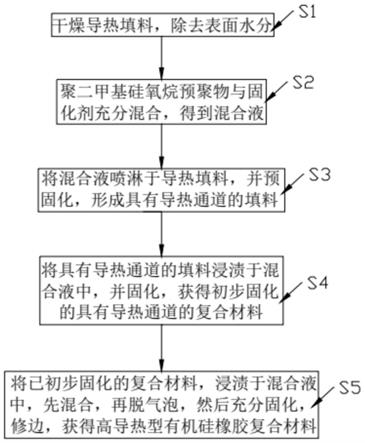
1.本发明涉及橡胶材料技术领域,特别是涉及一种高导热型有机硅橡胶复合材料的制备方法。
背景技术:
2.随着经济的快速发展,高铁、地铁等轨道交通也得到了快速发展,高铁等轨道交通工具的运行速度很高,其速度大,动能大,需要良好的轨道缓冲减振装置,而未经减振的轨道,在列车高速运行过程中,会对各零部件造成极大的冲击力,引起各零部件的损坏,现有技术中通常是在轨道设置具有橡胶弹性体的减振装置进行减振,通过设置减振装置,减缓了列车高速运行的冲击力,但高速运行的轨道交通工具除了巨大冲击力外,还会使减振零部件的发热量大,且巨大的冲击力极易造成减振装置弹性体中的损伤,降低减振零部件的导热性能和减振性能,如能提高减振弹性体元件的耐热性能,并保持其良好的散热能力和减振性能,则能维持轨道交通工具各零部件的正常运转。
3.现有技术中为了改善减振装置中的橡胶弹性体元件的导热性能,主要通过有机硅橡胶与导热填料物理混合,并在两者物理混合的过程形成导热通道,但在物理混合过程中,导热填料未能形成大量的导热通道,且导热填料的搭接点热阻较大,影响有机硅橡胶复合材料导热性能的提高。而且,有机硅橡胶的弹性形变较大,所形成的导热通道在橡胶的弹性变形过程中容易发生移位破坏,不利于有机硅橡胶复合材料在高频动态形变过程中保持稳定的导热性能。
4.因此,研发适应于轨道交通的高导热型有机硅橡胶复合材料具有重要意义。
技术实现要素:
5.为解决上述问题,本发明提供一种高导热型有机硅橡胶复合材料的制备方法,其工艺简单,制备容易,制得的复合材料有着稳固的导热通道,其导热系数高、热膨胀系数低、热稳定好,在热传导过程中能较好的配合,兼具良好的散热能力和减振性能。
6.本发明采用的技术方案是:
7.一种高导热型有机硅橡胶复合材料的制备方法,包括如下步骤:
8.s1:将导热填料于80~120℃干燥8~24h,除去吸附在导热填料表面的水分;
9.s2:将聚二甲基硅氧烷预聚物与固化剂充分混合,得到混合液;
10.s3:在搅拌下,将s2中的混合液喷淋于s1中干燥后的导热填料上,在低于50℃的温度下预固化,形成具有导热通道的填料;
11.s4:将具有导热通道的填料浸渍于s2中的混合液中,先进行高速混合,然后于60~100℃温度下,固化10~60min,获得初步固化的具有导热通道的复合材料;
12.s5:将s4中已初步固化的复合材料,浸渍于s2中的混合液中,先进行高速混合,再进行脱气泡操作,然后在20~150℃的温度下,充分固化,修边后,获得高导热型有机硅橡胶复合材料。
13.进一步地,s1中,所述的导热填料为粒径范围是20nm~200nm的具有多层结构的石墨烯微片。
14.进一步地,s2中,所述聚二甲基硅氧烷预聚物与固化剂的质量比5~10:1,优选10:1进行配比。
15.进一步地,s3中,混合液与导热填料的质量比1:10~100。
16.进一步地,s3中,预固化过程可以分为2个的固化阶段,第一阶段可以在常压下或在真空状态下进行,优选在真空状态下进行,且真空状态下的固化温度优选为80℃,常压下优选为90℃,第一阶段的固化时间为10~60min,优选为30min。
17.进一步地,s4中,具有导热通道的填料与混合液的质量比为1:0.5~5。
18.进一步地,s4中,具有导热通道的填料与混合液中高速混合过程中,转速控制在5000~20000rpm,优选10000rpm。
19.进一步地,s4中的高速混合时间为3~10min;s5中的高速混合时间为3~10min,优选5min。
20.进一步地,s5中的充分固化时间为5~3h。
21.进一步地,s5中,将进行高速混合后的浆料加入模具中,再进行脱气泡操作,除去残留的空气后,固化成型,并修边后,得到高导热型有机硅橡胶复合材料。
22.本发明的有益效果如下:
23.本技术提供的制备方法,其工艺流程简单,制备容易,制备过程中,首先构建导热通路,并通过分阶段的逐步固化,稳固导热通道,使得最终制得的复合材料具备导热系数高、热膨胀系数较低、导热性能稳定的特点,并且在热传导过程中能较好的配合,防止热膨胀产生变形和新的缝隙,其修复功能和导热性能可灵活调整,可在200℃温度下长期使用,适用于高速运行的轨道交通工具的减振零配件,可以阻止轨道交通工具运行过程中高频动态形变引起减振零配件导热性能的下降以及减缓减振零配件的热氧老化,延长轨道交通工具减振零配件的使用寿命,更好地保护轨道交通工具的安全运行。
附图说明
24.图1为本技术实施例1-3中的制备流程图。
具体实施方式
25.为了便于理解本发明,下面将参照实施例对本发明进行更全面的描述,以下给出了本发明的较佳实施例。但是,本发明可以以许多不同的形式来实现,并不限于本文所描述的实施例。提供这些实施例的目的是使对本发明的公开内容的理解更加透彻全面。实施例中使用到的各类原料,除非另有说明,均为常见市售产品。
26.除非另有定义,本文所使用的所有的技术和科学术语与属于本发明的技术领域的技术人员通常理解的含义相同。在本发明的说明书中所使用的术语只是为了描述具体的实施例的目的,不是旨在于限制本发明。本文所使用的术语“和/或”包括一个或多个相关的所列项目的任意的和所有的组合。
27.本发明实施例中揭露的数值是近似值,而并非确定值。在误差或者实验条件允许的情况下,可以包括在误差范围内的所有值而不限于本发明实施例中公开的具体数值。
28.本发明实施例中揭露的数值范围用于表示在混合物中的组分的相对量以及其他方法实施例中列举的温度或者其他参数的范围。
29.本技术提供的高导热型有机硅橡胶复合材料的制备方法,包括如下步骤:
30.s1:将导热填料于80~120℃干燥8~24h,除去吸附在导热填料表面的水分;
31.s2:将聚二甲基硅氧烷预聚物与固化剂充分混合,得到混合液;
32.s3:在搅拌下,将s2中的混合液喷淋于s1中干燥后的导热填料上,在低于50℃的温度下预固化,形成具有导热通道的填料;
33.s4:将具有导热通道的填料浸渍于s2中的混合液中,先进行高速混合,然后于60~100℃温度下,固化10~60min,获得初步固化的具有导热通道的复合材料;
34.s5:将s4中已初步固化的复合材料,浸渍于s2中的混合液中,先进行高速混合,再进行脱气泡操作,然后在20~150℃的温度下,充分固化,修边后,获得高导热型有机硅橡胶复合材料。
35.具体地,s1中,所述的导热填料为粒径范围是20nm~200nm的具有多层结构的石墨烯微片。
36.s2中,所述聚二甲基硅氧烷预聚物与固化剂的质量比5~10:1,优选10:1进行配比。
37.s3中,混合液与导热填料的质量比1:10~100。
38.s3中,预固化过程可以分为2个的固化阶段,第一阶段可以在常压下或在真空状态下进行,优选在真空状态下进行,且真空状态下的固化温度优选为80℃,常压下优选为90℃,第一阶段的固化时间为10~60min,优选为30min。
39.s4中,具有导热通道的填料与混合液的质量比为1:0.5~5。
40.s4中,具有导热通道的填料与混合液中高速混合过程中,转速控制在5000~20000rpm,优选10000rpm。
41.s4中的高速混合时间为3~10min;s5中的高速混合时间为3~10min,优选5min。
42.s5中的充分固化时间为5~3h。
43.s5中,将进行高速混合后的浆料加入模具中,再进行脱气泡操作,除去残留的空气后,固化成型,并修边后,得到高导热型有机硅橡胶复合材料。
44.本技术提供的制备方法,其工艺流程简单,制备容易,制备过程中,首先构建导热通路,并通过分阶段的逐步固化,稳固导热通道,使得最终制得的复合材料具备导热系数高、热膨胀系数较低、导热性能稳定的特点,并且在热传导过程中能较好的配合,防止热膨胀产生变形和新的缝隙,其修复功能和导热性能可灵活调整,可在200℃温度下长期使用,适用于高速运行的轨道交通工具的减振零配件,可以阻止轨道交通工具运行过程中高频动态形变引起减振零配件导热性能的下降以及减缓减振零配件的热氧老化,延长轨道交通工具减振零配件的使用寿命,更好地保护轨道交通工具的安全运行。
45.下面为本技术的具体实施例:
46.下面实施例中的用到的组分聚二甲基硅氧烷预聚物为道康宁的sylgard 184有机硅氧烷预聚体,固化剂为道康宁的sylgard 184固化剂。
47.实施例1:
48.s1:将10g石墨烯微片放在80℃干燥箱中干燥12h,除去吸附在石墨烯微片表面的
水分;
49.s2:将40g聚二甲基硅氧烷预聚物与4g固化剂充分混合后,得到聚二甲基硅氧烷预聚体混合液;
50.s3:在搅拌下,将5g混合液喷淋于10g石墨烯微片上,在50℃下预固化30min,获得石墨烯微片导热通道;
51.s4:将10g石墨烯微片导热通道浸渍于15g聚二甲基硅氧烷预聚体混合液中,先在10000rpm转速的高速混合机中混合10min,再进行脱气泡操作,然后在80℃温度的真空状态下固化20min,得到稳固导热通道的聚二甲基硅氧烷/石墨烯微片复合物;
52.s5:将25g聚二甲基硅氧烷/石墨烯微片复合物浸渍于25g聚二甲基硅氧烷预聚体混合液中,先在10000rpm转速的高速混合机中混合10min,再进行脱气泡操作,然后在130℃下固化100min,修边后得到导热有机硅/石墨烯微片复合材料。
53.实施例2
54.s1:将20g石墨烯微片放在100℃干燥箱中干燥15h,除去吸附在石墨烯微片表面的水分;
55.s2:将60g聚二甲基硅氧烷预聚物与9g固化剂充分混合后,得到聚二甲基硅氧烷预聚体混合液;
56.s3:在搅拌下,将12g混合液喷淋于20g石墨烯微片上,在60℃下预固化20min,获得石墨烯微片导热通道;
57.s4:将20g石墨烯微片导热通道浸渍于20g聚二甲基硅氧烷预聚体混合液中,先在15000rpm转速的高速混合机中混合15min,再进行脱气泡操作,然后在90℃下的真空状态下固化30min,得到稳固导热通道的聚二甲基硅氧烷/石墨烯微片复合物;
58.s5:将20g石墨烯微片导热通道浸渍于60g聚二甲基硅氧烷预聚体混合液中,先在15000rpm转速的高速混合机中混合15min,再进行脱气泡操作,然后在120℃下固化120min,修边后得到导热有机硅/石墨烯微片复合材料。
59.实施例3
60.s1:将10g石墨烯微片放在80℃干燥箱中干燥20h,除去吸附在石墨烯微片表面的水分;
61.s2:将90g聚二甲基硅氧烷预聚物与18g固化剂充分混合后,得到聚二甲基硅氧烷预聚体混合液;
62.s3:在搅拌下,将5g混合液喷淋于石墨烯微片上,在80℃下预固化30min,获得石墨烯微片导热通道;
63.s4:将10g石墨烯微片导热通道浸渍于20g聚二甲基硅氧烷预聚体混合液中,先在12000rpm转速的高速混合机中混合20min,再进行脱气泡操作,然后在80℃下的真空状态下固化30min,得到稳固导热通道的聚二甲基硅氧烷/石墨烯微片复合物;
64.s5:将10g聚二甲基硅氧烷/石墨烯微片复合物浸渍于90g聚二甲基硅氧烷预聚体混合液中,先在12000rpm转速的高速混合机中混合均匀,再进行脱气泡操作,先在80℃固化30min,然后在120℃下固化120min,修边后得到导热有机硅/石墨烯微片复合材料。
65.将实施例1~3制备得到的导热型硅橡胶复合材料进行综合性能测试,测试结构如表1所示:
66.表1
67.实施例123导热系数2.151.570.91拉伸强度(mpa)9.29.19.5邵氏a硬度777065
68.由表1可以看出:采用本发明的制备方法制备出的高导热型硅橡胶复合材料,具有导热系数高,热膨胀系数较低的特点,将其应用于轨道减振装置时,在热传导过程中能更好的与其它零部件配合,防止热膨胀产生变形和新的缝隙。
69.现有技术中,主要是在有机硅橡胶与导热填料物理混合的过程形成导热通道,但在物理混合过程中,导热填料未能形成大量的导热通道,且导热填料的搭接点热阻较大,影响有机硅橡胶复合材料导热性能的提高。而且,有机硅橡胶的弹性形变较大,所形成的导热通道在橡胶的弹性变形过程中容易发生移位破坏,不利于有机硅橡胶复合材料在高频动态形变过程中保持稳定的导热性能。具体地,本技术提供的制备方法,其在制备过程中,首先构建导热通路,并通过分阶段的逐步固化,稳固导热通道,使得最终制得的复合材料具备导热系数高、热膨胀系数较低、导热性能稳定的特点,并且在热传导过程中能较好的配合,防止热膨胀产生变形和新的缝隙,其修复功能和导热性能可灵活调整,可在200℃温度下长期使用,适用于高速运行的轨道交通工具的减振零配件,可以阻止轨道交通工具运行过程中高频动态形变引起减振零配件导热性能的下降以及减缓减振零配件的热氧老化,延长轨道交通工具减振零配件的使用寿命,更好地保护轨道交通工具的安全运行。
70.以上实施例的说明只是用于帮助理解本发明的方法及其核心思想。应当指出,对于本技术领域的普通技术人员来说,在不脱离本发明原理的前提下,还可以对本发明进行若干改进和修饰,这些改进和修饰也落入本发明权利要求的保护范围内。
71.对所公开的实施例的上述说明,使本领域专业技术人员能够实现或使用本发明。对这些实施例的多种修改对本领域的专业技术人员来说将是显而易见的,本文中所定义的一般原理可以在不脱离本发明的精神或范围的情况下,在其它实施例中实现。因此,本发明将不会被限制于本文所示的这些实施例,而是要符合与本文所公开的原理和新颖特点相一致的最宽的范围。
72.以上所述实施例仅表达了本发明的几种实施方式,其描述较为具体和详细,但并不能因此而理解为对本发明专利范围的限制。应当指出的是,对于本领域的普通技术人员来说,在不脱离本发明构思的前提下,还可以做出若干变形和改进,这些都属于本发明的保护范围。因此,本发明专利的保护范围应以所附权利要求为准。
再多了解一些
本文用于企业家、创业者技术爱好者查询,结果仅供参考。