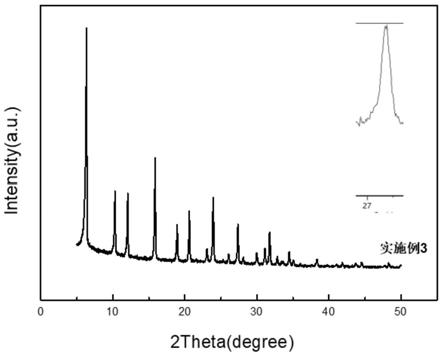
1.本发明提供一种八面沸石分子筛的改性方法、所得到的改性八面沸石分子筛及应用,属于沸石分子筛催化剂制备技术领域。
背景技术:
2.八面沸石是具有fau(骨架类型代码)结构的x型和y型沸石的总称。八面沸石中骨架硅铝比(指sio2和al2o3的摩尔比,下同)大于3的称之为y型沸石(或称之为y型分子筛,或称之为y型沸石分子筛),y型沸石在催化剂制备中具有重要用途。例如,合成得到的y型沸石(即nay沸石),经过脱钠和提高硅铝比(即降低了晶胞常数)后,可以作为催化裂化催化剂、加氢裂化催化剂的主要酸性活性组分,在汽油和柴油等轻质油品的生产中占有很重要的地位。
3.y型沸石的应用受其结晶度以及硅铝比(晶胞常数)影响较大。结晶度大小直接反映沸石晶体结构的完整程度。结晶度和硅铝比(晶胞常数)对于沸石的稳定性影响明显。通常,结晶度高和硅铝比高(低晶胞常数)的沸石显示出更好的稳定性(scherzer julius.applied catalysis,1991,75(1):1-32)。在烃类的催化裂化工艺过程,催化剂在反应-再生系统中要经历高温水热条件下反复循环使用,如果催化剂的稳定性不好,活性就会丧失,就失去其使用价值。结晶度越高,其单位重量沸石的比表面积和孔体积越大,总体酸密度越高,可以使汽油产物的收率和辛烷值相应提高(陈俊武等,《催化裂化工程与工艺》,第2版,中国石化出版社,北京,2005年)。沸石的骨架铝含量下降,其晶胞常数会减小,骨架硅铝比就会升高,提高了其稳定性(包括热稳定性和水热稳定性),硅铝比的提高还会导致酸密度下降、酸强度提高,从而提高汽油选择性(scherzer julius,catalysis reviews,1989,31(3):230-249.)。减小晶胞常数,即提高沸石硅铝比的方法主要有水热脱铝法、氟硅酸铵((nh4)2sif6)液相超稳法和sicl4气相法脱铝补硅(气相超稳法)。水热脱铝法首先要进行铵交换,接着再进行高温水蒸气处理,一般需要反复处理两遍以上,过程长能耗高。而且y沸石在经受这样的处理过程中,往往由于脱铝后没有被硅及时填补的羟基窝空穴的存在及其进一步的发育形成的晶体结构缺陷(即通常所说的二次孔),会导致结晶度明显下降。(nh4)2sif6液相处理脱铝补硅方法,不仅有铵离子的引入,会给后续污水处理造成压力,更为关切的是含氟元素化合物的大量使用存在环境污染的风险。相比之下,sicl4气相法脱铝补硅制备的产品结晶度高、硅铝比高(汪颖军,孙羽佳,所艳华,工业催化,2015,23(11):849-853),整个过程可以不需要铵交换,有利于减少氨氮排放和环境保护,符合现代工业发展的需求。
4.关于“结晶度”,在沸石分子筛领域一般用“相对结晶度”表示,即选定一个被认可的、结晶度高的沸石分子筛作为标准物,把所测试的沸石分子筛样品的特征x-射线衍射峰的峰面积(或峰高)与标准物的特征x-射线衍射峰的峰面积(或峰高)进行对比,所得百分数即为该样品的“相对结晶度”。但在科研和实际生产工作中,为了表示某种沸石分子筛样品
(经历某种处理过程或使用过程后)的稳定性、或者为了表示某种改性处理工艺对沸石分子筛晶体完整程度或晶格有序性的影响,也常常用“结晶保留度”来表示,其计算方法是把处理后的沸石分子筛样品的相对结晶度除以处理前的沸石分子筛样品的相对结晶度,所得百分数即为“结晶保留度”。“结晶保留度”能给出一个沸石分子筛样品在经受某种改性处理或使用过程前后的晶体完整程度或晶格有序性的保持或变化情况。沸石分子筛样品经受某种改性处理或使用过程后得到的产品,其结晶度的高低,不仅依赖于其原料沸石分子筛样品的相对结晶度,也依赖于其经受这种改性处理或使用过程的结晶保留度。所以“相对结晶度”和“结晶保留度”都是非常重要的数据。经过某种改性处理或使用过程后,最终产品的结晶度高低不仅依赖于原料结晶度的高低、也依赖于经受该过程其结晶保留度的高低,因此“结晶保留度”是考察沸石分子筛处理(使用)过程或方法优劣的一个重要指标。
5.四氯化硅气相脱铝补硅法(气相超稳法)制备高硅y沸石及其原理,是由匈牙利学者beyer和belenykaja在1980年首先发表的(beyer h k,belenykaja i,studies in surface science and catalysis,1980,5:203-210)。一般采用氮气保护下的sicl4气体与脱水后的nay沸石在一定温度下进行反应。整个反应过程以sicl4作为外来的硅源,通过同晶取代,脱除y沸石的骨架铝,引入从四氯化硅来的硅,从而完成脱铝补硅。这种方法可以有效避免nay沸石或其它低硅铝比y沸石在水蒸气处理条件下进行脱铝补硅反应时产生羟基空穴、发生晶格塌陷及结构破坏产生的缺陷,具有脱铝较均匀、补硅比较及时,孔道更畅通的特点,所制超稳y沸石结晶保留度高、总比表面积高、总孔体积大、稳定性高。但beyer等人报道的气相超稳方法,采用固定床反应器(床层反应),是将一定量的四氯化硅在457~557℃温度条件下,通过具有一定厚度的nay沸石粉末床层,而且反应时间要2个小时,是一种间歇式的方法,不适合于连续化、规模化制备气相超稳y沸石。
6.cn1127161公开了一种含稀土的富硅超稳y型分子筛的制备方法,是以nay为原料,在固体recl3存在时用sicl4进行气相脱铝补硅反应,一步完成nay的超稳化和稀土离子交换。反应在管式炉中进行,反应时间为10分钟~5小时,最好为20分钟~4.5小时,根据该方法所制备的分子筛其晶胞常数为2.430~2.460nm,稀土含量为0.15~10.0重%,na2o含量小于1.0重%。该分子筛可以用于制备石油烃类的裂化催化剂。
7.他们进一步的工作(cn 1382525a)公开了一种稀土高硅y型沸石的制备方法,将含稀土的y型沸石进行干燥处理,使其水含量低于10重%,然后按照y型沸石:四氯化硅=1:0.1~0.9的重量比,通入干燥空气携带的四氯化硅气体,在温度为150-600℃的条件下,反应10分钟至6小时。然后用干燥空气吹扫5分钟至2小时,用脱阳离子水洗涤除去沸石中残存的na
、cl-、al
3
等可溶性副产物。该方法制备的高硅y型沸石具有较高的稀土含量和较好的晶胞收缩,晶胞收缩在2.425nm~2.460nm。
8.cn 1683245(zl200410031181.0)公开了一种含稀土高硅y型沸石的制备方法,该方法包括将含稀土y型沸石与四氯化硅在一个反应设备中接触反应。该反应设备反应器为带搅拌的釜式反应器。含稀土y型沸石与四氯化硅接触温度为100-500℃,接触的时间为5分钟至10小时。
9.cn 101081369a公开了一种含稀土高硅y型沸石的制备方法,将含稀土的y型沸石进行干燥处理,使其水含量低于1重%,然后按照sicl4:y型沸石=0.1~0.9:1的重量比,sicl4由干燥空气携带进入反应体系,在温度为150-600℃的条件下,反应10分钟至6小时,
得到气相超稳y型沸石。
10.cn 102049315a公开了一种催化裂化催化剂的制备方法,该方法包括在惰性载气流的携带下,使分子筛随惰性载气流流动,在一个管状反应器中与气相sicl4在流动状态下接触反应,载气的流速使sicl4与分子筛在反应器内的停留时间为10秒至100分钟,优选的停留时间为1分钟至20分钟,惰性载气流的流速优选为0.015-3m/s,更优选为0.03-3m/s,进一步优选为0.1-2.5m/s。然后将所得与气相sicl4接触后的分子筛与粘结剂、粘土和水混合打浆并造粒,得到催化裂化催化剂。所述接触在管状反应器中进行,所述管状反应器包括管体和位于管体两端的第一进料口和出料口,所述分子筛和气相sicl4从第一进料口进入所述管体内进行接触反应,接触反应后的产物从出料口排出所述管体外,所述管体包括第一倾斜段、竖直段和第二倾斜段,所述第一倾斜段的一端与所述竖直段的一端相接,所述出料口位于所述第一倾斜段的另一端,且所述第一倾斜段与所述竖直段连接的位置高于所述出料口所在的位置,所述第二倾斜段的一端与所述竖直段的另一端相接,所述第一进料口位于所述第二倾斜段的另一端,所述第一进料口所在的位置高于所述第二倾斜段与所述竖直段连接的位置。该方法为了流化分子筛,气体的量必须足够大,不然容易造成装置堵塞。
11.cn 103787352a(zl201210417837.7)公开了一种制备催化裂化催化剂的方法,该方法使用倾斜管式气相超稳反应器,在不用载气的情况下,使分子筛在机械输送装置和/或重力的作用下移动,从气相超稳反应器的分子筛入口移动到气相超稳反应器的分子筛出口,并且使分子筛与气相sicl4在该气相超稳反应器中接触反应。所述的分子筛和四氯化硅共用物料进口,或者分子筛进口和四氯化硅进口处于所述气相超稳反应器的同一端。反应器管体为直管,所述管体的至少一部分可围绕管体轴线转动。反应温度为250-700℃,反应停留时间为10秒-120分钟,优选为1分钟至60分钟。
技术实现要素:
12.本发明的主要目的在于提供一种八面沸石分子筛的改性方法、所得到的改性八面沸石分子筛及应用,以期得到热稳定性高、水热稳定性高、钠含量低、晶胞常数低的高结晶度、高硅铝比的y型沸石和\或稀土y型沸石。
13.为了达到上述目的,本发明提供了一种八面沸石分子筛的改性方法,该方法包括:将八面沸石分子筛与气态四氯化硅进行接触反应,所述接触反应的时间不超过5秒钟,所述接触反应的空间为反应区域内八面沸石分子筛松堆体积的2倍以上,所述接触反应的温度为250-600℃。
14.本发明所述的八面沸石分子筛的改性方法,其中,所述八面沸石分子筛与所述气态四氯化硅逆流接触,进行反应。
15.本发明所述的八面沸石分子筛的改性方法,其中,所述八面沸石分子筛是nay型沸石分子筛;所述八面沸石分子筛的骨架硅铝摩尔比以sio2和al2o3摩尔比计,为3.2~10;及/或,所述八面沸石分子筛的形态为粉末状,90%的颗粒直径不大于500微米。
16.本发明所述的八面沸石分子筛的改性方法,其中,所述八面沸石分子筛中,钠元素以na2o计的含量不高于15wt%,稀土元素以re2o3计的含量不高于23wt%;所述稀土元素包括镧、铈、镨、钕、镱中的一种或多种。
17.本发明所述的八面沸石分子筛的改性方法,其中,所述八面沸石分子筛与所述气
态四氯化硅进行接触反应之前,还包括所述八面沸石分子筛进行干燥的步骤,以使所述八面沸石分子筛的含水质量百分比不大于5%;及/或,所述八面沸石分子筛与所述气态四氯化硅进行接触反应之后,还包括对反应后的八面沸石分子筛进行脱气、洗涤、干燥中的一种或几种处理步骤。
18.本发明所述的八面沸石分子筛的改性方法,其中,所述脱气的方式包括闪蒸、抽真空、加热挥发中一种或多种;所述洗涤用液体为水,或者含盐酸、硫酸、磷酸、醋酸、草酸、酒石酸、柠檬酸、氯化铵、硫酸铵、硝酸铵、磷酸铵中的一种或多种的水溶液;所述洗涤的温度为常温~120℃,洗涤的时间为5min~4h,洗涤时固液质量比为1:5~30。
19.本发明所述的八面沸石分子筛的改性方法,其中,所述八面沸石分子筛与气态四氯化硅的接触反应在反应器中进行,八面沸石分子筛从反应器的顶部进入,气态四氯化硅从反应器的下部进入,八面沸石分子筛与气态四氯化硅在反应器中逆流接触,进行反应,反应后的物料从反应器的底部输出;及/或,所述反应器中八面沸石分子筛与气态四氯化硅形成全混流或部分全混流的混合状态。
20.本发明所述的八面沸石分子筛的改性方法,其中,所述反应器为气相超稳反应器,所述接触反应的空间为所述反应器的容积,所述反应器的容积为所述接触反应的时间内进入所述反应器的八面沸石分子筛松堆体积的10倍以上;及/或,所述反应器的纵向高度与横向内直径之比为不小于2:1。
21.本发明所述的八面沸石分子筛的改性方法,其中,所述八面沸石分子筛和气相四氯化硅接触反应的温度为300-550℃,接触反应的时间为不超过1秒钟。
22.本发明所述的八面沸石分子筛的改性方法,其中,所述八面沸石分子筛以惰性气体为载气进行输送,所述惰性气体包括空气、氮气、氩气、氦气中的一种或多种,所述惰性气体的用量为所述八面沸石分子筛质量的0%~20%;及/或,所述反应器中八面沸石分子筛和气相四氯化硅的质量比为1:0.05~0.5。
23.为了达到上述目的,本发明还提供了上述的八面沸石分子筛的改性方法得到的改性八面沸石分子筛。
24.本发明所述的改性八面沸石分子筛,其中,所述改性八面沸石分子筛的结晶保留度不小于85%,晶胞常数低于24.55埃。
25.为了达到上述目的,本发明还提供了上述的改性八面沸石分子筛在催化裂化催化剂中的应用。
26.本发明的有益效果:
27.本发明提供一种能够连续化、高效率制备高结晶度和低晶胞常数y型沸石的方法,该方法操作步骤简单,操作成本低,对工艺设备的要求低,硅铝比的提升显著;
28.本发明方法使得原材料八面沸石分子筛的结构得到了优化,结晶度得以高度保留,晶胞常数大幅度降低,显著提高了裂化催化剂的热稳定性、水热稳定性、裂化活性。本发明所得改性八面沸石分子筛结晶保留度不小于85%,优化的条件下达到100%,晶胞常数低于24.60埃(根据需要,优化的条件下低于24.50埃进一步优化的条件下低于24.40埃),具有很强的应用性。
29.说明书附图
30.图1为本发明气态超稳反应器结构示意图;
31.图2为本发明实施例3所得分子筛的xrd谱图;
32.图3为本发明对比例3所得分子筛的xrd谱图。
33.其中,附图标记:
34.11 反应器主体
35.12 沸石分布器
36.13 第一输送器
37.14 第二输送器
38.15 喷嘴
39.16 气化装置
40.17 四氯化硅入口
具体实施方式
41.以下对本发明的实施例作详细说明,本实施例在以本发明技术方案为前提下进行实施,给出了详细的实施方式和过程,但本发明的保护范围不限于下述的实施例,下列实施例中未注明具体条件的实验方法,通常按照常规条件。
42.本发明研究人员在进行四氯化硅气相超稳研究过程中,通过大量的基础研究,发现四氯化硅与八面沸石分子筛的同晶置换脱铝补硅反应本身是一个瞬间完成的快反应,这是在现有技术没有报道过的一个重要实验现象。同时研究人员还发现接触瞬间没有反应的四氯化硅即使进一步增加其与八面沸石分子筛的接触时间,也不再发生反应或者是不明显的发生反应,只是以吸附态存在于八面沸石分子筛中。进一步地,研究人员发现四氯化硅过长时间的吸附于八面沸石分子筛,会使八面沸石分子筛的结晶度下降。再者,四氯化硅与八面沸石分子筛的混合接触与扩散不仅仅是影响改性产品硅铝分布的重要因素,更是影响反应效率及改性产品硅铝比和结晶度的重要因素。
43.由此,本发明提出了一种八面沸石分子筛的改性方法,通过综合控制八面沸石分子筛和气态四氯化硅的接触反应时间和混合接触反应空间两个因素,通过这两个因素的协同作用,具体为通过较短接触反应时间和较大接触反应空间的协同作用,强化了扩散和反应的效率,减少了结晶度损失,从而实现了更高效率、连续化制备高结晶度、低晶胞常数(高硅铝比)八面沸石分子筛(尤其是y沸石分子筛)的目的。
44.基于此,本发明提供了一种八面沸石分子筛的改性方法,该方法包括:将八面沸石分子筛与气态四氯化硅进行接触反应,所述接触反应的时间不超过5秒钟,所述接触反应的空间为反应区域内八面沸石分子筛松堆体积的2倍以上,所述接触反应的温度为250-600℃。
45.本发明八面沸石分子筛的改性方法,与水热超稳改性制备高硅y型沸石的方法相比,具有反应时间短、工艺流程短、可以不使用铵交换步骤,且所得的产物在提高硅铝比的同时可以有较高的相对结晶度或结晶保留度的优点;与氟硅酸铵液相超稳改性方法相比,本发明改性方法具有反应时间短且不用考虑处理环境敏感的氟化合物和氨氮排放的优点;与现有技术四氯化硅气相超稳法相比,本发明改性方法具有改性时间短,改性效率高,且改性产品相对结晶度高(或结晶保留度高)、晶胞常数低的优点,另外本发明改性工艺操作稳
定、效率高、容易实现工业放大生产。
46.在一实施方式中,本发明八面沸石分子筛为钠型八面沸石分子筛。在另一实施方式中,本发明八面沸石分子筛为nay型沸石分子筛,其骨架硅铝摩尔比(以sio2和al2o3摩尔比计)为3.2~10,优选为4.5~5.5。
47.在一实施方式中,本发明八面沸石分子筛含有钠元素,钠元素以na2o计含量不高于15wt%,优选不高于14wt%。在另一实施方式中,本发明八面沸石分子筛含有稀土元素,稀土元素以re2o3计含量不高于23wt%,优选不高于20wt%。稀土元素包括但不限于镧、铈、镨、钕、镱中的一种、两种或两种以上。其中,八面沸石分子筛中除了沸石的骨架元素硅、铝、氧之外,还可以包含但不限于钠、铵、氢等的一种或多种。
48.在一实施方式中,本发明八面沸石分子筛的激光散射仪法颗粒度,90%颗粒的直径(dv 0.9)不大于500微米,优选的是不大于100微米,进一步优选的是不大于30微米。
49.在一实施方式中,八面沸石分子筛在与气态四氯化硅进行接触反应前,还包括进行干燥的步骤。干燥的标准是控制八面沸石分子筛的含水量低于5wt%,优化的是含水量低于4wt%。干燥的方法包括但不限于焙烧、喷雾干燥、输送床干燥等方法。
50.在一实施方式中,八面沸石分子筛与气态四氯化硅逆流接触,进行反应。在另一实施方式中,八面沸石分子筛与四氯化硅的接触反应在反应器中进行,八面沸石分子筛从反应器的顶部进入,气态四氯化硅从反应器的下部进入,八面沸石分子筛与气态四氯化硅在反应器中逆流接触,进行反应,反应后的物料从反应器的底部输出。
51.在另一实施方式中,八面沸石分子筛与气态四氯化硅的反应在图1气态超稳反应器中进行。如图1所示,气态超稳反应器包括反应器主体11、第一输送器13、第二输送器14和四氯化硅入口17。反应器主体11例如为立式反应器主体,其纵轴线与水平面的夹角为90
°
。在一实施方式中,反应器主体11为柱体状,其横截面为圆形,该反应器主体11的纵向高度与内直径之比为不小于2:1,优选不小于3:1。其中,纵向高度例如为反应器主体11的上底面至下底面之间的高度,内直径为反应器主体11内壁在横截面上所形成的圆形的直径。
52.第一输送器13设置于反应器主体11的顶部,用于将八面沸石分子筛输送至反应器;第二输送器14设置于反应器主体11的底部,用于将改性后的八面沸石分子筛输送出反应器。四氯化硅入口17设置于反应器主体11的下部,气态四氯化硅通过四氯化硅入口17进入反应器主体11,并向上流动,与下行的八面沸石分子筛逆流接触,并进行反应,改性后的八面沸石分子筛通过第二输送器14输送出反应器。
53.本发明中第一输送器13和第二输送器14例如为绞龙输送机、螺旋输送机、带式输送机、气流输送机、活塞输送机或管链式输送器中的一种或多种。根据反应温度控制需要,输送装置上可附带设计伴热装置。本发明中四氯化硅入口17例如与气化装置16通过管线连通,如此将四氯化硅通入气化装置16进行气化后,通过四氯化硅入口17输送至反应器。在一实施方式中,上述管线的一端设置于反应器主体11内,该端设置有四氯化硅喷嘴15,如此将四氯化硅均匀喷出至反应器主体11内。
54.在一实施方式中,反应器主体11与第一输送器13之间设置有沸石分布器12,如此可以将八面沸石分子筛均匀地输送至反应器主体11内,进而保证反应器主体11内部八面沸石分子筛分布的分散性。本发明对沸石分布器12的结构不作特别限定,例如沸石分布器12上设置均匀孔。
55.如此,八面沸石分子筛通过第一输送器13从气相超稳反应器的顶部输入,气态四氯化硅通过四氯化硅入口17从气相超稳反应器的下部输入,八面沸石分子筛下行,四氯化硅气体上行,从而使两种反应物在反应器中实现逆向、不超过5秒钟的快速接触反应,接触反应的温度为250-600℃。两种反应物进行接触反应的空间为反应区域内八面沸石分子筛松堆体积的2倍以上。反应后的物料从气相超稳反应器的底部通过第二输送器14输出,例如输送至后续脱气及洗涤装置等。
56.在一实施方式中,反应器中八面沸石分子筛与四氯化硅气体形成全混流或部分全混流的混合状态,以使八面沸石分子筛充分进行改性反应。
57.在一实施方式中,八面沸石分子筛与四氯化硅气体输送至反应器和/或在反应器内下行或上行时,还可以利用干燥的惰性气体进行输送,以促进反应物料(八面沸石分子筛或/和四氯化硅)的传输,但本发明不以此为限。惰性气体包括空气、氮气、氩气、氦气中的一种或多种,惰性气体的用量为所述八面沸石分子筛质量的0%~20%。
58.在一实施方式中,接触反应的时间为八面沸石分子筛在反应器内的停留时间,即八面沸石分子筛进入反应器主体11至离开反应器主体11的时间;八面沸石分子筛从进入反应器主体11至输出反应器主体11的时间不超过5秒钟;接触反应的空间即为反应器的容积,反应器的容积为反应器内八面沸石分子筛松堆体积的2倍以上,换言之,反应器的容积为反应时间内进入反应器的八面沸石分子筛松堆体积的2倍以上优选10倍以上。较大的接触反应空间给两种反应物的混合与扩散以及副产物三氯化铝的扩散提供了条件。
59.在一实施方式中,八面沸石分子筛和气相四氯化硅接触反应的时间不超过3秒钟,优选不超过1秒钟。短的反应时间可以减少八面沸石分子筛结晶度的损失。
60.在一实施方式中,八面沸石分子筛与气态四氯化硅接触反应的温度为300-550℃。该接触反应的温度由八面沸石分子筛原料的温度和进料速度控制,也可以通过在反应器中设置加热或制冷机构进行温度调节。原料的温度由原料的干燥和/或加热过程控制,或者由原料的干燥和/或加热过程以及输送过程的伴热装置联合控制。
61.在一实施方式中,本发明反应器中八面沸石分子筛和气相四氯化硅的质量比为1:0.05~0.5。该质量比是指反应时间内(即:八面沸石分子筛在反应器内的停留时间内),进入反应器的八面沸石分子筛质量与进入反应器的四氯化硅质量之比。
62.在一实施方式中,本发明八面沸石分子筛与四氯化硅气体进行接触反应后,将改性的八面沸石分子筛进行包括闪蒸、抽真空、加热挥发中的一种或几种的脱气处理步骤,以脱除少量未反应的吸附态四氯化硅。脱除的少量未反应的吸附态四氯化硅可经过计量后经由四氯化硅入口重新进入反应器回用。
63.在一实施方式中,脱气处理后的八面沸石分子筛还可以进行洗涤处理,洗涤所用液体为水,或者含盐酸、硫酸、磷酸、醋酸、草酸、酒石酸、柠檬酸、氯化铵、硫酸铵、硝酸铵、磷酸铵中的一种或多种的水溶液;洗涤温度为常温~120℃,洗涤时间为5min~4h,洗涤时固液质量比为1:5~30。优选的是洗涤温度为常温~95℃,洗涤时间为10min~1h,洗涤时固液质量比为1:5~20。然后,洗涤后的八面沸石分子筛还可以进行干燥步骤,但不发明不以此为限。
64.如此,本发明提供了一种以常规的八面沸石为原料,优选以常规的nay沸石或/和含稀土的nay沸石为原料,能够连续化、高效率制备高结晶度和低晶胞常数改性y型沸石的
方法。在该改性方法中,气体sicl4和固体nay分子筛通过逆流接触进行反应,与并流接触方式相比,可以在短时间内保证sicl4和nay分子筛充分发生反应,并且可以及时带走反应热量,避免分子筛结构坍塌。通过该改性方法,本发明可得到高结晶度、低晶胞常数改性八面沸石分子筛,尤其是改性y型沸石分子筛,改性分子筛与分子筛原料相比结晶保留度不小于85%,晶胞常数低于24.55埃优选地,改性分子筛与分子筛原料相比结晶保留度不小于90%,晶胞常数低于24.50埃进一步地,改性分子筛与分子筛原料相比结晶保留度不小于100%,晶胞常数低于24.40埃
65.本发明不特别限定由改性八面沸石分子筛制备裂化催化剂的方法,例如,将本发明上述方法得到的改性八面沸石分子筛输送进催化剂制备装置,与制备催化剂所用的其它原料混合打浆、成型、焙烧,然后再进行洗涤、干燥得到裂化催化剂。洗涤所用液体为水,或者含盐酸、硫酸、磷酸、醋酸、草酸、酒石酸、柠檬酸、氯化铵、硫酸铵、硝酸铵、磷酸铵中的一种或多种的水溶液;洗涤温度为常温~120℃,洗涤时间为5min~4h,洗涤时固液质量比为1:5~30。优化的是洗涤温度为常温~95℃,洗涤时间为10min~1h,洗涤时固液质量比为1:5~20。
66.采用本发明改性方法制备的高结晶度、低晶胞常数y型沸石制备成催化剂,应用于重油催化裂化工艺中,和现有技术改性y型沸石制备的催化剂相比,具有轻质油收率高、特别是汽油收率高的特点。
67.综上所述,本发明提供的改性方法是以干燥后的粉状nay型或/和含稀土的nay型沸石为原料,控制其含水量,然后按照y沸石:四氯化硅=1:0.05~0.5的重量比,通入干燥的四氯化硅气体,在温度250~600℃下,气固接触反应5秒钟以内,同时控制反应空间,然后再对所得产品进行相应的洗涤、过滤处理,任选干燥,得到相对结晶度或者与沸石原料相比结晶保留度不小于85%、晶胞常数低于24.55埃的最终改性产品。
68.本发明改性方法操作步骤简单,原料成本低,对工艺设备的要求低,所得产品硅铝比提升显著,相对结晶度或者结晶保留度不小于85%,优化的条件下达到100%,晶胞常数低于24.60埃(根据需要,优化的条件下低于24.50埃进一步优化的条件下低于24.40埃),具有很强的应用性。
69.另外,由本发明改性方法制备的高结晶度、低晶胞常数改性y型沸石与改性前相比,其结构得到了优化,由其制备的催化剂具有较高的热稳定性、水热稳定性、裂化活性。
70.本发明所述的方法中,使用的原料八面沸石所要求的硅铝比、钠含量、稀土含量、水含量和颗粒度等性质,是工业上容易达到的指标,现有工业技术和装备可以大量提供这样的原料,是市场或催化剂(分子筛)企业可以提供的常规产品,并不需要使用特别的加工手段。本发明所述的方法中,使用的原料四氯化硅也是市场上可以直接获得的工业品。
71.以下将通过具体实施例对本发明技术方案进一步进行详细说明。
72.实施例和对比例中,nay沸石、低rey沸石和高rey沸石为兰州催化剂厂提供的工业上现有的(中间)产品,相对结晶度和骨架硅铝比见表1。
73.用荷兰制造的panalytical x'pert power型x射线粉末衍射仪对样品的晶相、相对结晶度或结晶保留度、和骨架硅铝比进行分析,具体测定方法如下:
74.测试条件:使用cu-kα辐射,工作电压为40kv,工作电流为40ma,相对结晶度测试时2θ角度在5
°
~50
°
之间(扫描速度为2
°
/min),骨架硅铝比测试时2θ角度在28
°
~32
°
之间(扫描速度为0.5
°
/min)。
75.1)相对结晶度测定方法:取约0.3g待分析样品在玛瑙研钵中充分研磨10分钟,在120℃烘箱中干燥2h后将其轻压成表面平整、厚度均一的片,随后进行测试。相对结晶度的计算方法为:以(331)、(511、333)、(440)、(533)、(642)、(822、660)、(555、751)、(664)晶面对应的八个特征峰的峰面积之和同标样相应峰面积之和的比值与标样结晶度的乘积。
76.2)结晶保留度测定方法:取约0.3g待分析样品在玛瑙研钵中充分研磨10分钟,在120℃烘箱中干燥2h后将其轻压成表面平整、厚度均一的片,随后进行测试其相对结晶度。结晶保留度的计算方法为产物或产品样品相对结晶度与反应原料或原粉相对结晶度的比值(以百分数表示)。
77.其中:
78.3)骨架硅铝比测定方法:按样品与硅粉质量比为20:1的比例准确称取适量样品与硅粉,两者在研钵中研磨至混合均匀(至少研磨10min)后于120℃下干燥2h,之后在恒湿器(内盛cacl2过饱和水溶液)中吸水16h以上,然后将其轻压成表面平整的片进行测定,并根据下式计算晶胞常数:
[0079][0080]
式中:λ为u-kα1波长(h2 k2 l2)为x射线衍射指标平方和。
[0081]
按照breck-flanigen公式计算骨架硅铝比:si/al=(25.858-α)/(α-24.191),sio2/al2o3=2
×
(si/al)。
[0082]
采用光散射激光纳米粒度仪测定分子筛颗粒分布情况。激光粒度仪型号为英国马尔文(malvern)仪器有限公司的mastersizer s ver.2.19,粒径范围0.02~2000μm。采用湿法分散技术进行测定,将分子筛固体研磨粉末后,在150ml水中加入0.1g研磨好的y分子筛,混合后,放入超声波仪器样品池中高频震荡15min。将超声分散后的分子筛浆液,通过循环泵进入粒度仪,待分子筛颗粒在整个循环系统中均匀分布后,测定其粒度分布。
[0083]
采用美国kti技术公司设计并制造的ace r
催化裂化催化剂评价设备对催化剂进行评价。催化剂装量为9克,剂油比(wt/wt)6,反应时间75秒,反应温度530℃。以一种减压瓦斯油(vgo)为反应原料油。原料油性质为:密度(20℃)0.93g/cm3,残炭4.19wt%,饱和分64.68wt%,芳香分28.44wt%,c含量86.76wt%,h含量11.63wt%。利用在线炼厂气分析色谱对反应产生的气相产物进行分析,模拟蒸馏色谱对产生的液相产物进行分析。催化剂积碳经过在线再生后,通过二氧化碳分析仪分析后得到相应积碳含量。催化剂在催化裂化反应评价前经800℃、100%水蒸气、老化处理4小时。
[0084]
实施例1
[0085]
经过400℃干燥6h的nay沸石(松堆密度0.2294cm3/g,90%的颗粒直径(dv 0.9)为14.99微米),经过输送器送至立式反应器(每分钟进入反应器的干燥nay为30克),分子筛由立式反应器的顶部进入反应器向下运动,在400℃条件下与由反应器下部进入的四氯化硅
蒸汽接触时间为4秒钟,然后由另一个输送器将粗产物分子筛从反应器下部移出反应器。反应器的容积为30cm3,本实施例中反应器的容积为接触时间内进入反应器的nay沸石物料松堆体积的约3倍。反应器中nay沸石与四氯化硅重量比保持在1:0.1。从反应器中移出的粗产物经过抽真空脱气(目的主要是除去少量吸附但未反应的四氯化硅与少量在高温下仍处于气态的三氯化铝),之后经6倍的水、在90℃搅拌洗涤三次、过滤、干燥后,得到产物a,对其进行相关的测试表征,其结果列于表1。
[0086]
实施例2
[0087]
经过550℃干燥4h的nay沸石(松堆密度0.2294cm3/g,90%的颗粒直径(dv 0.9)为14.99微米),经过输送器送至立式反应器(每分钟进入反应器的干燥nay为30克),分子筛由立式反应器的顶部进入反应器向下运动,在420℃条件下与由反应器下部进入的四氯化硅蒸汽接触时间为1秒钟,然后由另一个输送器将粗产物分子筛从反应器下部移出反应器。反应器的容积为30cm3,本实施例中反应器的容积为接触时间内进入反应器的nay沸石物料松堆体积的约14倍。反应器中nay沸石与四氯化硅重量比保持在1:0.15。从反应器中移出的粗产物经过抽真空脱气,之后经6倍的水、在40℃搅拌洗涤三次、过滤、干燥后,得到产物b,对其进行相关的测试表征,其结果列于表1。
[0088]
实施例3
[0089]
经过600℃干燥2h的nay沸石(松堆密度0.2294cm3/g,90%的颗粒直径(dv 0.9)为14.99微米),经过输送器送至立式反应器(每分钟进入反应器的干燥nay为14克),分子筛由立式反应器的顶部进入反应器向下运动,在450℃条件下与由反应器下部进入的四氯化硅蒸汽接触时间为1.5秒钟,然后由另一个输送器将粗产物分子筛从反应器下部移出反应器。反应器的容积为30cm3,本实施例中反应器的容积为接触时间内进入反应器的nay沸石物料松堆体积的约20倍。反应器中nay沸石与四氯化硅重量比为1:0.2。从反应器中移出的粗产物经过抽真空脱气,之后经6倍的水、在40℃搅拌洗涤三次、过滤、干燥后,得到产物c,对其进行相关的测试表征,其结果列于表1。
[0090]
实施例4
[0091]
经过600℃干燥2h的nay沸石(松堆密度0.2294cm3/g,90%的颗粒直径(dv 0.9)为14.99微米),经过输送器送至立式反应器(每分钟进入反应器的干燥nay为30克),分子筛由立式反应器的顶部进入反应器向下运动,在450℃条件下与由反应器下部进入的四氯化硅蒸汽接触时间为1秒钟,然后由另一个输送器将粗产物分子筛从反应器下部移出反应器。反应器的容积为30cm3,本实施例中反应器的容积为接触时间内进入反应器的nay沸石物料松堆体积的约14倍。反应器中nay沸石与四氯化硅重量比为1:0.25。从反应器中移出的粗产物经过闪蒸(目的主要是除去少量吸附但未反应的四氯化硅与少量在高温下仍处于气态的三氯化铝),之后经5倍的水、在70℃搅拌洗涤三次、过滤、干燥后,得到产物d,对其进行相关的测试表征,其结果列于表1。
[0092]
实施例5
[0093]
经过600℃干燥2h的nay沸石(松堆密度0.2294cm3/g,90%的颗粒直径(dv 0.9)为14.99微米),经过输送器送至立式反应器(每分钟进入反应器的干燥nay为30克),分子筛由立式反应器的顶部进入反应器向下运动,在450℃条件下与由反应器下部进入的四氯化硅蒸汽接触时间为1秒钟,然后由另一个输送器将粗产物分子筛从反应器下部移出反应器。反
应器的容积为30cm3,本实施例中反应器的容积为接触时间内进入反应器的nay沸石物料松堆体积的约14倍。反应器中nay沸石与四氯化硅重量比为1:0.3。从反应器中移出的粗产物经过闪蒸,之后经6倍的水、在30℃搅拌洗涤三次、过滤、干燥后,得到产物e,对其进行相关的测试表征,其结果列于表1。
[0094]
实施例6
[0095]
本实施例提供了一种高结晶度和低晶胞常数的低稀土y型沸石,其是由以下步骤制备得到的:
[0096]
经过600℃干燥4h的低稀土nay沸石(主要稀土元素含量la2o3为0.52wt%,ceo2为1.0wt%,pr6o6为0.11wt%,nd2o3为0.34wt%。松堆密度0.2328cm3/g,90%的颗粒直径(dv 0.9)为10.83微米),经过输送器送至立式反应器(每分钟进入反应器的干燥低稀土nay沸石为30克),分子筛由立式反应器的顶部进入反应器向下运动,在420℃条件下与由反应器下部进入的四氯化硅蒸汽接触时间为1秒钟,然后由另一个输送器将粗产物分子筛从反应器下部移出反应器。反应器的容积为30cm3,本实施例中反应器的容积为接触时间内进入反应器的nay沸石物料松堆体积的约14倍。反应器中低稀土nay沸石与四氯化硅重量比为1:0.15。从反应器中移出的粗产物经过闪蒸,之后经6倍的水、在80℃搅拌洗涤三次、过滤、干燥后,得到产物f,对其进行相关的测试表征,其结果列于表1。
[0097]
实施例7
[0098]
本实施例提供了一种高结晶度和低晶胞常数的高稀土y型沸石,其是由以下步骤制备得到的:
[0099]
经过600℃干燥2h的高稀土nay沸石(主要稀土元素含量la2o3为3.33wt%,ceo2为6.60wt%,pr6o6为0.71wt%,nd2o3为2.22wt%。,松堆密度0.2562cm3/g),经过输送器送至立式反应器(每分钟进入反应器的干燥高稀土nay沸石为30克),分子筛由立式反应器的顶部进入反应器向下运动,在420℃条件下与由反应器下部进入的四氯化硅蒸汽接触时间为1秒钟,然后由另一个输送器将粗产物分子筛从反应器下部移出反应器。反应器的容积为30cm3,本实施例中反应器的容积为接触时间内进入反应器的nay沸石物料松堆体积的约15倍。反应器中高稀土nay沸石与四氯化硅重量比为1:0.15。从反应器中移出的粗产物经过闪蒸,之后经10倍的水、在70℃搅拌洗涤三次、过滤、干燥后,得到产物g,对其进行相关的测试表征,其结果列于表1。
[0100]
对比例1
[0101]
本对比例与实施例1的区别在于反应空间约等于nay沸石固体物料松堆体积、且接触反应时间为14秒钟,由以下步骤制备得到:
[0102]
经过400℃干燥6h的nay沸石(松堆密度0.2294cm3/g,90%的颗粒直径(dv 0.9)为14.99微米),经过输送器送至立式反应器(每分钟进入反应器的干燥nay为30克),分子筛由立式反应器的顶部进入反应器向下运动,在400℃条件下与由反应器顶部进入的四氯化硅蒸汽接触时间为14秒钟,然后由另一个输送器将粗产物分子筛从反应器下部移出反应器。反应器的容积为30cm3,本实施例中反应器的容积与接触时间内进入反应器的nay沸石物料松堆体积约相等。反应器中nay沸石与四氯化硅重量比保持在1:0.1。从反应器中移出的粗产物经过抽真空脱气,之后经6倍的水、在90℃搅拌洗涤三次、过滤、干燥后,得到产物h,对其进行相关的测试表征,其结果列于表1。
[0103]
对比例2
[0104]
本对比例与实施例1的区别在于反应空间约等于nay沸石固体物料松堆体积的1.4倍、且反应时间为10秒钟,由以下步骤制备得到:
[0105]
经过400℃干燥6h的nay沸石(松堆密度0.2294cm3/g,90%的颗粒直径(dv 0.9)为14.99微米),经过输送器送至立式反应器(每分钟进入反应器的干燥nay为30克),分子筛由立式反应器的顶部进入反应器向下运动,在400℃条件下与由反应器顶部进入的四氯化硅蒸汽接触时间为10秒钟,然后由另一个输送器将粗产物分子筛从反应器下部移出反应器。反应器的容积为30cm3,本实施例中反应器的容积为接触时间内进入反应器的nay沸石物料松堆体积的约1.4倍。反应器中nay沸石与四氯化硅重量比保持在1:0.1。从反应器中移出的粗产物经过抽真空脱气,之后经6倍的水、在90℃搅拌洗涤三次、过滤、干燥后,得到产物i,对其进行相关的测试表征,其结果列于表1。
[0106]
对比例3
[0107]
本对比例与实施例3的区别在于反应空间约等于nay沸石固体物料松堆体积、且反应时间为20分钟,由以下步骤制备得到:
[0108]
经过600℃干燥2h的nay沸石(松堆密度0.2294cm3/g,90%的颗粒直径(dv 0.9)为14.99微米),经过输送器送至立式反应器(每分钟进入反应器的干燥nay沸石为0.35克),分子筛由立式反应器的顶部进入反应器向下运动,在450℃条件下与由反应器顶部进入的四氯化硅蒸汽接触时间为20分钟,然后由另一个输送器将粗产物分子筛从反应器下部移出反应器。反应器的容积为30cm3,本实施例中反应器的容积与接触时间内进入反应器的nay沸石物料松堆体积约相等。反应器中nay沸石与四氯化硅重量比为1:0.2。从反应器中移出的粗产物经过抽真空脱气,之后经6倍的水、在40℃搅拌洗涤三次、过滤、干燥后,得到产物j,对其进行相关的测试表征,其结果列于表1。
[0109]
对比例4
[0110]
本对比例与实施例6的区别在于反应空间约等于固体物料松堆体积、且接触时间为14秒钟,由以下步骤制备得到:
[0111]
经过600℃干燥4h的低稀土nay沸石(主要稀土元素含量la2o3为0.52wt%,ceo2为1.0wt%,pr6o6为0.11wt%,nd2o3为0.34wt%。松堆密度0.2328cm3/g,90%的颗粒直径(dv 0.9)为10.83微米),经过输送器送至立式反应器(每分钟进入反应器的干燥低稀土nay沸石为30克),分子筛由立式反应器的顶部进入反应器向下运动,在420℃条件下与由反应器顶部进入的四氯化硅蒸汽接触时间为14秒钟,然后由另一个输送器将粗产物分子筛从反应器下部移出反应器。反应器的容积为30cm3,本实施例中反应器的容积与接触时间内进入反应器的低稀土nay沸石物料松堆体积约相等。反应器中低稀土nay沸石与四氯化硅重量比为1:0.15。从反应器中移出的粗产物经过闪蒸,之后经6倍的水、在80℃搅拌洗涤三次、过滤、干燥后,得到产物k,对其进行相关的测试表征,其结果列于表1。
[0112]
实施例8
[0113]
以干基计,取实施例1所得分子筛1.75kg、苏州高岭土2.5kg、铝溶胶粘结剂0.75kg,与适量蒸馏水混合打浆,配置成固含量为28wt%的浆液,经喷雾干燥成型、600℃焙烧、洗涤、干燥,得到催化剂1。
[0114]
以干基计,取对比例1所得分子筛1.75kg、苏州高岭土2.5kg、铝溶胶粘结剂
0.75kg,与适量蒸馏水混合打浆,配置成固含量为28wt%的浆液,经喷雾干燥成型、600℃焙烧、洗涤、干燥,得到催化剂2。
[0115]
催化剂的催化裂化反应评价结果见表2
[0116]
实施例9
[0117]
以干基计,取实施例6所得分子筛1.75kg、苏州高岭土2.5kg、铝溶胶粘结剂0.75kg,与适量蒸馏水混合打浆,配置成固含量为28wt%的浆液,经喷雾干燥成型、600℃焙烧、洗涤、干燥,得到催化剂3。
[0118]
以干基计,取对比例4所得分子筛1.75kg、苏州高岭土2.5kg、铝溶胶粘结剂0.75kg,与适量蒸馏水混合打浆,配置成固含量为28wt%的浆液,经喷雾干燥成型、600℃焙烧、洗涤、干燥,得到催化剂4。
[0119]
催化剂的催化裂化反应评价结果见表3
[0120]
表1
[0121][0122]
从表1的实验数据可以看出,实施例1-7得到的产物不仅相对结晶度高、结晶保留度高,而且晶胞常数低、硅铝比高。而采用对比例1中的实施方式,和实施例1相比,得到的产物结晶度低,晶胞收缩也受到影响、硅铝比提升也不明显;而从对比例2可以看出,当反应空
间升为反应器中nay沸石松堆体积的约1.4倍时,和实施例1相比,情况有所好转,但相对结晶度和硅铝比仍显较低;对比例3和实施例3相比;不仅结晶度低,硅铝比也不高。另外,图2和图3分别为实施例3和对比例3所得改性沸石分子筛的xrd谱图,对比例3的改性沸石分子筛在xrd谱图上有一些特征衍射峰呈现为两个峰,说明由于反应器空间大小和位于反应器内的nay沸石物料的体积不匹配、混合扩散受到影响,且nay沸石与四氯化硅的接触时间过长,导致所得产物性能不好。将对比例4所得产物的结晶度、结晶保留度数据与实施例6相比,也可以看出明显的性能下降。这些实施例和对比例数据进一步说明,相对于进入反应器的nay沸石进料的松堆体积,较大的反应空间应(2倍以上)和短反应时间都是重要的参数。
[0123]
表2
[0124]
产率,wt%催化剂1催化剂2干气2.142.09液化气18.5218.68汽油38.6736.89柴油22.3922.33油浆9.1711.00焦炭9.119.01合计100.00100.00汽油 柴油61.0659.22
[0125]
从表2可以看出,采用本发明的方法,改性的高结晶度沸石(来自实施例1)制备的催化剂1与对比例催化剂2相比具有明显的优势,由其催化减压瓦斯油,所得高价值的汽油收率明显提高,总轻油收率也明显提高,而低价值的油浆的产率明显降低,焦炭产率相当。
[0126]
表3
[0127][0128]
从表3可以看出,采用本发明的方法,以高结晶度、低稀土含量沸石(来自实施例6所得产品)制备的催化剂3与对比催化剂4(沸石来自对比例4所得产品)相比具有明显的优势,由其催化减压瓦斯油,所得高价值的汽油收率明显提高,总轻油收率也明显提高,而低
价值的焦炭和油浆的产率明显降低。
[0129]
当然,本发明还可有其它多种实施例,在不背离本发明精神及其实质的情况下,熟悉本领域的技术人员可根据本发明作出各种相应的改变和变形,但这些相应的改变和变形都应属于本发明权利要求的保护范围。
再多了解一些
本文用于企业家、创业者技术爱好者查询,结果仅供参考。