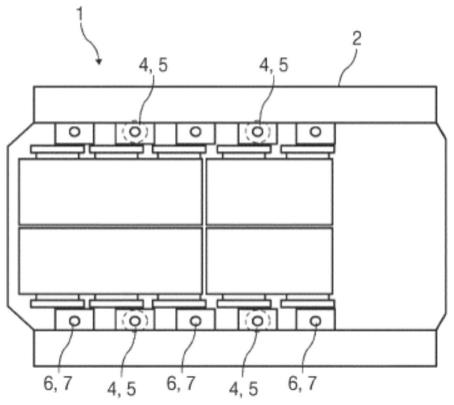
1.本发明涉及一种根据权利要求1的前序部分的用于电池包的颗粒分离器。本发明还涉及一种根据权利要求6的前序部分的具有这种颗粒分离器的电池壳体、一种根据权利要求7的包括这种电池壳体连同封装在其中的电池模块的电池包以及一种根据权利要求9的包括这种电池包的机动车。
背景技术:
2.文献de 10 2013 204 585 a1提出一种例如用在电动车或混动车中的电池包。对于单独电池单元例如因过载或热过载而通过过压机制从其内部释放出气体的脱气情况,在电池包壳体内设有专用自由空间,释放出的气体能卸压至其中且同时可降低其温度和其压力。接着,气体通过过压泄放装置从电池包壳体内被对外释放。气体此时流过设于过压泄放装置中的例如呈旋风分离器或带有纤维复合物或开孔式海绵状结构的表面过滤器形式的颗粒分离器。气体所含的颗粒例如像石墨粉尘在此能在流过颗粒分离器时被滤出,以便降低例如由流出气体内的炽热颗粒引起的爆炸危险。
技术实现要素:
3.本发明基于以下任务,即,指明一种改进的用于电池包的颗粒分离器。本发明还基于以下任务,即,指明一种改进的用于电池包的电池壳体、一种改进的电池包以及一种改进的机动车。
4.根据本发明,该任务关于颗粒分离器通过一种具有权利要求1的特征的颗粒分离器来完成。关于电池壳体、电池包和机动车,该任务通过权利要求6、权利要求7或权利要求9的特征来完成。
5.本发明的有利设计是从属权利要求的主题。
6.一种颗粒分离器设立用于从颗粒-电池气体混合物中分离出固体颗粒,并且具有设立用于通入过压的颗粒-电池气体混合物的入口。该颗粒分离器具有设立用于电池气体卸压的出口。
7.根据本发明,该颗粒分离器具有气体通道,其沿着轴向呈螺旋状盘绕并且将所述入口与出口流体连通。在出口侧端,颗粒分离器具有颗粒排废机构,其在径向上、即在垂直于轴向延伸的方向上打开并设立用于供颗粒经过。
8.有利地,由于将电池气体与颗粒分离开而降低其点燃概率。尤其要防止在一个电池单元热过载时所释放的炽热颗粒例如石墨颗粒或金属颗粒在流出至环境时点燃电池气体。
9.常见的颗粒-电池气体分离器通过加速来分离颗粒-电池气体混合物,其中,因为其惯性较大,故较重的颗粒不如较轻的电池气体快速被排出。在此,颗粒在沿加速路径的任何位点下落。
10.与之相比,所提出的颗粒分离器具有如下优点,即,该颗粒与电池气体一起被引导
经过螺旋形气体通道,并且除了轴向的、在螺旋形气体通道的纵向上指向的线性速度分量外还有角速度分量,其在气体通道的螺旋形状的切向上取向并且对运动的颗粒-电池气体混合物施以离心力。在离心力作用下,较重的颗粒径向向外、即垂直于线性速度分量且垂直于角速度分量来运动并同时径向向内排挤较轻的电池气体。
11.通过颗粒排废机构的径向开口,颗粒在此处流出并且能集中汇集和容放,而电池气体可基本未减速地轴向流出和卸压。有利地,所提出的颗粒分离器的流阻相对于现有技术的解决方案被降低。由此可以实现很高效的在过压下通过颗粒分离器被排出的颗粒-电池气体混合物的卸压。
12.在本发明的一个实施方式中,该气体通道通过设于立管内的蜗杆形成。该蜗杆具有蜗杆螺旋线,其绕轴向的、即在立管纵向上延伸的蜗杆轴盘旋。
13.立管具有径向朝内突出向蜗杆轴的且在纵轴向上盘绕的膛线。该膛线对应于蜗杆螺旋线来盘绕。
14.立管在入口侧用筛板被透气封闭并且在出口侧在出口喇叭口中呈漏斗形扩宽。颗粒排废机构布置为在出口喇叭口区域中在立管周面内的径向缝。
15.借助蜗杆螺旋线和对应盘旋的膛线,可以很简单地形成螺旋形气体通道。蜗杆和立管可设计成能够彼此拆开。由此可以实现简单廉价的制造和安装。此外,借助蜗杆形成螺旋形气体通道提供如下优点,即,立管的很大的净内径可供颗粒-电池气体混合物流通所用,从而实现通过颗粒分离器的很好卸压。
16.在一个实施方式中,该蜗杆螺旋线和膛线在立管周面的内侧分别具有近似三匝。蜗杆螺旋线匝数的增加造成径向加速的增大,进而也造成颗粒与电池气体的改善分离,但在这里,额外匝所达成的改善程度随着变长的蜗杆螺旋线而逐渐减弱。近似三匝的数量被证明是在颗粒分离器的良好分离作用与主要由其轴向长度决定的结构空间要求之间的最佳折中。
17.在一个实施方式中,颗粒排废机构延伸经过蜗杆螺旋线的整个螺旋线高度并且具有径向开口。由此将被径向朝外排挤的颗粒尽量完全甩出和进而达成很高的颗粒分离器分离作用。
18.在一个实施方式中,筛板设立用于拦截具有至少1.5毫米的横截面的颗粒。通过拦截较大的、因此也较重的且惯性较大的颗粒,允许颗粒分离器的较短构型和改善颗粒-电池气体混合物通过。同时,足够大的筛眼允许低的流阻和进而经过颗粒分离器的高效卸压。具有约1.5毫米横截面的筛眼被证明是在出色的分离作用与低流阻之间的良好折中。
19.电池壳体设立用于气密封装至少一个电池模块并且包括具有至少一个设于其中的缺口的绝缘衬(isoliereinlagen),缺口设立用于在高于电池壳体(2)内腔内的预定过压极限值的情况下将该内腔流体连通至其环境。
20.在所述至少一个缺口内设置根据本发明的颗粒分离器。在绝缘衬内留出至少一个分离腔,该分离腔与该至少一个颗粒分离器的颗粒排废机构流体连通。
21.在至少一个电池模块的一个电池单元热过载之后,所形成的颗粒-电池气体混合物在超出预定的过压极限值的情况下通过颗粒分离器被排出。在此,可能仍然炽热的能点燃流出到环境中的电池气体的颗粒通过颗粒排废机构被引导入流动平稳的分离腔。因此,流出的电池气体的点燃概率被显著降低。
22.电池包包括根据本发明的带有本发明颗粒分离器的电池壳体,其中,在电池壳体内封装有至少一个电池模块。通过阻止在热过载情况下流出的电池气体的点燃,可以改善这种电池包的工作安全性。
23.在一个实施方式中,该至少一个电池模块包括至少一个锂离子电池单元。锂离子电池单元具有高能量密度和长使用寿命并且在热过载下排出颗粒-电池气体混合物,其点燃概率可以利用本发明的颗粒分离器被有效降低。
24.另外,提出一种机动车、最好是电动车,其至少有时用这种电池包工作和/或馈电。这种机动车具有很高的工作安全性。尤其是,这样设计的电动车满足与在确定热过载与电池燃烧开始之间的时段相关的现行法律、法规和/或标准安全规则。
附图说明
25.以下结合图来详细解释本发明的实施例,其中:
26.图1示意性示出电池包的横截面,
27.图2示意性示出绝缘衬的入口侧透视图,
28.图3示意性示出绝缘衬的出口侧透视图,
29.图4示意性示出轴向分离器的透视图,
30.图5示意性示出带有立管和蜗杆的拆解的轴向分离器的透视图,
31.图6示意性示出立管的细节透视图,
32.图7示意性示出轴向分离器的出口侧视图,
33.图8示出具有八百颗粒的计算机模拟结果,其中,轴向分离器是倒置的。
具体实施方式
34.彼此对应的部分在所有图中带有相同的附图标记。
35.图1示出具有电池壳体2的电池包1的横截面示意图。电池壳体2是气密构成的。在电池壳体2内部设有电池模块3。
36.在电池包1或电池模块3受损的情况下可能形成电池气体,其为了避免电池包1爆炸应该被可控地散出至环境。电池气体从电池壳体2沿着绝缘衬4排出。
37.绝缘衬4具有以下还将解释的、为将电池气体排出而设立的在电池壳体2内部与其环境之间的缺口5,缺口分别通过保险膜片6和/或膜片阀7被气密封闭。如果电池壳体2内的过压达到预定的极限值,则保险膜片6破裂和/或膜片阀7打开。因此,处于过压的电池气体的卸压可穿过绝缘衬4来实现。
38.图2从电池壳体2的壳体内部的视角示意性示出绝缘衬4的透视图。破裂的保险膜片6或打开的膜片阀7使得电池气体通过轴向分离器100从入口8沿轴向z排出向电池壳体2的外部环境。轴向分离器100布置在穿过绝缘衬4的圆筒形缺口5内。在入口侧,轴向分离器100通过筛板121被封闭。以下还将详细解释筛板121的布置和工作方式。
39.图3从相对的视角、即从电池壳体2的环境看地示意性示出绝缘衬4的透视图。轴向分离器100在出口侧具有扩宽成喇叭状的出口喇叭口111,流出的电池气体经此被排出向环境。
40.在出口喇叭口111中空出一个径向的缝状颗粒排废机构112。颗粒排废机构112设
置用于排出由流出的电池气体所携带的且小到足以穿过入口侧的筛板121的固体颗粒。
41.颗粒如以下还将详细解释的那样在径向y上被引导经过颗粒排废机构112,而电池气体在轴向z上流出。排出的颗粒通过被设计成在颗粒排废机构112与分离腔10之间的流体连通机构的颗粒通道9被引导入在绝缘衬4内留出的分离腔10。
42.图4以外侧透视图示出轴向分离器100。轴向分离器100沿轴向z被电池气体流过,电池气体在电池壳体2的用筛板121封闭的入口侧端流入并在用出口喇叭口111封闭的出口侧端流出。
43.在筛板121与出口喇叭口111之间设有圆筒形的空心立管110,立管内容置有在图4中看不到的蜗杆120。在出口喇叭口111与立管110相接的套口处,在轴向分离器100的周面内留出有颗粒排废机构112。颗粒排废机构112以长缝形式沿轴向分离器100的周面延伸占据从总周长的大致三分之一到六分之一的长度。
44.在颗粒排废机构112的长度范围,出口喇叭口111的外周面回缩,并且比出口喇叭口111的余部更明显地隆起。
45.轴向分离器100最好由轻型的极其耐热耐压的材料制造。在这里尤其考虑酚甲醛树脂例如像pf 1110。
46.图5示出处于拆卸状态的轴向分离器100,即,蜗杆120被取出。在立管110的入口侧端,沿轴向开设一个锁止槽113,其设计成对应于在径向y上从筛板121突出的锁止凸起122。
47.所取出的蜗杆120包括蜗杆螺旋线123,其具有在蜗杆120的纵向上、即在轴向z上延伸的蜗杆轴124。在此,蜗杆螺旋线123具有大致2.5整匝。但也可能的是蜗杆螺旋线123具有其它的匝数。蜗杆螺旋线123最好在大致100-120毫米的轴向伸展范围情况下具有近似三匝。
48.在入口侧端,蜗杆轴124固定连接至与之垂直安置的筛板121。在安装状态下,筛板121的锁止凸起122锁定在立管110的锁止槽113内。蜗杆120和立管110连同颗粒排废机构112由此在安装状态下相对抗转动地固定在一起。
49.在出口侧端,蜗杆轴124在轴向上突出超过蜗杆120。
50.图6从入口侧端、即与出口喇叭口111对置的一端的视图示出立管110。在立管110的内壁上布置螺旋形膛线114。螺旋形膛线114径向向内地从立管110的内壁突出。膛线114的绕匝在方向和螺距上设计为与蜗杆120的蜗杆螺旋线123的匝相同。在锁止的安装位置,即,在筛板121的锁止凸起122卡锁在锁止槽113中时,蜗杆螺旋线123和膛线114在径向y上正好相对。
51.在出口喇叭口111的出口侧端设置圆弧段状的凸片115,其径向朝内突出直至立管110的中心并且收缩成尖。在凸片115的缩成尖的内端设有蜗杆轴承116,蜗杆轴承具有孔,用于容纳蜗杆轴124的出口侧突出端。
52.圆弧段形凸片115的外圆弧连至出口喇叭口111的周面的出口侧端并且在出口喇叭口111的周面上近似延伸占据与颗粒排废机构112一样的角度范围(或周向部)。换言之,颗粒排废机构112和凸片115在轴向z上彼此对准地布置。出口喇叭口111因此在凸片115区域内、即在颗粒排废机构112的出口侧被覆盖。
53.安置在凸片115上的蜗杆轴承116与锁止槽113一起造成蜗杆120在两侧抗旋转地容置于立管110内。凸片115因为对轴向流动施以反向阻力而造成流出的电池气体的在凸片
115和颗粒排废机构112之间的区域内局部升高的流动压力。
54.图7示出具有装接的出口喇叭口111和装入的蜗杆120的立管110的出口侧俯视图。
55.以下将解释轴向分离器100的工作方式。在热过载情况下,电池模块3可能爆裂且同时释放出电池气体和灼热颗粒例如石墨颗粒或金属颗粒,其可能形成可点燃的混合物。所提出的轴向分离器100将颗粒与流出的电池气体分离并因此降低混合物点燃概率。
56.通过筛板121,颗粒-电池气体混合物中的较大颗粒被拦截而未进入轴向分离器100,因此留在电池壳体2内部。筛板121的孔眼尺寸最好被按如下方式选择,即,具有1.5毫米或更大的直径的颗粒被拦截。
57.电池气体和直径小于筛板121的孔眼尺寸的颗粒进入轴向分离器100并通过蜗杆螺旋线123和在立管110边缘处对置的且对应构成的膛线114沿螺旋形轨迹在轴向z上被引导经过轴向分离器100。
58.颗粒-电池气体混合物的螺旋形引导也在筛板121的入口侧造成涡旋。由此,分离出的大颗粒被引导离开筛板121或飘散并且避免筛板121的堵塞。
59.筛板121还可被设计成隆凸状,这帮助沉积于其上的大颗粒被引导离开或飘散。
60.此外,颗粒-电池气体混合物的强制螺旋形流动造成其分解,其中,在离心力的作用下,较重颗粒径向朝外运动,即,运动向立管110的内壁,并且同时径向向内排挤较轻的电池气体,即,朝向蜗杆轴124。径向分解在轴向z上增强并且在出口喇叭口111处以最大程度达成在出口喇叭口111的内壁处流动的颗粒与被排挤入出口喇叭口111内的电池气体之间的分离。
61.沿径向y作用的离心力同时造成颗粒沿径向经缝状颗粒排废机构112流出,如图7示意性所示。颗粒的流出因在颗粒排废机构112处借助凸片115提高的流动压力而得到辅助。
62.排出的颗粒通过颗粒通道9被压迫入分离腔10的流动平稳区域中并汇集在那里。通过这种方式被净化的、仅还具有直径一般在10微米到100微米之间的很小很轻的颗粒的电池气体混合物通过出口喇叭口111被卸压,经过下游的保险膜片6和/或下游的膜片阀7并且被排出至电池壳体2的环境。因为颗粒的炽热时间随其尺寸减小,故还包含的很小很轻的颗粒在流出到环境中时渐熄并且不会再点燃电池气体。
63.事实表明,当电池气体通过本发明的轴向分离器100被引导出电池壳体2时,在例如由金属钉子扎入电池包1引起的电池模块3热过载与电池燃烧之间的时段可被延长。因此,例如在不带本发明颗粒分离器的预测试中确定电池气体在不到五分钟内被颗粒点燃。而在利用本发明的颗粒分离器测试时没有识别到颗粒点燃电池气体。取而代之,电池气体的点燃总是因其它点燃源例如像高压火花放电而在超过5分钟后才发生。因此提供满足法定的规则和标准的更长时段用以警告使用者,例如用这样的电池包1馈电的电动车的乘客。本发明的一个优点因此在于带有所提出的轴向分离器100的电池包1的改善的使用安全性和扩展的应用范围。
64.常见的颗粒-电池气体分离器通过加速来分离颗粒-电池气体混合物,在这里,因较重的颗粒具有较大惯性,与之相比,较轻的电池气体更快速地被排出。在此,颗粒在沿加速路径的任何位置下落。与之相比,本发明的一个优点在于,该颗粒在封装区域、即分离腔10内汇集和最终存放,因此能够轻松防止火焰的出现或传播。
65.为了测试轴向分离器100的有效性,执行计算机模拟。为此采用软件starccm 并且执行3d欧拉-拉格朗日气体-颗粒模拟。
66.在计算机模拟中假定以下边界条件:静态模拟,气体质量流量25g/s,气体入口温度为300℃(最差情况场景),绝热壁温,颗粒初始温度为1000℃,颗粒材料为石墨和nmc(锂-镍-锰-钴氧化物)和铜,颗粒形状为球形。
67.在计算机模拟中获得以下结果:轴向分离器100内的压力降为340毫巴,最大马赫数0.54,对于直径为50-1000微米的颗粒的分离率为100%。
68.图8示意性表明具有八百个颗粒的这种计算机模拟结果。在该图示中示出轴向分离器100的局部。在此,轴向分离器100是倒立的,即,出口喇叭口111靠上布置,其下方是立管110,立管下方是入口8。分离腔10位于其左侧。颗粒的路径以多条线(运动轨迹800)的形式被示出,其示意性表明总共八百个在欧拉-拉格朗日气体-颗粒模拟中模拟的运动轨迹。从图示中能看到颗粒如何以低于3,000m/s的较低速度“从下方”进入轴向分离器100,接着在流过螺旋盘绕的气体通道时在z方向上“向上方”加速到超过12,000m/s,并且最后在y方向上从轴向分离器100离开并进入分离腔10,它们在分离腔内突然减速且最后停止,即,积存。如上已经描述地,对于具有50-1000微米直径的颗粒,分离率为100%。
69.关于轴向分离器100在机动车内的安装位置要注意的是,它可以是任意的,即,轴向分离器原则上可以在机动车内处于任何空间取向。但在此有以下限制,即,在安装位置应该保证积存在分离腔10中的颗粒没有又通过缝状颗粒排废机构112落回至轴向分离器。由此,几乎任何安装位置意味着就机动车内可供使用的狭窄结构空间的灵活充分利用而言的设计自由度的改善。
70.附图标记列表
71.1电池包
72.2电池壳体
73.3电池模块
74.4绝缘衬
75.5缺口
76.6保险膜片
77.7膜片阀
78.8入口
79.9颗粒通道
80.10分离腔
81.100轴向分离器,颗粒分离器
82.110立管
83.111出口喇叭口,出口
84.112颗粒排废机构
85.113锁止槽
86.114膛线
87.115凸片
88.116蜗杆轴承
89.120蜗杆
90.121筛板
91.122锁止凸起
92.123蜗杆螺旋线
93.124蜗杆轴
94.z轴向
95.y径向
再多了解一些
本文用于企业家、创业者技术爱好者查询,结果仅供参考。