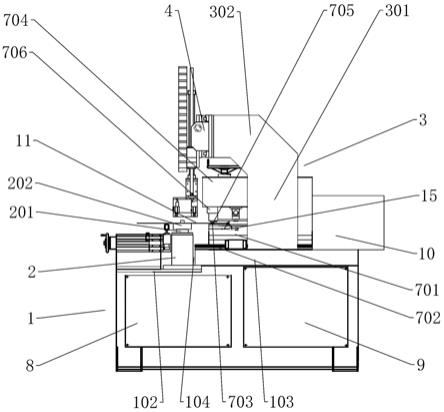
1.本发明涉及专利领域,尤其是涉及一种智能纵横强化机。
背景技术:
2.圆形锯片是一种常用的切割工具,其在被制造时,需要经过多次热处理以达到较好的热硬度、耐磨性和耐高温性能,然而不可避免的是在热处理的过程中,会产生内部应力不均匀或张力偏离要求值的问题。传统的方式是通过人工捶打,只能一片片的处理,劳动强度大,对人员技术要求高,且整体相率较低。
3.中国专利文献cn 202387804 u记载了一种圆锯片径向与切向复合应力碾压处理装置,但是该结构主要通过碾压的方式对圆锯表面进行处理,且没有检测系统对于锯片进行精细化的应力均布,在使用的过程中存在缺陷,因此需要改进。
技术实现要素:
4.本发明提供了一种智能纵横强化机,解决圆锯片在生产过程中应力分布不均匀,且矫正强化过程比较复杂,需要人工处理,劳动强度大,效率低的问题。
5.为解决上述技术问题,本发明所采用的技术方案是:一种智能纵横强化机,包括机架,其特征是,机架包括支撑架,支撑架上设有物件支撑台和固定座,物件支撑台上设有工作台,工作台用于固定工件,固定座上设有强化单元,工作台位于强化单元的正前方,强化单元包括床身,床身和固定座滑动连接,床身上部通过摆动缸和摆动头连接,摆动头用于对工件进行矫正强化,固定座上设有横梁支座,横梁支座的的上部设有横梁总成,横梁总成上设有上片机械手和下片机械手,横梁支座包括相对设置的两个竖向支撑,竖向支撑的上部设有弯折部,两个弯折部通过横梁总成连接。
6.优选的方案中,所述支撑架内设有旋转动力总成和液压动力总成,旋转动力总成和液压动力总成分别用于对工作台与强化单元提供动力。
7.优选的方案中,所述工作台设置在物件支撑台的中部,物件支撑台两侧对称设有激光检测系统和张力检测系统,激光检测系统和张力检测系统之间的距离沿远离工作台的方向越来越大。
8.优选的方案中,所述物件支撑台两侧还设有毛坯杆座和成品托板,毛坯杆座和成品托板分别位于激光检测系统与张力检测系统的外侧,毛坯杆座两侧设有用于分片的磁力分片机构。
9.优选的方案中,所述摆动头内设有液压缸,液压缸的底部设有第一打点座,床身的上部设有第二打点座,第二打点座和第一打点座正对设置。
10.优选的方案中,所述第一打点座通过同步连杆和第二打点座连接。
11.优选的方案中,所述工作台内设有主轴,主轴的顶部设有固定头,主轴和旋转动力总成通过同步带连接。
12.优选的方案中,所述物件支撑台和固定座之间设有阶台。
13.优选的方案中,所述床身上可拆卸的设置有自适应辅助固定机构,自适应辅助固定机构用于对不同直径和厚度的工件进行夹持。
14.本发明的有益效果为:通过在机架上设置工作台和强化单元,能将工作台上的锯片表面进行锤击强化,工作台可以根据激光检测系统13和张力检测系统的检测数据,将锯片需要加工的部位直接旋转至强化单元的第一打点座和第二打点座之间,借助摆动缸完成锯片表面的捶打强化,上片机械手配合下片机械手将毛坯杆座经过工作台上的加工后向成品托板进行流转,整体自动化完成锯片的检测和修正,精度高,效果好,且无需人工干预,大幅提高了锯片的生产效率。
附图说明
15.下面结合附图和实施例对本发明作进一步说明:图1是本发明的右视示意图;图2是本发明的正视示意图;图3是本发明的自适应辅助固定机构整体结构图;图4是图3的俯视示意图;图5是图3的正视示意图;图6是图3的爆炸示意图状态一;图7是图3的爆炸示意图状态二;图8是图3的爆炸示意图状态三;图9是本发明的夹持座结构示意图;图10是本发明的调整件结构示意图;图11是本发明的滑杆结构示意图;图12是图8的a处放大示意图。
16.图中:机架1;支撑架101;物件支撑台102;固定座103;阶台104;毛坯杆座105;成品托板106;工作台2;主轴201;固定头202;横梁支座3;竖向支撑301;弯折部302;横梁总成4;上片机械手5;下片机械手6;强化单元7;床身701;导轨702;第二打点座703;摆动头704;第一打点座705;液压缸706;摆动缸707;调整手柄708;第一滑槽709;第一螺纹孔710;锁块711;同步连杆712;旋转动力总成8;液压动力总成9;进给系统10;工件11;磁力分片机构12;激光检测系统13;张力检测系统14;自适应辅助固定机构15;夹持座1501;夹板1502;安装槽1503;夹紧板1504;滑块1505;驱动板1506;限位板1507;螺杆1508;滑杆1509;第一弹簧1510;板体1511;第三弹簧1512;第二滑槽1513;第一直槽1514;第二螺纹孔1515;滑板1516;支撑板1517;凹槽1518;第二直槽1519;第二让位槽1530;复位圆杆1520;第二弹簧1521;圆柱头1522;第一耳板1523;第一让位槽1524;安装直板1525;圆弧接触板1526;第三耳板1527;第四耳板1528;螺母1529;板体1530;第四弹簧1531;圆弧部1532;锁钉16;伸缩缸17;顶杆1701;安装座1702;弧形槽1703;通孔1704;调整件18;第一支撑环1801;第二支撑环1802;第二耳板1803。
具体实施方式
17.实施例1
如图1-2中,一种智能纵横强化机,包括机架1,其特征是,机架1包括支撑架101,支撑架101上设有物件支撑台102和固定座103,物件支撑台102上设有工作台2,工作台2用于固定工件11,固定座103上设有强化单元7,工作台2位于强化单元7的正前方,强化单元7包括床身701,床身701和固定座103滑动连接,床身701上部通过摆动缸707和摆动头704连接,摆动头704用于对工件11进行矫正强化。床身701后方通过进给系统10驱动,由此结构,以使得支撑台102和固定台103配合,同时强化单元7正对工作台2保证了捶打时工件11受力均匀,整体的强化效果更好,对于不同直径的工件11,可以根据捶打的区域,调整床身701相对固定座103的位置,捶打准确和方便,摆动头704在摆动缸707的作用下,对需要矫正的部位进行精准的施力。
18.优选的方案中,所述支撑架101内设有旋转动力总成8和液压动力总成9,旋转动力总成8和液压动力总成9分别用于对工作台2与强化单元7提供动力。由此结构,以使得整体使用方便,工作台2上设置有角度编码器,可以在旋转动力总成8的驱动下转动到设计位置,整体快速精确,液压动力总成9则能为摆动头704提供稳定的下压力。
19.优选的方案中,所述工作台2设置在物件支撑台102的中部,物件支撑台102两侧对称设有激光检测系统13和张力检测系统14,激光检测系统13和张力检测系统14之间的距离沿远离工作台2的方向越来越大。由此结构,工作台2带动工件11沿匀速周向转动,借助激光检测系统13和张力检测系统14可以对锯片的表面的相对位置偏差和张力的分布范围进行检测,在初始标定时,设置强度单元7的位置为相对的零点位置,对于不符合要求的区域,此时位于工作台2内的角度编码器记录此时的角度值,在工件11完成整圈的检测后,根据不符合要求的角度值,依次转动到强化单元7的正下方,然后调整床身701的位置,在摆动头704的捶打下,完成矫正,待所有不合格点矫正完成后,重复步骤激光检测系统13和张力检测系统14可以对锯片的表面的相对位置偏差和张力的分布范围进行复检,直至所有区域通过生产的技术指标要求。
20.优选的方案中,所述物件支撑台102两侧还设有毛坯杆座105和成品托板106,毛坯杆座105和成品托板106分别位于激光检测系统13与张力检测系统14的外侧,毛坯杆座105两侧设有用于分片的磁力分片机构12。由此结构,以使得可以借助机械手依次将毛坯杆座105上的工件11移动到工作台2上完成检测矫正和强化后,转移到成品托板106上,保证了整体流程运转的高效,且避免了调试的繁琐,对于不同规格和批次的来料都能进行快速的生产。
21.优选的方案中,所述摆动头704内设有液压缸706,液压缸706的底部设有第一打点座705,床身701的上部设有第二打点座703,第二打点座703和第一打点座705正对设置。液压缸706的一端设置有调整手柄708,调整手柄708和摆动头704螺纹连接,液压缸706滑设在摆动头704内侧,由此结构,通过改变调整手柄708的位置,从而调整液压缸706的位置,从而改变第一打点座705和第二打点座703之间的距离,从而调整了捶打的力度和效果,且可以适应不同厚度的锯片的生产。
22.优选的方案中,所述第一打点座705通过同步连杆712和第二打点座703连接。第一打点座705上设置有旋转气缸,第二打点座703转动设置在床身701上,由此结构,通过旋转气缸的工作,同步连杆712可以控制第一打点座705和第二打点座703同步转向,从而对工件11施加不同的强化图形。
23.优选的方案中,所述工作台2内设有主轴201,主轴201的顶部设有固定头202,主轴201和旋转动力总成8通过同步带连接。固定头202的下部设置有拉紧气缸,由此结构,以使得在工件11放置好后,通过拉紧气缸可以将工件11牢固的固定在固定头202上,从而保证了检测数据的稳定,且为强化提供基础,避免了受力不均导致工件强化不准确。
24.优选的方案中,所述物件支撑台102和固定座103之间设有阶台104。由此结构,以使得整体空间利用率更高,更有利于调试和检测生产。
25.优选的方案中,所述固定座103上设有横梁支座3,横梁支座3的的上部设有横梁总成4,横梁总成4上设有上片机械手5和下片机械手6。由此结构,以使得采用龙门式结构整体刚性好,承载能力强,上片机械手5和下片机械手6分别用于将毛坯杆座105上的工件11向成品托板106上流转,自动化生产整体稳定性高,控制更方便,效率也有充分保障。
26.优选的方案中,所述横梁支座3包括相对设置的两个竖向支撑301,竖向支撑301的上部设有弯折部302,两个弯折部302通过横梁总成4连接。由此结构,以使得整体安装和拆下方便,整体刚性好,弯折部302为横梁总成4提供了支撑基础,对整体空间的利用率更高。
27.实施例2如图3-12中,不同于实施例1,在床身701上可拆卸的设置有自适应辅助固定机构15,自适应辅助固定机构15用于对不同直径和厚度的工件11进行夹持,保证了强化单元7对工件11在强化时,工件11整体更加稳定,强化效果更好,避免了因为延伸部分底部并未被全部支撑,导致强化时颤动,整体的质量不稳定,效果不佳。
28.优选的方案中,床身701的两侧分别设置有第一滑槽709,第一滑槽709内设置有多个第一螺纹孔710,锁块711滑设在第一滑槽709内,锁块711通过锁定16和床身701连接;自适应辅助固定机构15包括夹持座1501,夹持座1501上滑设有夹板1502,夹持座1501的底部通过驱动板1506和滑块1505连接,滑块1505滑设在第一滑槽709内,滑块1505远离锁块711的一侧连接有伸缩缸17,伸缩缸17通过安装座1702和床身701连接,安装座1702上设有螺杆1508,螺杆1508和伸缩缸17平行设置,螺杆1508通过调整件18和伸缩缸17连接,调整件18通过第一弹簧1510和夹板1502连接。由此结构,以使得伸缩缸17的顶杆1701可以推动滑块1505在第一滑槽709内移动,滑块1505拉动驱动板1506从而带动夹持座1501向工件方向移动,由于调整件18的位置相对固定,因此第一弹簧1510被拉伸,从而第一弹簧1510的一端固定在夹板1502靠近工件11的一侧,从而第一弹簧1510给予夹板1502的前端一个向下的力,夹板1502下压,然后对工件11的上表面给予限位和支撑,配合第二打点座703对工件11在竖直方向上进行限位,防止摆动头704工作时,产生振动或颤动,避免导致强化效果不好。
29.优选的方案中,驱动板1506通过限位板1507和夹板1502连接。驱动板1506上设置有第一让位槽1524,夹板1502上设有安装直板1525,安装直板1525通过锁钉16固定在夹持座1501的底部,由此结构,以使得限位板1507给予夹板1502限制,防止其跑偏失稳,同时整体移动更顺畅。
30.优选的方案中,安装座1702底部设置有多个通孔1704,螺钉16穿设在通孔1704内,安装座1702相对伸缩缸17的一侧设置有弧形槽1703,螺杆1508的小端穿设在弧形槽1703内,螺杆1508的大端直径大于弧形槽1703的宽度,小端通过锁定16和安装座1702连接,调整件18包括从下到上设置的第一支撑环1801、第二支撑环1802和第二耳板1803,第一支撑环
1801套设在伸缩缸17外侧,第一支撑环1801内径和伸缩缸17外径相匹配,螺杆1508穿设在第二支撑环1802内,第一弹簧1510和第二耳板1803连接,螺杆1508通过对称设置的螺母1529对调整件18锁止。由此机构,以使得可以通过改变螺母1529的位置从而快速的移动调整件18,从而改变第一弹簧1510的预紧力,整体使用更方便,调整更高效。
31.优选的方案中,夹持座1501包括滑板1516,滑板1516底部设置有第二滑槽1513,第二滑槽1513的宽度和床身701的宽度相匹配,滑板1516一侧相对设置有两个支撑板1517,支撑板1517的内侧设有凹槽1518,凹槽1518内设有第二直槽1519,第二直槽1519贯穿设置在支撑板1517上,夹板1502包括板体1511,板体1511外侧相对设置有两个第一耳板1523,第一弹簧1510一侧固定在第一耳板1523上,板体1511一侧对称设有第二让位槽1530,第二让位槽1530内设置有圆柱头1522,圆柱头1522滑设在凹槽1518内,圆柱头1522通过锁钉16和第二直槽1519铰接,板体1511的底部通过多个第二弹簧1521和复位圆杆1520连接,滑板1516两侧分别设置有第二螺纹孔1515,第二螺纹孔1515通过锁钉16和驱动板1506连接,板体1511的下部还设有圆弧接触板1526。由此结构,以使得夹板1502可以在凹槽1518内上下移动,圆弧接触板1526直接接触工件11,圆弧接触板1526采用橡胶材质,能在受力时增大接触面积,整体的夹持效果好,同时可以在受第一弹簧1510拉力状态下,在第二直槽1519内转动,此时复位圆杆1520受挤压,紧紧的抵靠在滑板1516的表面,当顶杆1701带动滑块1505离开工件11时,夹板1502在第二弹簧1521的作用下恢复至初始位置,整体运动高效精准。由于锯片的外侧的切割镶片颗粒的厚度一般都比锯片基体后,因此采用夹板1502下压的方式,可以完整的避开对切割镶片的影响,整体安全高效,保证了锯片的质量。
32.优选的方案中,滑板1516上设有安装槽1503和第一直槽1514,安装槽1503和第一直槽1514连通,安装槽1503内滑设有夹紧板1504,第一直槽1514内设有滑杆1509,滑杆1509两侧分别设置有第四耳板1528,第四耳板1528通过第三弹簧1512和第四弹簧1531分别和滑板1516及驱动板1506连接。夹紧板1504底部设有圆弧部1532,驱动板1506上设置有第三耳板1527,第四弹簧1531固定在第三耳板1527上,第三弹簧1512通过锁钉16和滑板1516连接,由此结构,以使得当滑块1505靠近工件11时,拉动第四弹簧1531从而驱动滑杆1509在第一直槽1514内移动,从而滑杆1509推动夹紧板1504从安装槽1503内滑出,夹紧板1504从下部将工件11夹持,夹紧板1504从下部夹持避免了对镶片的影响,当矫正强化完成后,滑块1505在顶杆1701的作用下回到初始位置,此时第三弹簧1512拉动滑杆1509复位,此时夹紧板1504落回至安装槽1503内。
33.上述的实施例仅为本发明的优选技术方案,而不应视为对于本发明的限制,本发明的保护范围应以权利要求记载的技术方案,包括权利要求记载的技术方案中技术特征的等同替换方案为保护范围。即在此范围内的等同替换改进,也在本发明的保护范围之内。
再多了解一些
本文用于企业家、创业者技术爱好者查询,结果仅供参考。