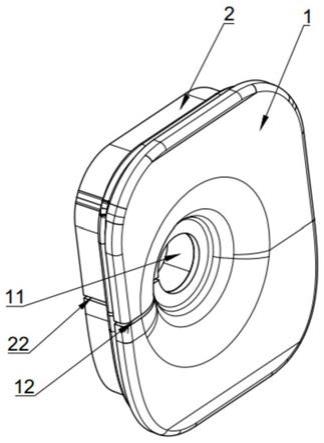
1.本发明涉及汽车零部件技术领域,具体涉及一种吸音线束堵盖。
背景技术:
2.目前国内已上市的纯电动桥车或suv车型,普遍存在较大的线束过孔。一般采用线束自带橡胶堵盖或者塑料堵盖进行封堵过孔。该类堵盖需要集成缠绕在线束上供货,一般不具备吸音功能,如果线束或堵盖损坏,就得全套更换,使用不经济。现有的堵盖一般只能适用于较薄的但钣金件固定,而且使用的橡胶重量较大,橡胶气味也重。
技术实现要素:
3.基于上述表述,本发明提供了一种吸音线束堵盖,以解决现有线束堵盖不能隔音、有异味和不能适应多种钣金壁安装要求。
4.本发明解决上述技术问题的技术方案如下:
5.一种吸音线束堵盖,包括固定层和吸音层,吸音层固定在固定层的背部,吸音层的形状与固定层相同,吸音层的长宽尺寸比固定层的长宽尺寸小;固定层中心设置扩口形的前线孔,吸音层对应位置设置后线孔;固定层侧边设置直通前线孔的前切口,吸音层对应位置直通后线孔的后切口;固定层周围设置环形的凹槽,凹槽后方设置用于止挡的环形凸台。所述的固定层采用发泡pe材料制作。本技术的线束堵盖能避免线束过中心孔后的密封,线束堵盖不用提前集成到线束,简化线束结构,减小安装成本和使用。能有效的隔绝外侧腔体的声音和气流。能适应单层和双层钣金的固定。通过材料发泡pe材料密度小、质量轻,而且没有异味。
6.优选的,所述的凹槽底部设置阶梯形的阶梯凹槽。前侧的钣金插入凹槽的前侧内沉槽内,从而可以增加紧固效果。
7.优选的,所述的的凹槽前方侧壁上设置环形的内凸边。通过设置内凸边,从而使得凹槽与钣金配合紧密,还可避免凹槽内进入灰尘。
8.优选的,所述前线孔的扩口形内壁向外凸起。前线孔的前侧扩口壁设置向上凸起,便于增强前切口周围的结构强度,避免拉线的过程中,造成前切口周围过度的磨损。
9.优选的,所述的前线孔内设置环形的前孔唇,前孔唇为薄壁结构,厚度为1.5-3mm。通过减小前孔唇的壁厚尺寸,弱化前孔唇的结构刚性,增强结构弹性,可以弥补线束空间中位置误差。
10.优选的,所述的发泡pe材料的密度为30-50kg/m3。将材料密度控制在30-50kg/m3,使得材料保持必要的硬度,避免太软而容易松脱,同时避免过硬,导致线束不容易穿过,同时避免不便于堵盖固定到钣金件上。
11.优选的,所述的吸音层采用超细纤维材料制作。超细纤维微孔结构具有吸音功能,能充分吸收外侧腔体内的高频噪音。
12.与现有技术相比,本技术的技术方案具有以下有益技术效果:本技术的线束堵盖
能避免线束过中心孔后的密封,线束堵盖不用提前集成到线束,简化线束结构,减小安装成本和使用。能有效的隔绝外侧腔体的声音和气流。能适应单层和双层钣金的固定。通过材料发泡pe材料密度小、质量轻,而且没有异味。通过采用合适密度的发泡pe材料,可以保证适度的硬度和形变,便于安装和使用。通过设置薄壁结构的前孔唇,可以弥补线束空间中位置误差。通过设置阶梯凹槽,可以适用于单层和双层钣金件的安装。通过采用超细纤维材料制作吸音层,便于吸收刺耳的高频噪音。
附图说明
13.图1为本发明线束堵盖安装到车辆a柱钣金上的安装示意图;
14.图2为本发明线束堵盖的结构示意图;
15.图3为本发明线束堵盖沿竖直中轴面剖视图;
16.图4为本发明线束堵盖第二种方案沿竖直中轴面剖视图;
17.图5为图4的局部放大e视图;
18.图6为本发明固定层不同密度材料所对应的形变压力实验数据表。
19.附图中,各标号所代表的部件列表如下:
20.1、固定层;2、吸音层;6、线束堵盖;7、a柱钣金;8、线束;11、前线孔;12、前切口;13、凹槽;14、凸台;21、后线孔;22、后切口;71、板金件;111、前孔唇;131、阶梯凹槽;132、内凸边。
具体实施方式
21.为了便于理解本技术,下面将参照相关附图对本技术进行更全面的描述。附图中给出了本技术的实施例。但是,本技术可以以许多不同的形式来实现,并不限于本文所描述的实施例。相反地,提供这些实施例的目的是使本技术的公开内容更加透彻全面。
22.本实施例中,如图1、图2、图3所示。一种吸音线束堵盖,其特征在于,包括固定层1和吸音层2,吸音层2固定在固定层1的背部,吸音层2的形状与固定层1相同,吸音层2的长宽尺寸比固定层1的长宽尺寸小;固定层1中心设置扩口形的前线孔11,吸音层2对应位置设置后线孔21;固定层1侧边设置直通前线孔11的前切口12,吸音层2对应位置直通后线孔21的后切口22;固定层1周围设置环形的凹槽13,凹槽13后方设置用于止挡的环形凸台14。本技术的线束堵盖6固定到汽车钣金上,尤其在对于a柱钣金7,线束堵盖6中心设置通孔,主要用于线束8通过,同时起到密封的作用。线束堵盖6包括固定层1和吸音层2,固定层1主要用于固定到汽车钣金上。
23.固定层1为方形片状结构,占用车内空间小。固定层1沿外周边设置环形的凹槽13,便于卡住在钣金孔内。凹槽13前方为前堵面,凹槽13后方设置环形的凸台14,其中凸台14截面为拱形,两侧边光滑,便于通过挤压变形卡入钣金上的孔内。吸音层2紧贴在固定层1后方,吸音层2尺寸比固定层1小,与钣金上的安装孔的尺寸相等。可通过胶水将吸音层2固定到在固定层1上。吸音层采用超细纤维材料,超细纤维微孔结构具有吸音功能,能充分吸收外侧腔体内的高频噪音。线束堵盖6安装到钣金上的安装孔内时,吸音层2先穿过安装孔,然后通过环形凸台14,最后卡入环形的凹槽13内。线束堵盖6中心设置用于线束通过的中心孔,线束堵盖6一侧壁设置直通所述中心孔的切口。对应位置,固定层1上设置前线孔11和直
通前线孔11的前切口12;吸音层2上设置后线孔21和直通后线孔21的后切口22。在安装线束时,直接将线束从切口位置横向插入线束堵盖6的中心孔内。
24.所述的固定层1采用发泡pe材料制作。发泡pe材料相对于橡胶材料,密度小,质量轻,而且没有异味。所述的发泡pe材料的密度为30-50kg/m3。发泡pe材料不同密度,对应的硬度不同,通常密度越大,材料越硬。通过实验测得,本技术中的发泡pe材料不同密度对应的25%应变压缩应力表。将材料密度控制在30-50kg/m3,30kg/m3对应的25%应变压缩应力为≥0.066mpa,50kg/m3对应的25%应变压缩应力为≥0.215mpa,使得材料保持必要的硬度,避免太软而容易松脱。硬度不能太高,避免线束不容易穿过,同时不便于堵盖固定到钣金件上。所述的吸音层2采用超细纤维材料制作。吸音层2是超细纤维铺成的厚毡,超细纤维微孔结构具有吸音功能,能充分吸收外侧腔体内的高频噪音。
25.本实施例中,如图4、5所示。所述的凹槽13底部设置阶梯形的阶梯凹槽131。凹槽13用于嵌入和固定在钣金孔内,凹槽13内靠前侧设置内沉槽,形成阶梯凹槽131。对于双层焊接的钣金件71,前侧的一层钣金件口径稍小,前侧的钣金插入凹槽13的前侧内沉槽内,从而可以增加紧固效果。所述的的凹槽13前方侧壁上设置环形的内凸边132。由于线束堵盖6为发泡pe材料,为避免应力集中,在凹槽13内直角地方设置圆弧形。同时由于凹槽13低圆弧形的存在,使得凹槽13与钣金配合不紧密。在凹槽13前侧设置向后延伸的内凸边132,内凸边132略微伸出凹槽13前侧面0.5-1mm,线束堵盖6安装插入钣金孔后,内凸边132紧贴钣金,从而使得凹槽13与钣金配合紧密。同时可以避免凹槽13内进入灰尘。所述前线孔11的扩口形内壁向外凸起。前线孔11为喇叭形,便于线束的通过。将前线孔11的前侧扩口壁设置向上凸起,便于增强前切口12周围的结构强度,避免拉线的过程中,造成前切口12周围过度的磨损。
26.本实施例中,如图3、图4所示。所述的前线孔11内设置环形的前孔唇111,前孔唇111为薄壁结构,厚度为1.5-3mm。固定层1的厚度为10-12mm,固定层1前侧开口通过前线孔11过度到前孔唇111,前孔唇111的厚度为1.5-3mm。通过减小前孔唇111的壁厚尺寸,弱化前孔唇111的结构刚性,增加结构弹性,此处容易变形,从而弥补线束空间中位置误差。
27.以上所述仅为本发明的较佳实施例,并不用以限制本发明,凡在本发明的精神和原则之内,所作的任何修改、等同替换、改进等,均应包含在本发明的保护范围之内。
再多了解一些
本文用于企业家、创业者技术爱好者查询,结果仅供参考。