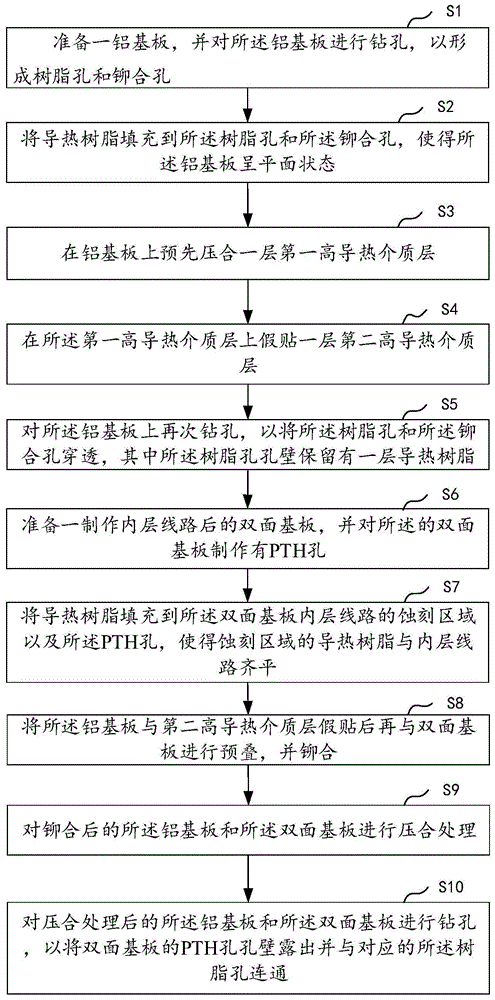
本发明涉及电路板生产工艺领域,尤其涉及一种适用于插件方式耐高压的金属基线路板制作方法及线路板。
背景技术
目前有产品设计要求,双面基板需要与铝基板相压合,且导热率要求大于8W/m.k,介电层耐电压DC大于5000V,且需要使用PTH上插件的方式;但就目前的制作方法及材料,导热率低于4W/m.k,且单面双层(多层)铝基线路板,钻孔后孔壁为金属铝,如果使用有插脚的元器件,必然造成元器件短路,导致元器件贴装方式受限,此类产品常规制作方法只能实现贴片方式安装元器件。
鉴于目前的产品制作方法及材料无法满足产品的要求,提出一种适用于插件方式耐高压的金属基线路板制作方法。
技术实现要素:
本发明的目的是提供一种适用于插件方式耐高压的金属基线路板制作方法及线路板,旨在解决金属基线路板无法使用插件方式将元器件与金属基线路板相连接的问题。
为解决上述技术问题,本发明的目的是通过以下技术方案实现的:提供一种适用于插件方式耐高压的金属基线路板制作方法,包括:
准备一铝基板,并对所述铝基板进行钻孔,以形成树脂孔和铆合孔;
将导热树脂填充到所述树脂孔和所述铆合孔,使得所述铝基板呈平面状态;
在铝基板上预先压合一层第一高导热介质层;
在所述第一高导热介质层上假贴一层第二高导热介质层;
对所述铝基板上再次钻孔,以将所述树脂孔和所述铆合孔穿透,其中所述树脂孔孔壁保留有一层导热树脂;
准备一制作内层线路后的双面基板,并对所述的双面基板制作有PTH孔;
将导热树脂填充到所述双面基板内层线路的蚀刻区域以及所述PTH孔,使得蚀刻区域的导热树脂与内层线路齐平;
将与所述第二高导热介质层假贴后的所述铝基板再与双面基板进行预叠,并铆合;
对铆合后的所述铝基板和所述双面基板进行压合处理;
对压合处理后的所述铝基板和所述双面基板进行钻孔,以将双面基板的PTH孔孔壁露出并与对应的所述树脂孔连通。
进一步的,所述在铝基板上预先压合一层第一高导热介质层,包括:
将所述第一高导热介质层其中一面的保护膜撕掉;
将所述第一高导热介质层假贴于所述铝基板上;
将所述第一高导热介质层另一面的保护膜撕掉;
将铜箔与假贴在所述铝基板上的所述第一高导热介质层进行压合处理;
对压合后的所述铝基板上的所述铜箔进行线路蚀刻处理,以将所述铜箔蚀刻掉。
进一步的,所述在所述第一高导热介质层上假贴一层第二高导热介质层,包括:
将所述第二高导热介质层其中一面的保护膜撕掉;
将所述第二高导热介质层假贴于第一高导热介质层上;
所述对所述铝基板上再次钻孔,以将所述树脂孔和所述铆合孔穿透之后,包括:
将所述第二高导热介质层另一面的保护膜撕掉。
进一步的,所述第一高导热介质层由无玻纤高导热介质材料制造而成,厚度参数控制在90μm-110μm。
进一步的,所述第二高导热介质层由无玻纤高导热介质材料制造而成,厚度参数控制在140μm-160μm。
进一步的,所述假贴的参数设置为:温度参数控制在110℃-130℃、压力参数控制在5kg/cm2。
进一步的,所述对铆合后的所述铝基板和所述双面基板进行压合处理中的压合的参数设置为:升温速率调整为2-3℃/min,固化时间大于40min。
进一步的,所述对压合处理后的所述铝基板和所述双面基板进行钻孔,以将双面基板的PTH孔孔壁露出并与对应的所述树脂孔连通,包括:
使用CCD钻孔机对压合处理后的所述铝基板和所述双面基板进行钻孔,所述CCD钻孔机中使用的钻刀直径小于所述树脂孔的孔径,以保留所述PTH孔内壁上的所述导热树脂。
进一步的,所述将导热树脂填充到所述树脂孔,使得所述铝基板呈平面状态之前,包括:
在所述铝基板底部贴阻挡膜,以将所述树脂孔塞孔;
所述将导热树脂填充到所述树脂孔,使得所述铝基板呈平面状态之后,包括:
将所述阻挡膜撕除;
对撕膜后的所述铝基板进行削溢胶处理,以削除塞孔时溢到所述铝基板板面的导热树脂;
对削溢胶后的所述铝基板进行磨板处理。
本发明实施例还提供一种适用于插件方式耐高压的金属基线路板,其中:所述线路板由上述的制作方法制得。
本发明实施例提供一种适用于插件方式耐高压的金属基线路板制作方法及线路板,其中制造方法包括:准备一铝基板,并对所述铝基板进行钻孔,以形成树脂孔和铆合孔;将导热树脂填充到所述树脂孔和所述铆合孔,使得所述铝基板呈平面状态;在铝基板上预先压合一层第一高导热介质层;在所述第一高导热介质层上假贴一层第二高导热介质层;对所述铝基板上再次钻孔,以将所述树脂孔和所述铆合孔穿透;准备一制作内层线路后的双面基板,并对所述的双面基板制作有PTH孔;将导热树脂填充到所述双面基板内层线路的蚀刻区域以及所述PTH孔,使得蚀刻区域的导热树脂与内层线路齐平;将与所述第二高导热介质层假贴后的所述铝基板再与双面基板进行预叠,并铆合;对铆合后的所述铝基板和所述双面基板进行压合处理;对压合处理后的所述铝基板和所述双面基板进行钻孔,以将双面基板的PTH孔孔壁露出并与对应的所述树脂孔连通。
本发明实施例通过在树脂孔填充导热树脂,再次对树脂孔和PTH孔返钻并露出PTH孔的方式,使得后期使用有插脚的元器件插入PTH孔时,不会造成元器件短路的现象,进而解决单面多层金属基线路板无法使用插件方式的问题;另一方面,用两次压合方式将无玻纤高导热介质材料压进铝基板和双面基板上,进而解决高导热介质材料压合后厚度簿导致无法耐高压的问题。
附图说明
为了更清楚地说明本发明实施例技术方案,下面将对实施例描述中所需要使用的附图作简单地介绍,显而易见地,下面描述中的附图是本发明的一些实施例,对于本领域普通技术人员来讲,在不付出创造性劳动的前提下,还可以根据这些附图获得其他的附图。
图1为本发明实施例提供的适用于插件方式耐高压的金属基线路板制作方法的流程示意图;
图2为本发明实施例提供的适用于插件方式耐高压的金属基线路板制作方法的子流程示意图。
具体实施方式
下面将结合本发明实施例中的附图,对本发明实施例中的技术方案进行清楚、完整地描述,显然,所描述的实施例是本发明一部分实施例,而不是全部的实施例。基于本发明中的实施例,本领域普通技术人员在没有做出创造性劳动前提下所获得的所有其他实施例,都属于本发明保护的范围。
应当理解,当在本说明书和所附权利要求书中使用时,术语“包括”和“包含”指示所描述特征、整体、步骤、操作、元素和/或组件的存在,但并不排除一个或多个其它特征、整体、步骤、操作、元素、组件和/或其集合的存在或添加。
还应当理解,在此本发明说明书中所使用的术语仅仅是出于描述特定实施例的目的而并不意在限制本发明。如在本发明说明书和所附权利要求书中所使用的那样,除非上下文清楚地指明其它情况,否则单数形式的“一”、“一个”及“该”意在包括复数形式。
还应当进一步理解,在本发明说明书和所附权利要求书中使用的术语“和/或”是指相关联列出的项中的一个或多个的任何组合以及所有可能组合,并且包括这些组合。
结合图1,本发明实施例提供一种适用于插件方式耐高压的金属基线路板制作方法,包括以下步骤:
S1、准备一铝基板,并对铝基板进行钻孔,以形成树脂孔和铆合孔;
S2、将导热树脂填充到树脂孔和铆合孔,使得铝基板呈平面状态;
S3、在铝基板上预先压合一层第一高导热介质层;
S4、在第一高导热介质层上假贴一层第二高导热介质层;
S5、对铝基板上再次钻孔,以将树脂孔和铆合孔穿透,其中所述树脂孔孔壁保留有一层导热树脂;
S6、准备一制作内层线路后的双面基板,并对的双面基板制作有PTH孔;
S7、将导热树脂填充到双面基板内层线路的蚀刻区域以及PTH孔,使得蚀刻区域的导热树脂与内层线路齐平;
S8、将与第二高导热介质层假贴后的铝基板再与双面基板进行预叠,并铆合;
S9、对铆合后的铝基板和双面基板进行压合处理;
S10、对压合处理后的铝基板和双面基板进行钻孔,以将双面基板的PTH孔孔壁露出并与对应的所述树脂孔连通。
本实施例中各步骤的标号仅为方便说明,不代表对各步骤执行顺序的限定,在实际应用时,可以根据需要各步骤执行顺序进行调整,或同时进行,这些调整或者替换均属于本发明的保护范围。
在一实施例中,第一高导热介质层的厚度控制在90μm-110μm。
在一实施例中,第二高导热介质层的厚度控制在140μm-160μm。
在本实施例中,第一高导热介质层和第二高导热介质层均由无玻纤高导热介质材料即为不含玻璃纤维的绝缘制造而成,通过选用导热率可达到12W/m.k的无玻纤高导热介质材料替代玻纤维,使得可以实现导热率大于8W/m.k的设计要求。
由于高导热介质材料流动性底,如果采用一次压合的方式,会导致第一高导热介质层和第二高导热介质层厚度不均、且厚度偏薄,从而无法保证耐高电压能力DC大于5000V;另一方面,根据材料性能,为了实现耐高压能力,介质层厚度需要大于等于250μm。高导热介质内加入了高导热的硼、硅等填料,故凝胶窗口非常窄,通过本实施例中步骤S3和步骤S9,即采用两次压合方式将无玻纤高导热介质材料压进铝基板和双面基板上,进而解决高导热介质材料压合后厚度簿导致无法耐高压的问题。
在步骤S9中的压合的参数设置为:升温速率调整为2-3℃/min,固化时间大于40min,因为双面基板上的蚀刻区域已被导热树脂填充,即双面基板表面处于平面状态,使得第一高导热介质层和第二高导热介质层压合于双面基板时,第一高导热介质层和第二高导热介质层不会产生损耗,进而保证了第一高导热介质层和第二高导热介质层的厚度以及均匀性。在本实施例中,第一高导热介质层和第二高导热介质层的总厚度达到250μm,即可达到耐高压的目的。在实际生产过程中,压合设备的压合参数也可以做相应的调整。
在实际生产过程中,第一高导热介质层还粘接有位于其上下两侧的保护膜,该保护膜起到保护、支撑第一高导热介质层的作用。同理,第二高导热介质层上下两侧也分别粘接有保护膜。
结合图2,步骤S3包括:
S31、将第一高导热介质层其中一面的保护膜撕掉;
S32、将第一高导热介质层假贴于铝基板上;
S33、将第一高导热介质层另一面的保护膜撕掉;
S34、将铜箔与假贴在铝基板上的第一高导热介质层进行压合处理;
S35、对压合后的铝基板上的铜箔进行线路蚀刻处理,以将铜箔蚀刻掉;
S36、将蚀刻处理后的铝基板进行切板处理,以将压合后溢胶即废料边切除;
S37、采用常规磨板流程对铝基板进行磨板处理。
其中,步骤S32通过贴膜机将第一高导热介质层假贴于铝基板上,贴膜机的参数设置为:温度参数控制在110℃-130℃、压力参数控制在5kg/cm2。
由于第一高导热介质层不具有玻璃纤维支撑,直接将第一高导热介质层和第二高导热介质层进行钻孔,以钻出和铝基板中的树脂孔和铆合孔对应的通孔时,钻孔在去除保护膜时容易使得第一高导热介质层破碎,进而导致第一高导热介质层报废,而本申请实施例中,通过将第一高导热介质层假贴在铝基板上,让铝基板作为支撑体,使得对铝基板将树脂孔和铆合孔钻透时,不会导致第一高导热介质层破碎,进而很好的对第一高导热介质层起到保护的作用。
步骤S33中,通过将铜箔压合于第一高导热介质层上,使得第一高导热介质层与铜箔充分结合在一起;压合后的第一高导热介质层上侧有铜箔、下侧有铝基板作为支撑,使得第一高导热介质层在压合过程均匀性佳且不会有损耗。
步骤S34中通过常用的蚀刻机进行蚀刻处理。
更进一步的,步骤S2之前包括:
S11、对钻孔后的铝基板进行磨板处理;
S12、在磨板处理后的铝基板底部贴阻挡膜,防止导热树脂塞树脂孔时,导热树脂流出树脂孔外。
其中,导热树脂通过真空塞孔机塞到树脂孔和铆合孔内,其中导热树脂要求处于饱满、无空洞的状态。
在本实施例中,步骤S2之后包括:
S21、将阻挡膜撕除;
S22、对撕膜后的铝基板进行削溢胶处理,以削除塞孔时溢到铝基板板面的导热树脂;
S23、对削溢胶后的铝基板进行磨板处理。
其中,步骤S22通过砂带机进行削溢胶处理,削溢胶后导热树脂与铝基板板面齐平,无凸起。
在一实施例中,步骤S4包括:
S41、将第二高导热介质层其中一面的保护膜撕掉;
S42、将第二高导热介质层假贴于第一高导热介质层上;
步骤S5之后,还包括以下步骤:
S51、将第二高导热介质层另一面的保护膜撕掉。
本实施例中的假贴处理和步骤S32中使用的设备和参数一致,故不再赘述。
在步骤S7中,通过丝印树脂的方式将双面基板的蚀刻区域填充,使得双面基板表面处于水平状态。通过将导热树脂填充到双面基板内层线路的蚀刻区域,避免二次压合时高导热介质材料渗入蚀刻区域,而导致高导热材料的损耗,从而降低产品耐电压性能。
在一实施例中,步骤S6包括以下步骤:
S61、选择一张芯板,按设计尺寸开料,以形成双面基板;
S62、钻出外围对位孔以及需要制作PTH孔的孔位;
S63、按常规参数将双面基板进行沉铜、电镀;其中,在整板沉铜、电镀的同时,PTH孔的孔位也会镀上铜层,最后形成PTH孔;
S64、用常规制作要求,制作出双面基板的内层线路;其中,双面基板的外层采用菲林保护,不做线路;
S65、按常规制作方法对制作内层线路后的双面基板进行棕化,通过棕化处理提高压合的结合力。
通过步骤S8,控制双面基板的PTH孔与相应的铝基板的树脂孔的对准精度,以利于步骤S9的顺利进行。
在本实施例中,步骤S9之后包括以下步骤:
S91、对压合后的铝基板和双面基板即电路板打出定位孔;其中,采用CCD打靶机进行打孔;
S92、对电路板溢胶即废料边进行铣边处理;
S93、将铝基板板面贴抗蚀高温膜,以保护铝面不被蚀刻;
S94、按常规制作方法,将电路板外层线路制作出;
S95、按常规制作方法,对电路板外层线路面进行防焊制作;
在本实施例中,步骤S10中使用CCD钻孔机对压合处理后的铝基板和双面基板进行钻孔,由于在步骤S8中,通过铆合的方式使得双面基板的PTH孔与相应的树脂孔对应,且树脂孔中的导热树脂在步骤S5中被钻掉,所以只需要对双面基板的PTH孔进行再次钻孔,以将PTH孔内的导热树脂钻掉,进而实现将PTH孔孔壁的镀铜露出,从而使得元件的插脚能够与PTH孔上的镀铜接触导通,而树脂孔的导热树脂起到绝缘的作用并且可以安放元件的插脚。
在本实施例中,步骤S10中CCD钻孔机中使用的钻刀直径小于树脂孔的孔径,具体的,CCD钻孔机中使用的钻刀直径比树脂孔的孔径小0.04-0.06mm,在本实施例中,由于CCD钻孔机具有CCD功能,所以能够保证钻孔精度,避免PTH孔孔壁上的镀铜遭到破损。
在本实施例中,步骤S10之后还包括以下步骤:
S101、按产品设计要求锣板制作;
S102、撕除铝基板板面的抗蚀高温膜;
S103、对铝基板外表面进行磨板;
S104、对电路板进行开短路测试;
S105、按常规制作方法对电路板板面进行OSP表面处理;
S106、对电路板做外观检查;
S107、检验合格后,按设计包装要求包装出货。
本发明实施例还提供一种适用于插件方式耐高压的金属基线路板,金属基线路板由上述的制作方法制得。
以上所述,仅为本发明的具体实施方式,但本发明的保护范围并不局限于此,任何熟悉本技术领域的技术人员在本发明揭露的技术范围内,可轻易想到各种等效的修改或替换,这些修改或替换都应涵盖在本发明的保护范围之内。因此,本发明的保护范围应以权利要求的保护范围为准。
本文用于企业家、创业者技术爱好者查询,结果仅供参考。