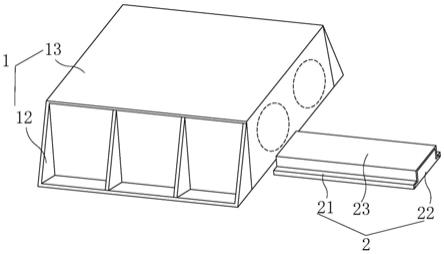
1.本发明涉及建筑施工技术领域,特别是涉及一种盾构混凝土套筒始发进洞方法及建筑结构。
背景技术:
2.随着城市化进程的不断加快,人口的涌入导致城市交通压力剧增,为了满足国民对于交通出行的需求,地下轨道交通的发展刻不容缓。地下轨道交通建设的主要方法有盾构法、明挖法、盖挖逆作法以及矿山法等,盾构法因为其安全性、掘进速度快、对地面影响小等优点,在众多工法中脱颖而出。盾构法施工一般分为三个阶段,即盾构始发、正常掘进和接收。盾构始发在施工流程中所占比例较小,却是事故的高发段,经常成为制约整个盾构隧道工程的关键点。针对不同地质地形特征以及周边环境的影响,如,城市近郊山坡地形且坡顶存在密集敏感建筑等特殊环境,业者需要选择一种最佳的盾构设备始发进洞施工方法。
技术实现要素:
3.本发明的一个目的在于提供一种适应复杂地形与周边敏感环境的盾构混凝土套筒始发进洞方法。
4.本发明的另一个目的在于提供一种盾构混凝土套筒始发进洞方法设计的建筑结构。
5.为实现上述目的,本发明的技术解决方案是:本发明是一种盾构混凝土套筒始发进洞方法,包括以下步骤:步骤s1,主体结构的端头桩基础支护:步骤s11,场地平整:在桩基础施工前需对场地平整夯实,保证场地有一定硬度以免钻机沉陷或倾斜;步骤s12,桩基础施工:步骤s121,放线定位:采用全站仪精确定位桩孔的位置,根据桩定位点拉十字线钉放四个控制桩,以四个控制护桩为基准控制护筒的埋设位置和钻机的准确就位;步骤s122,钻机就位:桩基础采用旋挖钻机施工,通过测设的桩位准确确定钻机的位置,并保证钻机稳定,通过手动粗略调平以保证钻杆基本竖直后,利用自动控制系统调整钻杆保持竖直状态;步骤s123,埋设护筒:护筒安装时,钻机操作手利用扩孔器将桩孔扩大,之后通过大扭矩钻头将钢护筒压入设计标高;护筒压入前及压入后,通过靠在护筒上的精确水平仪调整护筒的垂直位置;步骤s124,钻进成孔:钻进前需制作泥浆,钻孔过程中应随时检验泥浆比重和含砂率,并填写泥浆试验记录表,并随时注意地质变化,根据地质情况的变化随时调整泥浆的性能指标,保证泥浆的各项指标符合规范要求;钻孔过程中根据地质情况控制进尺速度:由硬地层钻到软地层时,可适当加快钻进速度;当软地层变为硬地层时,要减速慢进;步骤s125,反复清孔:钻孔达到设计深度后需进行清孔,清孔采用换浆法清孔,清
孔时注意保持孔内水位;清孔分两次进行,第一次清孔在钻孔深度达到设计深度后进行,待钢筋笼安装到位后下放导管再进行第二次清孔;步骤s126,制安钢筋笼:钢筋笼采用钢筋场集中加工,现场拼接,钢筋笼加工采用长线法施工,钢筋笼分2或3节加工制作,基本节长12m或9m,最后一节为调整节;钢筋笼的起吊利用吊机进行接高及下放,吊点设置在每节钢筋笼最上一层加劲箍处钢筋笼安装深度误差为0
‑
100mm,桩顶纵筋锚入回填素混凝土长度为0
‑
560mm;步骤s127,下导管:完全下放导管到孔底后,并经检查无误后,轻轻提起导管,控制底口距离孔底0.3m,并位于钻孔中央;步骤s128,二次清孔:导管下放到位后,应立即进行孔底沉渣检测,若沉渣厚度不满足设计要求时,采用气举反循环二次清孔,循环时应注意保持泥浆水头并补充优质泥浆防止塌空;清孔结束立即拆除吸泥弯头,开始浇注水下混凝土,浇注混凝土前孔底沉渣厚度不大于5cm;步骤s129,浇注桩身混凝土至桩顶:灌注混凝土前需对混凝土输送管路及容器洒水润湿,然后在填充导管内安装隔水设施,待储料斗储满混凝土后,开始灌注水下混凝土;首批灌注混凝土的数量满足导管首次埋置深度为0
‑
1m和填充导管底部高度的需要,封底时导管埋入混凝土中的深度为0
‑
1m,灌注混凝土过程中要经常量测孔内混凝土面的上升高度,导管到达一定埋深后,逐级快速拆卸导管,并在每次起升导管前,探测一次孔内混凝土面高度,控制灌注的桩顶标高比设计标高高出0.4m
‑
0.6m;步骤s13,混凝土养护:桩基灌注完成后自然养护28天后,进行桩基强度及桩基小应变检测;步骤s2,主体结构的挡土墙设支护:采用分段施工的方法,每段施工步骤为:步骤s21,场地平整:根据设计要求合理布置施工场地,先平整场地、清除杂物;步骤s22,放线定位:施工前根据放出的基坑边缘线,四周交点用钢钎打入地下,桩位中心点用钎子插入地下并用白灰明示;步骤s23,基槽开挖垫层施工:根据测量放点,基槽开挖采用挖掘机配合人工进行开挖,不得挖到设计标高以下,开挖至设计高程后应进行验槽,合格后再进行下一步施工;挖至满足承载力要求的土层,然后用人工砂石回填到基座设计标高,砂石比例6:4,压实系数>0.97;若发现地基与设计要求有出入应按实际情况调整设计,改变挡土墙起点位置或基底标高以及其他工程措施处理;端头加固区挡墙底部有桩基的应对桩头进行凿桩处理,桩基锚筋应锚入挡墙内,待基底验槽合格后,浇筑垫层;步骤s24,基础钢筋绑扎:钢筋绑扎前将垫层清理干净,并用粉笔在垫层上划好主筋、分布筋间距,按划好的间距,先摆放受力主筋、后放分布筋,在绑扎基础钢筋的同时预留墙身外墙和扶壁钢筋;在钢筋与模板之间垫好垫块,间距为0m
‑
1.5m,保护层厚度50mm;绑扎顺序为绑底板底钢筋、绑底板面钢筋、按定位下面板、扶壁插筋、划好底板钢筋的分档标志,并摆好下层钢筋,绑好暗梁;摆放钢筋马凳后,绑上层钢筋的纵横两个方向定位钢筋,然后穿放纵横钢筋并绑扎;步骤s25,基础模板安装:挡土墙基础模板采用厚胶合板,方木作为次楞,间隔竖向布置;外主楞采用方木横向放置,间距200mm
ꢀ‑
300mm。水平外楞采用钢管支撑,300mm
‑
700mm间距布置,钢管另一端抵在基槽底或基坑壁上;
步骤s26,基础混凝土浇筑:浇筑砼前,应将杂物及其它垃圾清除干净,对模板、钢筋、预埋件、预留孔洞、防水措施等进行检查修整,验收合格后才能浇筑;混凝土浇筑顺序由中间向两侧分层浇筑原则进行,分层厚度不大于30cm
ꢀ‑
50cm;振捣泵送混凝土时,使用插入式振捣器应快插慢拔,插点要均匀排列,逐点移动,顺序进行,不得遗漏,做到均匀振实;步骤s27,拆模养护:混凝土浇筑完毕后,应在12h以内加以覆盖和浇水,混凝土有足够的润湿状态;拆模时,混凝土强度达到要求强度后才可拆模,混凝土养护期一般不少于14d;步骤s28,墙身钢筋绑扎:面板、扶壁钢筋绑扎前,先对底板预埋筋进行清理;面板、扶壁钢筋直径小于φ22时采用绑扎连接,当面板、扶壁钢筋直径≥φ22时采用焊接的方式连接;面板水平钢筋在内侧,竖向钢筋在外侧,先绑好控制墙体截面及钢筋间距和水平筋间距用的定位筋,间距为0m
‑
1.5m,然后于下部及齐胸部绑两根水平筋固定位置,并在水平筋上划好分档标志,然后绑其余竖筋,最后绑其余水平筋,在接头范围内水平筋不少于三根,绑扣不少于3扣;面板钢筋绑扎完成后绑扎扶壁钢筋保证同一截面钢筋接头数量不超过截面钢筋数量的50%;步骤s29,墙身模板安装:墙土墙墙身模板采用厚胶合板,方木作为次楞,间隔竖向布置;外主楞采用双排扣件式钢管横向放置,300mm
‑
700mm;挡土墙施工时采用承插型盘扣式钢管支架搭设双排脚手架;步骤s210,墙身混凝土浇筑:浇筑工艺同步骤s26;步骤s211,拆模养护:同步骤s27。
6.步骤s212,下一段挡墙施工:本段挡墙施工完成后,施工下一段挡墙,工艺同上,直至完成所有挡墙;步骤s3,端头回填加固:步骤s31,建造排水反滤层:在混凝土回填前,在挡土墙墙背设计规定的范围应回填砂砾或碎石等透水性材料作为排水反滤层,渗水可通过反滤层经挡土墙内预埋的泄水孔排到外部;步骤s32,端头加固区回填:端头加固区回填采用c15素混凝土进行回填,素砼回填前均需分区块平整场地至场平标高,待桩基检测合格后进行;步骤s33,场地清理:在混凝土回填范围内清除地表虚渣回填土,保证回填混凝土与桩基的连接,减少不均匀沉降;步骤s34,大体积混凝土浇筑:大体积混凝土施工采用分层连续浇筑,每层厚度按300~500mm控制,层间最长间歇时间不应大于混凝土的初凝时间;混凝土浇筑宜从低处开始,采用天泵沿长边方向由区域ⅱ向区域ⅰ分层分段连续浇筑施工;浇筑分段应根据现场实际情况进行确认,沿线路纵向每20m
‑
40m设置变形缝;步骤s4,始发平台建造,包括以下步骤:步骤s41,始发平台桩基础支护;步骤s42,始发平台挡土墙设支护;步骤s43,始发平台回填加固:步骤s431,清理现场:回填前清理现场所有障碍物,尤其是改迁现场各类管线;步骤s432,场地整平:路堤填筑前,整个场区先进行清表和场地整平,并对场地进行碾压,保证天然地基压实系数达到0.90后再填筑;填筑过程应分级分层进行,每一级内应
分层填筑碾压,单层填筑厚度为20~30cm,逐层填筑、逐层碾压;步骤s432,建造排水反滤层:素土回填前,在挡土墙墙背设计规定的范围应回填砂砾或碎石等透水性材料作为排水反滤层,渗水可通过反滤层经挡土墙内预埋的泄水孔排到外部;步骤s433,始发平台回填:始发平台回填采用素土进行回填;填料应为c组及c组以上填料或改良土,压实系数≥0.90;回填区顶部浇筑300mm或1200mm厚的混凝土硬化,挡土墙施工时顶部预留内侧横向钢筋与硬化道路固接。
7.本发明是一种盾构混凝土套筒始发进洞方法设计的建筑结构,由主体结构和始发平台组成;所述主体结构的外端与始发平台的内端衔接。
8.所述主体结构包括多根端头桩、两座挡土墙、回填层;所述两座挡土墙的下端固定在地面上且相对而设,在两座挡土墙之间形成回填层的容置空间,多根端头桩的下端间隔固定在地面上且位于两座挡土墙之间,回填层填充在两座挡土墙之间。
9.所述始发平台包括两座始发平台挡土墙、始发平台回填层、始发平台顶板;所述两座始发平台挡土墙的下端固定在地面上且相对而设,始发平台顶板的两端固定在两座始发平台挡土墙顶端,始发平台顶板与两座始发平台挡土墙之间形成始发平台回填层的容置空间,始发平台回填层填充在两座始发平台挡土墙之间。
10.所述回填层为混凝土。
11.所述回填层为素土。
12.采用上述方案后,由于本发明包括端头桩基础支护、挡土墙设支护、端头回填加固和始发平台建造等四个方面的施工步骤,端头桩基础支护、挡土墙设支护、端头回填加固构造出用于盾构始发施工的主体结构,始发平台建造为盾构机的入场施工提供了施工平台,能够较好适应复杂地形与周边敏感环境的盾构始发施工,实现了满足周边环境影响较小的条件下盾构安全快速始发,为今后类似工程提供了借鉴与参考。
13.下面结合附图和具体实施例对本发明作进一步的说明。
附图说明
14.图1是发明建筑结构的示意图;图2是本发明主体结构的截面图;图3是本发明始发平台的截面图。
具体实施方式
15.如图1所示,本发明是一种盾构混凝土套筒始发进洞方法,包括以下步骤:步骤s1,主体结构1的端头桩11基础支护:步骤s11,场地平整:在桩基础施工前需对场地平整夯实,保证场地有一定硬度以免钻机沉陷或倾斜;步骤s12,桩基础施工:步骤s121,放线定位:采用全站仪精确定位桩孔的位置,根据桩定位点拉十字线钉放四个控制桩,以四个控制护桩为基准控制护筒的埋设位置和钻机的准确就位;护桩要做好保护工作,防止施工过程中被扰动。
16.步骤s122,钻机就位:事先检查钻机的性能状态是否良好,保证钻机工作正常。为加快施工进度,本次桩基础采用旋挖钻机施工,通过测设的桩位准确确定钻机的位置,并保证钻机稳定,通过手动粗略调平以保证钻杆基本竖直后,利用自动控制系统调整钻杆保持竖直状态。
17.步骤s123,埋设护筒:护筒采用10mm钢板卷制成型,其内径比设计桩径大0.2m,上下口外围加焊加劲环。护筒安装时,钻机操作手利用扩孔器将桩孔扩大,之后通过大扭矩钻头将钢护筒压入设计标高;护筒压入前及压入后,通过靠在护筒上的精确水平仪调整护筒的垂直位置。护筒顶一般高于原地面0.3m,以便钻头定位及保护桩孔。
18.步骤s124,钻进成孔:钻进前需制作泥浆,钻孔过程中应随时检验泥浆比重和含砂率,并填写泥浆试验记录表,并随时注意地质变化,根据地质情况的变化随时调整泥浆的性能指标,保证泥浆的各项指标符合规范要求;钻孔过程中根据地质情况控制进尺速度:由硬地层钻到软地层时,可适当加快钻进速度;当软地层变为硬地层时,要减速慢进。
19.步骤s125,反复清孔:钻孔达到设计深度后需进行清孔,清孔采用换浆法清孔,清孔时注意保持孔内水位;清孔的目的是清除钻渣和沉淀层,尽量减少孔底沉淀厚度,防止桩底存留过厚沉渣而降低桩的承载力。清孔分两次进行,第一次清孔在钻孔深度达到设计深度后进行,第一次清孔就应满足规范要求,否则不应下放钢筋笼。待钢筋笼安装到位后下放导管再进行第二次清孔。
20.步骤s126,制安钢筋笼:钢筋笼采用钢筋场集中加工,现场拼接,钢筋笼加工采用长线法施工,钢筋笼分2或3节加工制作,基本节长12m或9m,最后一节为调整节;钢筋笼的起吊利用25t吊机进行接高及下放,吊点设置在每节钢筋笼最上一层加劲箍处,吊耳采用圆钢制作并与相应主筋焊接。钢筋笼安装深度误差为0
‑
100mm,桩顶纵筋锚入回填素混凝土长度为0
‑
560mm。
21.步骤s127,下导管:导管采用250mm内径导管,中间节长3m,配备0.5m、1m、1.5m非标准节。导管在使用前,除应对其规格、质量和拼接构造进行认真地检查外,应进行试拼和试压,导管须经水密试验不漏水。导管长度应按孔深和工作平台高度决定,完全下放导管到孔底后,并经检查无误后,轻轻提起导管,控制底口距离孔底0.3m,并位于钻孔中央。
22.步骤s128,二次清孔:导管下放到位后,应立即进行孔底沉渣检测,若沉渣厚度不满足设计要求时,采用气举反循环二次清孔,循环时应注意保持泥浆水头并补充优质泥浆防止塌空;清孔结束经监理工程师现场检验合格后,立即拆除吸泥弯头,开始浇注水下混凝土,浇注混凝土前孔底沉渣厚度不大于5cm,孔内沉渣测量采用前端悬挂平砣测绳测量,测出的差值即为沉渣厚度。
23.步骤s129,浇注桩身混凝土至桩顶:桩身混凝土设计标号c35,混凝土配合比设计通过试配确定;灌注混凝土前需对混凝土输送管路及容器洒水润湿,然后在填充导管内安装隔水设施,待储料斗储满混凝土后,开始灌注水下混凝土;首批灌注混凝土的数量满足导管首次埋置深度为0
‑
1m和填充导管底部高度的需要,封底时导管埋入混凝土中的深度为0
‑
1m,首批混凝土方量是根据桩径和导管埋深及导管内混凝土的方量而定,拌制好的混凝土用砼运输车运至桩基口处,注入钻机提升的料斗内。灌注混凝土过程中要经常量测孔内混凝土面的上升高度,导管到达一定埋深后,逐级快速拆卸导管,并在每次起升导管前,探测一次孔内混凝土面高度,控制灌注的桩顶标高比设计标高高出0.4m
‑
0.6m。
24.步骤s13,混凝土养护:桩基灌注完成后自然养护28天后,进行桩基强度及桩基小应变检测。
25.步骤s2,主体结构1的挡土墙12设支护:采用分段施工的方法,每段施工步骤为:步骤s21,场地平整:根据设计要求合理布置施工场地,先平整场地、清除杂物。规划行车路线时,行车道范围内局部土质较软部分考虑采用砖渣铺设压实;步骤s22,放线定位:施工前根据放出的基坑边缘线,四周交点用钢钎打入地下,桩位中心点用钎子插入地下并用白灰明示;步骤s23,基槽开挖垫层施工:根据测量放点,基槽开挖采用挖掘机配合人工进行开挖,不得挖到设计标高以下,机械如不能准确的挖至设计基底标高时,可在该标高以上暂留一层不挖,以便在抄平后,由人工配合挖至设计标高;开挖至设计高程后(部分挡土墙基础置于实地上)应进行验槽,合格后再进行下一步施工;如挡土墙底路基承载力达不到挡土墙基底压应力要求应及时通知设计单位。挖至满足承载力要求的土层,然后用人工砂石回填到基座设计标高,砂石比例6:4,压实系数>0.97;若发现地基与设计要求有出入应按实际情况调整设计,改变挡土墙起点位置或基底标高以及其他工程措施处理;端头加固区挡墙底部有桩基的应对桩头进行凿桩处理,桩基锚筋应锚入挡墙内,待基底验槽合格后,视情况浇筑垫层,垫层采用c15混凝土;步骤s24,基础(踵板、趾板)钢筋绑扎:钢筋绑扎前将垫层清理干净,并用粉笔在垫层上划好主筋、分布筋间距,按划好的间距,先摆放受力主筋、后放分布筋,在绑扎基础钢筋的同时预留墙身外墙和扶壁钢筋;在钢筋与模板之间垫好垫块,间距为0m
‑
1.5m,保护层厚度50mm;绑扎顺序为绑底板底钢筋、绑底板面钢筋、按定位下面板、扶壁插筋,按图纸要求划好底板钢筋的分档标志,并摆好下层钢筋,绑好暗梁;摆放钢筋马凳后,绑上层钢筋的纵横两个方向定位钢筋,然后穿放纵横钢筋并绑扎;步骤s25,基础(踵板、趾板)模板安装:挡土墙基础模板采用15mm厚胶合板,10
×
10cm方木作为次楞,间隔(间距250mm)竖向布置;外主楞采用10
×
10cm方木横向放置,间距200mm
ꢀ‑
300mm。水平外楞采用钢管支撑,300mm
‑
700mm(最佳500 mm)间距布置,钢管另一端抵在基槽底或基坑壁上;步骤s26,基础(踵板、趾板)混凝土浇筑:为保证砼浇筑施工的连续性,提前通知拌合站做好混凝土供应计划,并已提前做好砼配合比试验。浇筑砼前,应将杂物及其它垃圾清除干净,对模板、钢筋、预埋件、预留孔洞、防水措施等进行检查修整,验收合格后才能浇筑;混凝土浇筑顺序由中间向两侧分层浇筑原则进行,分层厚度不大于30cm
ꢀ‑
50cm(最佳厚度为40cm);振捣泵送混凝土时,使用插入式振捣器应快插慢拔,插点要均匀排列,逐点移动,顺序进行,不得遗漏,做到均匀振实;每段混凝土要连续浇注不得间断,要掌握好时间,使下层混凝土尚未初凝便覆盖上层砼,直至浇筑完成;步骤s27,拆模养护:混凝土浇筑完毕后,应在12h以内加以覆盖和浇水,混凝土有足够的润湿状态;拆模时,混凝土强度达到要求强度后才可拆模,混凝土养护期一般不少于14d;步骤s28,墙身(面板、扶壁)钢筋绑扎:面板、扶壁钢筋绑扎前,先对底板预埋筋进行清理;面板、扶壁钢筋直径小于φ22时采用绑扎连接,当面板、扶壁钢筋直径≥φ22时采用焊接的方式连接;面板水平钢筋在内侧,竖向钢筋在外侧,先绑好控制墙体截面及钢筋间
距和水平筋间距用的定位筋,间距为0m
‑
1.5m,然后于下部及齐胸部绑两根水平筋固定位置,并在水平筋上划好分档标志,然后绑其余竖筋,最后绑其余水平筋,在接头范围内水平筋不少于三根,绑扣不少于3扣;面板钢筋绑扎完成后绑扎扶壁钢筋;钢筋的搭接位置、接头长度均按设计及施工规范的要求,保证同一截面钢筋接头数量不超过截面钢筋数量的50%;步骤s29,墙身(面板、扶壁)模板安装:墙土墙墙身模板采用15mm厚胶合板,10
×
10cm方木作为次楞,间隔(间距250mm)竖向布置;外主楞采用双排ф48.3
×
3.6mm扣件式钢管横向放置,300mm
‑
700mm(最佳500 mm);支撑体系采用m14对拉螺栓,间距500
×
500mm。本工程挡土墙墙身最低4m,最高12.7m,施工时采用φ48规格的承插型盘扣式钢管支架搭设双排脚手架;脚手架距墙身0.15m,便于钢筋及模板安装,立挂密目安全网对施工区全封闭,外架搭设随施工层同步进行。立杆横距选用0.9m,立杆纵距选用1.5m,水平杆步距选用1.5m。沿架体外侧纵向每5跨每层应设置一根竖向斜杆或每5跨间设置扣件钢管剪刀撑,端跨的横向每层应设置竖向斜杆。对双排脚手架的每步水平杆层,每2跨设置1道水平斜杆,上下相邻两步水平杆层水平斜杆应错开。脚手板采用冲压钢脚手板,每4步1设。可调托座插入立杆不得小于150mm,丝杆外漏长度不应大于300mm,作为扫地杆的最底层水平杆离地高度不应大于200mm;步骤s210,墙身(面板、扶壁)混凝土浇筑:对于最高12.7m的挡土墙墙身分两次浇筑,第一次浇筑下部7m墙身,完成施工后浇筑上部剩余墙身。浇筑施工采用混凝土泵车,浇筑工艺同步骤s26;步骤s211,拆模养护:同步骤s27;步骤s212,下一段挡土墙施工:本段挡墙施工完成后,施工下一段挡墙,工艺同上,直至完成所有挡墙。
26.步骤s3,端头回填加固:步骤s31,建造排水反滤层:在混凝土回填前,在挡土墙墙背设计规定的范围应回填砂砾或碎石等透水性材料作为排水反滤层,渗水可通过反滤层经挡土墙内预埋的泄水孔排到外部;步骤s32,端头加固区回填:端头加固区回填采用c15素混凝土进行回填,素砼回填前均需分区块平整场地至场平标高,待桩基检测合格后进行;步骤s33,场地清理:在混凝土回填范围内清除地表虚渣回填土,保证回填混凝土与桩基的连接,减少不均匀沉降;步骤s34,大体积混凝土浇筑:大体积混凝土施工采用分层连续浇筑,每层厚度按300~500mm控制,层间最长间歇时间不应大于混凝土的初凝时间;混凝土浇筑宜从低处开始,采用天泵沿长边方向由区域ⅱ向区域ⅰ分层分段连续浇筑施工;浇筑分段应根据现场实际情况进行确认,沿线路纵向每20m
‑
40m(最佳30m)设置变形缝;步骤s4,始发平台建造,包括以下步骤:步骤s41,始发平台桩基础支护;步骤s42,始发平台挡土墙设支护;步骤s43,始发平台回填加固:步骤s431,清理现场:回填前清理现场所有障碍物,尤其是改迁现场各类管线;步骤s432,场地整平:路堤填筑前,整个场区先进行清表和场地整平,并对场地进行碾压,保证天然地基压实系数达到0.90后再填筑;填筑过程应分级分层进行,每一级内应
分层填筑碾压,单层填筑厚度为20~30cm,逐层填筑、逐层碾压,回填剖面示意图见图3。;步骤s432,建造排水反滤层:素土回填前,在挡土墙墙背设计规定的范围应回填砂砾或碎石等透水性材料作为排水反滤层,渗水可通过反滤层经挡土墙内预埋的泄水孔排到外部,反滤包大样与端头回填加固相同;步骤s433,始发平台回填:始发平台回填采用素土进行回填;填料应为c组及c组以上填料或改良土,压实系数≥0.90;回填区顶部浇筑300mm或1200mm厚的混凝土硬化,挡土墙施工时顶部预留内侧横向钢筋与硬化道路固接。
27.如图1
‑
图3所示,本发明是一种盾构混凝土套筒始发进洞方法设计的建筑结构,由主体结构1和始发平台2组成;所述主体结构1的外端与始发平台2的内端衔接。
28.所述主体结构1包括多根端头桩11、两座挡土墙12、回填层13;所述两座挡土墙12的下端固定在地面10上且相对而设,在两座挡土墙12之间形成回填层的容置空间,多根端头桩11的下端间隔固定在地面10上且位于两座挡土墙12之间,回填层13填充在两座挡土墙12之间(需要特别说明的是:两座挡土墙可以是一座,另一座挡墙可以是施工现场的山体)。
29.所述始发平台2包括两座始发平台挡土墙21、始发平台回填层22、始发平台顶板23;所述两座始发平台挡土墙21的下端固定在地面10上且相对而设,始发平台顶板23的两端固定在两座始发平台挡土墙21顶端,始发平台顶板23与两座始发平台挡土墙21之间形成始发平台回填层的容置空间,始发平台回填层22填充在两座始发平台挡土墙21之间。
30.所述回填层13为混凝土或素土。
31.以上所述,仅为本发明较佳实施例而已,故不能以此限定本发明实施的范围,即依本发明申请专利范围及说明书内容所作的等效变化与修饰,皆应仍属本发明专利涵盖的范围内。
再多了解一些
本文用于企业家、创业者技术爱好者查询,结果仅供参考。