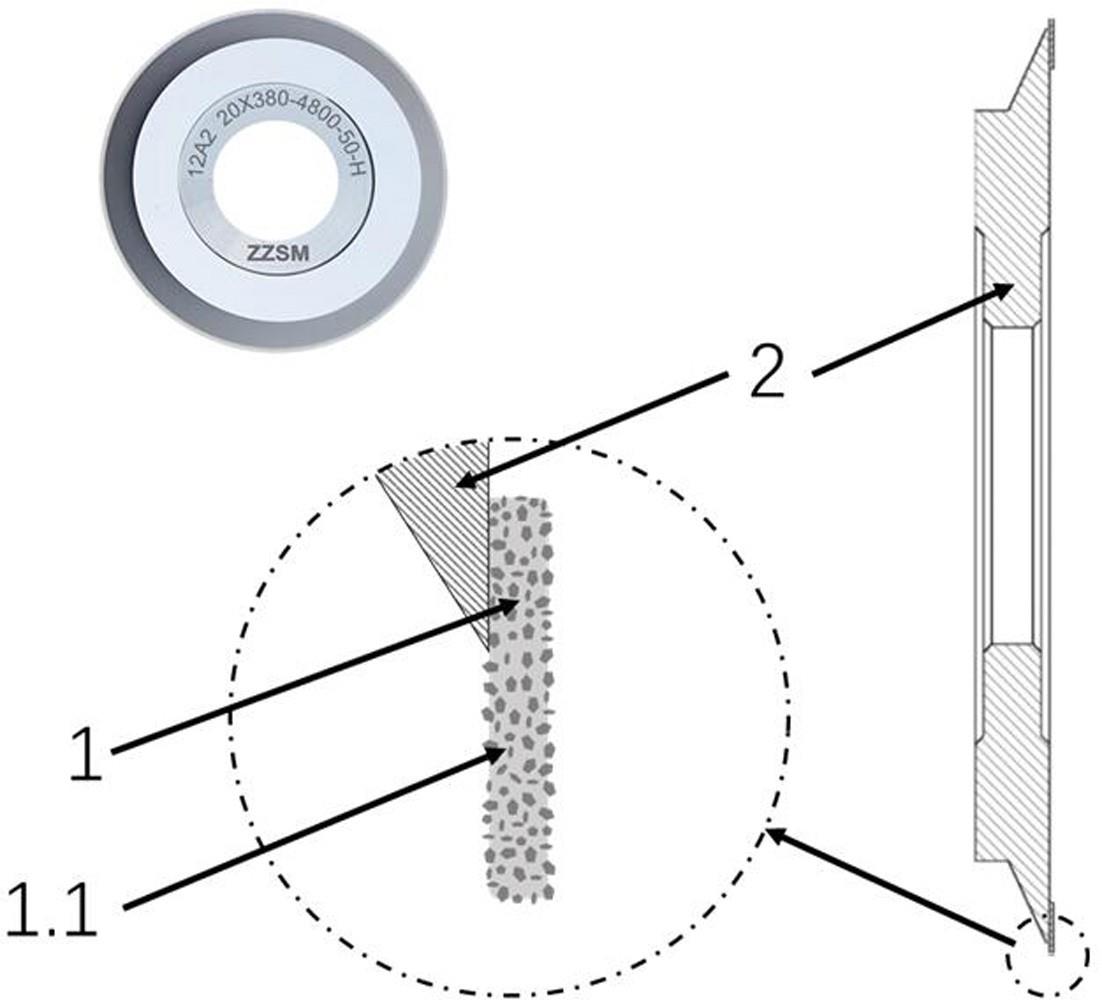
一种超薄ic晶圆专用划片刀及其制作方法
技术领域
1.本发明属于半导体芯片加工制造技术领域,具体涉及一种超薄ic晶圆专用划片刀及其制作方法。
背景技术:
2.随着手机、电脑、汽车电子等产品对ic晶圆芯片需求的日益增加,半导体行业近年来处在高速发展阶段。ic晶圆划切属于半导体制造封测阶段关键工序,划切工序中划片机带动划片刀高速转动对晶圆进行划切,完成晶圆上ic芯片阵列的相互分离。
3.随着ic芯片尺寸的小型化,芯片厚度逐渐变薄,特别是存储类型的ic芯片,其晶圆的厚度通常在50~100μm之间。这类超薄晶圆极容易发生裂片,因此通常在这类晶圆背面贴上daf膜(die attach film,晶片黏结薄膜),来减少裂片发生概率。但daf膜在划切过程中会产生高延展性碎屑,造成划片刀刀刃变钝,极易造成背崩、背裂、侧崩等,给超薄晶圆的划片加工造成困难,最终导致ic晶圆上批量芯片报废。
4.因此有必要针对超薄ic晶圆的特点,以及划片刀导致薄晶圆背崩、背裂、侧崩等根本问题,展开深入划切机理层面的研究,以开发超薄ic晶圆专用划片刀。
5.公开号为cn113172781a的发明专利公开了一种超薄晶圆的划切方法,该方法基于常规划片刀和划片机,巧妙改进切割工艺参数,调整切割道顺序,可以明显改善裂片和背崩。但这种方法没有针对划片刀产生背崩、裂片的根本原因,而是采用参数调整进行改善,属于治标不治本,而且切割程序较为复杂,效率偏低。在针对含有daf膜的ic晶圆时,不能改善这类材料对刀尖磨料的粘附,因此背崩和背裂的改善效果也很有限。
6.公开号为cn110216598a的发明专利公开了一种半导体用划片刀及其加工工艺,提出在铝轮毂上开槽,调整电镀刀刃过程中高低电位的平衡,来提高刀刃内外侧的厚度一致性。公开号为cn20497264u的实用新型专利提出一种新型超薄晶圆划片刀,采用和专利(公开号cn110216598a)近似的技术,通过保证刀刃厚度的内外一致,进而实现超薄刀刃制造。这类做法可以明显增加刀刃长度,提高刀刃可使用寿命,但对划片刀的背崩性能,特别是含有daf膜的超薄ic晶圆的背崩、背裂、侧崩等没有改善作用。
7.公开号为cn204604125u的实用新型专利、以及专利(公开号cn112621143a)和专利(公开号cn113172781a)公开了晶圆划片刀的常规制作方法,并没有针对含有daf膜的超薄ic晶圆的苛刻划切工艺做出任何针对性的改进,因此以上专利公开的划切方法难以实现很好的超薄ic晶圆切割性能。
8.公开号为cn108130583a的发明专利提出一种超薄划片刀的电镀液配方,可以实现刀刃厚度可以达到20~30μm,切割大晶片合格率较高,切割超薄ic晶圆缝宽约30μm,缝宽略大,但是无法保证背崩和侧崩等指标有较好效果。同样的,公开号为cn 113215641 a的发明专利公开了一种划片刀电镀液及其制备方法,并公开了含有镍盐和钴盐的电镀液成分,电镀后所得到刀刃的结合剂为镍钴合金,具有更好的厚度一致性和更高的寿命。但未提及背崩性能,特别是超薄ic晶圆这种极端工况下,背崩、侧崩、背裂等性能无法保证。
9.基于现有技术中存在的问题,本发明提出一种超薄ic晶圆专用划片刀,通过对金刚石微粉粒度及镍基结合剂配方进行设计,同时对金刚石浓度、划片刀厚度精度、刀刃长度进行精准控制,以期实现提高划片刀刀刃刚度,保证良好的刀刃自锐性,防止由于daf等延展性强材料对刀尖磨料粘附,而导致背裂的发生。
技术实现要素:
10.本发明目的是提供一种超薄ic晶圆专用划片刀,能够改善50~100μm厚度范围的超薄ic硅晶圆的切割质量,减少常规刀片切割时典型的背崩、侧崩、背裂的发生,进而提升晶圆划切良率和加工效率。
11.本发明还提供了所述超薄ic晶圆专用划片刀的制作方法。
12.为了实现上述目的,本发明采用以下技术方案:一种超薄ic晶圆专用划片刀,由基体和镀覆在基体表面的复合镀层构成,其中复合镀层由电镀镍结合剂和金刚石磨料组成;复合镀层的厚度为13~16μm。
13.具体的,所述基体为铝基体。
14.具体的,所述超薄ic晶圆专用划片刀采用电镀工艺在基体上镀覆复合镀层。
15.具体的,复合镀层伸出基体之外的部分为刀刃,构成划片刀的工作部分,刀刃长度为380~440μm,刀刃的长厚比为(24~34):1。
16.具体的,金刚石磨料在复合镀层中均匀分布,所述金刚石磨料为4800目金刚石微粉;金刚石微粉的颗粒等效粒径中值d50为1.67μm;所述金刚石磨料选用多棱角型晶型。
17.具体的,为了具备较好的防背崩性能,金刚石磨料在复合镀层中体积占比为10.1%~15.2%。
18.上述超薄ic晶圆专用划片刀的制作方法,以铝基体为例,包括铝基体加工、电镀、磨外圆、铝腐蚀出刃、电解抛光等工序,具体步骤如下:(1)铝基体加工将铝棒车断,再经过粗加工和精加工,制成外径56mm、内孔径19.054mm的碟形铝基体;其中铝基体的大端面用于电镀沉积含有金刚石磨料的复合镀层,铝基体的大端面平面精度要求在1μm以内;(2)电镀将加工好的铝基体用夹具进行组装,并对铝基体上不需电镀区域用密封垫进行遮挡;组装后进行除油清洗,之后放入电镀槽,在包含电镀液 4800目金刚石磨料的混合液中进行电镀;电镀液的成分包括镍盐和硼酸,其中,镍盐为硫酸镍或氨基磺酸镍,电镀液ph为4.2~4.8;(3)磨外圆磨外圆工序是在铝基体半径方向去除20μm厚度的材料;磨外圆工序可去除电镀过程导致镀层外圆处不均匀部分,同时可将刀刃外圆进行加工提高圆度、以及减小刀刃外圆相对于基体内孔的偏心量;(4)铝腐蚀出刃铝腐蚀出刃工序采用强碱溶液,同时控制碱溶液浓度、温度及铝腐蚀时间,将与镀层边缘接触的铝基体进行溶解去除,同时不对电镀后形成的复合镀层进行任何损伤;去除
后镀层露出部分形成刀刃;(5)电解抛光将铝腐蚀出刃后的刀片,放入抛光电解液内,通电10~15s进行电解抛光;抛光电解过程,可去除0.2~0.4μm厚度的电镀镍结合剂,而铝基体不产生任何变化,电解抛光工序可去除电镀过程导致的刀刃的局部高点,提高平整性,同时铝腐蚀后的刀刃是黑色的,电解后可去除这部分黑色材料,形成光亮的镀层;电解抛光后的划片刀已经具备成品的全部状态,可在电解抛光后进行人工目检,将刀刃或者基体上有缺陷的划片刀进行报废,刀刃和基体均完好的划片刀,可进行切割性能检测。
19.进一步的,步骤(2)中,电镀液中金刚石磨料的含量为1-1.5g/l,优选为1.2g/l。
20.进一步的,步骤(2)中,电镀液主要成分是氨基磺酸镍和硼酸,其中氨基磺酸镍的浓度为350
±
50g/l,硼酸的浓度为35
±
5g/l。
21.进一步的,步骤(2)中,电镀时选用的结合剂为高刚性电镀镍结合剂,此结合剂在切割超薄ic晶圆时能够减少切割过程中刀刃的摆动,进而减少侧崩。
22.进一步的,步骤(2)中,通过调整电镀电流,电镀液ph,以及表面活性剂和硬度调整剂(糖精钠)的浓度等,可以实现对刀刃电镀镍结合剂的硬度和弹性模量进行改善;具体的,电镀时ph在4.2~4.8之间,电流密度为0.86~0.90a/dm2,电镀时间为78~80min;表面活性剂为脂肪醇聚氧丙烯醚,浓度为0.3~0.5g/l;硬度调整剂为糖精钠,浓度为0.050~0.055g/l;电镀时电镀镍硬度波动范围在650~720hv,这个硬度范围的电镀镍,刚性最优。
23.进一步优选的,当电流密度维持在0.88a/dm2水平时,得到的复合镀层厚度范围为13~16μm,这种厚度的刀刃在划切50~100μm厚度超薄ic硅晶圆时,缝宽在15~18μm之间,充分满足超薄ic硅晶圆划切缝宽的要求(缝宽≤20μm)。
24.通过以上参数调整,可以实现刀刃长厚比l/t在(24~34):1之间,弹性模量e可达200gpa以上,刚性极好,切割过程中,相同切割波动载荷下,刀刃摆动更小,因而侧崩更好。
25.进一步的,步骤(3)中,为了保持稳定的背崩性能,金刚石浓度需要维持较低水平,通过精准控制单位电镀液中金刚石含量,进而控制电镀后复合镀层(或者出刃后刀刃)的金刚石磨料的体积占比在10.1%~15.2%范围之间。
26.进一步的,步骤(4)中,强碱溶液为氢氧化钠溶液;具体的,步骤(4)中,氢氧化钠溶液的浓度为120
±
10g/l,溶液温度控制在55
±
1℃,腐蚀时间为85min,可腐蚀出刀刃长度l在380~440μm之间,而且圆周方向不同位置刃长一致性极好,差异在30μm以内,这样可以控制划片刀刀刃的长厚一直保持比l/t在(24~34):1之间。
27.进一步的,步骤(5)中,抛光电解液由体积分数20%的h2so4、体积分数20%的h3po4、以及体积分数60%的水组成。
28.进一步的,本发明还提供了所述专用划片刀在切割超薄ic晶圆中的应用。
29.进一步的,所述超薄ic晶圆的表面可以附着有daf膜。
30.与现有技术相比,本发明的有益效果是:1、本发明的ic晶圆,材料为单晶硅,属于硬脆材料,这类带有daf膜的超薄硅晶圆,
在用常规划片刀划切时,过薄的硅晶圆极易在划切过程中极易发生背崩、背裂和侧崩;本发明通过对划片刀结构即加工工艺进行调整,制作出一种50~100μm厚度超薄ic硅晶圆划切专用,特别能够适用于背面含有daf膜的应用场合,具有更好的背崩、背裂,侧崩抑制性能;划片刀复合镀层采用的金刚石磨料为多棱角型4800目极细粒度微粉,能克服daf膜的粘附,防止背裂。
31.2、本发明的划片刀的刀刃具有极高的刚度,能够减少切割过程刀刃摆动导致的ic芯片侧面崩裂,提高极限进刀速度,进刀速度可以提升,由不到20mm/s,提升至40mm/s。
32.3、精确控制缝宽在15~18μm之间,保证划切过程能够在40μm宽度的切割道内,距离切割道边缘存在10μm以上的安全余量,减少崩边裂纹超出切割道边缘,减小崩裂处进入ic芯片内部的风险。
附图说明
33.图1是本发明实施例1所述划片刀的结构示意图,左上为俯视图,右侧为截面图,中间为截面图的局部放大图;图2是图1中局部放大图;图3是不同粒度磨料在去除工件材料时的差异图;图4是本发明实施例1所述划片刀中4800目金刚石磨料粒度分布图;图5是不同类型金刚石磨料的形状对比图,其中左图为本发明使用的多棱角型金刚石磨料(4800目),右图为现有技术中钝圆型金刚石磨料(4800目);图6是本发明实施例1制备的划片刀刀刃刚性等效示意图,其中将划片刀刀刃部分等效为悬臂梁;图7是采用实施例1所述划片刀以及现有技术中传统的20x380-4800-50-m规格刀片对含有daf膜的超薄ic晶圆切割测试侧崩效果图,左图为本发明的切割效果,右图为现有技术中刀片的切割效果;图8是采用实施例1所述划片刀以及现有技术中传统的20x380-4800-50-m规格刀片对100μm厚度、不含有daf膜的ic晶圆划切后背崩效果图,左图为本发明的切割效果,右图为现有技术中刀片的切割效果;图中,1是复合镀层,1.1是刀刃,2是铝基体,3是金刚石磨料,4是电镀镍结合剂,t为刀刃厚度,l为刀刃漏出部分长度。
具体实施方式
34.下面结合实施例对本技术的技术方案进行清楚、完整地描述,显然,所描述的实施例仅仅是本技术一部分实施例,而不是全部的实施例。基于本技术中的实施例,本领域普通技术人员在没有做出创造性劳动前提下所获得的所有其他实施例,都属于本技术保护的范围。
35.本说明书所附图式所绘示的结构、比例、大小等,均仅用以配合说明书所揭示的内容,以供熟悉此技术的人士了解与阅读,并非用以限定本发明可实施的限定条件,故不具技术上的实质意义,任何结构的修饰、比例关系的改变或大小的调整,在不影响本发明所能产生的功效及所能达成的目的下,均应仍落在本发明所揭示的技术内容得能涵盖的范围内。
同时,本说明书中所引用的如“上”、“下”、“左”、“右”、“中间”及“一”等的用语,亦仅为便于叙述的明了,而非用以限定本发明可实施的范围,其相对关系的改变或调整,在无实质变更技术内容下,当亦视为本发明可实施的范畴。
36.实施例1如图1、2、6所示,一种超薄ic晶圆专用划片刀,由高精度铝基体2和镀覆在铝基体2表面的复合镀层1构成,其中复合镀层1由电镀镍结合剂4和金刚石磨料3组成;复合镀层1的厚度为13~16μm。
37.本发明所述超薄ic晶圆专用划片刀采用电镀工艺在高精度铝基体2上镀覆复合镀层1,如图2所示,复合镀层1伸出铝基体2之外、露出的部分称为刀刃1.1,构成划片刀的工作部分,刀刃1.1长度为380~440μm,刀刃1.1的长厚比为(24~34):1。
38.如图2所示,金刚石磨料3在复合镀层1中均匀分布,所述金刚石磨料3为4800目金刚石微粉,本实施例对金刚石微粉的粒度分布、粗大颗粒比例进行了控制,金刚石微粉的颗粒等效粒径中值d50为1.67μm;所述金刚石磨料3选用多棱角型晶型。
39.为了具备较好的防背崩性能,金刚石磨料3在复合镀层1中体积占比为10.1%~15.2%。
40.本发明中金刚石磨料粒度选择的原理如下:如图3所示,不同粒度磨料在去除工件材料时的差异图,划片刀划切单晶硅材料的磨削机理是无数颗磨料对单晶硅进行划擦,金刚石磨料尖部在工件上压出微观崩碎,产生碎屑,并通过磨料前方的容屑槽带走。对于厚晶圆而言,整个磨料在从上到下划切工件过程中,磨料前部积累大量硅屑,因此磨料前部需要较大的容屑空间(容屑槽),随着划片刀的转动,容屑槽带走划切产生的硅屑,如果容屑空间不足会导致背崩过大。当切割超薄ic晶圆时,被去除单晶硅屑更少,不需要过大的磨料粒度来产生更大的容屑槽,过大的磨料粒度反而对工件产生更大冲击,产生更大的崩碎,在晶圆背面体现为背崩过大,甚至是背裂。而过小的磨料则由于切割能力不足,无法维持较高的进刀速度。例如,使用粒度d50为1.4μm的磨料做成划片刀划切单晶硅,进行切割测试,最大进刀速度仅为10mm/s,超过10 mm/s以后,通常会断刀。
41.同时,对含有daf膜超薄ic晶圆进行切割时,由于磨料在切割硅晶圆和daf膜后,daf膜带入切割区域的高延展性材料,容易粘附在刀尖,包裹磨料,使磨料失去切割作用,刀刃锋利度丧失。所以导致超薄ic晶圆切割载荷极小,对背崩、侧裂等切割品质要求较高。
42.因此,本发明经过大量对比试验发现,采用特制的4800目金刚石微粉作为磨料,切割此类超薄ic晶圆时的综合性能最优。本发明所述特制的4800目金刚石微粉具体粒度组成为:颗粒等效粒径中值d50为1.67μm,粒度分布如图4所示,从图4中可以看出,绝大部分磨料直径在1~2μm之间,这类极细颗粒的磨料每次对硅晶圆的去除量极小,对硅晶圆的冲击也极小,因此背崩和背裂效果均较高;其中,粒径超过5μm的粗大颗粒体积占比控制在1%以内。
43.本发明中金刚石磨料晶型选择的原理如下:如图5所示,含有钝圆型金刚石磨料的切割刀具在切割硅晶圆和daf膜时,daf膜带入切割区域的高延展性切屑,容易粘附在刀尖,包裹磨料,使磨料失去切割作用,刀刃锋利度丧失。
44.相对于钝圆型金刚石磨料,多棱角型金刚石磨料在划片刀划切过程中会形成更锋
利的微观切割刃,具有更好的背崩性能,因此,为了更好克服由于在超薄ic晶圆表面引入daf膜导致的高延展性切屑现象,本发明所述划片刀中的磨料选择多棱角型磨料。多棱角型磨料具有更好的锋利度和自锐性,可以使daf膜引入切割区域的高延展性材料不易粘附,还可以更好保持刀刃锋利度,进而减少背崩和背裂的发生。
45.虽然,与图5中钝圆型磨料相比,多棱角型磨料耐磨偏低,在切割厚晶圆等高载荷工况下,容易影响使用寿命,但是添加了多棱角型磨料的划片刀在切割超薄ic晶圆时,超薄晶圆切割载荷极小,具有较高的切割品质,能够满足加工要求。
46.上述超薄ic晶圆专用划片刀的制作方法,包括铝基体加工、电镀、磨外圆、铝腐蚀出刃、电解抛光等工序,具体步骤如下:(1)铝基体加工图1所示结构的专用划片刀在加工过程中,首先将外径为60mm的铝棒车断,经过粗加工和精加工,制成外径56mm、内孔径19.054mm的碟形铝基体2;其中铝基体2右侧的大端面用于电镀沉积含有金刚石磨料的复合镀层1,铝基体2右侧的大端面平面精度要求在1μm以内。
47.(2)电镀将加工好的铝基体2用夹具进行组装,并对铝基体2上不需电镀区域用密封垫进行遮挡;组装后进行除油清洗,之后放入电镀槽,在包含电镀液 4800目多棱角型金刚石磨料的混合液中进行电镀;本实施例中氨基磺酸镍体系电镀液,具体的,本实施例中使用的电镀液主要成分是氨基磺酸镍和硼酸,其中氨基磺酸镍的浓度为350
±
50g/l,硼酸的浓度为35
±
5g/l,余量为纯水,电镀液ph在4.2~4.8之间。
48.电镀过程中,需要考虑以下几点:a、发明人经过大量实验发现,电镀液中金刚石浓度越低,单位体积含有金刚石磨料越少,两颗磨料之间距离越大,磨料前部区域容屑槽形成更充分,更容易维持背崩稳定性,为了保持稳定的背崩性能,金刚石浓度需要维持较低水平。
49.如图1、2所示,在电镀过程中,精准控制单位氨基磺酸镍体系电镀液中金刚石磨料的含量保持在1.2g/l左右,进而控制电镀后复合镀层1(或者出刃后刀刃1.1)的金刚石磨料的体积占比在10.1%~15.2%范围之间,这个范围属于极低浓度,可防止背崩性能波动。
50.b、如图6所示,为本发明制备的划片刀刀刃刚性等效示意图,图中,1是复合镀层,1.1是出刃后刀刃,2是铝基体,t为刀刃厚度,l为刀刃漏出部分长度,由电镀镍结合剂4和金刚石磨料3复合形成的复合镀层1在铝腐蚀出刃工序之后,末端形成刀刃1.1,由于刀刃1.1在切割过程承受来自各方向的冲击载荷,划片刀刀刃1.1长度l通常是刀刃1.1厚度t的20倍以上,因此刀刃的抗弯高度存在较大风险,如变形过大,刀刃1.1会撞击被切芯片侧面,导致芯片侧崩;因此,在电镀工序中,本发明将刀刃1.1等效为一端固定的悬臂梁,得出刀刃1.1刚度正比于et
3 / l3,其中e为电镀镍的弹性模量;当电流密度维持在0.88a/dm2水平,电镀时间在78~80min时,得到的复合镀层1厚度范围为13~16μm,这种厚度的刀刃1.1在划切50~100μm厚度超薄ic硅晶圆时,缝宽在15~18μm之间,充分满足超薄ic硅晶圆划切缝宽的要求(缝宽≤20μm)。
51.c、本发明电镀时选用的结合剂为高刚性电镀镍结合剂,此结合剂在切割超薄ic晶
圆时能够减少切割过程中刀刃的摆动,进而减少侧崩。
52.电镀工序中,通过调整电镀电流,电镀液ph,以及表面活性剂和硬度调整剂(糖精钠)的浓度等,可以实现对刀刃电镀镍结合剂4的硬度和弹性模量进行改善。
53.具体的,本发明中ph精准控制在4.2~4.8之间;表面活性剂为脂肪醇聚氧丙烯醚,浓度在0.3~0.5g/l;硬度调整剂(糖精钠)的浓度保持在0.050~0.055g/l范围内,电镀镍硬度波动范围在650~720hv,这个硬度范围的电镀镍,刚性最优。
54.同时通过对划片刀刀刃1.1的结构进行调整,使刀刃1.1长厚比l/t在(24~34):1之间,弹性模量e可达200gpa以上,具体弹性模量e为203gpa,刚性极好,切割过程中,相同切割波动载荷下,刀刃1.1摆动更小,因而侧崩更好。
55.通过以上参数调整,刀刃1.1刚性提升后,侧崩明显改善,针对典型超薄ic晶圆的最高进刀速度可以从20mm/s提升至40mm/s,提升晶圆划切加工效率接近100%。
56.(3)磨外圆磨外圆工序是把铝基体2外径从55.60mm加工到55.56mm,即半径方向去除20μm厚度的材料;磨外圆工序可去除电镀过程导致镀层外圆处不均匀部分,同时可将刀刃1.1外圆进行加工提高圆度、以及减小刀刃1.1外圆相对于基体内孔的偏心量。
57.(4)铝腐蚀出刃如图6所示,铝腐蚀出刃工序采用氢氧化钠等强碱溶液,将与镀层边缘接触的铝基体2进行溶解去除,同时不对电镀后形成的复合镀层1进行任何损伤;去除后镀层露出部分形成刀刃1.1。
58.铝腐蚀工序(即刃长暴露工序)过程中精确控制碱溶液浓度、温度及铝腐蚀时间可以改善出刃效果,具体的,本实例中,铝腐蚀工序氢氧化钠碱溶液浓度为120
±
10g/l、溶液温度控制在55
±
1℃、腐蚀时间为85min时,可腐蚀出刀刃1.1长度l在380~440μm之间,而且圆周方向不同位置刃长一致性极好,差异在30μm以内,这样可以控制划片刀刀刃1.1的长厚一直保持比l/t在(24~34):1之间。
59.(5)电解抛光将铝腐蚀出刃后的刀片,放入抛光电解液内,通电10~15s进行电解抛光,具体的,抛光电解液由体积分数20%的h2so4、体积分数20%的h3po4、以及体积分数60%的纯水组成;抛光电解过程,可去除少量电镀镍结合剂,厚度在0.2~0.4μm之间,而铝基体2不产生任何变化,电解抛光工序可去除电镀过程导致的刀刃1.1的局部高点,提高平整性,同时铝腐蚀后的刀刃是黑色的,电解后可去除这部分黑色材料,形成光亮的镀层。
60.电解抛光后的划片刀已经具备成品的全部状态,可在电解抛光后进行人工目检,将刀刃或者基体上有缺陷的划片刀进行报废,刀刃和基体均完好的划片刀,可进行切割性能检测。
61.应用试验1采用实施例1所述划片刀划切12寸80μm厚度ic晶圆,晶圆底部贴有40μm厚度daf膜,在dfd6362全自动晶圆切割机上,采用step cut(阶梯切割)方式,采用本发明所述划片刀(规格为20x380-4800-50-h)作为z2轴刀片使用,直接决定侧崩性能,此应用要求侧崩<50μm。
62.采用行业常见超薄ic晶圆切割参数,z2轴:转速35krpm,进刀速度35mm/s,切40μm
晶圆厚度;切测试效果如图7所示,图7中左图为本发明制备的划片刀对含有daf膜的超薄ic晶圆切割测试侧崩效果图,右图为使用传统的20x380-4800-50-m规格刀片作为z2轴刀片,在同等切割参数下切割同类产品的侧崩效果图,从图7中可以看出,本发明切割测试侧崩在10μm以内,满足含有daf膜超薄ic晶圆切割的应用要求,而右图中侧崩已经延伸到台阶处,侧崩尺寸超过30μm,不能满足切割要求。
63.应用试验2采用实施例1所述划片刀划切12寸100μm厚度ic晶圆,无daf膜,在dfd6362全自动晶圆切割机上,采用step cut方式,采用本发明所述划片刀(规格为20x380-4800-50-h)作为z2轴刀片使用,直接决定背崩、背裂和侧崩性能,此应用要求侧崩<50μm,无背裂,背崩<50μm。
64.采用行业常见超薄ic晶圆切割参数,z2轴:转速35k,进刀速度45 mm/s,切60μm晶圆厚度;切测试效果如图8所示,图8中左图为本发明制备的划片刀对超薄ic晶圆切割测试背崩效果图,右图为使用传统的20x380-4800-50-m规格刀片作为z2轴刀片,在同等切割参数下切割同类产品的背崩效果图,从图8中可以看出,本发明切割测试背崩效果极好,崩口尺寸在10μm以内,未见背裂,而右图中背崩通常在30μm左右,最大处已超过50μm,不能满足切割要求。
65.上述试验结果表明,采用本发明制作的划片刀在对超薄ic晶圆进行划切时,能够减少切割过程刀刃摆动导致的ic芯片侧面崩裂,提高极限进刀速度,进刀速度可以提升,还能够能克服daf膜的粘附,防止背裂。综上所述,本发明所述划片刀能够显著改善50~100μm厚度范围的超薄ic硅晶圆的切割质量,减少常规刀片切割时典型的背崩、侧崩、背裂的发生,进而提升晶圆划切良率和加工效率。
66.上述实施例为本发明实施方式的举例说明,本发明的实施方式并不受上述实施例的限制,其它任何未背离本发明精神实质与原理下所作的改变、修饰、替代、组合、简化,均应为等效的置换方式,都包含在本发明的保护范围之内。
再多了解一些
本文用于企业家、创业者技术爱好者查询,结果仅供参考。