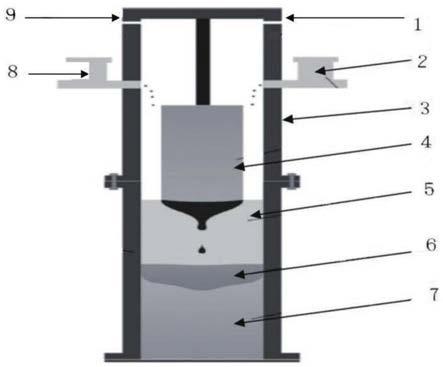
1.本发明属于钢铁冶金技术领域,具体涉及一种真空感应炉与加压电渣炉冶炼高氮模具钢的方法。
背景技术:
2.高氮模具钢是一类特殊的合金钢,属于马氏体不锈钢。在成分中添加氮元素,能够起到减轻模具钢的元素偏析、提高耐蚀性能、提高抛光性能、改善切削性能等作用;氮可以增加合金钢的屈服强度,每增加0.001%氮,可增加约6mpa的强度,并且与工艺条件无关。采用新的合金配比还可以节约钢中合金元素含量,是生产高端模具钢的有效途径。虽然氮在钢中的有益作用已经得到证实,但是由于氮在马氏体不锈钢中的溶解度很小(1600℃时仅为0.045wt%),因此,采用何种方法来得到马氏体不锈钢中高的氮含量是国内外研究的一个重点方向。工业化生产时,模具钢常规的冶炼方法为电炉 炉外精炼(或 电渣重熔)。在常压下,电炉冶炼模具钢时采用吹氮或添加氮化合金料来增加氮元素的含量,然而钢液中最大溶解的氮不超过0.20%,如果继续吹氮或添加氮化合金料,氮元素会在钢液中形成气泡溢出,浇注钢锭的表面会形成气泡缺陷,影响质量,而且氮化合金料的添加会增加模具钢中的杂质,因此,为得到高纯净度高氮模具钢,必须采用特殊的冶炼方法。现今,冶炼过程中的氮合金化仍然是含氮钢的主要生产方法。不锈钢的冶炼采用高压熔炼试验方法、反压铸造法、加压电渣重熔、电渣加热高压渗氮、高压下等离子熔炼、粉末冶金等方法。由于受到设备和工艺的限制,目前国内外高氮(氮含量0.20%以上)模具钢并没有形成大规模的工业化生产。
技术实现要素:
3.本发明公开一种真空感应炉与加压电渣炉冶炼高氮模具钢的方法,即氮含量为0.20%~0.40%的高氮模具钢冶炼方法,以填补高氮模具钢冶炼工艺的空白。
4.为实现上述目的,技术方案是采取“真空感应炉 加压电渣炉”的冶炼方法,生产氮含量为0.20%~0.40%的模具钢;真空感应炉和加压电渣炉冶炼过程中分别加入(fecr)n和si3n4两种氮化合金料,以达到氮的技术要求目标。
5.具体工艺步骤:
6.1.真空感应炉工艺:
7.①
真空感应炉浇注电极棒中的氮含量目标为0.08%~0.10%。
8.②
真空感应炉使用6t坩埚,冶炼分为五个阶段:准备阶段、真空熔化阶段、真空精炼阶段、充惰性气体阶段和浇注电极棒。
9.③
准备阶段采用精钢材、纯金属料和合金料搭配装料,炉中不加入硅铁或少量加入,主要是因为后期加压电渣重熔过程中加入的氮化合金料中含硅元素。
10.④
在熔化和精炼阶段炉内抽真空不大于5pa,过程中每隔10min搅拌一次,在精炼阶段后期添加脱氧剂,使钢液中的氧含量小于10
×
10-6
。
11.⑤
合金成分调整合格后破真空,炉内充入氩气,充氩压力在18000pa~25000pa,在此阶段后期向炉中加入(fecr)n,同时调入脱氧剂,待全熔后即翻炉浇注电极棒。
12.2.加压电渣炉工艺:
13.①
加压电渣炉重熔电渣锭
⑺
中氮含量目标为0.20%~0.40%。
14.②
加压电渣炉使用φ610mm结晶器
⑶
,冶炼分为五个阶段:准备阶段、造渣阶段、正常熔炼阶段、充填阶段和脱锭。
15.③
采用φ400mm电极棒
⑷
重熔,电极棒
⑷
表面进行车光处理,去掉电极表面的氧化皮和达到0.65的充填比,并切取本钢种底垫。
16.④
准备阶段在底垫上铺5kg~10kg的(fecr)n,加压电渣炉上方的渣料存储罐
⑻
中加入120kg~150kg的预熔渣,渣系为cac433(caf2:al2o3:cao=40%:30%:30%),并在渣中加入5kg~10kg的si3n4;在加压电渣炉上方的合金加料器
⑵
中加入50kg~80kg的si3n4,用于熔炼过程中加入。
17.⑤
准备好后开始给电起弧,进入造渣阶段,此阶段持续1h,造渣阶段大电流使渣料熔化为液态渣料
⑸
,同时电极棒
⑷
开始熔化,电极棒
⑷
的熔化速率为450kg/h~550kg/h;造渣开始10min~15min后由炉内氮气进口
⑼
充入氮气,压力开始提升,并在造渣结束前炉内压力达到设定的8.0bar~12.0bar;与此同时,加压电渣炉上方的合金加料器
⑵
开始向炉内加入si3n4,加入速率为熔速的1.45%~1.55%。
18.⑥
正常熔炼阶段,保持电流和电压平稳,保持炉内压力为8.0bar~12.0bar并与冷却水压力平衡;保持熔化速率450kg/h~550kg/h稳定,每分钟向炉中加入一次si3n4,并保持加入速率为1.45%~1.55%稳定;冷却水温差不高于8℃;保持熔炼阶段的各项参数稳定可使si3n4在金属熔池
⑹
中均匀熔化,成品材的氮元素由内到外均匀分布。
19.⑦
在电极棒
⑷
重量剩余200kg~250kg时开始进入充填阶段,此阶段持续40min~60min,保持炉内压力8.0bar~12.0bar稳定,熔化速率由450kg/h~550kg/h开始阶梯式降低,此时解除熔化速率与si3n4加入速率的对应关系,保持si3n4加入速率为1.45%~1.55%,以保证电渣锭
⑺
充填端的氮元素达到目标。
20.⑧
熔化结束后停电,冷却1h后脱锭,钢锭罩冷后温送退火。
21.3.化学成分检验
22.①
对钢锭的充填端
⑽
和底垫端(22)取样分析横截面上不同位置
⑾
、
⑿
、
⒀
和
⒆
、
⒇
、(21)的化学成分。
23.②
从充填端
⑽
到底垫端(22)的钢锭表面
⒁
、
⒂
、
⒃
、
⒄
、
⒅
5个点取样分析化学成分。
24.对本发明点的说明:
25.本发明首次提出采用真空感应炉 加压电渣炉的方法冶炼0.20%~0.40%的高氮模具钢。国内外马氏体不锈钢中添加氮元素的研究和实践较多,而且大部分是在实验室下采用加压感应炉熔炼、加压电渣炉吹氮、加压感应炉 加压电渣炉联合或二次加压电渣等方法。本发明所设计的冶炼方法已经过工业化生产实践验证,不同的是钢中增氮需经两个冶炼过程:第一,在真空感应炉冶炼时需要控制低氧、低硅,添加(fecr)n使氮达到0.08%~0.10%,真空感应炉冶炼电极棒即要保证脱气效果又要提高氮含量;第二,采用一次加压电渣炉重熔,过程中在8.0bar~12.0bar的压力状态下加入si3n4合金料使氮达到0.20%~
0.40%的目标,并使硅、氧满足标准要求。
26.本发明与现有技术相比具有下列优点:
27.①
在真空感应炉中增氮,可减少后期加压电渣炉si3n4的添加,降低了成本,提高了氮的均匀性和合格率。
28.②
加压电渣重熔添加的si3n4使钢液获得更高的氮含量,工艺的稳定性保证氮元素的分布均匀性;电极棒经过重熔净化,使钢锭的氧含量进一步降低,具有比其它冶炼方式更好的组织和性能;冶炼工艺生产效率高,氮含量控制精准,便于大规模的工业化生产。
附图说明
29.图1是加压电渣炉示意图;
30.图2是电渣锭检验化学成分的位置分布图。
31.附图图标:1-氮气出口、2-合金加料器、3-结晶器、4-电极棒、5-液态渣料、6-金属熔池、7-电渣锭、8-渣料存储罐、9-氮气进口、10-充填端、11-上中心、12-上半径处、13-上边部、14-1点、15-2点、16-3点、17-4点、18-5点、19-下边部、20-下半径处、21-下中心、22-底垫端。
具体实施方式
32.下面实施例结合附图详细说明本发明。
33.按照上述技术方案实施,提供以下三项优选实施例。
34.实施例1
35.采用真空感应炉 加压电渣炉冶炼高氮模具钢φ610mm电渣锭,目标钢种为40cr13nin0.3,合金成分和电渣锭目标值如表1。
36.表1
[0037][0038]
⑴
根据钢种的目标成分和工艺要求,真空感应炉的配料目标按照表2执行。
[0039]
表2
[0040]
[0041]
⑵
选择6t坩埚的真空感应炉,充氩阶段保证氩气压力在20000pa,合金成分达到目标值后调入15kg的(fecr)n用于增氮,调入ni-mg和si-ca粉用于脱氧。
[0042]
⑶
电极棒4尺寸为φ400mm,并清理干净表面的氧化皮。
[0043]
⑷
加压电渣炉(见图1)准备时在本钢种底垫上铺设5kg的(fecr)n,选用cac433渣系,渣量120kg,渣中加入8kg的si3n4,结晶器尺寸为φ610mm。
[0044]
⑸
造渣开始12min后由氮气进口9充氮气压力开始提升,20min后压力升至设定的8bar;熔化速率设定480kg/h,实际为478kg/h~485kg/h,由合金加料器2加入si3n4合金料的速率为1.45%,并随熔化速率的波动而波动。
[0045]
⑹
造渣1h后进入正常熔炼阶段,熔化速率、si3n4合金料加入速率与造渣阶段相同,压力和冷却水压力7.9bar~8.3bar电流为11ka~16ka,电压为60v~66v,冷却水温差为7.2℃~7.7℃,熔炼过程各项参数稳定。
[0046]
⑺
在电极棒4重量剩余244kg时开始进入充填阶段,充填总时间为47min,充填阶段压力维持在8.0bar左右,熔速阶梯式降低,si3n4合金料加入速率1.45%。
[0047]
⑻
充填结束,停电泄压,电渣锭7在结晶器3中冷却1h,脱锭后电渣锭罩冷10h,罩冷后温送退火,电渣锭7表面光滑无缺陷。
[0048]
⑼
在退火后的钢锭充填端10和底垫端22横截面11、12、13和19、20、21各位置以及钢锭表面14、15、16、17、18各位置取样分析(见图2),结果如下表,除氮、硅、氧其余元素无烧损,因此表中只列出上述三个元素的检测值;从分析结果来看,电渣锭7的截面和轴向的氮元素分布均匀,并得到了符合标准要求的硅和较低的氧含量,见表3。
[0049]
表3
[0050][0051]
实施例2
[0052]
采用真空感应炉 加压电渣炉冶炼高氮模具钢φ610mm电渣锭,目标钢种为30cr13nin0.35,合金成分和电渣锭目标值如表4。
[0053]
表4
[0054][0055]
⑴
根据钢种的目标成分和工艺要求,真空感应炉的配料目标按照表5执行:
[0056]
表5
[0057][0058]
⑵
选择6t坩埚的真空感应炉,充氩阶段保证氩气压力在20000pa,合金成分达到目标值后调入16kg的(fecr)n用于增氮,调入ni-mg和si-ca粉用于脱氧。
[0059]
⑶
电极棒4尺寸为φ400mm,并清理干净表面的氧化皮。
[0060]
⑷
加压电渣炉准备时在本钢种底垫上铺设5kg的(fecr)n,选用cac433渣系,渣量120kg,渣中加入10kg的si3n4,结晶器尺寸为φ610mm。
[0061]
⑸
造渣开始12min后由氮气进口9充氮气压力开始提升,20min后压力升至设定的8bar。熔化速率设定480kg/h,实际为479kg/h~483kg/h,由合金加料器2加入si3n4合金料的入速率为1.50%,并随熔化速率的波动而波动。
[0062]
⑹
造渣1h后进入正常熔炼阶段,熔化速率、si3n4合金料加入速率与造渣阶段相同,压力和冷却水压力7.8bar~8.3bar电流为11ka~15ka,电压为60v~65v,冷却水温差为7.3℃~7.8℃,熔炼过程各项参数稳定。
[0063]
⑺
在电极棒4重量剩余229kg时开始进入充填阶段,充填总时间为40min,充填阶段压力维持在8.0bar左右,熔速阶梯式降低,si3n4合金料加入速率1.50%。
[0064]
⑻
充填结束,停电泄压,电渣锭7在结晶器中冷却1h,脱锭后电渣锭罩冷12h,罩冷后温送退火,电渣锭7表面光滑无缺陷。
[0065]
⑼
在退火后的钢锭充填端10和底垫端22横截面11、12、13和19、20、21各位置以及钢锭表面14、15、16、17、18各位置取样分析(见图2),结果如下表,除氮、硅、氧其余元素无烧损,因此表中只列出上述三个元素的检测值;从分析结果来看,电渣锭7的截面和轴向的氮元素分布均匀,并得到了符合标准要求的硅和较低的氧含量,见表6。
[0066]
表6
[0067][0068][0069]
实施例3
[0070]
采用真空感应炉 加压电渣炉冶炼高氮模具钢φ610mm钢锭,目标钢种为30cr15mo1nin0.4,合金成分和电渣锭目标值如表7。
[0071]
表7
[0072][0073]
⑴
根据钢种的目标成分和工艺要求,真空感应炉的配料目标按照表8执行。
[0074]
表8
[0075][0076]
⑵
选择6t坩埚的真空感应炉,充氩阶段保证氩气压力在25000pa,合金成分达到目标值后调入15kg的(fecr)n用于增氮,调入ni-mg和si-ca粉用于脱氧。
[0077]
⑶
电极棒4尺寸为φ400mm,并清理干净表面的氧化皮。
[0078]
⑷
加压电渣炉准备时在本钢种底垫上铺设6kg的(fecr)n,选用cac433渣系,渣量
120kg,渣中加入10kg的si3n4,结晶器尺寸为φ610mm。
[0079]
⑸
造渣开始10min后由氮气进口9充氮气压力开始提升,20min后压力升至设定的10.0bar。熔化速率设定480kg/h,实际为478kg/h~483kg/h,由合金加料器2加入si3n4合金料的速率为1.55%,并随熔化速率的波动而波动。
[0080]
⑹
造渣1h后进入正常熔炼阶段,熔化速率、si3n4合金料加入速率与造渣阶段相同,压力和冷却水压力9.9bar~10.3bar电流为10ka~16ka,电压为60v~66v,冷却水温差为7.2℃~7.8℃,熔炼过程各项参数稳定。
[0081]
⑺
在电极棒4重量剩余232kg时开始进入充填阶段,充填总时间为40min,充填阶段压力维持在10.0bar左右,熔速阶梯式降低,si3n4合金料加入速率1.55%。
[0082]
⑻
充填结束,停电泄压,电渣锭7在结晶器中冷却1h,脱锭后电渣锭罩冷12h,罩冷后温送退火,电渣锭7表面光滑无缺陷。
[0083]
⑼
在退火后的钢锭充填端10和底垫端22横截面11、12、13和19、20、21各位置以及钢锭表面14、15、16、17、18各位置取样分析(见图2),结果如下表,除氮、硅、氧其余元素无烧损,因此表中只列出上述三个元素的检测值;从分析结果来看,电渣锭7的截面和轴向的氮元素分布均匀,并得到了符合标准要求的硅和较低的氧含量,见表9。
[0084]
表9
[0085]
再多了解一些
本文用于企业家、创业者技术爱好者查询,结果仅供参考。