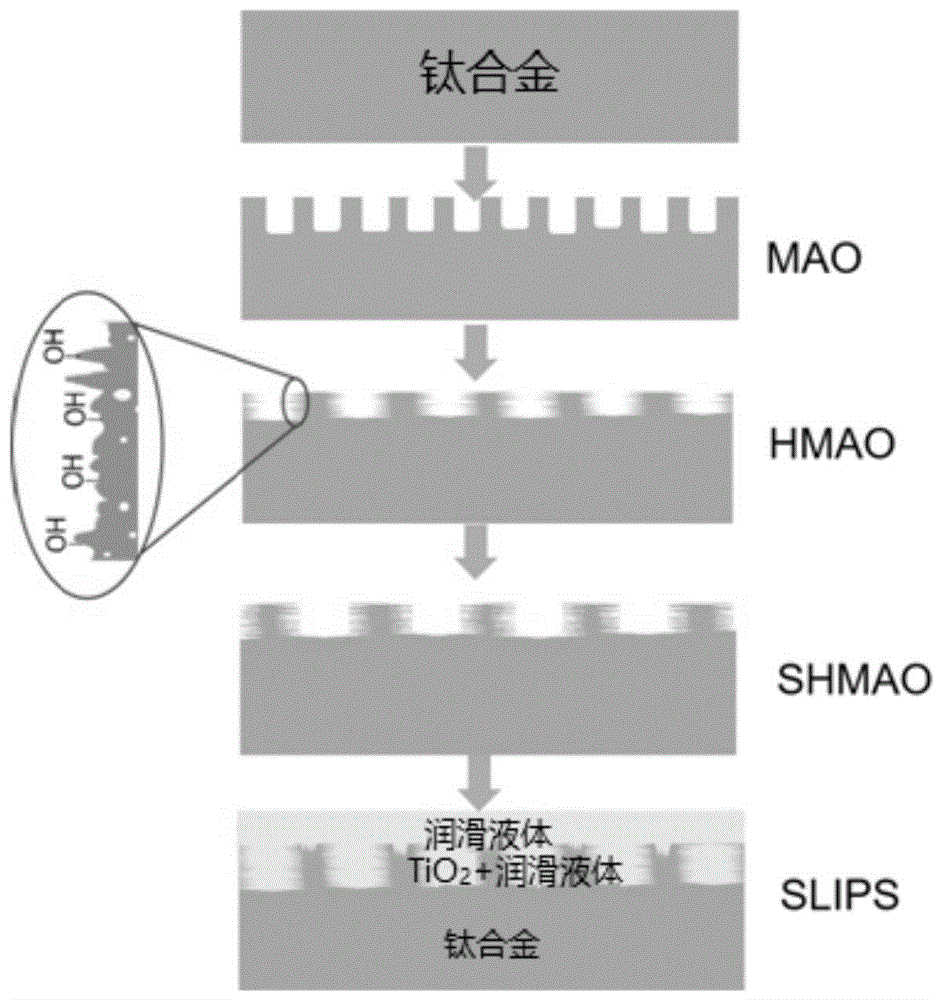
本发明涉及金属材料表面改性
技术领域:
,尤其涉及一种钛合金表面防污损的复合涂层及其制备方法和应用。
背景技术:
:钛金属素有“海洋金属”之称,具有优良的耐海水腐蚀性和综合力学性能,且在海水中几乎不发生腐蚀溶出,对海洋生态环境几乎不产生污染,因而被认为是一种非常理想的绿色海洋工程材料。然而,钛金属具有良好的生物相容性,是海洋生物理想的栖息之地,导致钛金属在海洋工程应用中的生物污损问题比其他金属材料更为严重。海洋生物污损形成对海洋工业具有极为严重的危害,不仅会造成海洋工程装备服役性能的下降,甚至会使装备损坏等严重影响。开发高效的针对钛金属表面海洋生物防护涂层,对于实现海洋工程设施中钛金属海洋装备的长寿命化具有非常重要意义。为了提高钛合金表面的防海洋生物污损的能力,相关技术主要针对用于涂覆钛合金表面的涂料进行改进,例如开发杀生物型防污涂料、释放型防污涂料和阻止型防污涂料;或者对钛合金表面进行改性。其中,对涂料进行改进的方法主要有:(1)通过在钛金属表面进行甜菜碱类分子和银化学修饰实现防污抗菌,但是这种方法涉及银贵金属,价格昂贵,工艺复杂不适宜海洋领域大规模应用。(2)在防污涂层中加入一种或多种含重金属的生物杀灭剂(如氧化亚铜、吡啶硫酮铜(吡硫鎓铜)、吡啶硫酮锌(吡硫鎓锌)和亚乙基双(二硫代氨基甲酸锌)(代森锌))进行杀菌防污。但是该防污涂层含有有毒金属离子,会对海洋生物和环境造成危害。(3)制备低表面能涂料。这类涂料虽然具有环境友好性以及较好的防海洋生物附着的性能,但是此类涂料在金属表面尤其是在钛合金等惰性金属表面存在结合力差,服役过程容易与基体材料剥离等缺点,导致防污寿命和效果大大降低。而对钛合金表面进行改性的方法包括:(1)利用皮秒激光与飞秒激光的综合作用形成超亲水-超疏水(或亲水-超疏水、疏水-超疏水)材料表面形貌,实现复合浸润性,能够减小待处理材料在水中的阻力,同时起到防污作用,但是皮秒激光与飞秒激光制备微纳结构的方法具有价格昂贵、无法在大工件表面制备等特点限制了其在海洋防污方面的应用。(2)在钛及钛合金板采用热氧化处理,利用含锶、钙、镁离子等钛酸盐化学反应形成微纳表面。此类方法需要添加多种离子,还涉及马弗炉高温处理等高能耗工艺,形成的是单层膜,且膜层较薄仅有纳米级别厚度,而较薄的膜层在服役过程中容易与基材剥离脱落,同时耐蚀性非常差,因此这种热氧化处理方法制备的膜层难以适用于海洋恶劣的环境。(3)采用微弧氧化在钛合金表面形成保护层,虽然该保护层具有一定的防污效果,但是相关技术采用的电解液普遍含有毒金属离子或试剂,会对海洋生物和环境及人体造成很大危害。(4)在对钛合金表面进行微弧氧化后,采用由二硫化钼和环氧树脂组成的混合物浸润微弧氧化涂层表面,然后固化形成固体膜层。其中二硫化钼和环氧树脂摩擦系数较大,难以在有机液体中均匀分散,而且二硫化钼和环氧树脂混合物并不具有憎有机或生物液体等各种液体的性能,难以实现超润滑防雾效果,不能应用于在海洋环境防污中。简言之,在钛合金防海洋生物污损方面,相关技术存在对生物及环境造成危害,涂层与基材结合力差,服役过程中容易与基材剥离脱落,耐磨耐蚀性差,或加工价格昂贵、无法大规模工业生产等等问题,因此开发一种防海洋生物污损效果好、环境友好、涂层与基材结合力好、工艺简单成本低、可以规模应用的技术对于海洋工业具有重要意义。技术实现要素:本发明旨在至少解决现有技术中存在的技术问题之一。为此,本发明提出一种钛合金表面防污损的复合涂层,具有长效的防海洋生物污损能力,同时与钛基材结合力强,具有良好的耐磨耐腐蚀能力。本发明还提出所述复合涂层的制备方法和应用。具体地,本发明采取如下的技术方案:本发明的第一方面是提供一种复合涂层,所述复合涂层包括与钛合金表面结合的二氧化钛多孔层,以及覆盖所述二氧化钛多孔层的润滑层,所述二氧化钛多孔层的孔隙内填充有润滑液体。根据本发明第一方面的复合涂层,至少具有如下有益效果:本发明的复合涂层中,二氧化钛多孔层与钛合金表面具有很强的结合力,润滑层能赋予复合涂层优异的防污能力,同时二氧化钛多孔层的孔隙可以通过毛细管作用固定丰富的润滑液体,可实现长效防污损的效果。在本发明的一些实施方式中,所述二氧化钛多孔层的孔隙的内壁与润滑液体之间存在疏水膜层。通过疏水膜层提高润滑液体与基材的相容性,同时对锁住在其中的润滑液体具有稳定作用,进而提高防污损复合涂层的稳定性,增强复合涂层的长期防污损能力。在本发明的一些实施方式中,所述二氧化钛多孔层的孔隙率为10%~15%。在本发明的一些实施方式中,所述二氧化钛多孔层的厚度为5~15μm。在本发明的一些实施方式中,所述润滑层由所述润滑液体形成(形成润滑层的润滑液体与填充在二氧化钛多孔层中的润滑液体相同)。在本发明的一些实施方式中,所述润滑层的厚度为8~10μm。在本发明的一些实施方式中,所述疏水膜层是疏水试剂与二氧化钛多孔层表面的羟基活性基团反应得到的有机膜层,所述疏水性试剂只要具有疏水性能同时与润滑液体具有良好相容性即可,包括但不限于二甲基二氯硅烷、1h,1h,2h,2h-全氟十烷基三乙氧基硅烷、1h,1h,2h,2h-全氟癸基三乙氧基硅烷、1h,1h,2h,2h-全氟辛基三乙氧基硅烷、1h,1h,2h,2h-全氟癸基三氯硅烷、十七氟癸基三甲氧基硅烷、十八烷基胺中的任意一种或多种。在本发明的一些实施方式中,步骤(3)中,所述润滑液体为具有强憎水憎油憎有机液体等液体能力的润滑液体,包括但不限于dupontkrytoxgpl103全氟油、全氟聚醚、二甲基硅油中的任意一种或多种。本发明的第二方面是提供一种钛合金表面防污损的复合涂层的制备方法,包括如下步骤:(1)对钛合金表面进行氧化处理,得到样品1;(2)将所述样品1浸泡于碱性溶液中,进行水热反应,得到样品2;(3)对所述样品2进行表面疏水修饰,然后采用润滑液体进行浸润,在钛合金表面形成复合涂层。根据本发明第二方面的钛合金表面防污损的复合涂层的制备方法,至少具有如下有益效果:本发明首先对钛合金表面进行氧化处理,在钛合金表面形成二氧化钛多孔结构,可作为中间连接层,增强与基材的结合力并提高耐磨性,有利于延长使用寿命;而且该二氧化钛多孔结构具有很大的内比表面积和内部存储空间。在此基础上进行水热反应,在二氧化钛多孔结构的巨大内比表面积和内部存储空间的基础上,原位生成了二级纳米结构,可以在浸润过程中通过毛细管作用锁定并储存更加大量的润滑液体,实现表面超润滑效果,使钛合金表面具有很好的防海洋生物污损能力;同时微纳多孔结构对锁住在其中的润滑液体具有稳定作用,可达到更长久防污损的效果;同时,水热处理可以在二氧化钛多孔结构表面原位形成更多的活性基团,有利于后续进行表面疏水修饰和润滑液体浸润,提高防污损能力。在本发明的一些实施方式中,步骤(1)中,所述氧化处理的方法采用微弧氧化。采用微弧氧化方法可以形成具有多孔结构的二氧化钛层,该二氧化钛层一方面可作为中间连接层,增强与基材的结合力并提高耐磨性;另一方面可以提供大内比表面积和内部存储空间。同时,微弧氧化相较普通的热氧化能够形成更厚的多层膜(热氧化处理只能形成几十纳米至200~300的纳米厚单层膜),增加了涂层厚度和耐蚀性,与基材具有更强的结合力,并为后续对涂层进行超润滑表面处理以及实现长期防污效果提供基础。在本发明的一些实施方式中,所述微弧氧化采用的电解液的组成包括:硅酸钠、六偏磷酸钠、甘油、氟化钾,ph为10~13。在本发明的一些实施方式中,所述电解液的组成包括:硅酸钠10~15g/l、六偏磷酸钠0.5~5g/l、甘油1~5g/l、氟化钾1~5g/l。在本发明的一些实施方式中,所述电解液的组成包括:硅酸钠10~12g/l、六偏磷酸钠0.5~2g/l、甘油2~4g/l、氟化钾2~3g/l。在本发明的一些实施方式中,所述电解液的ph采用常见的碱进行调节,例如氢氧化钠、氢氧化钾等,其在电解液中的浓度为1~5g/l。在本发明的一些实施方式中,所述微弧氧化采用的工艺参数为:电流密度30~800a/dm2,占空比为5~20%,频率为500~900hz,终止电压为200~600v,反应时间为2~30min,温度≤30℃。在本发明的一些实施方式中,所述微弧氧化采用的工艺参数为:电流密度30~800a/dm2,占空比为5~9%,频率为500~900hz,终止电压为250~400v。在本发明的一些实施方式中,所述微弧氧化在恒流模式下进行。在本发明的一些实施方式中,步骤(1)中,所述钛合金包括ta1、ta2、tc4、ti60、tc20/21/22/23等中的任意一种或多种。在本发明的一些实施方式中,在氧化处理前,还包括对钛合金进行表面粗化、清洁的步骤。其中表面粗化可采用喷砂的方法,清洁可采用丙酮、乙醇进行超声清洗30~60min。清洁后干燥,然后进行氧化处理。在本发明的一些实施方式中,步骤(2)中,所述碱性溶液为氢氧化钠溶液。在碱性溶液中进行水热反应,可以在微弧氧化形成的二氧化钛多孔结构表面原位生长纳米结构,同时增加更多羟基活性基团,有利于后续表面疏水修饰。在本发明的一些实施方式中,步骤(2)中,所述氢氧化钠溶液的浓度为1~5wt%。在本发明的一些实施方式中,步骤(2)中,所述水热反应的温度为30~180℃,时间为0.5~10h。在本发明的一些实施方式中,步骤(3)中,所述表面疏水修饰方法可以为,将所述样品2浸泡在疏水性试剂中进行反应1~4h。在本发明的一些实施方式中,所述疏水性试剂只要具有疏水性能同时与润滑液体具有良好相容性即可,包括但不限于二甲基二氯硅烷、1h,1h,2h,2h-全氟十烷基三乙氧基硅烷、1h,1h,2h,2h-全氟癸基三乙氧基硅烷、1h,1h,2h,2h-全氟辛基三乙氧基硅烷、1h,1h,2h,2h-全氟癸基三氯硅烷、十七氟癸基三甲氧基硅烷、十八烷基胺中的任意一种或多种。在本发明的一些实施方式中,所述样品2浸泡在疏水性试剂反应1~4h后进行加热处理,加热的温度为100~150℃,加热时间为1~4h。在本发明的一些实施方式中,步骤(3)中,所述润滑液体为具有强憎水憎油憎有机液体等液体能力的润滑液体,包括但不限于dupontkrytoxgpl103全氟油、全氟聚醚、二甲基硅油中的任意一种或多种。本发明的第三方面是一种钛基材料,包括钛合金,所述钛合金的表面具有上述复合涂层。本发明的第四方面是提供上述钛基材料在制备海洋设备、航空设备、生物医学设备、陆运交通工具、文体用品中的应用,尤其是提供上述钛基材料在制备海洋设备中的应用。相对于现有技术,本发明具有如下有益效果:本发明利用微弧氧化在钛合金基材上制备多孔陶瓷中间连接层,具有与基材结合力强,耐磨性好的特点;通过原位生长复合陶瓷微纳多孔结构,提高了涂层的稳定性,增加了涂层厚度,并使涂层与基体结合力大幅提高;采用润滑液体进行浸润,可实现超润滑效果,从而达到防止污损生物附着的目的。因此,本发明的复合涂层具有与基材结合力强,耐磨性好,使用寿命长的特点,表面防污损能力强,能够防止生物附着。本发明的制备方法操作简单,工艺可靠,制备费用低廉,所用化学试剂无环境危害,可进行大批量工业化生产。附图说明图1为实施例1的复合涂层的制备流程图,其中mao表示微弧氧化,hmao表示微弧氧化后水热处理,shmao表示疏水化处理;slips表示超润滑的复合涂层;图2为实施例1的复合涂层(a)和未经处理的ta2钛合金(b)表面生物附着后的激光共聚焦扫描显微图及其附着率对比图(c);图3为实施例2组1的陶瓷多孔结构的表面(a)和横截面(b)在放大1000倍下的扫描电镜图;图4为实施例2组1的陶瓷多孔结构的表面在放大7000倍下的扫描电镜图;图5为实施例2组1的陶瓷多孔结构表面生物附着后的激光共聚焦扫描显微图;图6实施例3组1的陶瓷复合微纳多孔结构的扫描电镜图;图7实施例3组2的陶瓷复合微纳多孔结构的扫描电镜图;图8实施例3组3的陶瓷复合微纳多孔结构的扫描电镜图;图9实施例3组4的陶瓷复合微纳多孔结构的扫描电镜图。具体实施方式以下将结合实施例对本发明的构思及产生的技术效果进行清楚、完整地描述,以充分地理解本发明的目的、特征和效果。显然,所描述的实施例只是本发明的一部分实施例,而不是全部实施例,基于本发明的实施例,本领域的技术人员在不付出创造性劳动的前提下所获得的其他实施例,均属于本发明保护的范围。实施例1一种钛合金表面防污损的复合涂层的制备方法,其制备流程如图1所示,具体包括如下步骤:(1)前处理采用80目的棕刚玉砂粒,利用喷砂机对ta2钛合金试样件进行表面均匀喷砂,使得ta1钛合金试样件表面形成均匀的粗糙表面。然后依次使用丙酮,乙醇进行超声清洗30min左右进行除油清洁表面处理,接着真空烘干。(2)微弧氧化表面处理在电解液中,以上述前处理后的样品作为阳极,304不锈钢作为阴极,采用30kw双极脉冲微弧氧化电源,进行微弧氧化处理,在钛合金表面形成陶瓷多孔结构。其中电解液的组成为:硅酸钠12g/l,氢氧化钠2g/l,六偏磷酸钠2g/l,甘油2g/l,氟化钾3g/l,ph=12.6。微弧氧化采用恒流模式,100a/dm2,占空比为5%,频率为800hz,终止电压为400v,反应温度用循环水冷交换器进行控温,温度控制在30℃以下。微弧氧化处理好的样品用去离子水进行浸泡清洗30min左右,然后用真空烘箱烘干。(3)原位水热反应将上述微弧氧化处理好的样品垂直放置于盛有5wt%氢氧化钠溶液的反应釜中,氢氧化钠溶液没过样品。在180℃下水热反应0.5h,形成陶瓷复合微纳多孔结构。反应结束后将样品取出,用去离子水进行浸泡清洗30min左右。(4)表面疏水修饰将步骤(3)处理好的样品完全浸渍在1h,1h,2h,2h-全氟辛基三乙氧基硅烷中进行反应4h,然后加热到150℃保持4h,从而实现表面疏水修饰。(5)润滑浸润使步骤(4)处理好的样品在dupontkrytoxgpl103全氟油中浸泡24h,然后竖立样品以除去多余润滑油,完成钛合金表面超润滑的复合涂层的制备。经过上述方法制得的复合涂层包括与钛合金表面结合的二氧化钛多孔层,以及覆盖所述二氧化钛多孔层的由润滑液体组成的润滑层,所述二氧化钛多孔层的孔隙内填充有润滑液体,而且二氧化钛多孔层的孔隙的内壁与润滑液体之间存在疏水膜层,如图1的slips所示。经检测,二氧化钛多孔层和润滑层的厚度均约为10μm。防污损附着性能检测:(1)生物膜是大型生物污损形成的重要前提,而生物膜主要由细菌和藻类组成。海洋小球藻是海洋藻类中最重要和最典型的微生物之一,因此以小球藻作为海洋藻类污损生物代表进行生物污损附着实验,对复合涂层的防污损附着性能进行检测。将本实施例的表面形成复合涂层的钛合金在海洋小球藻中进行挂样7天,然后采用激光共聚焦扫描显微镜进行观察,并用imagej软件进行表面附着率统计。同时以未进行任何处理的ta2钛合金进行比较,结果如图2所示。根据图2可以看出,挂样7天后,未处理的ta2钛合金表面存在附着有大量海洋小球藻,附着率接近80%。而形成复合涂层后,几乎没有观察到海洋小球藻的附着,附着率仅<0.05%,说明该复合涂层具有优异的防海洋生物附着能力。(2)将表面形成复合涂层的钛合金浸泡在海水中,在冲刷速度为120r/min条件下模拟海水冲刷。冲刷120min后复合涂层表面的水滴滑动速度为20m/s,反映出该复合涂层在经过海水长时间冲刷后依然具有很好的防污损能力,具有长效防污损能力;同时,经过长时间冲刷后,复合涂层能够依然保持良好的防污损能力,也反映出该复合涂层没有因冲刷而发生明显的磨损或涂层剥离,具有很好的耐磨性且与基体的结合力强。下面通过多组实验对制备复合涂层过程中各步骤形成的结构及性能进行研究。实施例2利用微弧氧化技术,在钛合金表面制备陶瓷多孔结构,具体包括如下步骤:(1)前处理采用80目的棕刚玉砂粒,利用喷砂机对ta1钛合金试样件进行表面均匀喷砂,使得ta1钛合金试样件表面形成均匀的粗糙表面。然后依次使用丙酮,乙醇进行超声清洗30min左右进行除油清洁表面处理,接着真空烘干。(2)微弧氧化表面处理在电解液中,以上述前处理后的样品作为阳极,304不锈钢作为阴极,采用30kw双极脉冲微弧氧化电源,进行微弧氧化处理,在钛合金表面形成陶瓷多孔结构。其中电解液组成为:电解液一:硅酸钠12g/l,氢氧化钠2g/l,六偏磷酸钠2g/l,甘油2g/l,氟化钾3g/l,ph=12.6;电解液二:硅酸钠10g/l,氢氧化钠4g/l,六偏磷酸钠0.5g/l,甘油4g/l,氟化钾3g/l,ph=12.6。微弧氧化采用恒流模式,具体的工艺参数见表1。反应温度用循环水冷交换器进行控温,温度控制在30℃以下。微弧氧化处理好的样品用去离子水进行浸泡清洗30min左右,然后用真空烘箱烘干。结构表征:(1)经检测,不同工艺下制得的陶瓷多孔结构的孔隙率如下表1所示。表1.微弧氧化工艺参数以及陶瓷多孔结构的孔隙率根据表1中组1~7可以看出,通过微弧氧化可以在钛合金表面形成多孔结构,孔隙率可高达14.694%。同时,通过调整微弧氧化工艺参数,可以改变多孔结构的孔隙率,控制在12%~15%之间;从组5和组6可以看出,占空比、终止电压过高会显著降低孔隙率。(2)组1的经过微弧氧化表面处理形成的陶瓷多孔结构的扫描电镜图如图3和4所示[图3(b)的截面图中加入封样树脂对陶瓷多孔结构进行封样,以便检测]。从图3和图4可以看出陶瓷多孔结构(即图3中的微弧氧化层)具有丰富的较均匀的孔隙,孔隙大小主要分布在0.5~4μm之间,陶瓷多孔结构的厚度约10μm。防污损附着性能检测:将组1的经过微弧氧化表面处理的钛合金在海洋小球藻中进行挂样7天,然后采用激光共聚焦扫描显微镜进行观察,并用imagej软件进行表面附着率统计,结果如图5所示。根据图5可以看出,挂样7天后,微弧氧化表面处理后的钛合金表面存在附着有大量海洋小球藻。同时,将图5与图2(b)进行比较可以发现,图2(b)中的海洋小球附着率比微弧氧化表面处理后的钛合金表面的海洋小球藻的附着率明显降低,,说明在微弧氧化表面处理后增加水热反应、表面疏水修饰和润滑浸润的超润滑防污策略能阻止生物污损形成。实施例3利用微弧氧化技术,在钛合金表面制备陶瓷多孔结构,然后在陶瓷多孔结构中原位生长陶瓷复合微纳多孔结构,具体包括如下步骤:(1)前处理采用80目的棕刚玉砂粒,利用喷砂机对ta1钛合金试样件进行表面均匀喷砂,使得ta1钛合金试样件表面形成均匀的粗糙表面。然后依次使用丙酮,乙醇进行超声清洗30min左右进行除油清洁表面处理,接着真空烘干。(2)微弧氧化表面处理在电解液中,以上述前处理后的样品作为阳极,304不锈钢作为阴极,采用30kw双极脉冲微弧氧化电源,进行微弧氧化处理,在钛合金表面形成陶瓷多孔结构。其中电解液采用实施例2的电解液一。微弧氧化采用恒流模式,具体的工艺参数见表2。表2.实施例3的微弧氧化工艺参数实施例3电解液电解液一电流密度(a/dm2)200占空比5%频率(hz)500终止电压(v)300反应温度用循环水冷交换器进行控温,温度控制在30℃以下。微弧氧化处理好的样品用去离子水进行浸泡清洗30min左右,然后用真空烘箱烘干。(3)原位水热反应将上述微弧氧化处理好的样品垂直放置于盛有氢氧化钠溶液的反应釜中,氢氧化钠溶液没过样品,进行水热反应,形成陶瓷复合微纳多孔结构。其中氢氧化钠溶液的质量浓度以及水热反应的时间、温度见下表3。表3.水热反应参数反应结束后将样品取出,用去离子水进行浸泡清洗30min左右。组1~组4的陶瓷复合微纳多孔结构的扫描电镜图依次如图6~9所示。从图6~9可以看出,水热反应后形成的陶瓷复合微纳多孔结构保留了微弧氧化形成的陶瓷多孔结构的多孔形貌,并且在表面原位生长出纳米柱阵列、纳米颗粒或者纳米线等二级纳米结构。这些在表面原位生长出的纳米柱阵列、纳米颗粒或者纳米线等二级纳米结构有利于增加二氧化钛与疏水试剂的反应活性位点,有利于增强后续润滑液体与陶瓷复合微纳结构之间毛细管力作用,以及固定更多的润滑液体,同时这些结构还能够对锁住在其中的润滑液体具有稳定作用,提高防污损复合涂层的稳定性,从而实现复合涂层的长效防污损效果。实施例4利用微弧氧化技术,在钛合金表面制备陶瓷多孔结构,然后在陶瓷多孔结构中原位生长陶瓷复合微纳多孔结构,接着进行表面疏水修饰,具体包括如下步骤:(1)前处理采用80目的棕刚玉砂粒,利用喷砂机对ta1钛合金试样件进行表面均匀喷砂,使得ta1钛合金试样件表面形成均匀的粗糙表面。然后依次使用丙酮,乙醇进行超声清洗30min左右进行除油清洁表面处理,接着真空烘干。(2)微弧氧化表面处理在电解液中,以上述前处理后的样品作为阳极,304不锈钢作为阴极,采用30kw双极脉冲微弧氧化电源,进行微弧氧化处理,在钛合金表面形成陶瓷多孔结构。其中电解液采用实施例1的电解液一。微弧氧化采用恒流模式,具体的工艺参数见表4。表4.实施例4的微弧氧化工艺参数实施例4电解液电解液一电流密度(a/dm2)100占空比5%频率(hz)800终止电压(v)350反应温度用循环水冷交换器进行控温,温度控制在30℃以下。微弧氧化处理好的样品用去离子水进行浸泡清洗30min左右,然后用真空烘箱烘干。(3)原位水热反应将上述微弧氧化处理好的样品垂直放置于盛有5wt%氢氧化钠溶液的反应釜中,氢氧化钠溶液没过样品。在180℃下水热反应0.5h,形成陶瓷复合微纳多孔结构。反应结束后将样品取出,用去离子水进行浸泡清洗30min左右。(4)表面疏水修饰将步骤(3)处理好的样品完全浸渍在1h,1h,2h,2h-全氟辛基三乙氧基硅烷中反应4h,然后加热到150℃保持4h,从而实现表面疏水修饰。经检测,经过本实施例的方法处理得到的样品的表面的静态接触角为152.1°。相比之下,若在本实施例的方法中省去步骤(3),也就是直接对微弧氧化后的样品进行表面疏水修饰,得到的样品的表面的静态接触角为128.07°。对比例1本对比例与实施例1的不同之处在于:本对比例相较实施例1省去原位水热反应步骤,即在微弧氧化表面处理后直接进行表面疏水修饰和润滑浸润。将本对比例处理后的钛合金浸泡在海水中,按照实施例1的测试方法模拟海水冲刷。结果显示,在冲刷速度为120r/min条件下被海水冲刷120min后,复合涂层表面的水滴滑动速度为8.3m/s,远远小于实施例1的20m/s,说明不进行原位水热反应步骤,无法实现长效防污损效果。对比例2本对比例与实施例1的不同之处在于:本对比例相较实施例1省去表面疏水修饰步骤,即在原位水热反应后直接进行润滑浸润。本对比例制备的涂层滑动性较差,无法进行模拟海水冲刷实验。即,将本对比例处理后的钛合金浸泡在海水中,在冲刷速度为120r/min条件下被海水冲刷120min后,水滴无法在涂层表面滑动,反映出根据本对比例的方法所得涂层的防污损能力较差。这可能是由于在原位水热反应后直接进行润滑浸润时,由于润滑液体与基体以及原位水热反应形成的陶瓷复合微纳多孔结构之间的相容性较差,在没有疏水试剂存在情况下,陶瓷复合微纳多孔结构的保持和稳定润滑液体性能差,经过海水冲刷后,润滑液体流失从而无法发挥润滑作用,因此水滴无法在涂层表面滑动,防污损性能差。上述实施例为本发明较佳的实施方式,但本发明的实施方式并不受上述实施例的限制,其他的任何未背离本发明的精神实质与原理下所作的改变、修饰、替代、组合、简化,均应为等效的置换方式,都包含在本发明的保护范围之内。当前第1页12
再多了解一些
本文用于企业家、创业者技术爱好者查询,结果仅供参考。