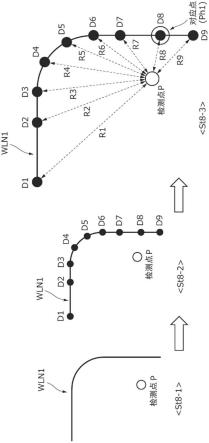
1.本发明涉及补焊设备以及补焊方法。
背景技术:
2.专利文献1公开了一种形状检查设备,其将狭缝光投射到焊道上,通过用狭缝光扫描焊道来对焊道上依次形成的形状线进行成像,并且基于依次形成的形状线的成像数据,获取焊道的三维形状作为点云数据。形状检查设备根据输入,对基于点群数据显示的焊道设置与通过狭缝光扫描焊道而形成的形状线不同的切割线,并且基于与切割线相对应的点云数据计算切割线处焊道的截面形状。形状检查设备将根据截面形状计算出的各种特征量与预先登记的各种特征量的允许范围进行比较,并且确定特征量的好坏。
3.引文列表
4.专利文献
5.专利文献1:jp-a-2012-37487
技术实现要素:
6.技术问题
7.本发明提供用于更有效且自动地对通过主焊所产生的焊接工件的缺陷部分执行补焊的补焊设备和补焊方法。
8.问题的解决方案
9.本发明提供一种补焊设备。该补焊设备包括:获取单元,被配置为获取外观检查结果,该外观检查结果包括关于由焊接机器人执行的主焊所产生的焊接工件的焊道的缺陷部分的位置的信息;以及机器人控制单元,被配置为在由焊接机器人执行的主焊的虚拟焊线上设置多个插补点,并且指示焊接机器人对与获取的缺陷部分的位置最接近的插补点执行补焊,该虚拟焊线是基于用于执行主焊的主焊程序模拟的。
10.本发明提供一种由补焊设备执行的补焊方法。该补焊方法包括以下过程:获取外观检查结果,该外观检查结果包括关于由焊接机器人执行的主焊所产生的焊接工件的焊道的缺陷部分的位置的信息;在由焊接机器人执行的主焊的虚拟焊线上设置多个插补点,该虚拟焊线是基于用于执行主焊的主焊程序模拟的;以及指示焊接机器人对与获取的缺陷部分的位置最接近的插补点执行补焊。
11.发明的有益效果
12.根据本发明,能够更有效且自动地对通过主焊所产生的焊接工件的缺陷部分执行补焊。
附图说明
13.图1是表示焊接系统的系统配置示例的示意图。
14.图2是表示根据第一实施例的检查控制设备、机器人控制设备以及主机设备的内
部配置示例的图。
15.图3是表示由根据第一实施例的焊接系统执行的主焊和补焊的操作步骤的一个示例的时序图。
16.图4是表示指定与检测点最接近的插补点的步骤的示例的流程图。
17.图5a是示意性地表示与位于虚拟焊线上并且与检测点最接近的对应点的指定相关的操作概要示例的图。
18.图5b是示意性地表示与位于虚拟焊线上并且与检测点最接近的对应点的指定相关的操作概要示例的图。
19.图6是表示根据第二实施例的检查控制设备、机器人控制设备以及主机设备的内部配置示例的图。
20.图7是表示由根据第二实施例的焊接系统执行的主焊和补焊的操作步骤的示例的时序图。
21.图8是表示根据第三实施例的检查控制设备、机器人控制设备以及主机设备的内部配置示例的图。
22.图9是表示由根据第三实施例的焊接系统执行的主焊和补焊的操作步骤的示例的时序图。
具体实施方式
23.(本公开的背景)
24.包括专利文献1在内的相关技术没有公开如下技术:焊接机器人等基于通过主焊所产生的工件(以下简称“焊接工件”)的外观检查结果自动地执行补焊以修正(修复)产生焊接缺陷(即缺陷)的部分。为了通过焊接机器人自动执行补焊,与主焊类似,需要预先准备用于补焊的程序,其中指定要执行补焊的部分。为了防止在实际对焊接缺陷部分执行补焊期间焊接机器人的前端部分与焊接工件或用于固定焊接工件的夹具产生干涉,优选地,通过部分改变为产生焊接工件而生成的主焊程序来生成补焊程序。即,通过巧妙地利用主焊时的焊接机器人的操作轨迹,能够使补焊时的焊接机器人的操作稳定。
25.在焊接工件的外观检查中,与焊接缺陷部分(以下,简称为“缺陷部分”)的位置相关的信息(例如坐标)由相机或投射激光的传感器等检查设备检测,并且该信息作为缺陷部分信息输出。因此,为了生成上述补焊程序,需要具体指定主焊程序的哪个焊接段与缺陷部分对应。然而,例如,当通过主焊形成的焊道较厚时,或者当从检查设备输出的缺陷部分的位置精度存在轻微误差时,检查设备检测到的缺陷部分信息不一定位于主焊程序所规定的焊接机器人的操作轨迹上。因此,在焊接机器人自动执行补焊的情况下,存在补焊的补焊位置的精度降低、补焊的效率没有提高的问题。
26.在以下的实施例中,对用于更有效并且自动地对通过主焊所产生的焊接工件的缺陷部分执行补焊的补焊设备以及补焊方法的示例进行说明。
27.在下文中,将适当地参考附图来详细描述具体公开根据本公开的补焊设备和补焊方法的实施例。可以省略不必要的详细描述。例如,可以省略公知事项的详细描述或基本相同配置的重复描述。这是为了避免以下描述中不必要的冗余,并有助于本领域技术人员的理解。应当注意的是,提供附图和以下描述是为了使本领域的技术人员能够充分理解本公
开内容,并不旨在限制权利要求的范围。
28.(第一实施例)
29.根据第一实施例的补焊设备获取外观检查结果,该外观检查结果包括关于由焊接机器人执行的主焊所产生的焊接工件的焊道的缺陷部分的信息,并且补焊设备基于外观检查结果,指示焊接机器人对位于主焊时的焊接机器人的操作轨迹上并且与缺陷部分最接近的对应部分执行补焊。以下,将要通过主焊执行焊接的工件定义为“原始工件”,将通过主焊产生(制造)的工件定义为“焊接工件”,并且将对检测到的“焊接工件”的焊接缺陷部分执行补焊后的工件定义为“补焊工件”。将通过焊接机器人等将原始工件与另一原始工件接合来产生焊接工件的过程定义为“主焊”,并且将通过焊接机器人等对焊接工件的缺陷部分进行修正(修复)的过程定义为“补焊”。“焊接工件”或“补焊工件”不限于通过一次主焊所产生的工件,也可以是通过两次或更多次主焊所产生的复合工件。
30.(焊接系统配置)
31.图1是表示焊接系统100的系统配置示例的示意图。焊接系统100包括:与外部存储设备st、输入接口ui1以及监控器mn1连接的主机设备1;机器人控制设备2;检查控制设备3;主焊机器人mc1a和补焊机器人mc1b。主焊机器人mc1a和补焊机器人mc1b可以被配置为单独的机器人,或者可以被配置为同一焊接机器人mc1。为了使以下说明易于理解,假设主焊和补焊都由焊接机器人mc1执行。尽管机器人控制设备2和主焊机器人mc1a、补焊机器人mc1b在图1中仅示出了一对,但也可以设置多个这样的对。焊接系统100还可以包括检查设备4。
32.作为补焊设备的一个示例的主机设备1经由机器人控制设备2对由焊接机器人mc1执行的主焊的执行(例如,主焊的开始和结束)进行统一控制。例如,主机设备1从外部存储设备st读出用户(例如,焊接操作员或系统管理员。以下同样适用)预先输入或设置的焊接相关信息,利用该焊接相关信息生成包括焊接相关信息的内容在内的主焊执行指令,并且将主焊执行指令发送到对应机器人控制设备2。当由焊接机器人mc1执行的主焊完成时,主机设备1从机器人控制设备2接收表示焊接机器人mc1执行的主焊完成的主焊完成报告,将对应焊接工件的状态更新为表示主焊完成的状态,并且将该状态记录在外部存储设备st中。上述的主焊执行指令不限于由主机设备1生成,也可以由例如执行主焊的工厂等中的设备的操作面板(例如,可编程逻辑控制器(plc))生成,或者由机器人控制设备2的操作面板(例如示教器(tp))生成。示教器(tp)是用于操作与机器人控制设备2连接的主焊机器人mc1a、补焊机器人mc1b等的设备。
33.主机设备1经由检查控制设备3统一控制由检查设备4执行的外观检查的执行(例如,外观检查的开始和结束)。例如,当主机设备1从机器人控制设备2接收到主焊完成报告时,主机设备1生成对由焊接机器人mc1产生的焊接工件的外观检查执行指令,并且向检查控制设备3发送外观检查执行指令。当检查设备4执行的外观检查完成时,主机设备1从检查控制设备3接收表示检查设备4执行的外观检查完成的外观检查报告,将对应焊接工件的状态更新为外观检查完成的状态,并且将该状态记录在外部存储设备st中。
34.主机设备1经由机器人控制设备2对由焊接机器人mc1执行的补焊的执行(例如补焊的开始和结束)进行统一控制。例如,当主机设备1接收到来自检查控制设备3的外观检查报告时,主机设备1对由焊接机器人mc1产生的焊接工件生成补焊执行指令,并且将补焊执行指令发送到机器人控制设备2。当由焊接机器人mcl执行的补焊完成时,主机设备1从机器
人控制设备2接收表示由焊接机器人mc1执行的补焊完成的补焊完成报告,将对应焊接工件的状态更新为补焊完成的状态,并且将该状态记录在外部存储设备st中。
35.这里,焊接相关信息是表示由焊接机器人mc1执行的主焊的内容的信息。焊接相关信息针对主焊的每个过程预先生成,并且登记在外部存储设备st中。焊接相关信息例如包括主焊中使用的原始工件的数量、包括在主焊中使用的原始工件的id、名称以及焊接部分在内的工件信息、执行主焊的预定执行日期、要产生的焊接工件的数量、以及主焊过程中的各种焊接条件。焊接相关信息不限于上述项目的数据。机器人控制设备2基于从主机设备1发送的执行指令,使焊接机器人mc1使用由该执行指令指定的多个原始工件来执行主焊。本说明书中不限定主焊的种类,为了使说明容易理解,以接合多个原始工件的过程为例进行说明。
36.主机设备1与监控器mn1、输入接口ui1和外部存储设备st连接,使得主机设备1可以向监控器mn1、输入接口ui1和外部存储设备st输入数据和从它们输出数据。主机设备1还与机器人控制设备2连接,使得主机设备1与机器人控制设备2之间能够进行数据通信。主机设备1可以包括以一体方式包括监控器mn1和输入接口ui1的终端设备p1,并且还可以以一体方式包括外部存储设备st。在这种情况下,终端设备p1是用户在执行主焊之前使用的个人计算机(pc)。终端设备p1不限于上述的pc,也可以是智能手机、平板终端等具有通信功能的计算机设备。
37.监控器mn1可以配置有诸如液晶显示器(led)或有机电致发光(el)之类的显示设备。监控器mn1可以显示例如包括表示主焊完成的通知或表示补焊完成的通知的画面,并且该通知从主机设备1输出。代替监控器mn1,扬声器(未示出)可以与主机设备1连接,或者监控器mn1和扬声器(未示出)可以都与主机设备1连接。主机设备1可以经由扬声器输出表示主焊完成的通知或表示补焊完成的声音。
38.输入接口ui1是检测用户的输入操作并且将输入操作输出到主机设备1的用户接口,例如可以由鼠标、键盘、触摸面板等构成。输入接口ui1例如接收用户生成焊接相关信息时的输入操作、或向机器人控制设备2发送主焊执行指令时的输入操作。
39.外部存储设备st例如由硬盘驱动器或固态驱动器构成。外部存储设备st存储例如针对每个主焊生成的焊接相关信息的数据、以及通过主焊产生的焊接工件或通过补焊修复的补焊工件的工件信息(参见上述说明)。
40.作为补焊设备的一个示例的机器人控制设备2与主机设备1连接,使得在机器人控制设备2与主机设备1之间可以进行数据通信,并且机器人控制设备2与焊接机器人mc1连接,使得在机器人控制设备2与焊接机器人mc1之间可以进行数据通信。当机器人控制设备2接收到从主机设备1发送的主焊执行指令时,机器人控制设备2基于主焊执行指令控制对应焊接机器人mc1以执行主焊。当机器人控制设备2检测到主焊完成时,机器人控制设备2生成表示主焊完成的主焊完成报告,并且将主焊完成报告通知给主机设备1。因此,主机设备1能够根据从机器人控制设备2发送的报告,适当地检测到主焊的结束。通过机器人控制设备2检测主焊完成的方法例如可以是基于来自送丝设备300中设置的传感器(未示出)的表示主焊完成的信号来确定主焊完成的方法,或者可以是已知的方法,并且检测主焊完成的方法的内容不受限制。
41.当机器人控制设备2接收到从主机设备1发送的补焊执行指令时,机器人控制设备
2根据由检查控制设备3生成的补焊程序,基于补焊执行指令控制对应焊接机器人mc1从而执行补焊。当机器人控制设备2检测到补焊完成时,机器人控制设备2生成表示补焊完成的补焊完成报告,并且将补焊完成报告通知给主机设备1。因此,主机设备1能够根据从机器人控制设备2发送的报告,适当地检测到补焊的结束。通过机器人控制设备2检测补焊完成的方法例如可以是根据来自送丝设备300所具备的传感器(未示出)的表示补焊完成的信号来确定补焊完成的方法,或者可以是已知的方法,并且检测补焊完成的方法的内容不受限制。
42.作为焊接机器人的一个示例的焊接机器人mc1与机器人控制设备2连接,使得焊接机器人mc1与机器人控制设备2之间能够进行数据通信。焊接机器人mc1在对应机器人控制设备2的控制下,根据来自主机设备1的指令执行主焊或补焊。如上所述,焊接机器人mc1可以包括设置用于主焊的主焊机器人mc1a和设置用于补焊的补焊机器人mc1b。
43.作为补焊设备的一个示例的检查控制设备3与主机设备1、机器人控制设备2、检查设备4连接,从而可以在检查控制设备3、主机设备1、机器人控制设备2和检查设备4之间进行数据通信。当检查控制设备3接收到从主机设备1发送的外观检查执行指令时,检查控制设备3使检查设备4对由焊接机器人mc1产生的焊接工件的焊接部分执行外观检查(例如,检查主焊形成的焊道是否符合预定主焊道的形状)。例如,检查控制设备3基于外观检查执行指令中包括的焊接工件的焊接部分的信息,控制检查设备4以检测形成在焊接部分中的焊道的形状,并且将每个主焊的预定主焊道(未示出)的形状与实际检测到的焊道的形状进行比较。检查控制设备3基于该比较生成外观检查报告,并且将外观检查报告发送到主机设备1。
44.当检查控制设备3确定焊接工件的外观检查结果不合格时,检查控制设备3通过使用从检查设备4获取的包括检测点的位置信息在内的外观检查结果生成用于修正(修复)焊接缺陷部分的补焊程序,该检测点表示检测到焊接缺陷部分的位置。检查控制设备3将补焊程序和外观检查结果相关联地发送到机器人控制设备2。
45.检查设备4与机器人控制设备2连接,从而可以在检查设备4和机器人控制设备2之间进行数据通信。检查设备4基于从检查控制设备3发送的外观检查执行指令,根据外观检查执行指令中包括的焊接部分信息、通过检查设备4(见图2)生成的焊接部分的焊道的形状数据、以及上述主焊道的形状数据,确定焊接部分是否存在焊接缺陷(执行外观检查)。检查设备4将焊接部分中被确定为焊接缺陷部分的缺陷部分的信息(例如,指示检测到焊接缺陷的部分的位置的检测点、焊接缺陷的种类)作为外观检查报告发送到检查控制设备3。
46.图2是表示根据第一实施例的检查控制设备3、机器人控制设备2以及主机设备1的内部配置示例的图。为了便于说明,图2中未示出监控器mn1和输入界面ui1。
47.焊接机器人mc1在机器人控制设备2的控制下,根据来自主机设备1的指令,执行主焊、补焊等各种过程。焊接机器人mc1在主焊或补焊过程中执行例如电弧焊接。或者,焊接机器人mc1也可以执行电弧焊接以外的焊接(例如,激光焊接或气焊)。在这种情况下,虽然未示出,但是激光头(而不是焊枪400)可以经由光纤与激光振荡器连接。焊接机器人mc1至少包括机械手200、送丝设备300、焊丝301和焊枪400。
48.机械手200具有多关节臂,并且基于来自机器人控制设备2的机器人控制单元25(参照后述)的控制信号使各臂移动。因此,机械手200能够通过臂的移动来改变工件wk和焊枪400之间的位置关系(例如,焊枪400相对于工件wk的角度)。
49.送丝设备300基于来自机器人控制设备2的控制信号(参照后述)控制焊丝301的送丝速度。送丝设备300可以包括能够检测焊丝301的剩余量的传感器(未示出)。机器人控制设备2基于传感器的输出,可以检测到主焊或补焊的过程已完成。
50.焊丝301由焊枪400保持。当从电源设备500向焊枪400供电时,在焊丝301的前端与工件wk之间产生电弧,执行电弧焊接。为了便于描述,省略了用于向焊枪400供应保护气体的配置等的图示和描述。
51.主机设备1使用用户预先输入或设置的焊接相关信息,生成使用多个原始工件的主焊或者对焊接工件的焊接缺陷部分进行修正(修复)的补焊的各种过程的执行指令,并且向机器人控制设备2发送执行指令。主机没备1至少包括通信单元10、处理器11和存储器12。
52.通信单元10与机器人控制设备2和外部存储设备st连接,从而可以在通信单元10、机器人控制设备2和外部存储设备st之间进行数据通信。通信单元10将由处理器11生成的主焊或补焊的各种过程的执行指令发送到机器人控制设备2。通信单元10接收从机器人控制设备2发送的主焊完成报告、外观检查报告、补焊完成报告,并且向处理器11输出主焊完成报告、外观检查报告和补焊完成报告。主焊或补焊执行指令例如可以包括用于控制包括在焊接机器人mc1中的机械手200、送丝设备300和电源设备500的控制信号。
53.处理器11例如由中央处理单元(cpu)或现场可编程门阵列(fpga)构成,并且与存储器12协作执行各种处理和控制。具体地,处理器11通过参照存储在存储器12中的程序并且执行该程序来实现单位控制单元13的功能。
54.存储器12例如包括作为在执行处理器11的处理时使用的工作存储器的随机存取存储器(ram),以及存储用于定义处理器的处理的程序的只读存储器(rom)。ram临时存储由处理器11生成或获取的数据。定义处理器11的处理的程序被写入rom。存储器12存储从外部存储设备st读取的焊接相关信息的数据和从机器人控制设备2发送的与焊接工件或补焊工件相关的工件信息的数据(参见以下说明)。
55.单位控制单元13基于存储在外部存储设备st中的焊接相关信息,生成用于执行使用在焊接相关信息中定义(即设置)的多个原始工件的主焊或对焊接工件的补焊的执行指令。单位控制单元13可以针对要由焊接机器人mc1执行的主焊或补焊的各种过程生成不同的执行指令。由单位控制单元13生成的主焊或补焊执行指令经由通信单元10发送到对应机器人控制设备2。
56.机器人控制设备2基于从主机设备1发送的主焊或补焊执行指令,控制对应焊接机器人mc1(具体而言,机械手200、送丝设备300、电源设备500)的处理。机器人控制设备2至少包括通信单元20、处理器21和存储器22。
57.通信单元20与主机设备1、检查控制设备3、焊接机器人mc1连接,从而可以在通信单元20、主机设备1、检查控制设备3、焊接机器人mc1之间进行数据通信。在图2中,虽然简化了图示,但是在机器人控制单元25和机械手200之间、机器人控制单元25和送丝设备300之间、以及电源控制单元26和电源设备500之间,经由通信单元20发送和接收数据。通信单元20接收从主机设备1发送的主焊执行指令或补焊执行指令。通信单元20将通过主焊所产生的焊接工件的工件信息或通过补焊所产生的补焊工件的工件信息发送到主机设备1。
58.这里,工件信息不仅包括焊接工件或补焊工件的id,还至少包括在主焊中使用的多个原始工件中的每一个的id、名称、焊接部分、在执行主焊时的焊接条件、以及在执行补
焊时的焊接条件。此外,工件信息可以包括表示检测点的位置的信息(例如,坐标),该检测点表示焊接工件的缺陷部分。焊接条件或补焊条件例如包括原始工件的材料和厚度、焊丝301的材料和线径、保护气体的类型、保护气体的流量、焊接电流的设置平均值、焊接电压的设置平均值、焊丝301的送丝速度和送丝量、焊接次数和焊接时间。另外,焊接条件或补焊条件例如可以包括表示主焊或补焊的种类(例如tig焊、mag焊、脉冲焊等)的信息、机械手200的移动速度和移动时间。
59.处理器21例如由cpu或fpga构成,与存储器22协作执行各种处理和控制。具体而言,处理器21通过参照存储在存储器22中的程序并执行该程序,来实现主焊程序生成单元23、计算单元24、机器人控制单元25以及电源控制单元26的功能。
60.存储器22例如包括作为在执行处理器21的处理时使用的工作存储器的ram,以及存储用于定义处理器21的处理的程序的rom。ram临时存储由处理器21生成或获取的数据。定义处理器21的处理的程序被写入rom。存储器22存储从主机设备1发送的主焊执行指令或补焊执行指令的数据,以及通过主焊所产生的焊接工件或通过补焊所产生的补焊工件的工件信息的数据。存储器22存储要由焊接机器人mc1执行的主焊程序。主焊程序是规定使用主焊的焊接条件接合多个原始工件的主焊的具体步骤(过程)的程序。
61.主焊程序生成单元23使用从主机设备1经由通信单元20发送的主焊执行指令中包括的多个原始工件的工件信息(例如,原始工件的id、名称和焊接部分),从而基于主焊执行指令生成焊接机器人mc1要执行的主焊的主焊程序。主焊程序可以包括在执行主焊时用于控制电源设备500、机械手200、送丝设备300、焊枪400的各种参数,诸如焊接电流、焊接电压、偏移量、焊接速度和焊枪400的姿势。生成的主焊程序可以存储在处理器21中,也可以存储在存储器22的ram中。生成的主焊程序经由通信单元20被发送到检查控制设备3的补焊程序生成单元38。
62.计算单元24执行各种计算。例如,计算单元24基于由主焊程序生成单元23生成的主焊程序,计算用于控制由机器人控制单元25控制的焊接机器人mc1(具体而言,机械手200、送丝设备300、电源设备500)的参数。
63.机器人控制单元25基于由主焊程序生成单元23生成的主焊程序,生成用于驱动焊接机器人mc1(具体而言,机械手200、送丝设备300、电源设备500)的控制信号。机器人控制单元25将生成的控制信号发送到焊接机器人mc1。
64.电源控制单元26基于主焊程序生成单元23生成的主焊程序和计算单元24的计算结果来驱动电源设备500。
65.检查控制设备3基于从主机设备1发送的外观检查执行指令,控制对由焊接机器人mc1执行的主焊所产生的焊接工件或补焊工件的外观检查处理。外观检查例如是检查在焊接工件或补焊工件上形成的焊道的形状是否满足焊接部分的预定焊接标准或强度标准,或满足焊接工件或补焊工件的质量标准。为了使下面的描述易于理解,检查控制设备3基于由检查设备4获取的表示焊道形状的三维(3d)点云数据执行外观检查,从而检查形成在工件wk(例如焊接工件或补焊工件)中的焊道是否满足预定焊接标准(例如,焊道的形状相同或相似于与工件wk对应的预定主焊道的形状)。以下,将在表示焊道的形状的3d点群数据中被确定为与主焊道的形状大不相同(即,与主焊道的形状不同也不相似)的焊接部分定义为“检测点”。表示检测点的位置的信息(例如,3d位置坐标)由检查控制设备3检测。检查控制
设备3至少包括通信单元30、处理器31、存储器32和检查结果存储单元33。
66.通信单元30与主机设备1、机器人控制设备2、检查设备4连接,从而可以在通信单元30、主机设备1、机器人控制设备2、检查设备4之间进行数据通信。尽管在图2中简化了图示,但是经由通信单元30在形状检测控制单元35和检查设备4之间发送和接收数据。通信单元30接收从主机设备1发送的外观检查执行指令。通信单元30将由检查设备4执行的外观检查的结果(例如,焊接工件或补焊工件是否存在焊接缺陷部分)发送到主机设备1。
67.处理器31例如由cpu或fpga构成,与存储器32协作执行各种处理和控制。具体而言,处理器31通过参照存储在存储器32中的程序并执行该程序,来实现确定阈值存储单元34、形状检测控制单元35、数据处理单元36、检查结果确定单元37、补焊程序生成单元38的功能。
68.存储器32例如包括作为在执行处理器31的处理时使用的工作存储器的ram,以及存储用于定义处理器31的处理的程序的rom。ram临时存储由处理器31生成或获取的数据。定义处理器31的处理的程序被写入rom。存储器32存储从主机设备1发送的焊接工件的外观检查执行指令的数据,以及通过主焊所产生的焊接工件或通过补焊所产生的补焊工件的工件信息的数据。存储器32存储从机器人控制设备2发送的主焊程序和计算结果。存储器32还存储由补焊程序生成单元38生成的补焊程序的数据。
69.补焊程序是使用通过基于主焊程序的主焊模拟获取的主焊的虚拟焊线(即基于主焊程序执行主焊从而焊接而成的虚拟焊线)上设置的多个插补点、以及位于虚拟焊线上并且与检测点最接近的对应插补点(对应点)的位置信息,来规定用于修正(修复)焊接工件中的焊接缺陷部分的补焊的具体步骤(过程)的程序。补焊程序由补焊程序生成单元38生成,并且从检查控制设备3发送到机器人控制设备2。
70.主焊模拟是由补焊程序生成单元38执行的、用于获取在基于主焊程序执行主焊时的虚拟焊线的模拟。通过主焊模拟获取的虚拟焊线被获取为在三维空间中绘制的焊线。因此,即使当焊线是具有难以用弧或直线图形元素表示的形状的焊线时,根据第一实施例的焊接系统100也可以在生成用于对缺陷部分执行补焊的补焊程序时通过使用虚拟焊线来容易地生成补焊程序。由于焊接系统100可以包括根据程序使用的用于驱动焊接机器人mc1(具体而言,机械手200、送丝设备300、电源设备500)的控制信号来执行模拟,所以焊接系统100具有高度的通用性和实用性。此外,在用于在主焊中焊接自由曲线的焊线的主焊程序中,根据第一实施例的焊接系统100也可以基于生成的主焊程序来获取虚拟焊线。
71.在通过由补焊程序生成单元38执行的主焊模拟获取的虚拟焊线上设置多个插补点,并且每个插补点是用于在生成补焊程序时确定对缺陷部分的检测点执行补焊时的具有预定长度的范围内的待补焊部分的点。插补点可以在虚拟焊线上以预定间隔设置,或者可以与在焊接虚拟焊线时焊接机器人mc1在预定时间间隔的位置相对应地设置。插补点不限于以预定间隔设置,并且可以基于虚拟焊线的线类型(直线、曲线等)、虚拟焊线的曲率等设置。例如,在被划分为直线段和具有预定曲率的弯曲段的虚拟焊线上,在弯曲段中设置插补点的间隔可以小于在直线段中设置插补点的间隔,并且可以随着曲率的增加以更小的间隔在弯曲段中设置插补点。插补点可以由用户设置。此外,插补点可以以任意间隔设置,例如,可以在同一直线段中以不同的间隔设置插补点。由此,当对缺陷部分的检测点执行补焊时,根据第一实施例的焊接系统100在设置位于虚拟焊线上并且与缺陷部分的检测点最接近的
对应插补点(对应点)时,能够容易地确定包括与检测点更接近的对应点的补焊部分。此外,根据第一实施例的焊接系统100可以通过与线类型相对应地改变所设置的插补点之间的间隔,来确定包括与检测点更接近的对应点的补焊部分。
72.检查结果存储单元33例如由硬盘驱动器(hdd)或固态驱动器(ssd)构成。检查结果存储单元33存储表示工件wk(例如,焊接工件或补焊工件)的焊接部分的外观检查结果的数据,作为由处理器31生成或获取的数据的示例。表示外观检查结果的数据例如由检查结果确定单元37生成。
73.确定阈值存储单元34例如由设置在处理器31内的高速缓冲存储器构成,并且与焊接部分相对应地存储在由检查结果确定单元37执行的确定处理中使用的阈值(例如,与焊接部分相对应地设置的阈值)。阈值的示例包括与焊接部分的位置偏差相关的允许范围(阈值)、与焊道的高度相关的阈值以及与焊道的宽度相关的阈值。确定阈值存储单元34也可以存储满足客户所要求的最低焊接质量等的允许范围(例如,与焊道的高度相关的最小允许值、最大允许值等),作为补焊后外观检查期间的阈值。另外,确定阈值存储单元34也可以存储每个焊接部分的外观检查次数的上限。因此,在外观检查的次数超过通过补焊修正缺陷部分的次数的预定上限的情况下,检查控制设备3确定为难以或不可能通过由焊接机器人mc1执行的自动补焊来修正缺陷部分,从而能够防止焊接系统100的工作效率降低。
74.形状检测控制单元35基于从检查设备4发送的焊接部分的焊道的形状数据(例如3d点云数据)以及从主机设备1发送的工件wk(例如焊接工件或补焊工件)的焊接部分的外观检查执行指令,来控制检查设备4的操作。当检查设备4位于检查设备4能够对焊接部分进行拍摄(即,能够检测焊接部分的3维形状)的位置时,形状检测控制单元35例如使检查设备4发射激光,从而获取焊接部分的焊道的形状数据。当形状检测控制单元35接收到由检查设备4获取的焊道的形状数据时,形状检测控制单元35将该形状数据发送到数据处理单元36。
75.数据处理单元36将从形状检测控制单元35发送的焊接部分的焊道的形状数据转换为表示焊接部分的3维形状的图像数据。形状数据例如是包括发射到焊道表面的激光的反射轨迹在内的形状线的点群数据。数据处理单元36对输入的形状数据进行统计处理,生成与焊接部分的焊道的3维形状相关的图像数据。为了突出焊道的位置和形状,数据处理单元36可以执行边缘强调修正,其中焊道的周边部分被突出。数据处理单元36可以对每个焊接部分或缺陷部分的外观检查次数进行计数,当外观检查的次数超过预先存储在存储器32中的次数并且焊接检查结果不好时,确定通过自动补焊很难或不可能修正缺陷部分。在这种情况下,检查结果确定单元37生成包括缺陷部分的位置和缺陷因素在内的警报画面,并且将生成的警报画面经由通信单元30发送到主机设备1。发送到主机设备1的警报画面显示在监控器mn1上。
76.检查结果确定单元37使用确定阈值存储单元34中存储的阈值,基于由形状检测控制单元35获取的与焊接部分的焊道相关的形状数据,确定焊接部分是否满足预定焊接标准(例如,由主焊或补焊形成的焊道形状是否相同或相似于对应主焊道形状)。检查结果确定单元37测量焊接缺陷的检测点(参见以上描述)的位置(参见图5a和图5b),分析缺陷内容,并且估计缺陷因素。在上述确定中,检查结果确定单元37基于焊道的形状数据,计算形成在焊道上的焊线上的每个焊接部分的检查分数。作为获取单元的示例的检查结果确定单元37生成并且获取缺陷部分的测量位置、检查分数和估计的缺陷因素作为焊接部分的外观检查
结果(外观检查报告),将生成的外观检查结果存储在存储器32中,并且经由通信单元30将外观检查结果发送到主机设备1。检查结果确定单元37可以基于上述检查分数来确定焊接机器人mc1是否可以执行补焊(换言之,是由焊接机器人mc1执行补焊还是用手动执行补焊更好),并且可以将确定结果包括在外观检查结果(外观检查报告)中并且输出外观检查结果。
77.补焊程序生成单元38具有基于从机器人控制设备2发送的主焊程序来模拟焊接机器人的主焊的虚拟焊线的功能,并且使用主焊的虚拟焊线、在虚拟焊线上设置的多个插补点、从检查结果确定单元37输出的工件wk(例如焊接工件或补焊工件)的外观检查结果、以及焊接工件或补焊工件的工件信息(例如,表示焊接工件或补焊工件的焊接缺陷的检测点位置的坐标等信息),来生成由焊接机器人mc1执行的工件wk(例如焊接工件或补焊工件)的补焊程序。稍后将参考图5a和图5b描述用于生成补焊程序的步骤的细节。补焊程序可以包括在执行补焊时用于控制电源设备500、机械手200、送丝设备300、焊枪400的各种参数,诸如焊接电流、焊接电压、偏移量、焊接速度和焊枪400的姿势。生成的补焊程序可以存储在处理器31或存储器32的ram中。
78.检查设备4例如是三维形状传感器。检查设备4包括激光光源(未示出),该激光光源能够基于从检查控制设备3发送的焊接部分位置信息扫描工件wk(例如焊接工件或补焊工件)的焊接部分,检查设备4还包括相机(未示出),该相机以能够对包括焊接部分的周边在内的成像区域进行成像的方式设置,并且对发射到焊接部分的激光中的反射激光的反射轨迹(即,焊接部分的形状线)进行成像。检查设备4将基于由相机拍摄的激光的焊接部分的形状数据(换言之,焊道的图像数据)发送到检查控制设备3。上述相机至少包括镜头(未示出)和图像传感器(未示出)。图像传感器例如是诸如电荷耦合元件(ccd)或互补金属氧化物半导体(cmos)之类的固态成像设备,并且将成像表面上形成的光学图像转换为电信号。
79.(焊接系统的操作)
80.接下来,将参考图3描述由根据第一实施例的焊接系统100执行的主焊和补焊的操作步骤。图3是表示由第一实施例的焊接系统100执行的主焊和补焊的操作步骤的示例的时序图。在图3的描述中,对于使用多个原始工件的主焊和基于焊接工件的外观检查结果不合格的事实执行的补焊的每个过程,将在主机设备1、机器人控制设备2和检查控制设备3中执行的操作步骤作为示例进行描述。
81.在图3中,主机设备1获取要经历主焊的原始工件的工件信息(例如,原始工件的id、名称和焊接部分)(st1),并且生成包括原始工件的工件信息在内的主焊执行指令。主机设备1向机器人控制设备2发送包括原始工件的工件信息在内的主焊执行指令(st2)。
82.当机器人控制设备2接收到从主机设备1发送的主焊执行指令时,机器人控制设备2使用包括在主焊执行指令中的多个原始工件的工件信息,来生成由焊接机器人mc1执行的主焊的主焊程序,并且使焊接机器人mc1根据主焊程序执行主焊(st3)。当机器人控制设备2通过各种已知方法确定由焊接机器人mc1执行的主焊完成时,机器人控制设备2生成表示主焊完成的主焊完成通知,并且将该通知发送到主机设备1(st4),并且将用于产生焊接工件的主焊程序发送到检查控制设备3(st5)。当主机设备1接收到主焊完成通知时,主机设备1生成焊接工件的外观检查执行指令,并且将外观检查执行指令发送到检查控制设备3(st6)。
83.检查控制设备3基于在步骤st6中发送的外观检查执行指令,使检查设备4对焊接工件执行外观检查(st7)。在步骤st7的外观检查中,由于焊接工件存在焊接缺陷部分,因此检查控制设备3确定需要补焊(st8),基于从机器人控制设备2发送的主焊程序进行模拟,获取主焊的虚拟焊线(st9)。检查控制设备3在获取的主焊的虚拟焊线上以预定间隔设置插补点,并且生成用于对缺陷部分执行补焊的补焊程序,该缺陷部分包括位于焊线上并且与检测点最接近的对应插补点(对应点)的位置(st10)。检查控制设备3生成包括步骤st8的确定结果和补焊程序在内的外观检查报告,并且将该外观检查报告发送到机器人控制设备2(st11)。检查控制设备3将以同样方式生成的外观检查报告发送到主机设备1(st12)。
84.当主机设备1在步骤st12中接收到外观检查报告时,主机设备1生成用于焊接工件的补焊执行指令,并且将补焊执行指令发送到机器人控制设备2(st13)。当机器人控制设备2接收到从主机设备1发送的补焊执行指令时,机器人控制设备2基于由补焊执行指令指定的用于焊接工件的补焊程序(在步骤st12中接收),使焊接机器人mc1根据补焊程序执行补焊(st14)。当机器人控制设备2通过各种已知方法确定由焊接机器人mcl执行的补焊已完成时,机器人控制设备2发送补焊工件的工件信息(例如,补焊工件的id,包括在主焊中使用的多个原始工件的各自的id在内的工件信息(例如,原始工件的id、名称、原始工件的焊接部分)、执行主焊和补焊时的焊接条件)到主机设备1(st15)。
85.当主机设备1接收到从机器人控制设备2发送的包括补焊工件的id在内的工件信息时,主机设备1设置与补焊工件的id相对应的适合用户经营者的管理id,并且将表示与管理id相对应的补焊工件的焊接完成的数据存储在外部存储设备st中(st16)。
86.接着,将参考图4和图5a详细描述在补焊程序的生成中通过使用从检查设备4输出的检测点(即,表示焊接缺陷部分的位置),指定位于主焊时的焊接机器人mc1操作的操作轨迹(即,焊线)上并且与检测点最接近的插补点(对应点)的位置的操作概要示例。
87.(操作概要示例)
88.图4是表示指定与检测点p最接近的对应点ph1的步骤的一个示例的流程图。图5a是示意性地表示与位于虚拟焊线wln1上并且与检测点p最接近的对应点ph1的指定相关的操作概要示例的图。在第一实施例中,图4所示的流程图的处理由检查控制设备3所具备的处理器31(具体而言,补焊程序生成单元38)执行。在图5a和图5b所示的操作概要示例中,焊线包括两个直线部分和一个弧(弯曲)部分,并且例如发生咬边(即,通过主焊在基材上形成的趾部的坡口)作为焊接缺陷。
89.在图5a所示的操作概要示例中,补焊程序生成单元38基于从机器人控制设备2发送的主焊程序,在执行主焊模拟获得的虚拟焊线wln1上以任意间隔设置多个插补点d1、d2、d3、d4、d5、d6、d7、d8、d9。
90.在图4中,补焊程序生成单元38获取从机器人控制设备2发送的主焊程序和由检查结果确定单元37生成的外观检查结果,并且执行主焊模拟(st8-1)。补焊程序生成单元38在步骤st8-1中获取的虚拟焊线wln1上的预定位置处设置多个插补点d1至d9(st8-2)。在所设置的多个插补点d1至d9的各个位置(坐标)与外观检查结果中包括的检测点p的位置(坐标)之间的距离r1、r2、r3、r4、r5、r6、r7、r8和r9中,补焊程序通过指定位于与检测点p最接近的位置处的插补点,来指定虚拟焊线wln1上的插补点(即,对应点ph1)(st8-3)。在图5a所示的示例中,与检测点p最接近的插补点是位于与检测点p最接近的距离r8处的插补点d8,补焊
程序生成单元38将包括在步骤st8-3中指定的对应点ph1(图5a的插补点d8)在内的预定长度的范围确定为补焊部分,并且生成规定了补焊部分和补焊中使用的各种参数(例如,焊接条件)的补焊程序(st9)。
91.尽管图5a示出了多个插补点d1至d9被设置在基于主焊程序焊接的一条虚拟焊线wln1上的示例,但不言而喻,补焊程序生成单元38也可以将虚拟焊线wln1划分为直线段和弯曲段,并在每个划分段中设置多个插补点。
92.将参考图4和图5b详细描述在虚拟焊线包括具有不同曲率的多个弧(曲线)的情况下,指定位于主焊时的焊接机器人mci操作的操作轨迹(即,焊线)上的插补点(对应点)的位置的操作概要示例。图5b是示意性地表示与位于虚拟焊线wln2上并且与检测点v最接近的对应点ph2的指定相关的操作概要示例的图。
93.在图5b所示的操作概要示例中,焊线包括两个弧(弯曲)部分和一个直线部分,并且例如发生咬边(即,通过主焊在基材上形成的趾部的坡口)作为焊接缺陷。
94.在图5b所示的操作概要示例中,补焊程序生成单元38基于从机器人控制设备2发送的主焊程序,将通过执行主焊模拟获取的虚拟焊线wln2划分为一个直线段wln22和曲率不同的多个弯曲段wln21、wln23,并且以任意间隔设置多个插补点d10、d11、d12、d13、d14、d15、d16。在此,补焊程序生成单元38比较虚拟焊线wln2上的曲率不同的多个弯曲段wln21、wln23的曲率,并且确定弯曲段wln23的曲率大于弯曲段wln21的曲率。补焊程序生成单元38在曲率大的弯曲段wln23中设置更多的插补点。
95.在图4中,补焊程序生成单元38获取从机器人控制设备2发送的主焊程序和由检查结果确定单元37生成的外观检查结果,并且执行主焊模拟(st8-1)。补焊程序生成单元38在步骤st8-1中获取的虚拟焊线wln2上的预定位置处设置多个插补点d10至d16(st8-2)。在所设置的多个插补点d10至d16的每个位置(坐标)与外观检查结果中包括的检测点v的位置(坐标)之间的距离r10、r11、r12、r13、r14、r15和r16中,补焊程序通过指定与检测点v最接近的插补点,来指定在虚拟焊线wln2上的插补点(即,对应点ph2)(st8-3)。在图5b所示的示例中,与检测点v最接近的插补点是位于与检测点v最接近的距离r10处的插补点d10。补焊程序生成单元38将包括在步骤st8-3中指定的对应点ph2(图5b的插补点d10)在内的预定长度的范围确定为补焊部分,并且生成规定了补焊部分和补焊中使用的各种参数(例如,焊接条件)的补焊程序(st9)。
96.如上所述,在根据第一实施例的焊接系统100中,补焊设备(例如检查结果确定单元37)获取外观检查结果,该外观检查结果包括由焊接机器人mc1执行的主焊所产生的焊接工件的焊道的缺陷部分(例如,检测点p)的位置的信息,在与焊接机器人mc1的主焊相关并且基于用于执行主焊的主焊程序模拟获得的虚拟焊线(例如,虚拟焊线wln1)上设置多个插补点,并且指示焊接机器人mc1对与获取的缺陷部分的位置最接近的插补点执行补焊。
97.由此,补焊设备能够自动且有效地对由主焊所产生的焊接工件的缺陷部分执行补焊。即使在根据主焊程序执行主焊的焊线具有诸如自由曲线的复杂形状时,补焊设备也可以通过基于主焊程序的主焊模拟自动获取虚拟焊线wln1,因此可以缩短确定与检测到缺陷部分的检测点最接近的对应点所需的时间。因此,补焊设备能够自动且有效地对由主焊所产生的焊接工件的缺陷部分执行补焊。
98.补焊设备基于外观检查结果生成用于执行包括插补点的位置在内的补焊的补焊
程序,并且根据生成的补焊程序使焊接机器人补焊插补点。由此,补焊设备可以指定在虚拟焊线wln1上设置的多个插补点中位于虚拟焊线wln1上(即,在主焊时焊接机器人mc1的操作轨迹上)并且与检测点p最接近的插补点,并且可以经由焊接机器人mc1以包括该插补点的位置的方式自动且更有效地执行补焊。
99.补焊设备在虚拟焊线wln1上与每个预定时间的焊接机器人的位置相对应地设置多个插补点。由此,补焊设备能够更有效地生成用于修复预定范围内的焊接部分的补焊程序,该预定范围包括焊接机器人mc1主焊时的操作的操作轨迹上的、与预定时间的焊接机器人mc1的位置(坐标)相对应的位置(坐标)。
100.当虚拟焊线包括直线段和弯曲段时,补焊设备将弯曲段中的多个插补点之间的间隔设置为小于直线段中的多个插补点之间的间隔。由此,补焊设备能够容易地与直线段和弯曲段相对应地在虚拟焊线wln1上设置多个插补点,可以指定这些插补点中的、位于虚拟焊线wln1上(即,在主焊时焊接机器人mc1操作的操作轨迹上)并且与检测点p最接近的插补点,并且可以经由焊接机器人mc1以包括该插补点的位置的方式自动且更有效地执行补焊。
101.当虚拟焊线wln1具有一个或多个直线段和一个或多个弯曲段时,补焊设备将弯曲段的多个插补点之间的间隔设置为小于直线段的多个插补点之间的间隔。由此,补焊设备能够减少虚拟焊线wln1上的与检测点接近的对应点的位置的偏差,并且可以设置能够指定更准确的对应点的插补点。
102.当虚拟焊线具有两个或更多个曲率不同的弯曲段时,补焊设备将曲率大的弯曲段中的多个插补点之间的间隔设置为小于曲率小的弯曲段中的多个插补点之间的间隔。因此,补焊设备能够减少虚拟焊线wln2上的曲率较大的段(例如,图5b的弯曲段wln23)的与检测点接近的对应点的位置偏差,并且可以设置能够指定更准确的对应点的插补点。
103.(第二实施例)
104.在第一实施例中,补焊程序由检查控制设备3生成。在第二实施例中,说明由机器人控制设备2a执行补焊程序的示例。
105.(焊接系统配置)
106.图6是表示根据第二实施例的检查控制设备3、机器人控制设备2a以及主机设备1的内部配置示例的图。在图6的说明中,对与图2相同的组件标注相同的符号,简化或省略其说明,并且对不同的内容进行说明。根据第二实施例的焊接系统100a的配置与根据第一实施例的焊接系统100的配置(参见图1)相同。
107.作为补焊设备的一个示例的机器人控制设备2a基于从主机设备1发送的主焊执行指令或补焊执行指令控制对应焊接机器人mc1(具体而言,机械手200、送丝设备300、电源设备500)的处理。机器人控制设备2a至少包括通信单元20、处理器21a和存储器22。
108.处理器21a例如由cpu或fpga构成,与存储器22协作执行各种处理和控制。具体而言,处理器21a通过参照存储在存储器22中的程序并执行该程序,来实现主焊或补焊程序生成单元23a、计算单元24、机器人控制单元25、电源控制单元26的功能。
109.主焊或补焊程序生成单元23a使用从主机设备1经由通信单元20发送的主焊执行指令中包括的多个原始工件的工件信息(例如,原始工件的id、名称和焊接部分),从而基于主焊执行指令生成焊接机器人mc1要执行的主焊的主焊程序。当由检查结果确定单元37执行的工件wk(例如焊接工件或补焊工件)的外观检查的结果确定为需要补焊时,主焊或补焊
程序生成单元23a基于生成的主焊程序执行主焊模拟,并且获取虚拟焊线。主焊或补焊程序生成单元23a通过使用通过主焊模拟获取的虚拟焊线、从检查结果确定单元37输出的工件wk(例如焊接工件或补焊工件)的外观检查结果、以及焊接工件或补焊工件的工件信息(例如,表示焊接工件或补焊工件的焊接缺陷的检测点位置的坐标等信息),生成将与缺陷部分的检测点最接近的插补点包括在焊接部分中、并且由焊接机器人mc1执行的工件wk(例如焊接工件或补焊工件)的补焊程序。用于生成补焊程序的步骤的细节与参考图4和图5a在第一实施例中描述的那些相同,因此将省略对其的描述。生成的主焊程序和补焊程序可以存储在处理器21a中,或者可以存储在存储器22的ram中。
110.(焊接系统的操作)
111.接下来,将参考图7描述由根据第二实施例的焊接系统100a执行的主焊和补焊的操作步骤。图7是表示由根据第二实施例的焊接系统100a执行的主焊和补焊的操作步骤的时序图。在图7的描述中,对于使用多个原始工件的主焊和基于焊接工件的外观检查结果不合格的事实执行的补焊的每个过程,将在主机设备1、机器人控制设备2a和检查控制设备3中执行的操作步骤作为示例进行描述。在图7的说明中,对与图3相同的过程赋予相同的步骤编号,简化或省略其说明,对不同的内容进行说明。
112.在图7中,当机器人控制设备2a通过各种已知方法确定焊接机器人mc1执行的主焊完成时,机器人控制设备2a生成表示主焊完成的主焊完成通知,并且将该通知发送到主机设备1(st4)。当主机设备1接收到主焊完成通知时,主机设备1生成焊接工件的外观检查执行指令,并且将外观检查执行指令发送到检查控制设备3(st6)。
113.检查控制设备3基于在步骤st6中发送的外观检查执行指令,使检查设备4对焊接工件执行外观检查(st7)。根据步骤st7的外观检查结果,在焊接工件中存在焊接缺陷部分,因此检查控制设备3确定为需要补焊(st8)。检查控制设备3生成包括步骤st8的确定结果在内的外观检查报告,并且将该外观检查报告发送到机器人控制设备2a(st11a)。检查控制设备3将以同样方式生成的外观检查报告发送到主机设备1(st12)。
114.机器人控制设备2a基于从检查控制设备3发送的外观检查报告和在步骤st3中生成的主焊程序,执行主焊模拟,并且获取主焊的虚拟焊线(st9a)。检查控制设备3在获取的主焊的虚拟焊线上以预定间隔设置插补点,并且生成用于对缺陷部分执行补焊的补焊程序,该缺陷部分包括位于焊线上并且与检测点最接近的对应插补点(对应点)的位置(st10a)。
115.当主机设备1在步骤st12中接收到外观检查报告时,主机设备1生成焊接工件的补焊执行指令,并且将补焊执行指令发送到机器人控制设备2a(st13)。当机器人控制设备2a接收到从主机设备1发送的补焊执行指令时,机器人控制设备2a基于由补焊执行指令指定的焊接工件的补焊程序,使焊接机器人mc1根据补焊程序执行补焊(st14a)。步骤st15之后的处理与图3中的处理相同,因此将省略对其的描述。
116.如上所述,在根据第二实施例的焊接系统100a中,机器人控制设备2a基于外观检查结果生成对多个插补点中位于虚拟焊线wln1上并且与检测点p的位置最接近的插补点(对应点)执行补焊的补焊程序。补焊设备(例如机器人控制设备2a)根据生成的补焊程序,使焊接机器人mc1补焊插补点。由此,补焊设备能够指定位于焊接机器人mc1的主焊时的操作轨迹上并且与外观检查中获取的检测点p最接近的插补点的位置,并且可以经由焊接机
器人mc1以包括该插补点的位置的方式自动且更有效地执行补焊。
117.(第三实施例)
118.在第二实施例中,由机器人控制设备2a生成补焊程序。在第三实施例中,说明由主机设备1a执行补焊程序的示例。
119.(焊接系统配置)
120.图8是表示根据第三实施例的检查控制设备3、机器人控制设备2以及主机设备1a的内部配置示例的图。在图8的说明中,对与图2相同的组件标注相同的符号,简化或省略其说明,并且对不同的内容进行说明。根据第三实施例的焊接系统100b的配置与根据第一实施例的焊接系统100的配置(参见图1)相同。
121.作为补焊设备的一个示例的主机设备1a经由机器人控制设备2对由焊接机器人mc1执行的补焊的执行(例如,补焊的开始和结束)进行统一控制。例如,当主机设备1a从检查控制设备3接收到外观检查报告时,主机设备1a生成补焊程序,生成由焊接机器人mc1所产生的焊接工件的补焊执行指令,并且将补焊程序发送到机器人控制设备2。主机设备1a至少包括通信单元10、处理器11a和存储器12。
122.处理器11a例如由cpu或fpga构成,与存储器12协作执行各种处理和控制。具体而言,处理器11a通过参照存储在存储器12中的程序并且执行该程序来实现单位控制单元13和补焊程序生成单元14的功能。
123.当从检查控制设备3发送的工件wk(例如,焊接工件或补焊工件)的外观检查的结果确定为需要补焊时,补焊程序生成单元14基于从机器人控制设备2发送的主焊程序,执行主焊模拟,并且获取虚拟焊线。补焊程序生成单元14通过使用获取的虚拟焊线、从检查控制设备3发送的工件wk(例如焊接工件或补焊工件)的外观检查结果、焊接工件或补焊工件的工件信息(例如,表示焊接工件或补焊工件的焊接缺陷的检测点位置的坐标等信息),生成由焊接机器人mc1执行的工件wk(例如,焊接工件或补焊工件)的补焊程序。用于生成补焊程序的步骤的细节与参考图4和图5a在第一实施例中描述的那些相同,因此将省略对其的描述。生成的补焊程序可以存储在处理器11a或存储器12的ram中。
124.(焊接系统的操作)
125.接下来,将参考图9描述由根据第三实施例的焊接系统100b执行的主焊和补焊的操作步骤。图9是表示由根据第三实施例的焊接系统100b执行的主焊和补焊的操作步骤的时序图。在图9的描述中,对于使用多个原始工件的主焊和基于焊接工件的外观检查结果不合格的事实执行的补焊的每个过程,将在主机设备1a、机器人控制设备2和检查控制设备3中执行的操作步骤作为示例进行描述。在图9的说明中,对与图3相同的过程赋予相同的步骤编号,简化或省略其说明,对不同的内容进行说明。
126.在图9中,当机器人控制设备2通过各种已知方法确定焊接机器人mc1执行的主焊完成时,机器人控制设备2生成表示主焊完成的主焊完成通知,并且将该通知发送到主机设备1a(st4),并且将用于产生焊接工件的主焊程序发送到主机设备1a(st5b)。当主机设备1a接收到主焊完成通知时,主机设备1a生成焊接工件的外观检查执行指令,并且将外观检查执行指令发送到检查控制设备3(st6)。
127.检查控制设备3基于在步骤st6中发送的外观检查执行指令,使检查设备4对焊接工件执行外观检查(st7)。根据步骤st7的外观检查结果,在焊接工件中存在焊接缺陷部分,
因此检查控制设备3确定为需要补焊(st8)。检查控制设备3生成包括步骤st8的确定结果在内的外观检查报告,并且将该外观检查报告发送到机器人控制设备2(st11b)。检查控制设备3将以同样方式生成的外观检查报告发送到主机设备1a(st12)。
128.主机设备1a基于从检查控制设备3发送的外观检查报告和从机器人控制设备2发送的主焊程序,执行主焊模拟,并且获取主焊的虚拟焊线(st9b)。检查控制设备3在获取的主焊的虚拟焊线上以预定间隔设置插补点,并且生成用于对缺陷部分执行补焊的补焊程序,该缺陷部分包括位于焊线上并且与检测点最接近的对应插补点(对应点)的位置(st10b)。
129.当主机设备1a在步骤st12中接收到外观检查报告时,主机设备1a生成焊接工件的补焊执行指令,并且将补焊程序和生成的补焊执行指令发送到机器人控制设备2(st13b)。当机器人控制设备2接收到从主机设备1a发送的补焊程序和补焊执行指令时,机器人控制设备2基于由补焊执行指令指定的焊接工件的补焊程序,使焊接机器人mc1根据补焊程序执行补焊(st14b)。步骤st15之后的处理与图3中的处理相同,因此将省略对其的描述。
130.如上所述,在根据第三实施例的焊接系统100b中,主机设备1a基于外观检查结果生成用于对多个插补点中位于虚拟焊线wln1上并且与检测点p的位置最接近的插补点(对应点)执行补焊的补焊程序。补焊设备(例如,主机设备1a)根据生成的补焊程序,使焊接机器人mc1对插补点(对应点)执行补焊。由此,补焊设备能够指定位于焊接机器人mc1的主焊时的操作轨迹上并且与外观检查中获取的检测点p最接近的插补点的位置,并且可以经由焊接机器人mc1以包括该插补点的位置的方式自动且更有效地执行补焊。
131.尽管上面参照附图描述了各种实施例,但无需说明的是,本公开不限于这样的示例。对本领域技术人员来说显而易见的是,可以在权利要求的范围内设想各种改变、修改、替换、添加、删除和等同例,应当理解,这样的改动也属于本发明的技术范围。上述各种实施例中的组件可以在不脱离本发明精神的范围内自由组合。
132.本技术基于2019年12月6日提交的日本专利申请no.2019-221598,其内容在此被并入作为参考。
133.工业实用性
134.本发明作为用于自动且更有效地对通过主焊所产生的焊接工件的缺陷部分执行补焊的补焊设备和补焊方法是有用的。
135.附图标记列表
136.1、1a 主机设备
137.2、2a 机器人控制设备
138.3 检查控制设备
139.4 检查设备
140.10、20、30 通信单元
141.11、11a、21、21a、31 处理器
142.12、22、32 存储器
143.13 单位控制单元
144.14、38 补焊程序生成单元
145.23 主焊程序生成单元
146.24 计算单元
147.25 机器人控制单元
148.26 电源控制单元
149.33 检查结果存储单元
150.34 确定阈值存储单元
151.35 形状检测控制单元
152.36 数据处理单元
153.37 检查结果确定单元
154.100、100a、100b 焊接系统
155.200 机械手
156.300 送丝设备
157.301 焊丝
158.400 焊枪
159.500 电源设备
160.mc1 焊接机器人
161.mc1a 主焊机器人
162.mc1b 补焊机器人
163.st 外部存储设备。
再多了解一些
本文用于企业家、创业者技术爱好者查询,结果仅供参考。