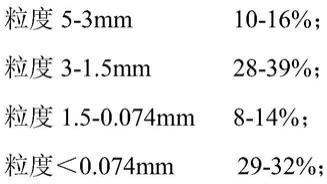
1.本技术涉及耐火材料领域,尤其涉及到一种水泥回转窑用抗扭拉耐磨耐火砖及其制备方法。
背景技术:
2.目前,在大型干法水泥回转窑预热带一般采用硅莫砖或抗剥落高铝砖,硅莫砖导热系数高、体积密度大,虽然具有一定的耐磨性能,但是对窑体的载荷和热损失都较大。抗剥落高铝砖具有良好的耐剥落性能,同样存在体积密度大,对窑体载荷大和热损失高的缺点。
3.因此,本领域技术人员提供了一种水泥回转窑用抗扭拉耐磨耐火砖及其制备方法,以解决上述背景技术中提出的问题。
技术实现要素:
4.针对现有技术的不足,本技术的目的就在于提供一种水泥回转窑用抗扭拉耐磨耐火砖及其制备方法,通过电熔氧化锆、电熔氧化铬、氧化铝超细粉和粘结剂的合理配比,制备一种水泥回转窑用抗扭拉耐磨耐火砖,在转动的窑体内,具有很好的抗扭转和抗拉伸性能,同时又有耐磨的功能,最突出的特点是使窑体载荷下降,热损失减少,长寿节能,经济效益和社会效益突出。
5.本技术采用的技术方案如下:一种水泥回转窑用抗扭拉耐磨耐火砖,由合成中铝熟料、二氧化锆粉、可塑粘土粉、氮化硅铁粉、α-氧化铝粉、结合剂按如下百分比配置而成:
6.合成中铝熟料:
7.二氧化锆粉:粒度<0.074mm
ꢀꢀꢀꢀꢀꢀꢀ
3-11%;
8.可塑粘土粉:粒度<0.074mm
ꢀꢀꢀꢀꢀꢀꢀ
2-9%;
9.氮化硅铁粉:粒度<0.074mm
ꢀꢀꢀꢀꢀꢀꢀ
3-9%;
10.α-氧化铝粉:粒度《0.001mm 3-8%;
11.此外添加结合剂,所述结合剂的加入量为上述组分总重量的3-5%。
12.更进一步的技术方案是,制作结合剂的原料包括工业磷酸50-61%,水28-38%,氢氧化铝粉8-12%。
13.更进一步的技术方案是,所述合成中铝熟料是将铝矾土和硬质粘土共磨成粉,经压砖机压成砖坯,干燥后高温烧结而成;所述合成中铝熟料中al2o3不低于60%,fe2o3不高于2.0%;合成中铝熟料体积密度不高于2.3g/cm3,吸水率小于2%,耐火度不低于1750℃。
14.更进一步的技术方案是,所述二氧化锆粉中zro2不低于95%,fe2o3不高于1.0%。
15.更进一步的技术方案是,所述可塑粘土粉中al2o3不低于33%,fe2o3不高于1.5%。
16.更进一步的技术方案是,所述氮化硅铁粉中si3n4占比为75-80%,fe占比12-17%。
17.更进一步的技术方案是,所述α-氧化铝粉中al2o3不低于99.5%,fe2o3不高于0.5%。
18.更进一步的技术方案是,一种水泥回转窑用抗扭拉耐磨耐火砖的制备方法,其特征在于:包括以下步骤:
19.(1)将工业磷酸、水、氢氧化铝粉按比例加入到容器中,加热到68-72℃,搅拌20-40分钟,反应成透明状胶体后取出,冷却至常温备用;所述工业磷酸的浓度为85%;
20.(2)依次将5-3mm的合成中铝熟料颗粒、3-1.5mm的合成中铝熟料颗粒、1.5-0.074mm的合成中铝熟料颗粒、2/3的步骤(1)制备的结合剂、二氧化锆粉、氮化硅铁粉、α-氧化铝粉、粒度小于0.074mm合成中铝熟料、可塑粘土粉加入到强制式搅拌机中混合1-3分钟,再加入1/3的步骤(1)制备的结合剂,然后混合2-3分钟,卸料备用;
21.(3)成型:将步骤(2)混合好的物料压制成砖坯;
22.(4)干燥:将步骤(3)成型好的砖坯送入干燥窑进行干燥,干燥窑进口温度50-70℃,出口温度95-105℃;
23.(5)烧成:将步骤(4)干燥好的砖坯送入隧道窑烧成,烧成温度为1380
±
50℃;
24.(6)冷却:将步骤(5)出窑后的耐火砖制品冷却至常温。
25.本技术的有益效果在于:
26.本技术通过对不同原料的优化对比,选择适合的原材料,采用科学的颗粒级配,制备出一种水泥回转窑用抗扭拉耐磨耐火砖,在转动的窑体内,具有很好的抗扭转和抗拉伸性能,同时又有耐磨的功能,最突出的特点是使窑体载荷下降,热损失减少,比传统耐火砖降低负荷23%,筒体温度降低46%,经济效益和社会效益突出。
具体实施方式
27.下面将结合本技术实施例,对本技术实施例中的技术方案进行清楚、完整地描述,显然,所描述的实施例仅仅是本技术一部分实施例,而不是全部的实施例。基于本技术中的实施例,本领域普通技术人员在没有做出创造性劳动前提下所获得的所有其他实施例,都属于本技术保护的范围。
28.实施例1
29.一种水泥回转窑用抗扭拉耐磨耐火砖,其特征在于:由合成中铝熟料、二氧化锆粉、可塑粘土粉、氮化硅铁粉、α-氧化铝粉、结合剂按如下百分比配置而成:
30.合成中铝熟料:
31.二氧化锆粉:粒度<0.074mm
ꢀꢀꢀꢀꢀꢀꢀ
5%;
32.可塑粘土粉:粒度<0.074mm
ꢀꢀꢀꢀꢀꢀꢀ
4%;
33.氮化硅铁粉:粒度<0.074mm
ꢀꢀꢀꢀꢀꢀꢀ
4%;
34.α-氧化铝粉:粒度《0.001mm
ꢀꢀꢀꢀꢀꢀꢀꢀ
4%;
35.此外添加结合剂,所述结合剂的加入量为上述组分总重量的3.5%。
36.其中,制作结合剂的原料包括工业磷酸55%,水35%,氢氧化铝粉10%。
37.其中,所述合成中铝熟料中al2o3不低于60%,fe2o3不高于2.0%;合成中铝熟料体积密度不高于2.3g/cm3,吸水率小于2%,耐火度不低于1750℃。
38.其中,二氧化锆粉中zro2不低于95%,fe2o3不高于1.0%。
39.其中,可塑粘土粉中al2o3不低于33%,fe2o3不高于1.5%。
40.其中,氮化硅铁粉中si3n4占比为75-80%,fe占比12-17%。
41.其中,α-氧化铝粉中al2o3不低于99.5%,fe2o3不高于0.5%。
42.水泥回转窑用抗扭拉耐磨耐火砖的制备方法,包括以下步骤:
43.(1)将工业磷酸、水、氢氧化铝粉按比例加入到容器中,加热到70℃,搅拌30分钟,反应成透明状胶体后取出,冷却至常温备用;所述工业磷酸的浓度为85%;
44.(2)依次将5-3mm的合成中铝熟料颗粒、3-1.5mm的合成中铝熟料颗粒、1.5-0.074mm的合成中铝熟料颗粒、2/3-的结合剂、二氧化锆粉、氮化硅铁粉、α-氧化铝粉、粒度小于0.074mm合成中铝熟料、可塑粘土粉加入到强制式搅拌机中混合2分钟,再加入1/3的结合剂,然后混合2.5分钟,卸料备用;
45.(3)成型:采用630吨压砖机,将混合好的物料压制成砖坯;
46.(4)干燥:将成型好的砖坯进入80米隧道干燥窑进行干燥,干燥窑进口温度50-70℃,出口温度95-105℃,每25分钟推一车;
47.(5)烧成:将干燥好的砖坯进入120米高温节能隧道窑烧成,最高烧成温度1380℃,每45分钟推一车;
48.(6)冷却:出窑后的耐火砖制品进行自然冷却6小时后,工业风机冷却至常温。
49.实施例2
50.一种水泥回转窑用抗扭拉耐磨耐火砖,其特征在于:由合成中铝熟料、二氧化锆粉、可塑粘土粉、氮化硅铁粉、α-氧化铝粉、结合剂按如下百分比配置而成:
51.合成中铝熟料:
52.二氧化锆粉:粒度<0.074mm
ꢀꢀꢀꢀꢀꢀꢀ
4%;
53.可塑粘土粉:粒度<0.074mm
ꢀꢀꢀꢀꢀꢀꢀ
4%;
54.氮化硅铁粉:粒度<0.074mm
ꢀꢀꢀꢀꢀꢀꢀ
4%;
55.α-氧化铝粉:粒度《0.001mm 4%;
56.此外添加结合剂,所述结合剂的加入量为上述组分总重量的4%。
57.其中,制作结合剂的原料包括工业磷酸55%,水35%,氢氧化铝粉10%。
58.其中,所述合成中铝熟料中al2o3不低于60%,fe2o3不高于2.0%;合成中铝熟料体积密度不高于2.3g/cm3,吸水率小于2%,耐火度不低于1750℃。
59.其中,二氧化锆粉中zro2不低于95%,fe2o3不高于1.0%。
60.其中,可塑粘土粉中al2o3不低于33%,fe2o3不高于1.5%。
61.其中,氮化硅铁粉中si3n4占比为75-80%,fe占比12-17%。
62.其中,α-氧化铝粉中al2o3不低于99.5%,fe2o3不高于0.5%。
63.水泥回转窑用抗扭拉耐磨耐火砖的制备方法,包括以下步骤:
64.(1)将工业磷酸、水、氢氧化铝粉按比例加入到容器中,加热到70℃,搅拌32分钟,反应成透明状胶体后取出,冷却至常温备用;所述工业磷酸的浓度为85%;
65.(2)依次将5-3mm的合成中铝熟料颗粒、3-1.5mm的合成中铝熟料颗粒、1.5-0.074mm的合成中铝熟料颗粒、2/3-的结合剂、二氧化锆粉、氮化硅铁粉、α-氧化铝粉、粒度小于0.074mm合成中铝熟料、可塑粘土粉加入到强制式搅拌机中混合2分钟,再加入1/3的结合剂,然后混合2.5分钟,卸料备用;
66.(3)成型:采用630吨压砖机,将混合好的物料压制成砖坯;
67.(4)干燥:将成型好的砖坯进入80米隧道干燥窑进行干燥,干燥窑进口温度50-70℃,出口温度95-105℃,每25分钟推一车;
68.(5)烧成:将干燥好的砖坯进入120米高温节能隧道窑烧成,最高烧成温度1380℃,每45分钟推一车;
69.(6)冷却:出窑后的耐火砖制品进行自然冷却6小时后,工业风机冷却至常温。
70.实施例3
71.一种水泥回转窑用抗扭拉耐磨耐火砖,其特征在于:由合成中铝熟料、二氧化锆粉、可塑粘土粉、氮化硅铁粉、α-氧化铝粉、结合剂按如下百分比配置而成:
72.合成中铝熟料:
[0073][0074]
二氧化锆粉:粒度<0.074mm
ꢀꢀꢀꢀꢀꢀꢀ
4%;
[0075]
可塑粘土粉:粒度<0.074mm
ꢀꢀꢀꢀꢀꢀꢀ
4%;
[0076]
氮化硅铁粉:粒度<0.074mm
ꢀꢀꢀꢀꢀꢀꢀꢀ
5%;
[0077]
α-氧化铝粉:粒度《0.001mm
ꢀꢀꢀꢀꢀꢀꢀꢀ
4%;
[0078]
此外添加结合剂,所述结合剂的加入量为上述组分总重量的4%。
[0079]
其中,制作结合剂的原料包括工业磷酸55%,水35%,氢氧化铝粉10%。
[0080]
其中,所述合成中铝熟料中al2o3不低于60%,fe2o3不高于2.0%;合成中铝熟料体积密度不高于2.3g/cm3,吸水率小于2%,耐火度不低于1750℃。
[0081]
其中,二氧化锆粉中zro2不低于95%,fe2o3不高于1.0%。
[0082]
其中,可塑粘土粉中al2o3不低于33%,fe2o3不高于1.5%。
[0083]
其中,氮化硅铁粉中si3n4占比为75-80%,fe占比12-17%。
[0084]
其中,α-氧化铝粉中al2o3不低于99.5%,fe2o3不高于0.5%。
[0085]
水泥回转窑用抗扭拉耐磨耐火砖的制备方法,包括以下步骤:
[0086]
(1)将工业磷酸、水、氢氧化铝粉按比例加入到容器中,加热到70℃,搅拌32分钟,反应成透明状胶体后取出,冷却至常温备用;所述工业磷酸的浓度为85%;
[0087]
(2)依次将5-3mm的合成中铝熟料颗粒、3-1.5mm的合成中铝熟料颗粒、1.5-0.074mm的合成中铝熟料颗粒、2/3-的结合剂、二氧化锆粉、氮化硅铁粉、α-氧化铝粉、粒度小于0.074mm合成中铝熟料、可塑粘土粉加入到强制式搅拌机中混合2分钟,再加入1/3的结合剂,然后混合2.5分钟,卸料备用;
[0088]
(3)成型:采用630吨压砖机,将混合好的物料压制成砖坯;
[0089]
(4)干燥:将成型好的砖坯进入80米隧道干燥窑进行干燥,干燥窑进口温度50-70℃,出口温度95-105℃,每25分钟推一车;
[0090]
(5)烧成:将干燥好的砖坯进入120米高温节能隧道窑烧成,最高烧成温度1380℃,每45分钟推一车;
[0091]
(6)冷却:出窑后的耐火砖制品进行自然冷却6小时后,工业风机冷却至常温。
[0092]
成品水泥回转窑用抗扭拉耐磨耐火砖的各项性能:
[0093]
抽取实施例1、2、3中的产品检测al2o3含量、fe2o3含量、密度、显气孔率、耐压强度、高温抗折强度、热震稳定性等指标,具体如表1所示:
[0094]
表1本技术成品的各项性能参数
[0095][0096]
由表1可知,本技术的水泥回转窑用抗扭拉耐磨耐火砖在高温条件下具有较好的抗扭转和抗拉伸性能,同时又有耐磨的功能,最突出的特点是使窑体载荷下降,热损失减少,经济效益和社会效益突出。
[0097]
其中:耐火原料取样执行gb/t17617;
[0098]
定形耐火制品验收抽样检验规则执行gb/t10325;
[0099]
定形耐火制品试样制备方法执行gb/t7321;
[0100]
数值修约规则与极限数值的表示和判定执行gb/t8170;
[0101]
al2o3的检测执行gb/t6900;
[0102]
fe2o3的检测执行gb/t6900;
[0103]
体积密度的检测执行gb/t2997;
[0104]
显气孔率的检测执行gb/t2997;
[0105]
常温耐压强度的检测执行gb/t5072;
[0106]
荷重软化开始温度的检测执行yb/t370;
[0107]
热膨胀率的检测执行gb/t7320;
[0108]
导热系数的检测执行gb/t5990;
[0109]
热震稳定性的检测执行gb/t30873;
[0110]
常温耐磨性的检测执行gb/t1830。
[0111]
以上所述仅为本技术的较佳实施例而已,并不用以限制本技术,凡依本技术范围所做的均等变化与修饰,皆应属本技术的涵盖范围。此外,应当理解,虽然本说明书按照实施方式加以描述,但并非每个实施方式仅包含一个独立的技术方案,说明书的这种叙述方式仅仅是为清楚起见,本领域技术人员应当将说明书作为一个整体,各实施例中的技术方案也可以经适当组合,形成本领域技术人员可以理解的其他实施方式。
再多了解一些
本文用于企业家、创业者技术爱好者查询,结果仅供参考。