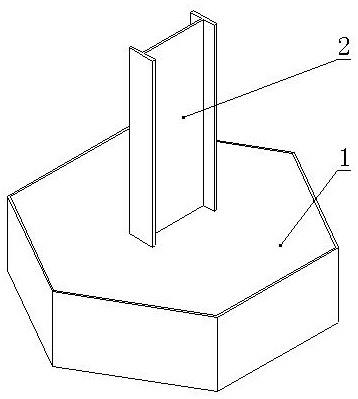
1.本发明涉及砸夯机械技术领域,具体涉及一种新型强夯机械。
背景技术:
2.在高速公路、铁路、机场、港口等基础加固工程中需要用到砸夯机械,根据夯砸冲击力度,砸夯机械分为普通砸夯机和强夯机。
3.普通砸夯机:利用冲击和冲击振动作用分层夯实回填土,其优点是:稳定性强,适用面广;缺点是:夯实力度较小,夯实次数较多,施工速度慢。
4.强夯机:先将重锤高高吊起,再使重锤自由落体,利用重锤高落差产生的冲击能量,对地基进行强力夯实,将回填土方强力挤入地基中,改变地基的空隙分布,以提高地基承载力,减小沉降;其优点是:夯实力度大,夯实次数较少,施工速度快;其缺点是:局部夯实质量得不到保障。
5.针对施工场地存在构筑物的工况,若单租用强夯机进行砸夯施工,在对构筑物附近区域施工时,强夯机产生的冲击力会影响构筑物自身结构安全,构筑物附近区域的压实度难以满足检测标准;若单租用普通砸夯机,虽然可以在不威胁构筑物安全的前提下使构筑物附近区域的压实度满足检测标准,但是施工周期太长,拖延工期。
6.因此很有必要设计一种新型强夯机械,使其不仅可以发挥强夯机的功能,也可以对构筑物附近区域施工,既能满足压实度检测标准,又不拖延工期。
技术实现要素:
7.本发明要解决的技术问题是弥补现有技术的不足,提供一种新型强夯机械。
8.要解决上述技术问题,本发明的技术方案为:
9.一种新型强夯机械,其特征是:包括拔桩机和夯锤,夯锤包括夯头和连接件,夯头的形状为n棱柱,n≥4,n为偶数,连接件为h型钢,连接件与夯头固定连接,夯头的重心同时在连接件腹板对称面和连接件两个翼缘的对称面上。
10.进一步地,所述夯头包括由钢板焊接而成的n棱柱壳体,n棱柱壳体包括n个侧板和底板,n棱柱壳体内固定有钢筋笼,所述连接件固定在钢筋笼上,n棱柱壳体内浇筑有混凝土块,混凝土块的顶面为平面,混凝土块的顶面与n棱柱壳体的顶面齐平。
11.进一步地,所述夯头的n棱柱壳体内焊接有若干钢筋柱,所述钢筋笼固定在钢筋柱上。
12.进一步地,所述夯锤的重量为4.5~5吨。
13.进一步地,所述夯头的外接圆柱直径为1500mm,所述连接件采用的h型钢为40b#型号,连接件顶面距离夯头顶面距离为1000mm。
14.本发明可以达到的有益效果为:
15.(1)创造性地将拔桩机与夯锤匹配应用,利用拔桩机的特点使新型强夯机械不仅具备重力冲击的功能,也可以解决传统的强夯机械对构筑物附近区域的压实度难以满足检
测标准的难题;
16.(2)相对于传统的强夯机械,机动性大大提高;
17.(3)利用拔桩机的震动下沉功能可以使夯锤在冲击力减小的前提下依然可以提升夯实施工速度;
18.(4)在保证沉降差符合要求的情况下,既能保证构筑物附近压实度达标,也可大大缩短施工工期,使施工成本大为降低。
附图说明
19.图1是本发明实施例中夯锤的示意图;
20.图2是本发明实施例中六棱柱壳体示意图;
21.图中:1
‑
夯头,2
‑
连接件,101
‑
侧板,102
‑
底板,103
‑
钢筋柱。
具体实施方式
22.下面结合附图和具体实施方式对本发明作进一步详细的说明。
实施例
23.一种新型强夯机械,包括拔桩机和夯锤,夯锤包括一体连接的夯头1和连接件2,夯锤的重量为4.85吨,其中夯头1的重量为约4.6吨,连接件2的重量约为0.25吨。
24.连接件2为40b#号h型钢,夯头1的重心同时在连接件2腹板对称面和连接件2两个翼缘的对称面上。
25.夯头1的形状为六棱柱,其外接圆柱直径为1500mm,高度约为400mm,其具体结构为:由钢板焊接成六棱柱壳体,n棱柱壳体包括6个侧板101和底板102,顶部为敞口,在六棱柱壳体内焊接有若干钢筋柱103,将绑扎好的钢筋笼置于六棱柱壳体内并绑扎在钢筋柱103上,再将连接件2通过绑扎与焊接竖直固定在钢筋笼上,使连接件2顶面距离夯头1顶面距离约为1000mm;再向六棱柱壳体内浇筑混凝土,形成混凝土块,混凝土块的顶面为平面,混凝土块的顶面与n棱柱壳体的顶面齐平。
26.本实施例的使用:
27.(1)强夯模式:采用拔桩机夹持夯锤的连接件2,将夯锤举升至规定高度i,再使拔桩机的夹持头松开夯锤,使夯锤自由落地;
28.(2)构筑物附近夯实模式:采用拔桩机夹持夯锤的连接件2,将夯锤举升至规定高度ⅱ,再使拔桩机的夹持头松开夯锤,使夯锤自由落地,再使拔桩机的夹持头夹持住夯锤的连接件2,开启震动压实的模式,由于拔桩机本身具备震动下沉的功能,故此处不再详述。
29.工程主机选用分析:
30.(1)不能选用起吊机的理由
31.现有技术中强夯机的夯锤一般配合起吊机一起使用,起吊机上设有卷扬机构,夯锤上设有挂钩,起吊机上的卷扬绳与夯锤连接,通过控制起吊机的卷扬机构使夯锤升高至某一高度再自由落体;此种机构的缺点在于:在对构筑物附近区域施工时,强夯机产生的冲击力会影响构筑物自身结构安全,构筑物附近区域的压实度难以满足检测标准,故工程主机不能选择为起吊机。
32.(2)不能选用挖掘机的理由
33.如果将工程主机选择为挖掘机,有如下不妥之处:需要另外制作挖掘机与夯锤的连接构件,使挖掘机与夯锤可以连接在一起;挖掘机为夯锤提供的最大起吊高度不够,起不到强夯的作用。
34.(3)选用拔桩机的理由
35.拔桩机的伸展高度可以使夯锤达到发挥强夯作用的高度;拔桩机本身具备h型钢的夹持头,可以灵活夹持和放开夯锤,这也是为什么夯锤的连接件2选择为h型钢的原因;拔桩机的机动性能良好,且具备震动下沉功能。
36.夯头的形状选择分析:
37.将夯头的形状选择为短柱状,是为了使其自由落体时不会倾倒;
38.短柱状一般包括圆柱和n棱柱,如果采用圆柱,则不能紧贴构筑物的边角部分,依旧存在局部压实度不达标的现象;如果采用三棱柱,但是自由落体时稳定性较差;
39.综合考虑夯锤自由落体着地的稳定性和焊接工艺的实施难易程度,本实施例将夯头的形状定为了六棱柱,并应用于工程实际。
40.工程任务为:回填断面宽24米,平均高度为4.02米,长度为1200米,合同工期为42天。
41.如果采用现有技术的强夯方法,施工期约需要28天,虽然可以满足工期要求,但是根据专业经验,在保证沉降差符合要求的情况下,对构筑物附近的夯实效果进行检测,压实度为86%,而检测标准为90%,显然夯实质量难以达标。
42.如果采用现有技术的普通砸夯方法,根据专业经验,在保证沉降差符合要求的情况下,对构筑物附近的夯实效果进行检测,压实度为95%,夯实质量达标,但是,施工期约需要51天,这必定会拖延工期,影响工程进度。
43.采用本实施例施工,施工期共用28天,节约工期14天,且构筑物附近夯实质量均达标,在充分考虑施工质量的前提下,采用本实施例施工与普通砸夯法相比,所获得经济效益,如下表所示。
[0044][0045]
在本发明的描述中,“内”、“外”、“上”、“下”、“前”、“后”等指示方位或位置关系的词语,仅是为了便于描述本发明,而不是指示或暗示所指的装置或元件必须具有特定的方位、以特定的方位构造和操作,因此不能理解为对本发明的限制。
[0046]
以上所述仅是本发明的其中一种实施方式,本发明的保护范围并不仅局限于上述实施例,应当指出,对于本技术领域的普通技术人员来说,在不脱离本发明思路的前提下所做出的若干改进和润饰均为本发明的保护范围。
再多了解一些
本文用于企业家、创业者技术爱好者查询,结果仅供参考。