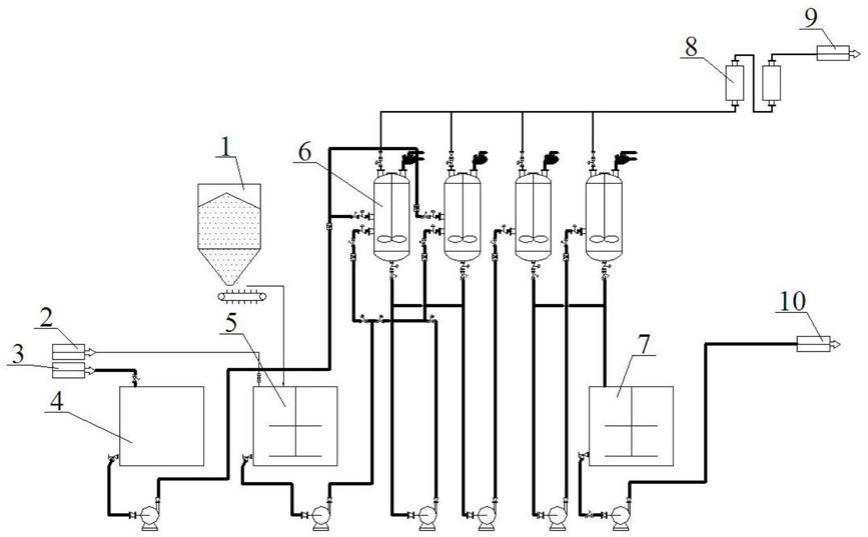
1.本发明属于铝灰综合利用技术领域,特别涉及铝灰综合利用过程中生产的连续稳定运行及氢气的安全、稳定利用的方法。
背景技术:
2.随着铝工业的发展,如何实现铝灰的综合利用技术越来越紧迫,目前,铝灰综合利用技术的研究成果比较多,其中,两段溶出综合利用技术已经实现产业化推广应用。
3.在现有技术中,公开号为cn110980783a的发明专利申请文件公开了一种两段法溶出新工艺处理混合型铝土矿的方法,采用了带压液固分离设备,避免了传统两段法溶出工艺中第一段溶出后矿浆需要降温和稀释才能实现液固分离的弊端,在尽量提高氧化铝溶出率的同时降低了能量的消耗;第二段溶出的高温溢流返回到预脱硅段,可使预脱硅矿浆温度达到95℃以上,减少了预脱硅矿浆的加热流程。较传统一段溶出相比,该两段溶出工艺中进入第二段高温溶出的矿浆量较小,高温段设备投资低,汽耗低。该两段溶出工艺处理含一水软铝石或一水硬铝石混合型三水铝石矿能够降低运行成本、能耗以及碱的消耗,实现拜耳法经济处理混合型铝土矿生产氧化铝。
4.然而,现有技术依然存在不足,原因在于:(1)铝灰中含有一定量的单质铝,其与碱反应剧烈,会产生大量的氢气,而氢气的爆炸范围较宽:4%~84%,因此,如何实现铝灰的少量多点加入且杜绝空气进入生产系统是一个技术难题;(2)铝灰中单质铝、氮化铝等物质与碱的反应是剧烈的放热反应,会产生大量的热,如何平衡反应过程中放出的大量的热,也是原有技术难点;(3)如何确保反应产物—氢气量及压力的稳定,实现其有效利用,也是原有技术难题之一。
5.因此,现有技术的主要缺点是:(1)不能有效杜绝氧气进入生产系统,经常产生闪爆,带来一定安全隐患;(2)一段溶出反应剧烈,热量急剧增加,带来一定安全隐患;(3)一段溶出采用间断进料、间断出料的工艺技术,生产不能连续运行,从而导致过程中产生的氢气量波动大,不能实现其安全、稳定、有效利用。
技术实现要素:
6.提供一种铝灰综合利用过程中一段溶出工序连续稳定运行的方法,以解决原有技术不能满足生产连续运行及氢气的安全、稳定、有效利用问题。
7.本发明采用的技术方案是:铝灰仓的铝灰采用锁气喂料螺旋加入料浆配料槽,将铝灰与工业水按一定比例混合后,连续加入一段溶出反应罐,与进入溶出反应罐中的分解母液混合并反应,分解母液经分解母液槽加入溶出反应罐中;具体分为以下两种溶出方式:
8.一段溶出方式一:溶出反应罐的料浆用泵从进料罐连续向后推进,直至一段溶出反应完毕进入溶出液罐,再进入下一工序;
9.一段溶出方式二:溶出反应罐呈阶梯分布,反应料浆自压从进料罐连续向后逐级推进,达到反应所需时间后进入出料罐,一段溶出反应完毕,出料至溶出液罐,然后再进入
下一道工序;
10.一段溶出产生的气体经过1~2级气液分离器进行气液分离后,气体自压经管道输送至氨气吸收系统进行处理,氨气吸收处理后的气体再输送至燃烧系统回收其氢气能源,实现氢能源的安全、稳定、有效回收利用。
11.其中,铝灰采用锁气喂料螺旋加入料浆配料槽时,与水按一定比例调配,调配固含为500~1000g/l,调配时间小于60分钟。
12.作为进一步的优选方案,料浆配料槽容积为20~30m3。
13.作为进一步的优选方案,将料浆配料槽所配料浆用泵连续均匀加入一段溶出反应罐,并与进入其中的分解母液反应。
14.作为进一步的优选方案,添加的调配料浆与分解母液的体积比为1:4~8。
15.作为进一步的优选方案,溶出反应罐的顶部有管道联通。
16.作为进一步的优选方案,溶出反应罐的顶部设置有安全阀,溶出罐周边设置有氢气浓度监测仪及报警装置。
17.本发明与原有技术相比,具有如下优点:
18.1、铝灰仓的铝灰采用锁气喂料螺旋喂料至配料槽,与工业水混合后用泵输送至一段溶出进料槽,避免铝灰添加过程中有氧气进入生产系统,导致因此给生产系统带来的不安全性。
19.2、实现了铝灰的连续进出料,保证整个生产过程连续运行,确保生产过程中产生的氢气的量与压力稳定,从而实现氢气的安全、稳定、有效回收利用。
附图说明
20.图1为本发明的一段溶出方式一;
21.图2为本发明的一段溶出方式二。
22.附图中的标记为:1-铝灰仓,2-水道专业来新水,3-分解母液,4-分解母液槽,5-料浆配料槽,6-溶出反应罐,7-溶出液罐,8-气液分离器,9-氨气吸收系统,10-下一道工序。
具体实施方式
23.下面将结合本发明实施例中的附图,对本发明实施例中的技术方案进行清楚、完整地描述。
24.实施例1:
25.如图1所示,本实施例提供了一种铝灰综合利用过程中一段溶出工序连续稳定运行的方法,具体步骤如下:将铝灰仓1中的铝灰采用锁气螺旋加入料浆配料槽,与水道专业来新水2混合,调配制浆。调配料浆用泵输送至一段溶出反应罐6与进入其中的分解母液3混合反应。一段溶出方式一:溶出反应罐6的料浆用泵从进料罐连续向后推进,直至一段溶出反应完毕进入溶出液罐7,再进入下一工序10;一段溶出方式二:一段溶出反应罐6呈阶梯状分布,反应料浆自压逐级向后输送,直至一段溶出反应完毕进入出料罐,出料至溶出液罐7再输送至下一道生产工序10。一段溶出反应产生的气体,通过其顶部设置的排气管道自压输送至气液分离器8进行汽液分离,然后经管道自压输送至氨气吸收系统9,经过氨气吸收后,用管道输送至燃烧系统,回收氢气能源。
26.实施例2:
27.本实施例在实施例1的基础上,进一步限定了:粉煤灰与工业水的混合比例为:制浆固含500~1000g/l,调配时间小于60分钟。
28.实施例3:
29.本实施例在实施例1的基础上,进一步限定了:粉煤灰与工业水制浆混合的配料槽容积为:20~30m3。
30.实施例4:
31.本实施例在实施例1的基础上,进一步限定了:所配铝灰浆用泵连续输送至一段溶出进料槽6,与进入的分解母液3混合、反应。
32.实施例5:
33.本实施例在实施例1的基础上,进一步限定了:所配铝灰浆与分解母液3添加至一段溶出反应罐6的体积比为1:4~8混合。
34.实施例6:
35.本实施例在实施例1的基础上,进一步限定了:一段溶出方式一:进料罐的料浆用泵从进料罐连续向后推进,直至一段溶出反应完毕进入溶出液罐7,再进入下一工序10。
36.实施例7:
37.本实施例在实施例1的基础上,进一步限定了:一段溶出方式二:一段溶出反应罐呈阶梯状分布,进料罐位置最高,出料罐位置最低。一段溶出反应罐的料浆,自压从进料罐向后逐级连续推送,直至反应完毕,从一段溶出出料罐出料至溶出液罐7,然后出料至下一道生产工序10。
38.实施例8:
39.本实施例在实施例1的基础上,进一步限定了:料浆在一段溶出反应罐里的停留时间为6~10小时。
40.实施例9:
41.本实施例在实施例1的基础上,进一步限定了:一段溶出反应罐6产生的气体,通过其顶部设置的管道自压输送至气液分离器8,进行1~2级汽液分离处理。
42.实施例10:
43.本实施例在实施例1的基础上,进一步限定了:一段溶出反应罐6产生的气体经过1~2级汽液分离处理后自压输送至氨气吸收系统9,经过氨气吸收后,用管道输送至燃烧系统,回收氢气能源。
44.实施例11:
45.本实施例在实施例1的基础上,进一步限定了:一段溶出反应罐6顶部设置有安全阀,其工作环境设置有气体检测仪和气体报警装置。
46.尽管参照前述实施例对本发明进行了详细的说明,对于本领域的技术人员来说,其依然可以对前述各实施例所记载的技术方案进行修改,或者对其中部分技术特征进行等同替换,凡在本发明的精神和原则之内,所作的任何修改、等同替换、改进等,均应包含在本发明的保护范围之内。
再多了解一些
本文用于企业家、创业者技术爱好者查询,结果仅供参考。