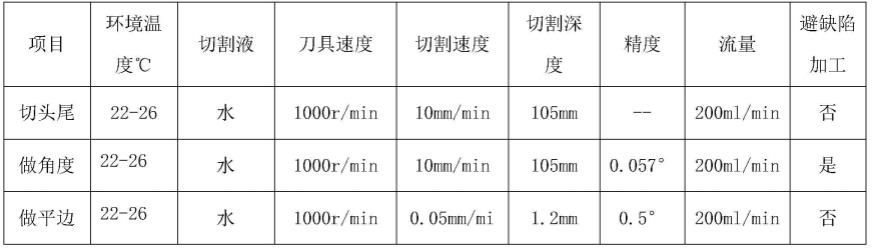
1.本发明涉及一种磷化铟缺陷晶棒分割制备单晶衬底片的方法,属于磷化铟缺陷晶棒的加工技术领域。
背景技术:
2.磷化铟(inp)是重要的
ⅲ‑ⅴ
族化合物半导体材料之一,是继si、gaas之后的新一代电子功能材料。磷化铟具有许多优点,如,直接跃迁型能带结构、高的电光转换效率和电子迁移率、易于制成半绝缘片材料、适合制作高频微波器件和电路、工作温度高、具有强的抗辐射能力、作为太阳能电池材料转换效率高等。这些特征决定了其在固体发光、微波通信、光纤通信、制导/导航、卫星等民用和军事领域的应用十分广阔。
3.磷化铟(inp)因具有电子迁移率高、耐辐射性能好、禁带宽度大等优点,在两大应用领域拥有关键优势:(1)光子领域:波长为1000nm以上的发射和探测能力;(2)射频领域:高频rf应用中的高速和低噪声性能。目前,inp晶圆市场的真正推动力在于光子应用。
4.目前磷化铟主要规格有2寸3寸及4寸规格,晶体主要以4寸晶体生长为主,晶体在现有的加工工艺过程中发现许多孪晶线(twin线)缺陷,此类缺陷切割成衬底片后表面极为细小的一道线,长度在1~100mm不等,甚至有栾晶线贯穿与整个晶棒,且绝大部分栾线带有倾斜角度,孪晶线位置由晶体生产过程而随机产生于晶片的边缘内部或者中心区域,极难发现。传统的加工方法为:切头尾——掏棒——做角度——滚外圆——磨定位边——切片——磨边,由于掏棒位置固定,无法在此基础上进行裁切调整,滚圆后的晶棒进一步缩小,由于晶体内部缺陷表观检测不详,可能掏取的区域含有多晶或者栾晶(twin 线)缺陷,很容易导致误掏或者误判,倾斜的栾晶线也会导致无法做成晶棒导致单晶无法使用或掏取的晶棒切片后也有相当一部分晶片含有小区域内的栾晶线缺陷,导致晶片出现报废现象,也即传统该工艺无法避开缺陷进行加工,因此加工过程中往往会因为缺陷导致晶片产生大量的报废片,这是造成生产成本居高不下在主要原因,为了解决这一问题,发明人研发了一种新的工艺,解决避开栾晶线的切割方法。
技术实现要素:
5.本发明提供一种磷化铟缺陷晶棒分割制备单晶衬底片的方法,通过对方法的改进,可有效避开晶棒缺陷,提升单晶有效利用率,降低成本。
6.为解决上述技术问题,本发明所采用的技术方案如下:
7.一种磷化铟缺陷晶棒分割制备单晶衬底片的方法,包括如下步骤:
8.1)将晶棒头尾切除,将晶棒头部[100]端面按要求做好角度;
[0009]
2)从晶棒头部锯出厚度为0.5~1.5mm样片,用盐酸腐蚀2~5min,水冲、烘干,用显微镜在10x物镜下观察晶胞方向,确定晶胞的[0-1-1]晶向,用平面磨床在晶棒的[0-1-1] 晶向边缘位置磨出5~10mm宽度的of定位平边作为标记;
[0010]
3)将加工好的晶棒在多线切割机上定位切片,切成厚薄均匀的晶片;
[0011]
4)将所有的晶片进行检查,避开缺陷,标出无缺陷合格片的外形,对照步骤2)中的标记,做好解理,得到解理平边;
[0012]
5)将解理平边作为定位边,将标记好的晶片合格区域采用激光划片机进行划片裁切,切成2寸、3寸或4寸毛坯晶片;
[0013]
6)将磷化铟毛坯晶片进行磨边后,得到合格的2寸、3寸或4寸晶片。
[0014]
步骤1)中,按照客户要求做好角度,客户要求的精度范围通常为0.01
°
~0.2
°
左右。
[0015]
步骤2)中,锯样片时,锯片方向垂直与晶棒的高度方向。
[0016]
通过本发明的磷化铟分割制备方法可以有效的避开单晶缺陷。
[0017]
作为常识,[100]面为晶片的表面,of平边就是大边,of平边方向为[0-1-1]方向。
[0018]
本发明设计步骤:切头尾做角度——做定位边标记——切片——避缺陷——划片——磨边,可使得4寸缺陷晶片通过本发明的方法可以得到2寸、3寸或4寸无缺陷衬底片。本发明通过单晶的表面进行评估晶片的有效区域对晶棒进行分割后,取消了掏棒和外圆加工,直接采用多线切割的方式切片,通过有效区位置的测量可避开缺陷,标记好2寸、3 寸或4寸的切割区域,然后按照衬片标记进行解理裁切出of平边,可以完美的避开栾晶 (twin线)缺陷,实现无损单晶的加工。
[0019]
磷化铟多晶或者栾晶(twin线)缺陷在现有工艺中,如下2种情况会导致报废:1) 晶棒缺陷的报废:大角度的倾斜栾晶(twin线)或多条栾晶缺陷,该类缺陷比较多,占比在60%左右的晶体均能出现,该类晶棒无法通过掏棒的方式完全利用有效的区域做出合格的衬底,只能掏取一部分有效区域进行利用。2)晶片缺陷的报废:晶棒加工好外形后,无法调整晶片外形来避开缺陷,切成晶片后部分隐形的栾晶(twin线)或者内部细小的多晶的存在导致晶片报废。本发明则可以利用的含有部分缺陷的单晶,将单晶晶棒有效区域最大化地加工成单晶片。
[0020]
为了进一步提高晶棒利用率,上述步骤1)中,头尾切除时,刀片转速为500~5000r/min,切割速度1~20mm/min,切割深度为50~120mm,水的流量为100~600ml/min。头尾切除时,对温度不做要求。
[0021]
为了进一步提高晶棒利用率,步骤1)中,做角度时,环境温度为15~28℃,刀片转速为500~5000r/min,切割速度1~20mm/min,切割深度为50~120mm,切割精度为 0.01~0.5
°
,水的流量为100~600ml/min。
[0022]
为了进一步提高晶棒利用率,步骤2)中,做标记时,环境温度为15~28℃,刀片转速为500~5000r/min,切割速度0.01~0.1mm/min,切割深度为0.1~2mm,切割精度为 0.1~0.5
°
,水的流量为100~600ml/min。
[0023]
为了进一步提高效率,步骤3)中,切片时,环境温度为20~26℃,碳化硅粉及切割液的质量比为(1.1~2):1,刀片转速为200~1000r/min,切割速度1~10mm/min,切割深度为50~120mm,切割精度为0.01~0.5
°
,切割液的流量为300~3000ml/min。
[0024]
为了进一步提高产品质量,步骤4)中,解理时,环境温度为15~28℃,刀片转速为 1~5r/min,切割速度1~50次/min,切割深度为0.1~1mm。
[0025]
为了进一步兼顾效率和质量,步骤5)中,激光划片时,激光瞬间温度较高,环境温度过低会引起晶片炸开破裂,环境温度设定为20~26℃,频率为20~100hz,切割速度 10~
500次/min,切割深度为0.3~1mm。
[0026]
为了方便控制,同时确保磨边效果,步骤6)中,磨边时,环境温度为15~28℃,刀片转速为500~5000r/min,切割速度1~10mm/min,切割深度为0.2~2mm,切割精度为 0.01~0.5
°
,水的流量为100~1000ml/min。
[0027]
本发明磷化铟缺陷晶棒分割制备单晶衬底片的方法,通过单晶的表面进行评估晶片的有效区域对晶棒进行分割后,取消了掏棒和外圆加工,采用直接多线切割的方式切片,然后的衬片进行有效标记裁切,通过标记位置采用激光划片的方法得到一个毛坯片,然后通过磨边方式得到磷化铟晶片的成品,可以完美地避开栾晶(twin线)缺陷,实现无损单晶的加工。
[0028]
本发明未提及的技术均参照现有技术。
[0029]
本发明磷化铟缺陷晶棒分割制备单晶衬底片的方法,在现有工艺基础上减少了掏棒及外圆加工步骤,引进了分选查片、标记裁切、激光划片新技术工艺路线,相比传统的加工工艺,具有如下有益效果:1、通过切割后的晶片分选可以合理的利用每一个片的有效区域,提升了单晶的利用率,避免了掏棒、定性后,切片的缺陷无法避开的问题,降低了不可控因素的风险;2、该方法比较灵活,可以依据不同的有效区域分别筛选划片,减少了晶片报废的现象,因为晶片尺寸越大其价值约高,3寸要大于2寸的价值,依据缺陷的位置进行分选出可以加工2寸或3寸的晶片,提升了单片价值;3、并采用了目前技术比较成熟的激光切割技术,激光切割的切缝隙在0.1mm左右,相比掏棒的1.5mm的损耗要节省约94%的材料损耗,比较省时省料;4、显著提高了晶向角度质量。
附图说明
[0030]
图1为vgf生产的晶体栾晶(twin线)缺陷晶体样本示意图;
[0031]
图2为将图1的晶棒进行“切头尾做角度——做定位边标记——切片”的加工步骤示意图;
[0032]
图3为将图2得到的切片进行“避缺陷——划片——磨边”的加工步骤示意图;
[0033]
图4为晶片示意图,1为[100]方向晶片表面,2为of平边[0-1-1]方向(定位边), 3为if平边[0-11]方向(小边);
具体实施方式
[0034]
为了更好地理解本发明,下面结合实施例进一步阐明本发明的内容,但本发明的内容不仅仅局限于下面的实施例。
[0035]
实施例1
[0036]
拿比较常见的栾晶twin线缺陷举例:由于twin线的倾斜贯穿,传统的掏棒工艺已经不适合该类缺陷磷化铟的加工生产,如图1所示,晶棒为圆形毛坯,高度(长度)约100mm 左右,直径为103~105mm的4寸规格,有两道三条栾晶(twin线),传统的加工方式由锥部垂直掏棒来制备2寸(3寸)规格,由于角度面要求,无法完全避开缺陷,导致单晶不能得到很好的利用,本例采用如下方法进行分割制备单晶衬底片:
[0037]
1)将晶棒头尾切除后晶棒长度为72mm,检查端面切割面是否有缺陷,将[100]端面的完整区域在x射线上进行定向,定向精度控制在0.03
°
,采用mb ts206内圆锯切割速度控
制在15mm/min进行切平,做角度0.07
±
0.05
°
,做角度正晶向31
°
39
′
45
″
,111 偏晶向31
°
44
′
05
″
,晶向0.07
°
切除头尾无效区域后做角度完成晶棒长度为68mm;
[0038]
2)在晶棒的头部[100]方向采用mb ts206内圆锯出一小片厚度为0.8mm样片,用盐酸(质量浓度为35%的盐酸与水混合而成)腐蚀5min,水冲2min,烘干,用显微镜在10x 物镜下观察晶胞方向,可观察到晶胞方向一面横向垂直一面横向平行,确定晶胞的[0-1-1] 晶向为of定位平边,用平面磨床在晶棒的[0-1-1]晶向边缘位置磨出12mm宽度作为of 定位平边作为标记;
[0039]
3)将加工好的晶棒采用ab胶粘胶在晶拖上固化,在高鸟610sd多线切片机上调整 (100)面在0.01
°
~0.5
°
范围内,多线切割成厚度为480μm的晶片,泥浆配置为六合盖普粉体有限公司1500目碳化硅粉及切割液(型号jx-8a,陕西省石油化工研究院)按照质量比1.5:1的比例配置,切片完成后脱胶清洗表面,得到480μm厚度的113片晶片,通过取样测试得到数据如下;
[0040]
片号bowwarpttvtirltirltv10.83217.7452.9192.1280.8271.22120-2.11319.7882.9152.6031.4270.869
[0041]
4)检查晶片表面缺陷位置进行标记,避开缺陷,标出无缺陷合格片的外形,用金刚笔在(0-1-1)标记位置避开缺陷在边缘划出2~4mm的缺口,沿着缺口掰开得到一个解理平边,标记3寸片36片,2寸片77片;
[0042]
5)将解理平边作为定位边,避开缺陷的2寸标记位置,采用科翰龙激光划片机按照步骤4)画出的外形进行划片裁切,划片裁切时预留好0.2~2mm加工余量;
[0043]
6)将磷化铟毛坯晶片测量直径在合格范围,在wgm4200磨边机上,采用 r0.1~r0.5mm的成型砂轮槽将边型磨成成品,共得到77片2寸晶片,36片3寸晶片,并采用丹东新东方晶体仪器有限公司生产的x射线定向仪抽测角度测量精度较好,2寸of 平边测得21
°
45
′
36
″
角度,if(0-11)测得:21
°
43
′
34
″
比较正常,测得3寸of平边晶向31
°
45
′
42
″
,if(0-11)测得:21
°
44
′
12
″
在范围内。
[0044][0045]
实施例1中各步骤参数
[0046]
[0047][0048]
通过本方案的调整,将掏棒滚圆工艺去除后,增加分选及避开缺陷,引进激光切割技术,避开缺陷进行划片,通过避开缺陷的分选方法可以避开缺陷位置,划出合格片,提升了晶片合格率;激光切割的切缝隙在0.1mm左右,相比掏棒的1.5mm的损耗要节省约94%的材料损耗。
[0049]
对比例1
[0050]
采用现有方法加工有缺陷的晶棒,晶棒为圆形毛坯,高度(长度)约100mm左右,直径为103~105mm的4寸规格,有两道三条栾晶(twin线),缺陷与实施例1中相似,加工步骤包括:切头尾、掏棒、做角度、滚外圆、磨定位边、切片和磨边,掏棒和滚外圆按照常规方法进行即可,其余步骤的参数要求,参照实施例1。
[0051]
实施例1和对比例1产出的合格率对比:
[0052]
加工方法晶棒编号晶棒长度产出片2寸片3寸片缺陷片成品率实施例1if20032-16811377360100.00%对比例1is20023651084905945.37%
[0053]
实施例1和对比例1的精度对比
[0054][0055]
晶片of平边≤0.05
°
为高精度晶向,由上表可明显看出,本技术显著提升了晶向角度质量。
[0056]
对比例2
[0057]
只将激光划片的环境温度提升至30-35℃,其余均参照实施例1,共得到75片2寸晶片,36片3寸晶片。
[0058]
对比例3
[0059]
只将激光划片的环境温度降低至10-15℃,其余均参照实施例1,共得到64片2寸晶片,33片3寸晶片。
再多了解一些
本文用于创业者技术爱好者查询,仅供学习研究,如用于商业用途,请联系技术所有人。