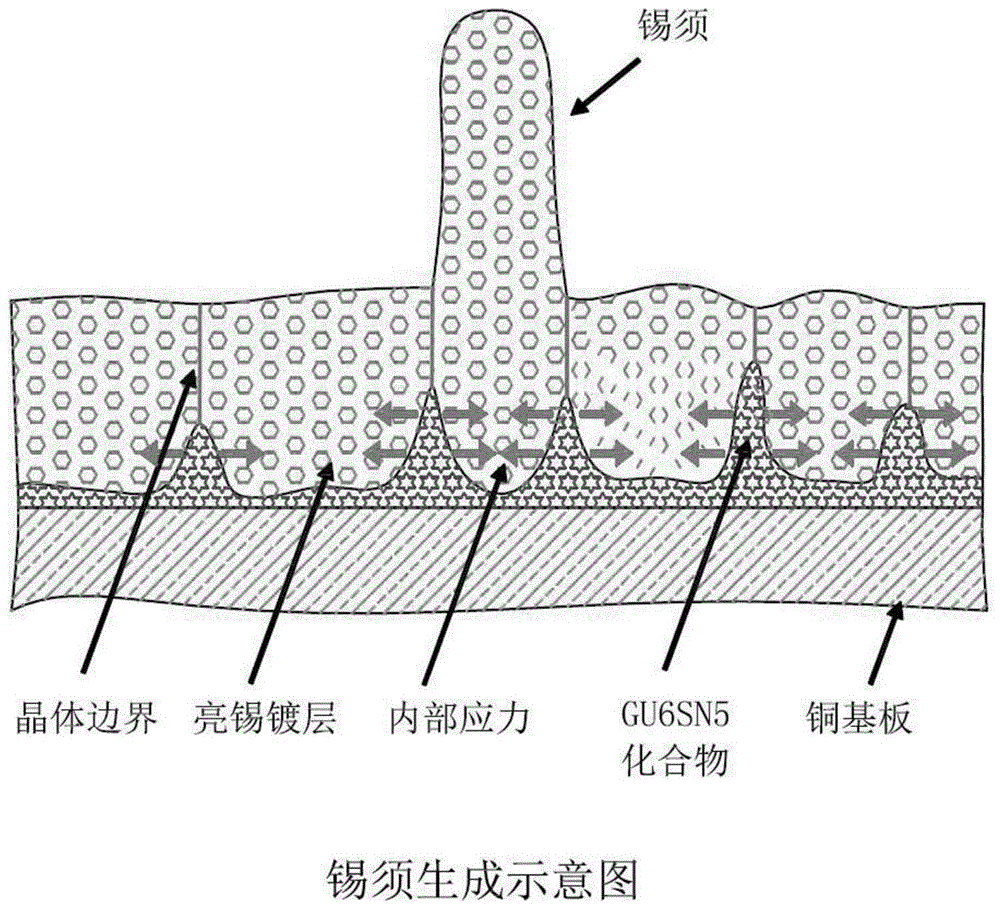
本发明属于薄膜电容器技术领域,具体涉及一种抑制汽车薄膜电容器电镀铜排锡须的方法。
背景技术:
锡须是电子产品及设备中一种常见的现象。晶须是一种头发状的晶体,它能从固体表面自然的生长出来,也称为“固有晶须”。晶须在很多金属上生长,最常见的是在锡、镉、锌、锑、铟等金属上生长。锡须会造成电子产品短路、绝缘耐压降低,从而导致产品失效,是需要避免和抑制。
在铜表面镀锡,在某种条件下会形成cu6sn5化合物,cu6sn5化合物的体积大于铜金属和金属体积,形成众多的晶体边界,该边界如“楔形”,造成了化合物从表面向外扩展形成锡须;另外镀槽中的杂质和其他缺陷也可能会增加晶须形成的可能性,尤其碳使锡膜应力越来越大,为锡须形成创造了条件;同时应用在高湿度环境中,锡层表面形成氧化膜,产生应压力,使锡分子沿着晶体边缘进行扩散,产生了点阵缺陷,这种点阵缺陷导致锡分子扩散过程中在螺旋位错处形成了锡须,尤其是凝结和腐蚀使杂质分离与水蒸汽凝结一起,产生非均匀的氧化物,在锡薄膜表面施加额外的差分应力,加速了锡须的生长。
现有抑制电容器铜排锡须的方法主要有3种:第1种方法是电镀锡合金法,如采用共沉积法形成锡铅合金、锡银合金、锡金合金等,利用合金分子比锡分子重的原理,形成合金阻隔层,在无铅工艺大规模使用之前是抑制锡须的主要方法,但因为环保和成本因素,该方法已逐渐淘汰;第2种方法是电镀亮锡时对化学浸锡镀液的改良,如酸性镀液采用甲基磺酸与硫酸的混合溶液、锡盐采用烷基磺酸锡盐与过氧化氢的混合溶液、且添加了抗氧化剂、辅助剂、光亮剂、湿润剂、表面活性剂等成分,该方法优点是镀锡层的柔韧性和延展性好,缓解了镀锡层表面裂纹,但抑制锡须效果不明显;第3种方法是镀锡后热处理,如大于150℃且大于5分钟的退火工艺或180℃-190℃的红外线加热工艺,都可以减少镀锡层内的机械应力、化学应力和热应力,减缓锡须的生长。第2种方法和第3种方法因无法阻止cu6sn5化合物的生产,所以无法从根本上解决锡须问题。
技术实现要素:
本发明针对上述缺陷,提供一种通过增加镀镍阻挡镀层,并且选择雾锡电镀的方法得到具有镀镍的阻挡层和雾锡镀层的抑制汽车薄膜电容器电镀铜排出现锡须的方法。
本发明提供如下技术方案:一种抑制汽车薄膜电容器电镀铜排锡须的方法,包括以下步骤:
s1:将电容器铜排置于加热的氢氧化钠溶液中,通入直流电,去除铜排表面的油污,然后采用蒸馏水清洗;
s2:将所述s1步骤处理后的铜排置于硫酸溶液中,通入直流电流进行酸洗,使硫酸溶液发生电解,产生的氢气和氧气使铜排表面的氧化物爆裂疏松、机械剥离,硫酸对铜排表面的氧化层进行溶解,然后再用蒸馏水清洗;
s3:将所述s2步骤处理后的铜排进行电镀,以镍板作为阳极,以甲基磺酸为主盐,以三价铬蓝白钝化剂dm-310为添加剂的电镀液,于0.5-2.5a.dm2的电流密度下进行电镀;电镀完成后,采用蒸馏水清洗并吹干;
s4:将纯硫酸和纯水按1:2配成浓度为2.5g/l-25g/l的硫酸溶液,在50-60℃温度下,加入snso4,防止snso4水解,待冷却后,加入作为有机添加剂的4#亚锡水,形成雾锡镀层电镀液;
s5:将经过所述步骤s3处理过的铜排置于所述步骤s4得到的雾锡镀层电镀液中于常温密闭环境下,以1-1.25a.dm2的电流密度进行雾锡镀层电镀,然后采用蒸馏水清洗并烘干,得到由上至下依次具有雾锡镀层和大于0.5μm的镀镍的阻挡层的电容器铜排,以抑制汽车薄膜电容器电镀铜排出现锡须。
进一步地,所述s1步骤中的氢氧化钠溶液温度为50-60℃。
进一步地,所述s1步骤中的氢氧化钠溶液浓度为60-120g/l。
进一步地,所述s1步骤中通入4-5v的直流电。
进一步地,所述s2步骤中的硫酸溶液浓度为120-150g/l。
进一步地,所述s2步骤中通入4-5v的直流电。
进一步地,所述s3步骤中所配置得到的电镀用溶液中甲基磺酸的浓度为100-150g/l。
进一步地,所述s5步骤中得到的雾锡镀层电镀液中硫酸的浓度为140-180g/l,snso4的浓度为15-30g/l,所述4#亚锡水的浓度为8~10ml/l。
进一步地,所述s5步骤中的雾锡镀层电镀液随着电镀的进行,补加纯硫酸和作为有机添加剂的4#亚锡水,4#亚锡水的补加通过滴定硫酸含量决定:每添加1份体积的h2so4须添加0.1份体积的4#亚锡水。
进一步地,所述阻挡层的厚度为2-3μm,所述雾锡镀层厚度为8-12μm。
本发明的有益效果为:
1、本发明提供的抑制汽车薄膜电容器电镀铜排出现锡须的方法,增加镀镍层作为阻挡层,利用其空穴率低的特点,可以有效阻止铜分子扩散到锡分子,进而可以减少如图1所示的锡与铜形成cu6sn5化合物,另基于锡与镍分子形成ni3sn4速度比锡与铜之间形成cu6sn5慢很多,所以通过镀锡形成雾锡镀层和铜基体金属之间的阻挡层,可以阻止铜扩散到锡中。
2、本发明提供的抑制汽车额薄膜电容器电镀铜排选择雾锡电镀,基于锡层因晶体间空位或空隙而出现内部应力,其中亮锡因光亮成分残留,在电流密度过高、操作温度过低时会产生锡须,而雾锡有机物或碳含量少(约为亮锡的1/20),微晶颗粒较大,约为1-5um,大颗粒晶粒之间致密度高,为铜扩散提供较少的间隙,压应力较低或未零,可以抑制锡须的生长。
3、本发明提供的抑制汽车薄膜电容器电镀铜排出现锡须的方法,在铜排基体与雾锡镀层之间形成的镀镍的阻挡层延展性高,不会受内部应力出现裂纹。
附图说明
在下文中将基于实施例并参考附图来对本发明进行更详细的描述。其中:
图1为现有技术中在同表面镀锡时表面出现的锡须示意图。
图2为本发明提供的一种抑制汽车薄膜电容器电镀铜排锡须的方法得到的汽车薄膜电容器电镀铜排表层电镀层结构图。
具体实施例方式
下面将结合本发明实施例中的附图,对本发明实施例中的技术方案进行清楚、完整地描述,显然,所描述的实施例仅仅是本发明一部分实施例,而不是全部的实施例。基于本发明中的实施例,本领域普通技术人员在没有做出创造性劳动前提下所获得的所有其他实施例,都属于本发明保护的范围。
本发明提供的一种抑制汽车薄膜电容器电镀铜排锡须的方法,包括以下步骤:
s1:将电容器铜排置于50-60℃、浓度为60-120g/l的氢氧化钠溶液中,通入4-5v的直流电,去除铜排表面的油污,然后采用蒸馏水清洗;
s2:将所述s1步骤处理后的铜排置于120-150g/l的硫酸溶液中,通入4-5v的直流电进行酸洗,使硫酸溶液发生电解,产生的氢气和氧气使铜排表面的氧化物爆裂疏松、机械剥离,硫酸对铜排表面的氧化层进行溶解,然后再用蒸馏水清洗;
s3:将所述s2步骤处理后的铜排进行电镀,以镍板作为阳极,以浓度为100-150g/l的甲基磺酸为主盐,以三价铬蓝白钝化剂dm-310为添加剂的电镀液,进行电镀;电镀完成后,采用蒸馏水清洗并吹干;
s4:将纯硫酸和纯水按1:2配成浓度为2.5g/l-25g/l的硫酸溶液,在50-60℃温度下,加入snso4,防止snso4水解,待冷却后,加入作为有机添加剂的4#亚锡水,形成雾锡镀层电镀液,得到的雾锡镀层电镀液中硫酸的浓度为140-180g/l,snso4的浓度为15-30g/l,所述4#亚锡水的浓度为8~10ml/l;
s5:将经过所述步骤s3处理过的铜排置于所述步骤s4得到的雾锡镀层电镀液中于常温密闭环境下,以以1-1.25a.dm2的电流密度进行雾锡镀层电镀,然后采用蒸馏水清洗并烘干,得到如图2所示的,由上至下依次具有厚度为8-12μm的雾锡镀层和大于0.5μm的镀镍的阻挡层的电容器铜排,以抑制汽车薄膜电容器电镀铜排出现如图1所示的锡须,在图2中镀镍层即为镀镍的阻挡层,铜基板即为进行抑制锡须处理的对象—汽车薄膜电容器铜排。
优选地,阻挡层的厚度为2-3μm。
s5步骤中,雾锡的添加剂成分少,柔软性好,脆性小,但电镀时镀覆时间长,镀层发暗,抗指纹能力较差,进而其在封闭环境下进行,封闭是在高温条件,封闭剂渗入镀锡层的微孔内,并在镀层表面形成一层有机分子膜,将整个镀层封闭。封闭后的镀锡层稍微发白,具有疏水功能,能抗指纹,不易受到污染,不影响电性能,不影响焊接性能等优点,改善其抗污染性能和耐高温焊接性能;可常温操作,但夏季由于温度高,以及电镀过程中会产生热量,加速sn2的氧化,导致镀液恶化,因此也应该配置冷冻机组,使温度保持在30℃以下。
本发明提供的抑制锡须方法中,雾锡镀层电镀液采用snso4作为镀液中的主盐,限定其浓度为15-30g/l,否则含量过高会降低镀液的分散能力,并使镀层结晶粗糙:含量过低时,工作电流密度减小,影响沉积速度;硫酸的作用是提高镀液的导电能力,防止sn2水解和氧化,保持镀液稳定,还能加速阳极溶解,限定其浓度为140-180g/l,在工艺范围内变动,不会给产品质量造成明显的影响,但过高时,阴极电流效率会降低,阴极上析氢增多,镀件上容易出现黑色气流条纹;
4#亚锡水作为雾锡镀层电镀液中唯一的有机添加剂(含有锡盐稳定剂和结晶细化剂),限定其浓度为8~10ml/l,否则含量不足时,镀层结晶粗糙,镀液的分散能力降低;过量时,容易出现水印、花斑。
s5步骤电镀完毕处理后,同光亮镀锡一样,采用相对分子质量大的聚丙烯酰胺沉淀,也可用市售的sy.800酸性镀锡处理剂进行处理,进行无害化处理。
上述制备方法中的加入的各化学原料重量份、各溶液浓度以及电镀所需要的直流电流强度、以及工艺条件所需要的温度条件可以根据实际所需要达到的抑制锡须的效果而在上述限定范围内进行选择,得到的镀镍的阻挡层和雾锡镀层的厚度进而也随着上述条件的变化而在限定范围内随之改变。
研究表明,大于20um的镀锡层可以减少镀层和铜材之间的相互应力,抑制锡须的生成,但镀层太厚,不能通过盐雾试验。
理论上镀镍层厚度需要≥0.5um,镀层厚度越厚,越有利于抑制锡须,如zhang[1]等报导(schettyr.minimizationoftinwhiskerformationforlead.freeelectronicsfinishing【c]//proceedingsofipcworksconference.[s.j.】:【s.n.】,2000:s·02-2一l—s-02—2—9)在铜基材上引入1.5um厚的镍镀层可以有效地减少在低应力镀锡层上锡须的生长,需要平衡的是镀层太厚,附着力降低,薄膜电容器母排跟芯子焊接困难,经过实际验证,选择镀镍层厚度为2-3um。
电子封装行业镀锡层厚度一般选择(9±3)um,连接器件或有较大面积的散热片器件,镀镍层厚度一般选择(15±3)um,汽车薄膜电容器母排经过综合评估,选择镀锡层厚度为8-12um。
测试例
采用本发明提供的抑制汽车薄膜电容器电镀铜排出现锡须的方法得到的电容器铜排,进行盐雾试验、老化试验和可焊性试验验证其抑制锡须的效果。具体参见如下步骤:
1、盐雾试验
按照gb/t2423.17-2008进行盐雾试验。测试条件/方法:将试验品放置于35℃±2℃;ph值6.5~7.2的盐雾箱,连续试验时间48小时,过程中喷雾不得中断。验收标准:要求搭接面到7级(要求搭接面的破坏面积满足0.25%<a≤0.5%)。
2、老化试验
按照iec60068-2-14方法进行老化试验,测试条件/方法:在-40℃恒温试验存储1000小时。验收标准:目视无锡须,镀层外观无明显变化。
3、可焊性试验
采用润湿称重法,测试条件/方法:温度235℃,深度2.0mm,速度20mm/s,时间t≤3s,t2≤5s,试样直径为0.95mm。
验收标准:润湿时间≥0.3s,零交时间≥0.3s,t1润湿力≥0.75mn,t2润湿力≥0.75mn,t(fmax2/3)≥0.25mn。
以上试验的具体条件、验收标准和结果见下表所示。
以上各实施例仅用以说明本发明的技术方案,而非对其限制;尽管参照前述各实施例对本发明进行了详细的说明,本领域的普通技术人员应当理解:其依然可以对前述各实施例所记载的技术方案进行修改,或者对其中部分或者全部技术特征进行等同替换;而这些修改或者替换,并不使相应技术方案的本质脱离本发明各实施例技术方案的范围。
此外,本领域的技术人员能够理解,尽管在此的一些实施例包括其它实施例中所包括的某些特征而不是其它特征,但是不同实施例的特征的组合意味着处于本发明的范围之内并且形成不同的实施例。例如,在上面的权利要求书中,所要求保护的实施例的任意之一都可以以任意的组合方式来使用。公开于该背景技术部分的信息仅仅旨在加深对本发明的总体背景技术的理解,而不应当被视为承认或以任何形式暗示该信息构成已为本领域技术人员所公知的现有技术。
本文用于企业家、创业者技术爱好者查询,结果仅供参考。