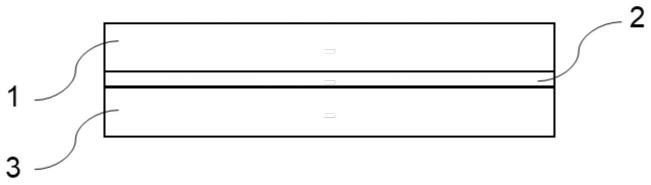
1.本实用新型属于半导体制造领域,涉及一种可拆卸基板。
背景技术:
2.将两个基板进行可拆卸的接合,在半导体制造领域具有重要的应用价值。例如:半导体基板需要尽可能的薄,特别是碳化硅材料。然而,过薄的基板强度相应降低,容易发生翘曲变形甚至裂纹。为避免上述问题,可以用粘接剂在薄板的一个表面粘贴一个支撑基板,然后在薄基板上进行相关制造工艺,最后将支撑基板拆卸下来。然而,碳化硅器件的制造工艺经常需要高温,例如300-800℃的高温离子注入、1000℃左右的欧姆退火等。树脂材料的粘接剂无法承受高温环境,使得碳化硅的制造工艺尚未完成,碳化硅薄板已经和支撑基板分开。
技术实现要素:
3.为解决现有技术中存在的技术问题,本实用新型提供一种可拆卸基板,所述可拆卸基板在使用时基板与支撑层的结合牢固,使用后仅通过加热和简单的能量施加即可实现拆卸,操作简便,易于进行工业化应用。
4.为达到上述技术效果,本实用新型采用以下技术方案:
5.本实用新型目的之一在于提供一种可拆卸基板,所述可拆卸基板包括依次连接的第一基板、金属层以及第二基板,所述第一基板和所述第二基板包括至少一层碳化硅层,所述碳化硅层设置于所述金属层一侧,和/或所述第一基板和/或所述第二基板为碳化硅基板。
6.本实用新型中,所述可拆卸基板的结构可以是第一基板或第二基板中的一个设置碳化硅层,也可以是第一基板和第二基板均设置碳化硅层;可以是第一基板和第二基板中的一个为碳化硅材质,也可以是第一基板和第二基板二者均为碳化硅材质;可以是第一基板和第二基板中的一个设置金属层,也可以是第一基板和第二基板均设置金属层;还可以是上述技术方案排列组合所形成的可拆卸基板。
7.本实用新型中,在一定的热处理条件下,金属层中的金属和其接触的碳化硅进行反应形成中间层,所述中间层包括金属硅化物和碳,使得第一基板和第二基板的接合强度降低。反应所生成的碳形成平行于所述基板平面的沉淀物,沉淀物是非连续的,使得形成的中间层中含有空隙或空洞,从而降低后续拆卸所需的外力。
8.本实用新型中,第一基板和第二基板形成的碳化硅层或者碳化硅基板材质可以是单晶或多晶。
9.作为本实用新型优选的技术方案,所述金属层的厚度为1~100nm,如2nm、5nm、10nm、15nm、20nm、25nm、30nm、40nm、50nm、60nm、70nm、80nm或90nm等,但并不仅限于所列举的数值,该数值范围其他未列举的数值同样适用。
10.作为本实用新型优选的技术方案,所述金属层包括w层、hf层、nb层、ni层、v层、mg
层、ti层、zr层、mo层、ta层、co层、fe层、cr层或cu层中的任意一种。
11.本实用新型中,所述金属层还可以是w和hf的组合、hf和nb的组合、nb和ni的组合、ni和v的组合、v和mg的组合、mg和ti的组合、ti和zr的组合、zr和mo的组合、mo和ta的组合、ta和co的组合、co和fe的组合、fe和cr的组合、cr和cu的组合或w、nb和ta的组合形成的合金金属层。
12.本实用新型中,不同的金属和碳化硅发生反应的温度不同。可根据不同的应用场景进行选择。其规律是:金属和碳化硅发生反应的温度越高,基板在拆卸前的工序中能承受的热预算越高,同时拆卸所需要的热处理的热预算也越高。
13.本实用新型中,可拆卸基板热处理后生成的金属硅化物包括硅化钨wsi2、硅化铪hfsi2、硅化铌nbsi2、硅化镍ni2si、硅化钒vsi2、硅化镁mg2si、硅化钛tisi2、硅化锆zrsi2、硅化钼mosi2、硅化钽tasi2、硅化钴cosi2、硅化铁fesi2、硅化铬crsi2或硅化铜cu5si等。
14.作为本实用新型优选的技术方案,所述第一基板和所述第二基板还包括半导体基板、金属基板或塑料基板。
15.本实用新型中,所述半导体材料可以是iv族半导体、i-iii-vi族半导体、ii-v族半导体、iv族半导体、i-iii-vi族半导体以及有机半导体等。
16.本实用新型中,所述可拆卸基板的拆卸方法为对所述可拆卸基板进行热处理,之后对所述金属层施加能量。
17.本实用新型中,所述热处理的温度不低于600℃,如650℃、700℃、750℃、800℃、850℃、900℃、950℃或1000℃等,但并不仅限于所列举的数值,该数值范围其他未列举的数值同样适用。
18.本实用新型中,热处理可以在真空或惰性气氛中进行。惰性气氛可以是氮气气氛或稀有气体气氛,如氩或氦等。在某些实施例中,热处理可以在活泼气氛中进行。
19.本实用新型中,经过热处理后的基板拆卸,可以通过向热处理后形成的中间层或中间层附近提供能量来实现,也可以通过化学方式实现。提供能量的方式包括施加机械力、超声波、插入薄板或者刀片;还可以施加水压,如水喷射或液体喷射;还可以施加气压。也可以采用上述多种方法的组合。化学方式包括蚀刻,可以使用至少含有h2so4、h2o2、h2o和hf的混合溶液,通过蚀刻从中间层去除硅化物。
20.本实用新型中,所述可拆卸基板的制备方法包括:
21.在所述第一基板和/或所述第二基板表面沉积金属层;
22.将所述第一基板和所述第二基板进行接合,所述金属层位于所述接合一侧。
23.本实用新型中,所述制备方法包括:
24.在所述第一基板和/或所述第二基板表面外延生长碳化硅层;
25.在所述第一基板和/或所述第二基板表面沉积金属层,所述金属层沉积于所述碳化硅层表面;
26.将所述第一基板和所述第二基板进行接合,所述金属层位于所述接合一侧。
27.本实用新型中,所述外延生长包括金属有机气相沉积(movpe)法,氢化气相沉积(hvpe)法、分子束外延(mbe)法以及氨热法、钠通量法等。
28.本实用新型中,所述接合是指,在真空环境下两个足够光滑、洁净的表面可形成分子粘附,表面粗糙度可以为0.5nm rms或更小。一般认为表面粗糙度越小,接合强度越高。具
体的,还可以在接合期间对基板施加压力,方向垂直于基板平面。施加的压力可以是恒定的,也可以随着时间变化。
29.本实用新型中,所述沉积的方法包括电子束蒸发、dc磁控溅射或射频溅射中的任意一种。
30.本实用新型中,对于熔点较高的金属,优选的沉积方法是电子束蒸发方法。
31.本实用新型中,所述金属层沉积前对所述第一基板和/或所述第二基板的表面进行粒子照射,从而使得表面活化。
32.本实用新型中,在接合之前,通过对需要接合的表面进行粒子照射表面活化,去除表面的氧化物和附着物,激活表面以提高接合强度。粒子可以是稀有气体,或含有稀有气体,例如可以是氩ar。
33.本实用新型中,所述可拆卸基板的应用包括用于制造薄型碳化硅肖特基二极管、薄型碳化硅mosfet或薄型氮化镓器件。
34.与现有技术相比,本实用新型至少具有以下有益效果:
35.本实用新型提供一种可拆卸基板,所述可拆卸基板在使用时基板与支撑层的结合牢固,使用后仅通过加热(加热后基板与支撑层间的接合强度降低50%以上)和简单的能量施加即可实现拆卸,操作简便,易于进行工业化应用。
附图说明
36.图1为本实用新型提供的可拆卸的基板的结构示意图;
37.图2为本实用新型应用例1制造薄型碳化硅肖特基二极管的流程示意图;
38.图3为本实用新型应用例2制造薄型碳化硅mosfet(第一种)的流程示意图;
39.图4为本实用新型应用例3制造薄型碳化硅mosfet(第二种)的流程示意图;
40.图5为本实用新型应用例4制造薄型氮化镓器件的流程示意图;
41.图中:1-第一基板,2-金属层,3-第二基板。
42.下面对本实用新型进一步详细说明。但下述的实例仅仅是本实用新型的简易例子,并不代表或限制本实用新型的权利保护范围,本实用新型的保护范围以权利要求书为准。
具体实施方式
43.为更好地说明本实用新型,便于理解本实用新型的技术方案,本实用新型的典型但非限制性的实施例如下:
44.实施例1
45.本实施例提供一种可拆卸基板,其结构如图1所示,所述可拆卸基板包括依次连接的第一基板1、金属层2以及第二基板3,所述第一基板1和所述第二基板3为碳化硅层,所述金属层为ni层。
46.实施例2
47.本实施例提供一种可拆卸基板,其结构如图1所示,所述可拆卸基板包括依次连接的第一基板1、金属层2以及第二基板3,所述第一基板1和所述第二基板3分别独立地包括一层碳化硅层,所述碳化硅层设置于所述金属层2一侧,所述第一基板1和所述第二基板3分别
独立地为碳化硅层,所述金属层2为ni层。
48.实施例3
49.本实施例提供一种可拆卸基板,其结构如图1所示,所述可拆卸基板包括依次连接的第一基板1、金属层2以及第二基板3,所述第一基板1和所述第二基板3分别独立地包括一层碳化硅层,所述碳化硅层设置于所述金属层2一侧,所述第一基板1和所述第二基板3分别独立地为氮化镓层,所述金属层2为ni层。
50.应用例1
51.本实施例提供一种可拆卸的基板,所述可拆卸的基板应用于制造薄型碳化硅肖特基二极管,其流程如图2所示,具体为:
52.(a)准备器件碳化硅基板20和支撑碳化硅基板10;器件碳化硅基板20包括单晶碳化硅层21和其上外延生长的外延碳化硅层22;支撑碳化硅基板可以使用便宜的单晶或多晶基板;
53.(b)在器件碳化硅基板20的外延碳化硅层22上形成金属层23,在支撑碳化硅基板的一个表面形成金属层13;在形成金属层22和23之前,可以对外延碳化硅层22的表面和支撑碳化硅基板的表面进行表面活化,以增加金属层和基板的结合力,金属层是镍ni;
54.(c)将支撑碳化硅基板10和器件碳化硅基板20通过金属层的接合,形成基板组件,金属层13和金属层23接合后形成界面层31;在接合前,对支撑碳化硅基板20上的金属层、器件碳化硅基板上10上的金属层进行表面活化,以提高接合强度;
55.(d)对器件碳化硅基板20的靠近单晶碳化硅层21的一面进行减薄,减薄后,单晶碳化硅层21被全部或部分地去除,减薄的方法包括研磨、抛光;
56.(e)将欧姆接触材料24施加至器件碳化硅基板的一个面上,欧姆接触材料为ni/au;
57.(f)进行热处理,一方面使得欧姆接触材料24性质发生变化,在表面形成欧姆接触层28,另一方面使得支撑碳化硅基板10和器件碳化硅基板20之间的金属和碳化硅发生反应,形成硅化物和碳;新的界面层32的接合强度降低至可拆卸的水平;热处理后的组合体在表面具有欧姆接触层28,在支撑碳化硅基板10和器件碳化硅基板20之间具有硅化物和析出的碳;
58.(g)将热处理后的组合体的欧姆接触层28的一个面通过粘接剂51的固定在载体基板50上;然后,将支撑碳化硅基板10和器件碳化硅基板20沿着界面层32拆卸开来;此时的器件碳化硅基板10虽然很薄,但由于被固定在载体基板上,仍可保持机械稳定;
59.(h)去除器件碳化硅基板20的外延碳化硅层22上的残留的硅化物及碳,去除方法包括抛光和清洗;
60.(i)在外延碳化硅层22上制作电子器件结构25,得到最终的薄型碳化硅肖特基二极管。
61.应用例2
62.本实施例提供一种可拆卸的基板,所述可拆卸的基板应用于制造薄型碳化硅mosfet器件,其流程如图3所示,具体为:
63.(a)器件碳化硅基板220包括单晶碳化硅层221和其上外延生长的外延碳化硅层222,电子器件结构225已经形成在外延碳化硅层222中,电子器件结构可以是mosfet的源
极;
64.(b)形成绝缘保护层226以覆盖器件结构225,并使得绝缘保护层的表面平整;
65.(c)在绝缘保护层226上形成碳化硅层227,并在其上形成金属层223;准备支撑碳化硅基板210,在其一个表面形成金属层213,所述金属为镍;在形成金属层之前,可对支撑碳化硅基板210的表面和器件碳化硅基板220的碳化硅层227的表面进行表面活化处理;
66.(d)使金属层213和金属层223接合,形成界面层231;在接合之前,对金属层的表面进行表面活化;
67.(e)对器件碳化硅基板220的单晶碳化硅层221的一面进行减薄,减薄后,单晶碳化硅层221被全部或部分地去除,减薄的方法包括研磨、抛光,;
68.(f)将欧姆接触材料224施加至器件碳化硅基板的一个面上。欧姆接触材料包括ti/ni/au;
69.(g)进行热处理,一方面使得欧姆接触材料224性质发生变化,在表面形成欧姆接触层228,另一方面使得支撑碳化硅基板210和器件碳化硅基板220之间的金属和碳化硅发生反应,形成硅化物和碳;新的界面层232的接合强度降低至可拆卸的水平;热处理后的组合体在表面具有欧姆接触层228,在支撑碳化硅基板210和器件碳化硅基板220之间具有硅化物和析出的碳;
70.(h)将热处理后的组合体的欧姆接触层228的一个面通过粘接剂251的固定在载体基板250上,然后,将支撑碳化硅基板210和器件碳化硅基板220沿着界面层232拆卸开来;此时的器件碳化硅基板210虽然很薄,但由于被固定在载体基板上,仍可保持机械稳定;
71.(i)去除碳化硅层227上残留的硅化物及碳,再去除碳化硅层227,去除方法包括抛光和清洗;在绝缘保护层226上形成栅极229,最终形成包括源极225、栅极229和欧姆接触层228作为漏极的薄型碳化硅mosfet;s、g、d分别表示源极、栅极和漏极。
72.应用例3
73.本实施例提供一种可拆卸的基板,所述可拆卸的基板应用于制造薄型碳化硅mosfet,其流程如图4所示,具体为:
74.(a)器件碳化硅基板320包括单晶碳化硅层321和其上外延生长的外延碳化硅层322,电子器件结构325已经形成在外延碳化硅层322中,电子器件结构可以是mosfet的源极;
75.(b)形成绝缘保护层326以覆盖器件结构325,并使得绝缘保护层的表面平整。将绝缘保护层326的表面通过粘接剂层341固定在第一基板340上;对器件碳化硅基板320的单晶碳化硅层321的一面进行减薄;减薄后,单晶碳化硅层321被全部或部分地去除;减薄的方法包括激光切割方式;
76.(c)在单晶碳化硅层321上形成金属层323。准备支撑碳化硅基板310,在其一个表面形成金属层313,所述金属为镍;在形成金属层之前,对支撑碳化硅基板310的表面和器件碳化硅基板320的单晶碳化硅层321的表面进行表面活化处理;
77.使金属层313和金属层323接合,形成界面层331;在接合之前,对金属层的表面进行表面活化;
78.(d)拆除第一基板340,得到组合体;
79.(e)进行热处理,使得支撑碳化硅基板310和器件碳化硅基板320之间的金属和碳
化硅发生反应,形成硅化物和碳;新的界面层332的接合强度降低至可拆卸的水平;
80.(f)将步骤e中热处理后的组合体通过粘接剂层371粘接至第二基板370;然后,将支撑碳化硅基板310和器件碳化硅基板320沿着界面层332拆卸开来;此时的器件碳化硅基板310虽然很薄,但由于被固定在第二基板370上,仍可保持机械稳定;
81.(g)拆卸后残留的界面层332中包括有金属硅化物,在其上形成包括金属铝al的欧姆接触电极343;
82.(h)将接触电极343通过粘接剂层381固定到载体基板380上;然后,拆除第二基板370;
83.(i)在绝缘保护层326上形成栅极329,最终形成包括源极325、栅极329和欧姆接触电极343作为漏极的薄型碳化硅mosfet。
84.应用例4
85.本实施例提供一种可拆卸的基板,其流程如图5所示,所述可拆卸的基板应用于制造薄型氮化镓器件,具体为:
86.(a)准备器件氮化镓基板420,在距离一个表面的一定深度处形成预埋的弱化层421,上述深度的氮化镓薄层可转移至另外一个基板;形成弱化层的方法包括离子注入;
87.(b)在器件氮化镓基板的一个表面形成碳化硅层422,然后在碳化硅层422上形成金属层423;准备支撑氮化镓基板410,在其一个表面形成碳化硅层412,然后在碳化硅层412上形成金属层413,所述金属为镍;在形成金属层之前,对碳化硅层412和422的表面进行表面活化处理;
88.(c)使金属层413和金属层423接合,形成界面层431;在接合之前,对金属层的表面进行表面活化;
89.(d)将器件氮化镓基板420沿着弱化层421分开,将氮化镓单晶薄层转移至组合体,剩余部分可以重复利用;
90.(e)在器件氮化镓基板420上外延生长形成外延层424,外延生长为金属有机气相沉积(movpe)法;外延层424具有gan和algan层,外延生长温度为1000℃,同时使得界面层431的金属和碳化硅发生反应,形成硅化物和碳;新的界面层432的接合强度降低至可拆卸的水平;
91.(f)在外延层424上形成器件结构425;
92.(g)在器件结构425上形成钝化层426,钝化层426覆盖器件结构425;
93.(h)将钝化层426接合到载体基板460上,然后将支撑氮化镓基板410和器件氮化镓基板420沿着界面层432拆卸开来;此时的器件氮化镓基板420虽然很薄,但由于被固定在载体基板460上,仍可保持机械稳定;
94.(i)去除碳化硅层422上残留的硅化物及碳,再去除碳化硅层422,去除方法包括抛光和清洗;
95.(j)将器件氮化镓基板420粘接至高导热基板480,形成最终的氮化镓器件。高导热基板480可以使金属、金刚石、氮化硅等,以有效地消除器件结构425产生的热量;
96.(k)也可以将器件氮化硅基板420的表面形成欧姆接触电极485,形成最终的氮化镓器件。
97.申请人声明,本实用新型通过上述实施例来说明本实用新型的详细结构特征,但
本实用新型并不局限于上述详细结构特征,即不意味着本实用新型必须依赖上述详细结构特征才能实施。所属技术领域的技术人员应该明了,对本实用新型的任何改进,对本实用新型所选用部件的等效替换以及辅助部件的增加、具体方式的选择等,均落在本实用新型的保护范围和公开范围之内。
98.以上详细描述了本实用新型的优选实施方式,但是,本实用新型并不限于上述实施方式中的具体细节,在本实用新型的技术构思范围内,可以对本实用新型的技术方案进行多种简单变型,这些简单变型均属于本实用新型的保护范围。
99.另外需要说明的是,在上述具体实施方式中所描述的各个具体技术特征,在不矛盾的情况下,可以通过任何合适的方式进行组合,为了避免不必要的重复,本实用新型对各种可能的组合方式不再另行说明。
100.此外,本实用新型的各种不同的实施方式之间也可以进行任意组合,只要其不违背本实用新型的思想,其同样应当视为本实用新型所公开的内容。
再多了解一些
本文用于企业家、创业者技术爱好者查询,结果仅供参考。