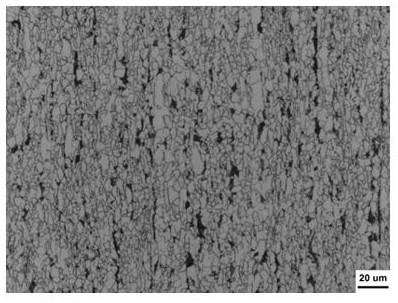
一种超薄超宽低温钢lt-fh32的生产方法
技术领域
1.本发明属于冶金技术领域,涉及一种超薄超宽低温钢板的生产方法。
背景技术:
2.超大型液化气体运输船(very large gas carrier,vlgc)是液化气船市场上的一型高技术、高附加值船舶,由于其技术含量高,开发难度大。超大型液化石油气船一般采用低温钢建造,以一条8.4万m3的vlgc为例,每条船低温钢板的需求量在1万吨左右,其中10mm以下超薄板就超过1000吨,而最关键的液货仓由于要减少焊道的影响,设计时需要采用超宽的钢板。对于宽度超过3800mm的钢板炉卷轧机无法生产,必须用中厚板轧机生产,而超薄超宽规格钢板用中厚板轧机很难实现控制轧制,必须采用热轧工艺,才能保证轧后钢板的板型良好,但对于低温钢,采用热轧工艺钢板的韧性难以达到要求。
技术实现要素:
3.本发明的目的在于提供一种超薄超宽低温钢特别是lt-fh32的生产方法,厚度为6~10mm,宽度为3800~4300mm,能较好地满足超大型液化石油气船用低温钢板lt-fh32的使用需求:屈服强度≥320mpa、抗拉强度≥450mpa、延伸率≥22%、-60℃夏比冲击功≥60j、屈强比≤0.8。
4.本发明的技术方案:一种超薄超宽低温钢lt-fh32的生产方法,所述钢板厚度为6~10mm,宽度为3800~4300mm,钢的成分按重量百分比计为c=0.05%~0.06%,si=0.10%~0.50%,mn=1.30%~1.40%,p≤0.012%,s≤0.003%,nb=0.010%~0.015%,ti=0.008%~0.02%,al=0.015%~0.05%,其余为fe和不可避免的杂质;金相组织为铁素体 珠光体,晶粒度为10~12级;关键工艺步骤包括:(1)开坯:按照上述成分采用转炉冶炼并浇注成板坯;然后进行加热并高温轧制成60~100mm的一火坯,待一火坯冷却后,采用火焰切割将一火坯切割成长度为成品宽度 50~80mm尺寸的小板坯;(2)轧制:二次进炉,快速加热到1220
±
20℃,出炉后长当宽轧制,采用两阶段轧制,第一阶段不展宽,横轧到底,中间坯为3~5倍成品厚度;第二阶段控轧轧制,开轧温度850~880℃,终轧温度控制在770~820℃;(3)预矫:轧后进行预矫,矫直速度0.3~0.35m/s,然后空冷至室温。
5.本发明的技术原理:本发明在成分设计上,通过采用低碳高锰、nb-ti-al多元微合金化成分设计来细化晶粒提高钢板的低温韧性。 c含量过低会降低强度,c含量增高虽然能够提高强度和降低ar3温度,但会在空冷过程中增加珠光体的含量和晶粒尺寸,严重恶化超薄钢板的低温韧性,因此控制最终碳含量0.05~0.06%;锰是弱碳化物形成元素,它可以降低奥氏体转变温度,细化铁素体晶粒,对提高钢板强度和韧性有益,因此,在成分设计时,锰设计下限1.30%,但当含量超过1.50%时,中心偏析加重,造成低温韧性严重恶化;为了确保
超薄超宽钢板的低温韧性,钢水必须具有较高的纯净度,p、s作为有害杂质元素,含量越低越好,考虑到制造成本,最终控制终点p≤0.012%,s≤0.003%;nb作为一种重要的微合金元素,添加适量的nb对轧制过程中推迟再结晶的发生、细化晶粒和析出强化的作用十分明显,为合理匹配强韧性和屈强比,通过奥氏体中nbc的热力学计算,以及nbc析出对晶粒尺寸影响的试验摸索,需要严格控制铌含量在0.010~0.015%之间;钢中进行微ti处理,添加0.008以上的ti有利于坯料加热过程中形成tin钉扎晶界,抑制奥氏体晶粒过分长大,并且在轧制过程中细化晶粒,改善钢板韧性的作用,但ti含量大于0.02%时,会形成部分ti复合夹杂物,反而成为钢中的断裂源,对钢的低温韧性非常有害。
6.本发明在工艺设计上,通过二火成材以及控制加热温度、轧制温度及道次压下率,特别是设定较低的二阶段轧制温度来控制轧后奥氏体晶粒尺寸及其均匀性和压扁程度;通过二火长当宽轧制可有效减少轧制道次,增加一阶段轧制道次压下率,避免展宽道次对超薄超宽板温降和板型的影响,保证二阶段轧制控制在完全非再结晶温度区间,消除混晶对钢板低温韧性的影响,并有效改善轧后板型;通过多道次低速恒定的高温预矫,改善钢板残余应力的均匀性,确保钢板的板型和不平度要求。
7.本发明的有益效果:本发明针对炉卷轧机无法生产的3800mm以上超薄超宽板,利用二火成材 长当宽轧制,配以合适的化学成分,打破中厚板轧机生产超薄超宽规格钢板的控轧能力不足的特点,生产出的钢板具有良好的综合力学性能:屈服强度≥320mpa、抗拉强度≥450mpa、延伸率≥22%、-60℃夏比冲击功≥60j、屈强比≤0.8。钢板板型良好,不平度≤3mm/m,同时钢板组织均匀、性能均匀、残余应力小、表现出优异的低温韧性。本发明生产的超薄超宽lt-fh32低温钢板具有高附加值,可批量供货,能够很好地满足超大型液化石油气船(vlgc)用低温钢板的使用需求。
附图说明
8.图1为本发明实施例1钢板金相组织照片。
9.图2为本发明对比例1钢板金相组织照片。
具体实施方式
10.根据本发明所述的生产方法,通过120t转炉冶炼、lf炉精炼、rh炉真空处理,并浇注成连铸坯,然后在5000mm双机架中厚板生产线上轧制成成品。下面通过实施例和对比例对本发明作进一步的说明。实施例和对比例中钢板的化学成分见表1。
11.表1 实施例和对比例中钢板的化学成分及ceq(重量,%)
实施例和对比例钢板的关键工艺参数如下。
12.实施例1钢板厚度8mm,钢板宽度为4200mm。连铸坯厚度为300mm,二火轧制,一火坯厚度80mm;二次进炉,加热温度为1236℃,出炉后长当宽轧制,采用两阶段轧制,中间坯30mm,第二阶段开轧温度864℃,终轧温度为782℃,轧后进行预矫,矫直速度0.35m/s,然后空冷至室温。
13.对比例1钢板厚度8mm,钢板宽度为3600mm。连铸坯厚度为300mm,二火轧制,一火坯厚度80mm;二次进炉,加热温度为1228℃,出炉后正常展宽轧制,采用两阶段轧制,中间坯30mm,为保证轧后板型,第二阶段开轧温度860℃,终轧温度为779℃,轧后进行预矫,矫直速度0.35m/s,然后空冷至室温。
14.实施例2钢板厚度10mm,钢板宽度为4280mm。连铸坯厚度为300mm,二火轧制,一火坯厚度100mm;二次进炉,加热温度为1236℃,出炉后长当宽轧制,采用两阶段轧制,中间坯40mm,第二阶段开轧温度856℃,终轧温度为782℃,轧后进行预矫,矫直速度0.30m/s,然后空冷至室温。
15.对比例2钢板厚度10mm,钢板宽度为4280mm。连铸坯厚度为300mm,二火轧制,一火坯厚度100mm;二次进炉,加热温度为1233℃,出炉后长当宽轧制,采用两阶段轧制,中间坯40mm,第二阶段开轧温度858℃,终轧温度为783℃,轧后进行预矫,矫直速度0.30m/s,然后空冷至室温。
16.实施例3钢板厚度6mm,钢板宽度为4050mm。连铸坯厚度为260mm,二火轧制,一火坯厚度60mm;二次进炉,加热温度为1232℃,出炉后长当宽轧制,采用两阶段轧制,中间坯20mm,第二阶段开轧温度875℃,终轧温度为770℃,轧后进行预矫,矫直速度0.35m/s,然后空冷至室温。
17.对比例3钢板厚度6mm,钢板宽度为3400mm。连铸坯厚度为180mm,一火轧制,加热温度为
1235℃,出炉后正常展宽轧制,采用两阶段轧制,中间坯50mm,为保证轧后板型,第二阶段开轧温度951℃,终轧温度为784℃,轧后进行预矫,矫直速度0.35m/s,然后空冷至室温。
18.实施例和对比例钢板的综合力学性能见表2。
19.表2 实施例和对比例钢板的综合力学性能其中,实施例1、对比例1、实施例2以及对比例2的冲击试样尺寸为10mm
×
7.5mm
×
55mm,试验结果应不小于规定值的75%;实施例2和对比例2的冲击试样尺寸为10mm
×
5mm
×
55mm,试验结果应不小于规定值的50%。
20.本发明实施例1、实施例2和实施例3钢板的综合力学性能满足要求。对实施例钢板进行金相组织观察,微观组织由细晶粒的铁素体 珠光体组织结构,晶粒度10-12级,如图1所示。而对比例钢板的综合力学性能不完全满足要求,对比例1与实施例1成分设计相同,采用常规二火展宽轧制,为保板型,轧制最大宽度为3600mm,展宽后第一阶段压缩比不足,第二阶段开轧温度较高,导致钢板晶粒度相对较大,且不均匀,其-60℃冲击功较差,金相组织如图2所示。而对比例2钢为桥梁板q345qe,采用本发明的轧制方式,其强度和低温韧性都满足要求,但由于合金元素nb等含量较高,其屈强比高于标准;对比例3为船板eh36,为提高韧性,成分设计加了0.25%的ni,采用常规一火展宽轧制,为保板型,轧制最大宽度为3400mm,可以看出虽然添加了ni元素,但由于采用传统热轧工艺,低温冲击韧性并没有得到改善。
21.因此,采用常规轧制方式,在工业化生产中超宽超薄钢板很难稳定控制低温韧性和屈强比同时达到要求,由此充分显示出本发明在成分和工艺设计上的巧妙、兼顾及独特性。
再多了解一些
本文用于企业家、创业者技术爱好者查询,结果仅供参考。