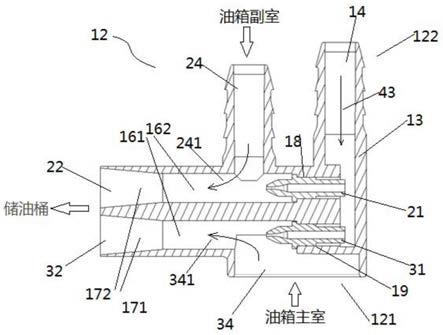
1.本发明涉及一种引射泵,尤其涉及一种主、副引射泵集成一体的双引 射泵,一种单引射泵以及具有该泵的燃油供应系统。
背景技术:
2.引射泵也称为射流泵,其利用具有一定压力的液体作为工作液体来引 射或抽吸具有较低压力或无压力液体,广泛地应用于多种流体设备中,例 如,在汽车的燃油供应系统,用以引射油箱底部的燃油。
3.在汽车油箱的应用场合,引射泵通常与用于将燃油从油箱泵送至发动 机的油泵相配合。具体地说,引射泵布置在油箱的底部,接收来自油泵支 路或回油管路的加压燃油以作为工作液体,并且将油箱底部的燃油抽吸至 油泵或油泵所在的储油桶,由此当油箱中燃油的液位亦即油位很低时也能 通过油泵泵送该燃油。特别地,在某些类型的汽车、例如四驱型汽车中, 油箱通常是包括主油箱和副油箱的马鞍形油箱。对于这种油箱,通常在主 油箱和副油箱中均布置引射泵。而且,现有的引射泵一般通过注塑成型。
4.专利文献1(cn206770296u)中公开了一种引射泵,如图1所示,该 引射泵1包括压力封闭区域2,靠近该压力封闭区域2的推进介质通路3、 推进射流喷嘴4、吸入通路5以及沿燃料液体流动方向位于该吸入通路5 下游的混合区段6和扩散区段7,该压力封闭区域2包括封闭件2a以及用 于保持该封闭件的保持座2b。该封闭件为球形件例如钢球。
5.然而,上述技术面临下述的困境:
6.1、现有的主引射泵和副引射泵都需要通过压装钢球来堵工艺孔,生产 线压装钢球的工序需要监控压装力和速度,压装钢球经常导致引射泵壳体 开裂。压完钢球还需要热铆封堵。
7.2、现有的燃油泵内,主引射泵和副引射泵是独立的两个总成,需要两 套独立的产品模具,两个独立的生产装配。
8.3、目前国内的模具水平在制造现有引射泵的时候,很难做出上述推进 射流喷嘴4的0.4mm的喷射孔。
9.4、由于引射泵喷嘴尺寸有不同的应用,造成市场上有很多的引射泵变 种。
10.为了解决相应存在的下述一项或多项问题:
[0011]1’
、生产成本高:需伺服电机压装钢球,需要热铆封堵钢球。质量风 险:压钢球容易开裂。
[0012]2’
、生产成本高:两套模具,两套生产。
[0013]3’
、规格变种多,物料管理麻烦。
[0014]4’
、目前工艺上难以实现0.4mm孔径等级的喷射孔,引射泵应用受限。
[0015]
综上,迫切需要一种新型的设计。
技术实现要素:
[0016]
为了解决上述技术问题,申请人经过锐意创新,认识到首先可以利用 可以独立加工的0.4mm孔径等级的喷嘴来替代一体形成于泵壳体中的喷 射孔,由此可以取消压装钢球这个工序,降低生产成本,降低开裂风险。 如此,通过将喷嘴做成独立的零件,可以在国内实现0.4mm的模具加工, 同时以后如果有不同的应用,只要变换喷嘴,可以保持引射泵壳体不变。
[0017]
进而,可以采用一种主、副引射泵集成一体的双引射泵设计,由此可 降低模具投资,相应解决上述技术问题。
[0018]
更具体地,本发明的目的是提供一种双引射泵,其特征在于,在泵壳 体中一体地并联形成有共用推进介质通路的主引射泵和副引射泵,所述主 引射泵还包括:主室侧吸入通路、主室侧混合区段、主室侧扩散区段和位 于所述推进介质通路与所述主室侧吸入通路之间的筒状主喷嘴装配部;所 述副引射泵还包括:副室侧吸入通路、副室侧混合区段、副室侧扩散区段 和固定于所述推进介质通路与所述副室侧吸入通路之间的筒状副喷嘴装配 部,所述主引射泵还包括:与所述泵壳体分体地形成、固定于所述主喷嘴 装配部的主喷嘴,所述主喷嘴通过其外周部分以形状配合的方式装配在所 述主喷嘴装配部中,并且所述副引射泵还包括:与所述泵壳体分体地形成、 固定于所述副喷嘴装配部的副喷嘴,所述副喷嘴通过其外周部分以形状配 合的方式装配在所述副喷嘴装配部中。
[0019]
由此,所述主引射泵的流路形成为:推进射流经由所述推进介质通路 从所述主喷嘴喷出时,与来自所述主室侧吸入通路的燃料在所述主室侧混 合区段混合后,经过所述主室侧扩散区段送出,所述副引射泵的流路形成 为:推进射流经由所述推进介质通路从所述副喷嘴喷出时,与来自所述副 室侧吸入通路的燃料在所述副室侧混合区段混合后,经过所述副室侧扩散 区段送出。
[0020]
在一个优选方案中,所述主喷嘴能够通过所述主室侧扩散区段和所述 主室侧混合区段到达所述主喷嘴装配部,
[0021]
所述副喷嘴能够通过所述副室侧扩散区段和所述副室侧混合区段到达 所述副喷嘴装配部。
[0022]
在一个优选方案中,所述主喷嘴和所述副喷嘴分别过盈配合于所述主 喷嘴装配部和所述副喷嘴装配部中。
[0023]
在一个优选方案中,所述主喷嘴和/或所述副喷嘴在远离各自的喷口 (30)一侧分别形成有凸肋,能够借助于该凸肋卡定于在所述泵壳体上相 应形成的卡槽。
[0024]
在一个优选方案中,所述主喷嘴和所述副喷嘴分别在靠近所述喷口一 侧形成有凸缘,能够借助于该凸缘止挡于在所述主喷嘴装配部和所述副喷 嘴装配部上形成的台肩部。
[0025]
在一个优选方案中,所述主喷嘴和所述副喷嘴在相比所述凸缘更靠近 所述喷口侧分别形成有筋位,供安装夹具保持以将所述主喷嘴和所述副喷 嘴分别送至所述主喷嘴装配部和所述副喷嘴装配部。
[0026]
在一个优选方案中,所述筋位能够被所述安装夹具经由形状卡合而施 力,使得所述主喷嘴和所述副喷嘴相对所述泵壳体分别旋转一定角度,从 而使所述凸肋卡定于所述卡槽。
[0027]
在一个优选方案中,在所述泵壳体的所述主喷嘴装配部和所述副喷嘴 装配部上,相比所述台肩部更远离所述推进介质通路一侧形成有凸起,在 所述凸肋卡定于所述卡槽时,该凸起卡定在形成于所述凸缘的周面上的凹 槽中。
[0028]
本发明还提供一种引射泵,在泵壳体中形成有:推进介质通路、推进 射流喷嘴、吸入通路以及沿燃料液体流动方向位于该吸入通路下游的混合 区段和扩散区段,其特征在于,所述推进射流喷嘴与所述泵壳体分体地形 成,所述泵壳体还形成有位于所述推进介质通路与所述吸入通路之间的筒 状喷嘴装配部,所述推进射流喷嘴能够通过所述扩散区段和所述混合区段 到达并卡定于所述喷嘴装配部。
[0029]
本发明还提供一种燃油供应系统,其包括用于容纳燃油的油箱,以及 与安放在油箱中的油泵相关联的、上述的双引射泵或上述的引射泵。
[0030]
根据本发明的上述技术方案,可以取消压装钢球这个工序,降低生产 成本,降低开裂风险。通过将主引射泵和副引射泵集成为一个泵壳体,可 降低模具投资。尤其是将喷嘴做成独立的零件,可以在国内实现0.4mm的 模具加工,同时以后如果有不同的应用,只要变换喷嘴,而保持引射泵壳 体不变。
附图说明
[0031]
下面将参照示意性的附图更详细地描述本发明。附图及相应的实施例 仅是为了说明的目的,而非用于限制本发明。其中:
[0032]
图1示出的一种常规引射泵的结构示意图。
[0033]
图2示出了适用根据本发明实施例的双引射泵的外观图。
[0034]
图3示出了根据本发明实施例的双引射泵的剖视图。
[0035]
图4示出了图3的双引射泵的组装前的外观图。
[0036]
图5示出了根据本发明实施例的引射泵的剖视图。
[0037]
图6示出了根据本发明实施例的一个喷嘴的立体图。
[0038]
图7示出了根据本发明实施例的双引射泵的立体图。
具体实施方式
[0039]
下面详细描述本发明的示例性实施例。下文描述的和附图示出的示例 性实施例旨在教导本发明的原理,使本领域技术人员能够在若干不同环境 中和对于若干不同应用实施和使用本发明。因此,示例性实施例并不意在 且不应该被认为是对本发明保护的范围的限制性描述。
[0040]
【双引射泵的总体结构】
[0041]
图2示出了根据本发明的双引射泵12的一个实施例的剖视图。为了简 化示图,省略示出储油桶。带有一定压力的驱动液体经由引射泵驱动软管 11供给至双引射泵12。副油箱吸油管13亦连接至双引射泵12。
[0042]
更具体地,如图3所示,该双引射泵12包括总体上集成为一体的主引 射泵121和副引射泵122。主引射泵121和副引射泵122共用推进介质通 路14,并且通过集成为一体而共用一个泵壳体13。
[0043]
沿液流43、341方向,主引射泵121还包括:主室侧推进射流喷嘴31、 与油箱主室侧
连通的主室侧吸入通路34、沿液流方向位于吸入通路34下 游侧的混合区段161和扩散区段171。
[0044]
沿液流43、241方向,副引射泵122还包括:副室侧推进射流喷嘴21、 与油箱副室侧的副油箱吸油管13连通的副室侧吸入通路24、沿液流方向 位于吸入通路24下游侧的混合区段162和扩散区段172。
[0045]
由如可知,沿液流方向,主引射泵121和副引射泵122构成为并联式 结构。其中,与油箱主室相连的一侧的主引射泵121的功能在于:将主油 箱内的燃油吸入储油桶内,如油箱主室的燃油流341所示;与油箱副室相 连的一侧的副引射泵122的功能在于:将副油箱内的燃油吸入储油桶内, 如油箱副室的燃油流241所示。
[0046]
在该实施例中,喷嘴21、31与泵壳体13是分体形成的。通过安装喷 嘴21、31形成负压,从而实现期望的引射功能。而且,省去了常规的包括 例如钢球的封闭件以及用于保持该封闭件的保持座的压力封闭区域。
[0047]
【喷嘴及其安装结构】
[0048]
图4示出了图3的双引射泵的组装前的外观图。其中,喷嘴21、31、 以及泵壳体13彼此独立地由注塑成型制成,根据应用场合,喷嘴21、31 具有类似结构,也可能完全相同的规格。尤其是,各喷嘴21、31分别具有 统一的外径尺寸,即使内孔径不同,也可以一致地安装适用于泵壳体13 内。
[0049]
下面参照参见图3-7说明具体的喷嘴结构及其组装。
[0050]
以喷嘴21为例,如图6所示,形成为中空结构,在喷口30侧起,分 别形成有筋位26、凸缘33、筒体311、筒体321以及凸肋28、29。如图所 示,该筋位26可以沿与凸缘33相交的方向连接于喷嘴端部以及凸缘33, 以提高刚度。
[0051]
组装过程大体上可以分为四个阶段,喷嘴装配前状态(图4);利用 与筋位16匹配的夹具将喷嘴21送入引射泵喷射管口22,经由扩散区段172 和混合区段162,最后到达装配部18,通过旋转装配定位于卡槽181。
[0052]
装配部18一体地设置于泵壳体13的通路内壁,介于推进介质通路14 与副室侧吸入通路24之间,具有与喷嘴21的外周侧过盈配合的相应形状。
[0053]
由此,主、副喷嘴可通过其外周部分以形状配合的方式装配在主、副 喷嘴装配部中。在此,该外周部分除了包括喷嘴21的与上述装配部18配 合的外周侧部分以外,还包括后面详述的凸肋28、29,凸缘33以及筋位 26。
[0054]
在装配部18的一侧形成有台肩部182以作为凸缘33的止挡部,在台 肩部182的更靠喷口30侧,装配部18还形成有凸起184(相对泵壳体13 的装配部18处的内壁面凸起大约0.1mm~0.2mm),以与喷嘴凸缘33上所 形成的一个凹槽27相配合。
[0055]
在装配部18的远离喷口30的另一侧形成有卡槽181(如图7所示, 以与凸肋28、29相卡合。
[0056]
由此,当喷嘴21到达装配部18,凸缘33被台肩部182止挡不能再深 入时,表明喷嘴21已顺着卡槽181装配到停止位置,随后用上述夹具对筋 位16施力,使喷嘴21旋转例如90
°
,喷嘴21上起倒钩作用的凸肋28、 29和泵壳体13内的卡槽凸起181配合卡定。
[0057]
在此所述的结构、安装过程同样适用于具有喷嘴31的主引射泵侧。
[0058]
在该装配部18处的这一段配合长度内,喷嘴21、31和泵壳体13只要 采用过盈配合
即可保证一定的密封性能。
[0059]
对于本领域技术人员而言,容易确保喷嘴21、31和泵壳体13的这段 配合处的尺寸,因为此处在模具上都是一体加工成型的,而且制品的圆度 也很容易得到确保。
[0060]
在旋转装配后,喷嘴21、31就不会从泵壳体13中脱落。
[0061]
旋转装配相比于常规的弹性卡扣装配的优点在于:
[0062]
1.装配过程中弹性卡扣有断裂风险。
[0063]
2.构件都是刚性连接的,尺寸好保证,同时装配过程中不需要留余量。
[0064]
虽然喷嘴装到位后,不会再受到旋转方向的力;而且喷嘴和泵壳体又 是过盈配合,泵壳体对喷嘴有一定的抱紧力,因而喷嘴几乎没有脱落的风 险,但是,在本实施例中,优选地,还在泵壳体13上设置凸起184(284) (高度大约0.1mm~0.2mm),与喷嘴凸缘33上的凹槽27相应卡合。即,在 喷嘴旋转装配的最后,凸起硬挤压进凹槽中。因为都是塑料件,而且凸起 高度很小,也可容易地实现。由此,进一步提高了卡定的可靠性。
[0065]
上述喷嘴上的筋位26,用于在夹具上定位,确保喷嘴21、31能进入 卡槽内。由此以简单的结构实现了方便可靠的可操作性。
[0066]
如上述,根据本发明的结构,仍然能够容易地由注塑成型制成上述一 体化集成的结构,避免了现有技术中的钢球、工艺孔等设置及其潜在技术 问题。在模具成本和生产成本方面都有很大优势,不仅节省钢球以及一根 软管,同时还节省安装,无开裂质量风险。
[0067]
而且,通过采用适配的喷嘴,能容易地实现0.4mm孔径等级的喷嘴, 扩大了油泵的流体应用范围,还能维持压力,并且可以平台化管理,不需 要很多的变种产品。
[0068]
【引射泵/单引射泵】
[0069]
尽管上面主要以包括总体上集成为一体的主引射泵121和副引射泵 122的双引射泵12为例进行了说明,但不言而喻,也可以变形为仅由主引 射泵121和副引射泵122的其中一者构成的引射泵即所谓单引射泵,同样 可以相应地实现上述的省去钢球、旋转安装、易适配喷嘴等各种优点。
[0070]
【燃油供应系统】
[0071]
根据本发明的单、双引射泵可以适用于一种燃油供应系统,其包括用 于容纳燃油的油箱,该单、双引射泵与安放在油箱中的油泵相关联,所述 油箱可为包括主油箱和副油箱的马鞍形油箱。
[0072]
应当指出,上面的说明仅是示例性的,本领域技术人员可以根据上述 说明对本发明实施例做出各种修改和变型,这些修改和变型均在本发明的 保护范围之内。
再多了解一些
本文用于企业家、创业者技术爱好者查询,结果仅供参考。